Das Sputtern anorganischer Werkstoffe ist eine Technik der physikalischen Gasphasenabscheidung (PVD), mit der dünne Schichten aus anorganischen Werkstoffen auf Substrate aufgebracht werden. Bei diesem Verfahren wird ein Zielmaterial in einer Vakuumkammer mit hochenergetischen Ionen beschossen, die in der Regel aus einem Inertgas wie Argon stammen. Die Ionen lösen Atome aus dem Target, die dann durch das Vakuum wandern und sich auf einem Substrat ablagern und einen dünnen Film bilden. Das Sputtern ist in Branchen wie der Halbleiterindustrie, der Optik und der Luft- und Raumfahrt für Anwendungen wie die Herstellung von integrierten Schaltkreisen, Antireflexbeschichtungen und korrosionsbeständigen Schichten weit verbreitet. Es ist ein vielseitiges und präzises Verfahren zur Herstellung hochwertiger, gleichmäßiger Dünnschichten aus anorganischen Materialien.
Die wichtigsten Punkte werden erklärt:
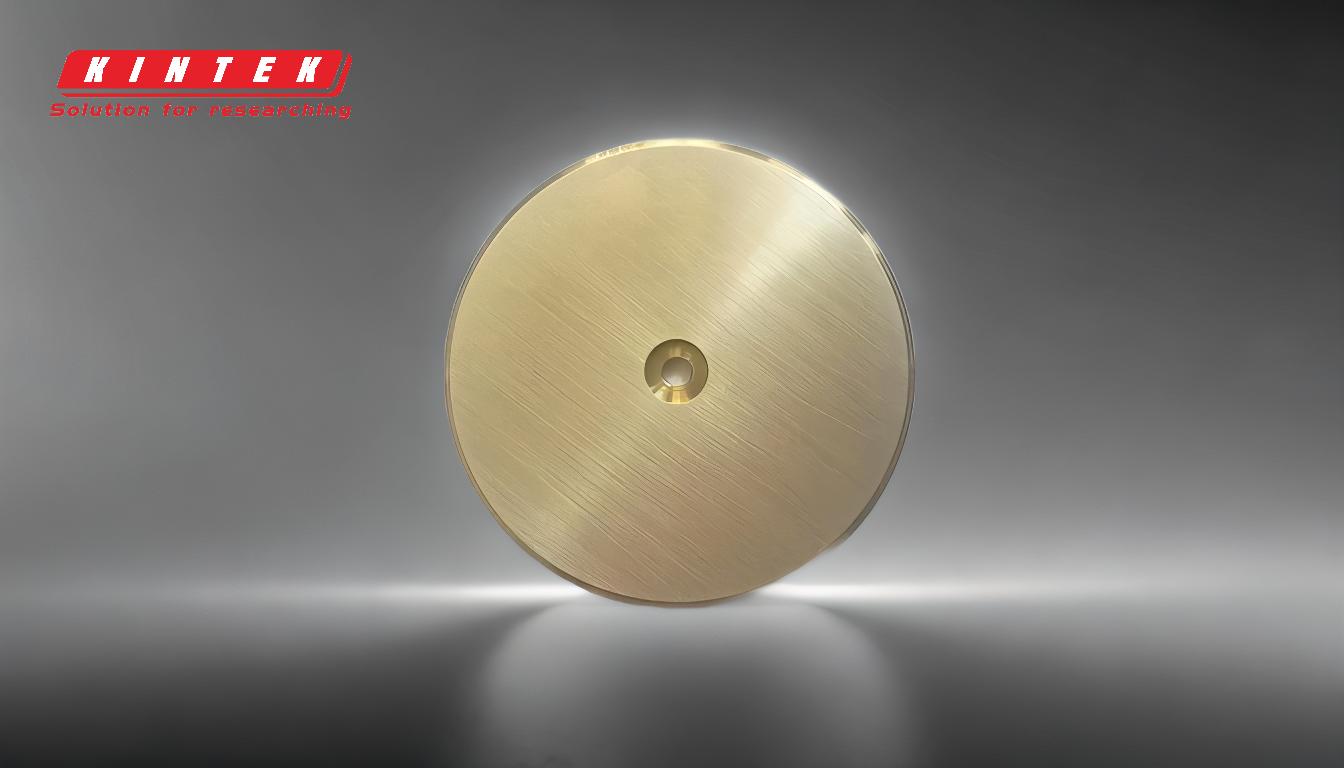
-
Definition von Sputtering:
- Beim Sputtern handelt es sich um ein physikalisches Aufdampfverfahren (PVD), bei dem hochenergetische Ionen ein Zielmaterial beschießen, wodurch Atome aus der Zieloberfläche herausgeschleudert werden.
- Diese ausgestoßenen Atome wandern durch ein Vakuum und lagern sich auf einem Substrat ab, wo sie einen dünnen Film bilden.
-
Mechanismus des Sputterns:
- Ionenbombardement: Die Ionen des Inertgases (in der Regel Argon) werden auf das Zielmaterial beschleunigt.
- Energieübertragung: Die Ionen übertragen ihre kinetische Energie auf die Zielatome, so dass diese herausgeschleudert werden.
- Ablage: Die herausgeschleuderten Atome wandern durch das Vakuum und lagern sich auf dem Substrat ab und bilden einen dünnen Film.
-
Anwendungen des Sputterns:
- Halbleiterindustrie: Das Sputtern wird zur Abscheidung dünner Schichten aus verschiedenen Materialien bei der Verarbeitung integrierter Schaltkreise verwendet.
- Optische Industrie: Es wird zur Abscheidung von Antireflexionsschichten auf Glas und zur Herstellung von Polarisationsfiltern verwendet.
- Architektonisches Glas: Das Sputtern wird zur Beschichtung von großflächigen Oberflächen eingesetzt, z. B. für Beschichtungen mit niedrigem Emissionsgrad auf Doppelglasfenstern.
- Datenspeicherung: Es wird für die Herstellung von CDs, DVDs und Festplatten verwendet.
- Luft- und Raumfahrt und Verteidigung: Durch Sputtern werden Gadoliniumschichten für die Neutronenradiographie aufgebracht.
- Medizinische Geräte: Es wird zur Herstellung von dielektrischen Stapeln verwendet, um chirurgische Instrumente elektrisch zu isolieren.
-
Vorteile des Sputterns:
- Präzision: Das Sputtern ermöglicht die Abscheidung sehr dünner und gleichmäßiger Schichten von einigen Nanometern bis zu Mikrometern Dicke.
- Vielseitigkeit: Es kann für die Abscheidung einer breiten Palette von Materialien verwendet werden, darunter Metalle, Legierungen und Keramiken.
- Qualität: Durch Sputtern entstehen hochwertige Schichten mit hervorragender Haftung und Gleichmäßigkeit.
- Komplexe Geometrien: Er kann komplexe Formen und große Flächen gleichmäßig beschichten.
-
Arten des Sputterns:
- DC-Zerstäubung: Verwendet eine Gleichstromversorgung zur Erzeugung des Plasmas.
- RF-Sputtern: Verwendet Hochfrequenz (RF) zur Erzeugung des Plasmas, geeignet für isolierende Materialien.
- Magnetronzerstäubung: Nutzt Magnetfelder zur Verbesserung des Sputterprozesses, um die Abscheideraten zu erhöhen und die Schichtqualität zu verbessern.
-
Beim Sputtern verwendete Materialien:
- Ziel-Materialien: Typischerweise anorganische Materialien wie Metalle (z. B. Aluminium, Gold), Legierungen und Keramiken (z. B. Oxide, Nitride).
- Substrate: Sie können aus verschiedenen Materialien bestehen, darunter Siliziumscheiben, Glas, Kunststoffe und Metalle.
-
Prozess-Parameter:
- Vakuum Niveau: Um die Reinheit der abgeschiedenen Schicht zu gewährleisten, ist ein Hochvakuum erforderlich.
- Gasdruck: Der Druck des Inertgases (in der Regel Argon) wirkt sich auf die Sputtergeschwindigkeit und die Schichtqualität aus.
- Stromversorgung: Die Art und Leistung der Stromversorgung (DC, RF) beeinflussen den Sputterprozess.
- Temperatur: Die Temperatur des Substrats kann sich auf die Filmeigenschaften wie Haftung und Spannung auswirken.
-
Historischer Kontext:
- Das Sputtern wird seit den frühen 1800er Jahren eingesetzt und hat sich zu einer ausgereiften und weit verbreiteten Technik für die Abscheidung dünner Schichten entwickelt.
- Es hat eine entscheidende Rolle bei der Entwicklung moderner Technologien gespielt, darunter Halbleiter, optische Beschichtungen und Datenspeichergeräte.
-
Zukünftige Trends:
- Fortschrittliche Materialien: Entwicklung neuer Zielmaterialien für spezielle Anwendungen.
- Prozess-Optimierung: Kontinuierliche Verbesserung der Sputtertechniken zur Verbesserung der Schichtqualität und der Abscheidungsraten.
- Nachhaltigkeit: Schwerpunkt auf der Verringerung des Energieverbrauchs und der Umweltauswirkungen von Sputtering-Verfahren.
Das Sputtern von anorganischen Materialien ist eine wichtige Technologie in der modernen Fertigung, die die Herstellung von Hochleistungs-Dünnschichten für eine Vielzahl von Anwendungen ermöglicht. Ihre Präzision, Vielseitigkeit und Fähigkeit zur Herstellung hochwertiger Schichten machen sie in Branchen wie der Halbleiterindustrie, der Optik und der Luft- und Raumfahrt unverzichtbar.
Zusammenfassende Tabelle:
Aspekt | Einzelheiten |
---|---|
Definition | Physikalisches Gasphasenabscheidungsverfahren (PVD), bei dem hochenergetische Ionen verwendet werden, um Atome aus einem Target auszustoßen. |
Mechanismus | Ionenbeschuss → Energieübertragung → Abscheidung auf dem Substrat. |
Anwendungen | Halbleiter, Optik, Architekturglas, Datenspeicherung, Luft- und Raumfahrt, medizinische Geräte. |
Vorteile | Präzision, Vielseitigkeit, hochwertige Filme, gleichmäßige Beschichtung auf komplexen Formen. |
Typen | DC-Sputtering, RF-Sputtering, Magnetron-Sputtering. |
Materialien | Metalle (z. B. Aluminium, Gold), Legierungen, Keramiken (z. B. Oxide, Nitride). |
Prozess-Parameter | Vakuumniveau, Gasdruck, Stromversorgung, Substrattemperatur. |
Entdecken Sie, wie das Sputtern Ihren Fertigungsprozess verbessern kann kontaktieren Sie unsere Experten noch heute !