Magnete spielen eine entscheidende Rolle im Sputterprozess, da sie die Effizienz, Stabilität und Gleichmäßigkeit erhöhen.Sie werden strategisch hinter dem Target platziert, um ein Magnetfeld zu erzeugen, das das Plasma in der Nähe der Targetoberfläche einschließt.Dieser Einschluss erhöht die Ionisierung des Sputtergases (in der Regel Argon), was wiederum die Sputterrate erhöht und die Abscheidung dünner Schichten auf dem Substrat verbessert.Darüber hinaus tragen Magnete dazu bei, einen gleichmäßigen Abtrag des Zielmaterials aufrechtzuerhalten und eine gleichbleibende Beschichtungsqualität zu gewährleisten.Durch das Einfangen von Elektronen und die Erhöhung der Plasmadichte verringern Magnete auch die thermische Schädigung des Substrats und ermöglichen ein schnelleres Dünnschichtwachstum bei niedrigeren Drücken.
Die wichtigsten Punkte werden erklärt:
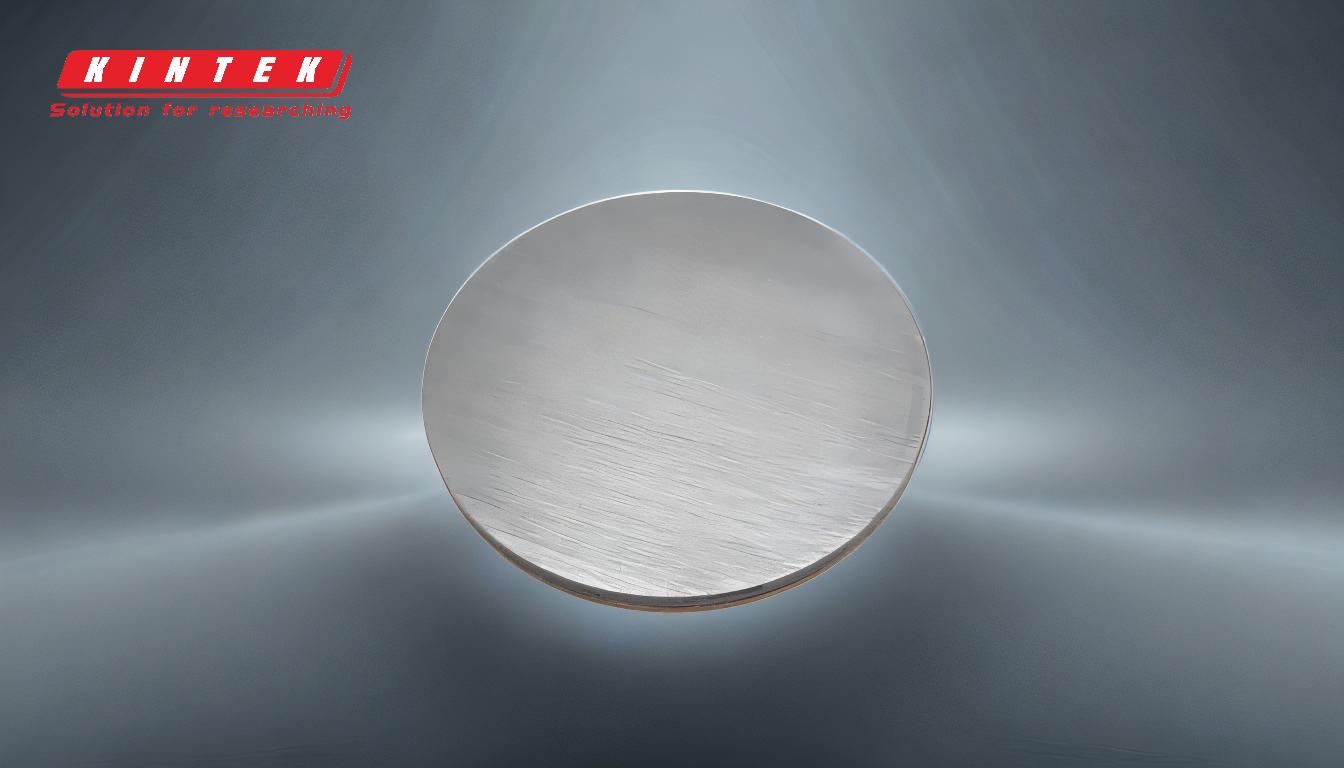
-
Plasmaeinschluss und verstärkte Ionisierung:
- Magnete erzeugen ein Magnetfeld, das die Elektronen in der Nähe der Oberfläche des Targets einfängt und ihre Weglänge sowie die Dichte des Plasmas erhöht.
- Durch diesen Einschluss wird die Ionisierung des Sputtergases (Argon) verstärkt, was zu einer höheren Wahrscheinlichkeit von Zusammenstößen zwischen Argon-Ionen und dem Targetmaterial führt.
- Die erhöhte Ionisierung führt zu einem effizienteren Sputterprozess, da die ionisierten Atome eher mit dem Target in Wechselwirkung treten und sich auf dem Substrat ablagern.
-
Erhöhte Sputtering-Rate:
- Durch das Magnetfeld werden die Elektronen spiralförmig bewegt und die Ionisierung des Argongases um das Target herum beschleunigt.
- Dieser Prozess erhöht die Sputterrate, indem er dafür sorgt, dass mehr Targetmaterial ausgestoßen und auf dem Substrat abgelagert wird.
- Schnellere Sputterraten ermöglichen ein schnelleres Dünnschichtwachstum, was besonders bei industriellen Anwendungen von Vorteil ist, bei denen Zeiteffizienz entscheidend ist.
-
Gleichmäßige Abtragung des Zielmaterials:
- Magnete tragen zu einer stabilen und gleichmäßigen Erosion des Zielmaterials bei, indem sie das Plasma in einem ringförmigen Doughnut fokussieren.
- Die gleichmäßige Erosion sorgt für eine gleichmäßige Ablagerung der Beschichtung auf dem Substrat und verbessert die Qualität und Zuverlässigkeit der Dünnschicht.
- Diese Gleichmäßigkeit ist entscheidend für Anwendungen, die präzise und wiederholbare Schichtdicken erfordern.
-
Geringere thermische Schädigung des Substrats:
- Durch die Begrenzung des Plasmas in der Nähe des Ziels reduzieren die Magnete die Anzahl der Elektronen, die das Substrat erreichen.
- Dadurch wird die thermische Schädigung des Substrats minimiert, was besonders bei wärmeempfindlichen Materialien wichtig ist.
- Eine geringere thermische Belastung ermöglicht auch die Abscheidung hochwertiger dünner Schichten, ohne die Integrität des Substrats zu beeinträchtigen.
-
Effizienz bei niedrigeren Drücken:
- Die verbesserte Ionisierung und Plasmadichte, die mit Magneten erreicht wird, ermöglicht effizientes Sputtern bei niedrigeren Drücken.
- Niedrigere Drücke verringern die Wahrscheinlichkeit einer Verunreinigung und verbessern die Reinheit der abgeschiedenen Dünnschicht.
- Diese Effizienz ist vorteilhaft für Anwendungen, die hochreine Beschichtungen erfordern, wie z. B. bei der Halbleiterherstellung.
-
Verbesserte Dünnschichtqualität und Wachstumsrate:
- Die Kombination aus erhöhter Ionisierung, gleichmäßiger Erosion und geringerer thermischer Schädigung führt zu qualitativ hochwertigeren Dünnschichten.
- Magnete tragen auch zu schnelleren Wachstumsraten der Dünnschichten bei, die für die Erfüllung der Produktionsanforderungen in verschiedenen Branchen unerlässlich sind.
- Die verbesserte Effizienz und Qualität machen das Magnetronsputtern zu einer bevorzugten Methode für die Dünnschichtabscheidung sowohl in der Forschung als auch im industriellen Umfeld.
Durch die Nutzung des Magnetfelds erreichen Sputtersysteme ein ausgewogenes Verhältnis von Effizienz, Gleichmäßigkeit und Qualität, was Magnete zu einem unverzichtbaren Bestandteil moderner Sputteranlagen macht.
Zusammenfassende Tabelle:
Hauptnutzen | Erläuterung |
---|---|
Plasmaeinschluss | Magnete fangen Elektronen ein und erhöhen die Plasmadichte und Ionisierung für eine effiziente Zerstäubung. |
Erhöhte Sputtering-Rate | Magnetfelder beschleunigen die Argon-Ionisierung und steigern so die Abscheidung des Zielmaterials. |
Gleichmäßige Erosion | Sorgt für eine gleichmäßige Zielerosion und eine zuverlässige Qualität der Dünnfilmbeschichtung. |
Reduzierte thermische Schädigung | Begrenzt das Plasma in der Nähe des Ziels und minimiert die Wärmeeinwirkung auf das Substrat. |
Effizienz bei niedrigeren Drücken | Ermöglicht hochreine Beschichtungen mit geringerem Kontaminationsrisiko. |
Verbesserte Dünnschichtqualität | Kombiniert gleichmäßige Erosion und schnellere Wachstumsraten für hervorragende Dünnschichten. |
Optimieren Sie Ihren Sputterprozess mit fortschrittlichen magnetischen Lösungen. Kontaktieren Sie unsere Experten noch heute !