Das Sputtern ist eine weit verbreitete Technik zur Abscheidung dünner Schichten, die jedoch einige Nachteile aufweist, die ihre Effizienz, Kosten und Anwendungseignung beeinträchtigen können.Zu diesen Einschränkungen gehören Probleme wie die Verunreinigung der Schichten, Einschränkungen bei der Materialauswahl, Probleme bei der Kontrolle der Schichtdicke und Schwierigkeiten bei der Kombination mit anderen Verfahren wie dem Lift-off-Verfahren.Außerdem kann das Sputtern unter niedrigen Abscheideraten, hohen Energiekosten aufgrund des Kühlungsbedarfs und Komplikationen wie Überhitzung beim HF-Sputtern oder Ladungsaufbau beim DC-Sputtern leiden.Das Verständnis dieser Nachteile ist entscheidend für die Optimierung des Sputterprozesses und die Auswahl der geeigneten Abscheidungsmethode für bestimmte Anwendungen.
Die wichtigsten Punkte erklärt:
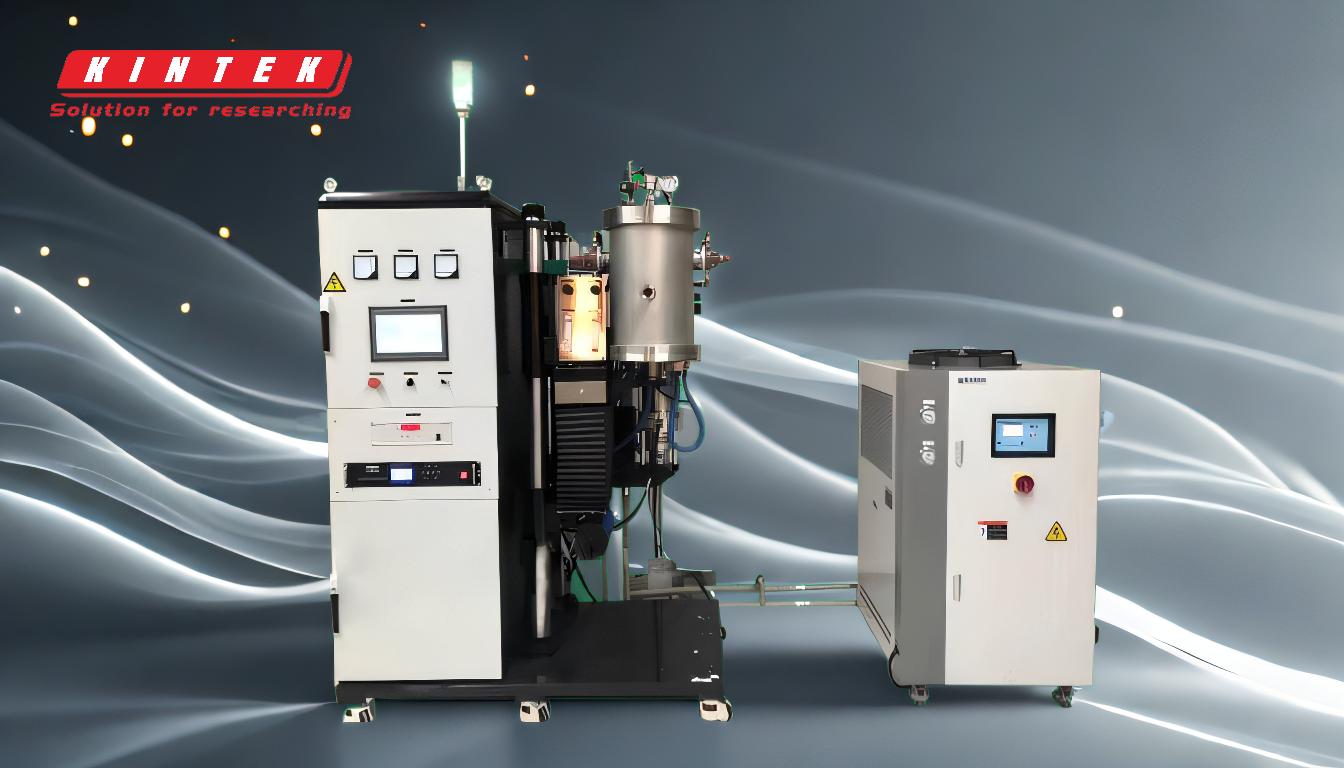
-
Filmverschmutzung:
- Beim Sputtern kann es durch die Diffusion von Verunreinigungen aus dem Ausgangsmaterial zu einer Verunreinigung der Schichten kommen.Dies ist besonders problematisch, wenn hochreine Schichten erforderlich sind, da selbst geringe Verunreinigungen die Leistung der Schicht beeinträchtigen können.
- Auch inerte Sputtergase wie Argon können zu Verunreinigungen in der wachsenden Schicht führen, was den Abscheidungsprozess weiter erschwert.
-
Einschränkungen bei der Materialauswahl:
- Der Sputterprozess wird durch die Schmelztemperatureigenschaften des Zielmaterials begrenzt.Materialien mit sehr hohen Schmelzpunkten können beim Sputtern eine Herausforderung darstellen, da sie unter den typischen Sputterbedingungen möglicherweise keine Atome effizient abtransportieren.
- Isolierende Materialien sind besonders schwierig zu sputtern, da sie Ladungen ansammeln können, was zu Prozessinstabilität führt.
-
Herausforderungen bei der Schichtdickenkontrolle:
- Beim Sputtern lässt sich die Schichtdicke nicht genau steuern, was bei Anwendungen, die sehr gleichmäßige oder spezifische Dicken erfordern, ein erheblicher Nachteil sein kann.
- Der diffuse Transport von Atomen beim Sputtern erschwert scharfe Grenzflächen oder ein kontrolliertes schichtweises Wachstum, was mit anderen Abscheidungsmethoden wie der gepulsten Laserabscheidung leichter zu erreichen ist.
-
Niedrige Abscheideraten:
- Beim Sputtern sind die Abscheideraten in der Regel niedriger als bei anderen Dünnschichttechniken.Dies kann die Produktionszeit und die Kosten erhöhen, insbesondere bei Anwendungen in großem Maßstab oder mit hohem Durchsatz.
- Der Bedarf an einem Kühlsystem zur Bewältigung der beim Sputtern entstehenden Wärme verringert die Produktionsraten weiter und erhöht den Energieverbrauch.
-
Hohe Substraterwärmung Effekte:
- Das Sputtering-Verfahren kann zu einer erheblichen Erwärmung des Substrats führen, was für temperaturempfindliche Materialien oder Substrate nachteilig sein kann.
- Überhitzung ist ein häufiges Problem beim HF-Sputtern, wo höhere Leistungen zur Erzeugung von Funkwellen erforderlich sind, was zu einer erhöhten thermischen Belastung des Systems führt.
-
Schwierige Kombination mit Lift-Off-Prozessen:
- Aufgrund des diffusen Atomtransports ist es schwierig, Sputtern mit Lift-off-Verfahren für die Schichtstrukturierung zu kombinieren.Dies macht eine vollständige Abschattung unmöglich, was zu Kontaminationsproblemen und einer geringeren Strukturierungsgenauigkeit führt.
- Die Unfähigkeit, eine scharfe Abschattung zu erreichen, kann die Auflösung und Präzision der strukturierten Schichten einschränken, was bei Anwendungen wie der Halbleiterherstellung von entscheidender Bedeutung ist.
-
Ladungsaufbau beim DC-Sputtern:
- Beim Gleichstromsputtern kann die Ansammlung von Ladungen auf dem Targetmaterial zu Prozessinstabilität und Lichtbogenbildung führen, wodurch das Target und die abgeschiedene Schicht beschädigt werden können.
- Besonders ausgeprägt ist dieses Problem beim Sputtern von Isoliermaterialien, wo die Ladungsansammlung das Plasma stören und die Abscheidungseffizienz verringern kann.
-
Wartung und Beschränkungen der Prozessparameter:
- Sputtersysteme müssen regelmäßig gewartet werden, um makellose dünne Schichten zu erzielen und zu erhalten.Das Vakuumsystem und andere Komponenten müssen in optimalem Zustand gehalten werden, um Verunreinigungen zu vermeiden und eine gleichmäßige Abscheidung zu gewährleisten.
- Die Prozessparameter beim Sputtern werden oft durch die Möglichkeiten des Vakuumsystems begrenzt, was die Bandbreite der Materialien und Bedingungen, die effektiv gesputtert werden können, einschränken kann.
Zusammenfassend lässt sich sagen, dass das Sputtern zwar ein vielseitiges und weit verbreitetes Verfahren zur Abscheidung von Dünnschichten ist, aber auch seine Tücken hat.Das Verständnis dieser Nachteile ist für die Optimierung des Prozesses und die Auswahl der geeigneten Abscheidungsmethode für bestimmte Anwendungen unerlässlich.Wenn man sich mit Themen wie Verunreinigung, Materialauswahl und Prozesskontrolle befasst, kann man einige dieser Einschränkungen abmildern und die Gesamteffizienz und -effektivität des Sputterns verbessern.
Zusammenfassende Tabelle:
Nachteil | Beschreibung |
---|---|
Filmverschmutzung | Verunreinigungen des Ausgangsmaterials oder der Sputtergase können die Filmqualität beeinträchtigen. |
Beschränkungen bei der Materialauswahl | Materialien mit hohem Schmelzpunkt oder isolierende Materialien lassen sich nur schwer effektiv sputtern. |
Herausforderungen bei der Schichtdickenkontrolle | Die genaue Kontrolle der Schichtdicke ist aufgrund des diffusen Atomtransports schwierig. |
Niedrige Abscheideraten | Sputtern hat im Vergleich zu anderen Abscheidungsmethoden langsamere Raten. |
Hohe Substraterwärmung | Die Erwärmung des Substrats kann temperaturempfindliche Materialien beschädigen. |
Schwierigkeiten mit Lift-Off | Die Kombination von Sputtern und Lift-Off-Verfahren ist eine Herausforderung. |
Ladungsaufbau beim DC-Sputtern | Isolierende Materialien können Ladung ansammeln und dadurch Instabilität verursachen. |
Wartung und Parameterbegrenzungen | Regelmäßige Wartung und Einschränkungen des Vakuumsystems beeinflussen die Prozesseffizienz. |
Benötigen Sie Hilfe bei der Optimierung Ihres Sputtering-Prozesses? Kontaktieren Sie noch heute unsere Experten für maßgeschneiderte Lösungen!