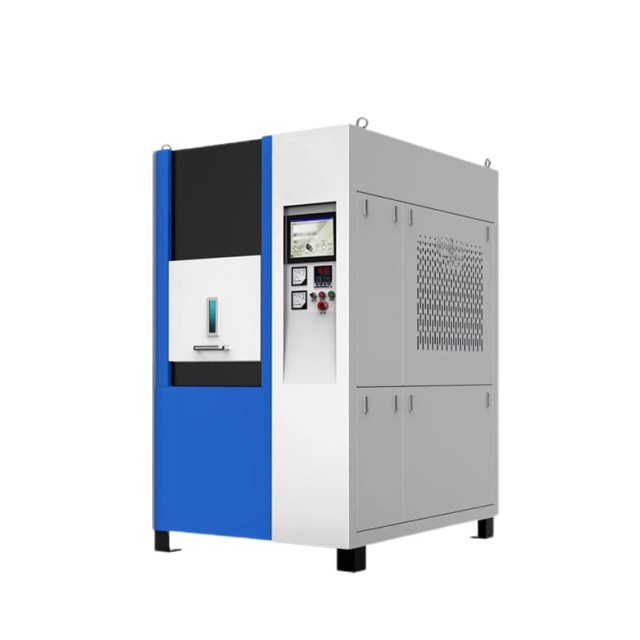
Vakuum-Heißpressofen
Spark-Plasma-Sinterofen SPS-Ofen
Artikelnummer : KTSP
Preis variiert je nach Spezifikationen und Anpassungen
- Ausgangsstrom
- 0-30000 A
- Nenntemperatur
- 2300 ℃
- Bemessungsdruck
- 100-500 KN
- Größe der Probe
- Ø30-Ø200 mm
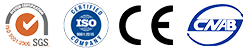
Versand:
Kontaktieren Sie uns um Versanddetails zu erhalten. Genießen Sie Garantie für pünktliche Lieferung.
Warum uns wählen
Zuverlässiger PartnerEinfacher Bestellprozess, Qualitätsprodukte und engagierter Support für Ihren Geschäftserfolg.
Einführung
Spark Plasma Sintering (SPS) ist ein schnelles Verfahren zur Materialvorbereitung, bei dem gepulster Strom zum Sintern von Materialien direkt in einer Form verwendet wird. Es kombiniert Plasmaaktivierung, Heißpressen und Widerstandserwärmung und bietet mehrere Vorteile gegenüber herkömmlichen Sinterverfahren. SPS ermöglicht eine gleichmäßige Erwärmung, hohe Heizraten, niedrige Sintertemperaturen, kurze Sinterzeiten und eine hohe Produktionseffizienz. Außerdem reinigt es die Oberflächen, verhindert das Kornwachstum und erleichtert die Herstellung einheitlicher und kontrollierbarer Strukturen. Im Vergleich zum konventionellen Sintern ist SPS umweltfreundlich, kosteneffizient und erfordert nur minimale Betriebszeiten.
Anwendung
Der Spark Plasma Sintering Furnace (SPS) ist ein vielseitiges und fortschrittliches Werkzeug, das in verschiedenen wissenschaftlichen und industriellen Anwendungen eingesetzt wird. Diese Technologie ist vor allem für ihre Fähigkeit bekannt, Materialien mit hoher Geschwindigkeit und hervorragender Kompaktheit zu sintern, was sie ideal für eine Reihe von speziellen Materialien und Prozessen macht. Nachfolgend sind die wichtigsten Anwendungsbereiche des SPS-Ofens aufgeführt:
- Sintern von Nanophasen-Materialien: Wird für die Konsolidierung von Materialien im Nanobereich verwendet, um deren mechanische und physikalische Eigenschaften zu verbessern.
- Funktional abgestufte Werkstoffe (FGM): Ermöglicht die Herstellung von Materialien mit räumlich variierenden Eigenschaften, die für fortschrittliche technische Anwendungen entscheidend sind.
- Nanoskalige thermoelektrische Materialien: Wesentlich für die Herstellung von Materialien, die in Energieumwandlungsgeräten verwendet werden.
- Seltene Erden-Dauermagnete: Entscheidend für die Herstellung von Hochleistungsmagneten, die in verschiedenen Elektronik- und Automobilanwendungen eingesetzt werden.
- Zielwerkstoffe: Werden bei der Herstellung von Materialien für die Dünnschichtabscheidung in der Elektronik und Optik verwendet.
- Nicht-Gleichgewichts-Materialien: Geeignet für die Synthese von Materialien, die nicht den traditionellen Gleichgewichts-Phasendiagrammen folgen.
- Medizinische Implantate: Hilft bei der Entwicklung von biokompatiblen Materialien mit präzisen mechanischen Eigenschaften für medizinische Geräte.
- Fügen und Umformen: Über das Sintern hinaus kann SPS zum Verbinden unterschiedlicher Materialien und zum Formen komplexer Formen verwendet werden.
- Oberflächenmodifizierung: Effektive Veränderung der Oberflächeneigenschaften von Materialien zur Verbesserung der Haltbarkeit oder Funktionalität.
- Festkörperelektrolyt- und elektrothermische Materialforschung: Ideal für die Untersuchung und Herstellung von Materialien, die in Festkörperbatterien und Wärmemanagementsystemen verwendet werden.
Merkmale
Der Spark Plasma Sintering Furnace (SPS) ist eine hochmoderne Lösung für das schnelle und effiziente Sintern einer Vielzahl von Materialien, einschließlich Metallen, Keramiken und Verbundwerkstoffen. Dieser fortschrittliche Ofen nutzt ein einzigartiges Drucksinterverfahren, bei dem Ein-Aus-Gleichstrom-Impulsströme zur Erzeugung von Entladungsplasma, Entladungsstoßdruck, Joule-Wärme und elektrischer Felddiffusion eingesetzt werden, wodurch der Sinterprozess erheblich verbessert wird. Nachfolgend sind die wichtigsten Merkmale des SPS-Ofens aufgeführt, wobei der Nutzen für den Kunden hervorgehoben wird:
- Automatisierte Programmsteuerung: Der SPS-Ofen verfügt über ein fortschrittliches Steuerungssystem, das kritische Prozesse wie die Steuerung von Sintertemperatur, Druck und Strom automatisiert. Diese Automatisierung gewährleistet nicht nur gleichbleibende und präzise Sinterbedingungen, sondern verringert auch die Notwendigkeit manueller Eingriffe, was Zeit spart und menschliche Fehler reduziert.
- Verbesserte Sicherheitsmaßnahmen: Ausgestattet mit einer Sicherheitsabschaltfunktion, schaltet sich der SPS-Ofen automatisch ab, wenn er abnormale Wassertemperaturen, Formschäden oder andere Notfälle feststellt. Diese proaktive Sicherheitsfunktion schützt sowohl die Anlage als auch den Bediener und gewährleistet eine sichere Arbeitsumgebung.
- Datenerfassungs- und Analysesystem: Der Ofen verfügt über ein hochentwickeltes Datenerfassungssystem, das kritische Prozessparameter wie Sinterspannung, Stromstärke, Steuerungstemperatur, angewandter Druck, Verdrängung und Vakuumgrad aufzeichnet und analysiert. Diese Fähigkeit ermöglicht eine detaillierte Verfolgung des Produktionsprozesses und hilft bei der Optimierung der Sinterbedingungen für eine bessere Produktqualität.
- Benutzerfreundliches Interface: Über ein großes LCD-Touch-Bedienfeld bietet der SPS-Ofen Echtzeit-Diagnosen und Statusaktualisierungen, einschließlich Verdrängungsdaten, Verriegelungsstatus, Alarmanzeigen und Druckeinstellungen. Diese intuitive Schnittstelle vereinfacht den Betrieb und die Wartung und erleichtert dem Bediener die effektive Steuerung des Sinterprozesses.
- Graphit-Hochdruckform: Die Verwendung einer robusten Graphitform im SPS-Ofen ermöglicht das Sintern unter hohem Druck, wodurch die Dichte und Qualität der gesinterten Produkte verbessert wird. Die Form ist mit einer Durchgangsbohrung für die Einführung von Thermoelementen versehen, die eine präzise Temperaturüberwachung während des Sintervorgangs ermöglichen.
Detail & Teile
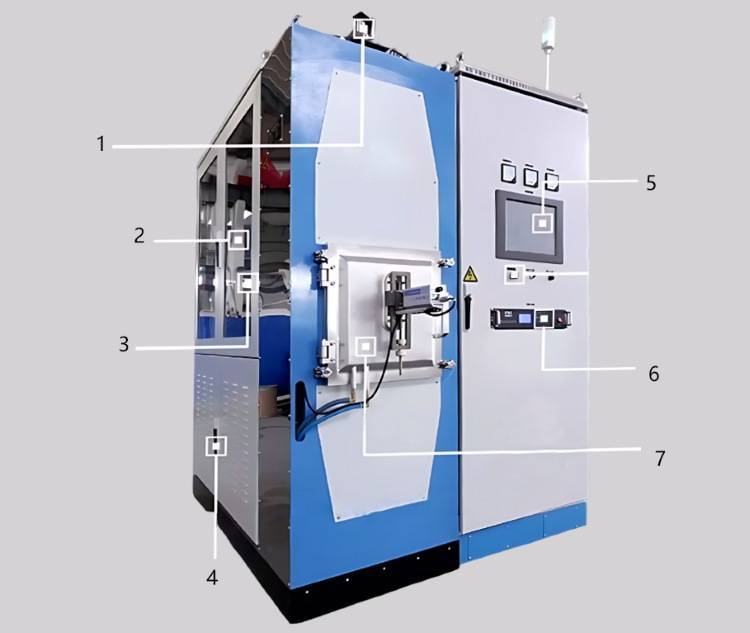
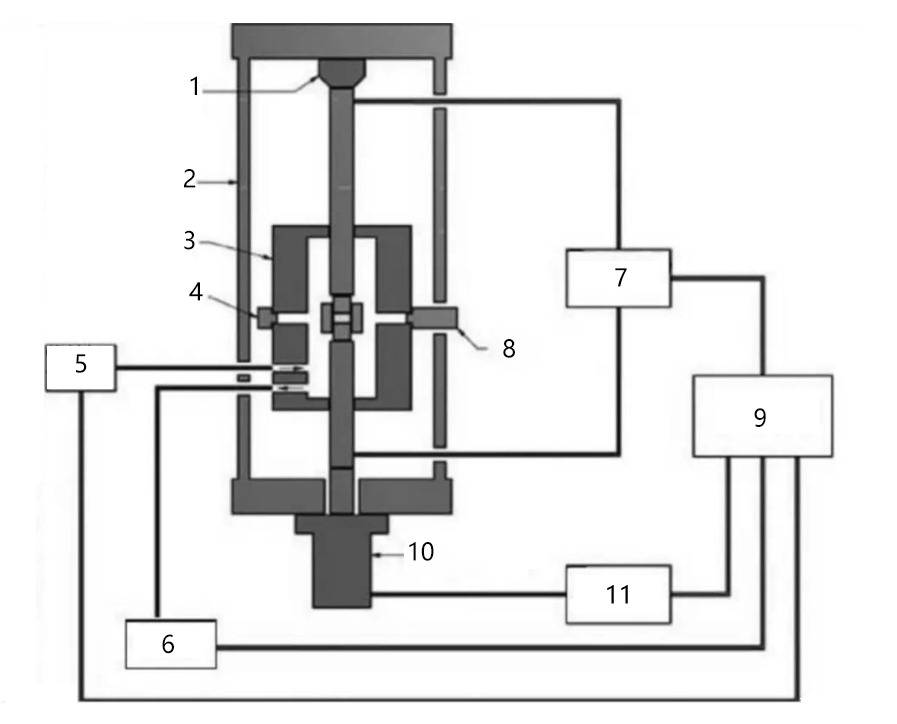
1. Beladeeinheit 2. Beschickungsrahmen 3. Vakuumkammer 4. Beobachtungsfenster 5. Inertgas-Kanal 6. Vakuumpumpe 7. Impulsschalter 8. Temperaturmesser 9. Steuerungssystem 10. Hydraulischer Zylinder 11. Hydraulisches System
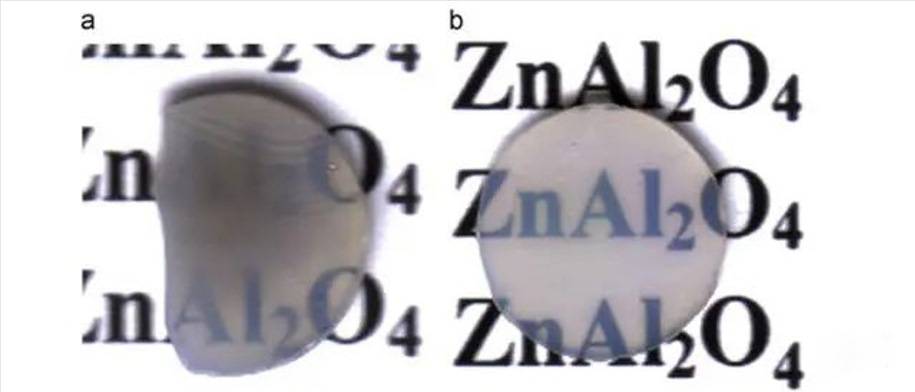
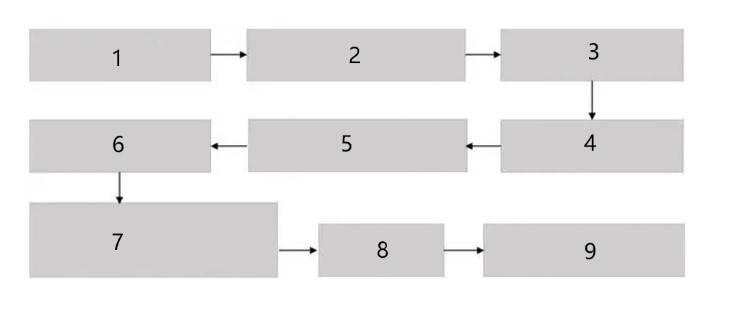
Prozessablauf des Funkenplasmasinterns (1.Geeignete Form auswählen 2.Benötigte Pulvermasse berechnen 3.Form füllen 4.Druck aufbringen 5.In das Plasmasintern einlegen 6.Statisches Druckgießen 7.Sinterparameter per Computer einstellen Plasma-Schnellsintern 8.Fertiges Produkt bemustern 9.Leistungsprüfung und Forschung)
Prinzip
Funkenplasmasintern (SPS) ist eine schnelle Materialvorbereitungsmethode, die Plasmaaktivierung, Heißpressen und Widerstandserhitzung kombiniert. Dabei wird ein Impulsstrom direkt durch die Form und die Pulverpartikel oder Schüttgutproben geleitet, um die Sinterung einzuleiten.
SPS nutzt die durch den Stromfluss erzeugte Joulesche Wärme, um die Probe zu erhitzen. Der Strom, der durch das Pulver fließt, erzeugt eine Funkenentladung zwischen benachbarten Partikeln, wodurch Gasmoleküle ionisiert und Positronen und Elektronen erzeugt werden. Das daraus resultierende Plasma reinigt und aktiviert die Partikeloberflächen, fördert die Materialwanderung und reduziert die Sintertemperatur und -zeit.
Die angelegte Impulsstromspannung sorgt für eine hohe Energiedichte, die ein schnelles Sintern und eine Dispersion des Entladungspunktes ermöglicht. Dieser einzigartige Heizmodus erleichtert die schnelle Abkühlung innerhalb der Kristallstruktur und ermöglicht die Herstellung hochwertiger amorpher und Nanomaterialien.
Vorteile
- Schnelles Sintern: SPS-Öfen bieten außergewöhnlich schnelle Heizraten, wodurch die Sinterzeit im Vergleich zu herkömmlichen Verfahren drastisch reduziert wird.
- Kompakter Aufbau: Die kompakte Bauweise von SPS-Öfen minimiert den Platzbedarf und ermöglicht einen effizienten Einsatz.
- Gleichmäßige Erwärmung: SPS-Öfen sorgen für eine gleichmäßige Erwärmung der gesamten Probe und damit für konstante Sinterergebnisse.
- Hohe Heizrate: Die hohe Aufheizrate von SPS-Öfen ermöglicht einen schnellen Temperaturanstieg und damit kürzere Prozesszeiten.
- Niedrige Sintertemperatur: SPS-Öfen arbeiten mit niedrigeren Sintertemperaturen als herkömmliche Verfahren, wodurch die Materialintegrität erhalten bleibt.
- Reinigung der Oberfläche: Die Plasmaentladung in SPS-Öfen reinigt die Oberfläche der Partikel, entfernt Verunreinigungen und verbessert die Bindung.
- Hemmung des Kornwachstums: SPS-Öfen minimieren das Kornwachstum, was zu einer gleichmäßigen und kontrollierbaren Produktstruktur führt.
- Vielseitige Materialkompatibilität: SPS-Öfen können eine breite Palette von Materialien sintern, darunter Metalle, Legierungen, Keramiken und Verbundwerkstoffe.
- Umweltverträglichkeit: Die SPS-Technologie ist umweltfreundlich und reduziert den Energieverbrauch und das Abfallaufkommen.
- Kosteneffizienz: SPS-Öfen bieten eine kosteneffiziente Lösung für das Hochgeschwindigkeitssintern und reduzieren die Produktionszeit und -kosten.
- Festkörper-Diffusions-Bonden: SPS-Öfen ermöglichen die Festkörperdiffusionsbindung zwischen Materialien und sorgen so für eine hohe Produktfestigkeit und Luftdichtheit.
- Fortschrittliche Materialsynthese: SPS-Öfen erleichtern die Synthese fortschrittlicher Materialien wie Nanomaterialien, funktional abgestufte Materialien und Seltenerdmagnete.
Technische Parameter
Der Spark Plasma Sintering Furnace (SPS) mit einem Druck von bis zu 20 Tonnen und einer Temperatur von bis zu 1600ºC ist ein Spark Plasma Sintering System, das für ein breites Spektrum an Materialforschung bis zu 1600ºC ausgelegt ist. Er kann zum Sintern, zur Sinterbindung, zur Oberflächenbehandlung und zur Synthese verwendet werden. Als Probenmaterial können Metalle, Keramiken, nanostrukturierte Materialien und amorphe Materialien verwendet werden. Dieses System eignet sich perfekt für die Erforschung von Festelektrolyten und elektrothermischen Materialien.
Ausstattung |
|
Temperaturregler |
|
Hydraulische Presse |
|
Vakuumkammer |
|
Abmessungen |
|
Technische Daten
Modell | KTSP-10T-5 | KTSP-20T-6 | KTSP-20T-10 | KTSP-50T-30 |
Nennleistung | 50Kw | 60Kw | 100Kw | 300Kw |
Ausgangsstrom | 0-5000A | 0-6000A | 0-10000A | 0-30000A |
Eingangsspannung | 0-10V | 0-10V | 0-10V | 0-10V |
Nenntemperatur | 2300℃ | |||
Nenndruck | 100KN | 200KN | 200KN | 500KN |
Größe der Probe | Ø30mm | Ø50mm | Ø100mm | Ø200mm |
Hub des Stößels | 100mm | 100mm | 100mm | 200mm |
Endvakuum | 1Pa |
Warnungen
Die Sicherheit des Bedieners steht an erster Stelle! Bitte bedienen Sie das Gerät mit Vorsicht. Das Arbeiten mit brennbaren, explosiven oder giftigen Gasen ist sehr gefährlich. Der Bediener muss alle erforderlichen Vorsichtsmaßnahmen treffen, bevor er das Gerät in Betrieb nimmt. Das Arbeiten mit Überdruck in den Reaktoren oder Kammern ist gefährlich. Der Bediener muss die Sicherheitsvorschriften strikt einhalten. Besondere Vorsicht ist auch beim Umgang mit luftreaktiven Materialien geboten, insbesondere unter Vakuum. Durch ein Leck kann Luft in das Gerät eindringen und eine heftige Reaktion hervorrufen.
Für Sie entworfen
KinTek bietet umfassenden, maßgeschneiderten Service und Ausrüstung für Kunden auf der ganzen Welt. Unsere spezialisierte Teamarbeit und unsere erfahrenen Ingenieure sind in der Lage, die kundenspezifischen Hardware- und Software-Ausrüstungsanforderungen zu erfüllen und unseren Kunden beim Aufbau der exklusiven und personalisierten Ausrüstung und Lösung zu helfen!
Bitte senden Sie uns Ihre Ideen, unsere Ingenieure sind jetzt für Sie bereit!
4.9
out of
5
The SPS furnace has brought about a remarkable improvement in our research capabilities, enabling us to conduct experiments and obtain results in a fraction of the time.
4.8
out of
5
This sintering furnace is a game-changer. Its speed, efficiency, and versatility have made it an indispensable tool in our lab, allowing us to explore new materials and processes.
4.7
out of
5
The SPS furnace is a well-built and reliable piece of equipment. Its user-friendly design and safety features make it an excellent choice for our research lab.
4.9
out of
5
The SPS furnace has exceeded our expectations. The quality of the sintered materials is exceptional, and the furnace's durability ensures consistent performance.
4.8
out of
5
The SPS furnace offers exceptional value for money. Its cost-effectiveness, combined with its high performance, makes it an attractive investment for any research institution.
4.7
out of
5
The SPS furnace is a testament to technological advancement. Its innovative features and groundbreaking capabilities have opened up new avenues of research for our team.
4.9
out of
5
The SPS furnace has significantly enhanced our research productivity. Its rapid sintering process has enabled us to complete experiments in a timely manner, leading to accelerated progress.
4.8
out of
5
The SPS furnace is a versatile tool that has facilitated the exploration of diverse materials and applications. Its ability to handle various materials sets it apart from other sintering furnaces.
4.7
out of
5
The SPS furnace is an invaluable asset to our lab. Its speed, reliability, and ease of use have made it a favorite among our researchers.
4.9
out of
5
The SPS furnace is a remarkable piece of equipment. Its ability to produce high-quality sintered materials in a matter of minutes is truly impressive.
Produkte
Spark-Plasma-Sinterofen SPS-Ofen
Fordern Sie ein Angebot an
Unser professionelles Team wird Ihnen innerhalb eines Werktages antworten. Sie können uns gerne kontaktieren!
Ähnliche Produkte
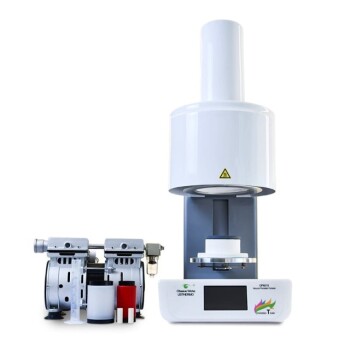
Erhalten Sie präzise zahnmedizinische Ergebnisse mit dem Dental-Vakuumpressofen. Automatische Temperaturkalibrierung, geräuscharmes Tablett und Touchscreen-Bedienung. Jetzt bestellen!
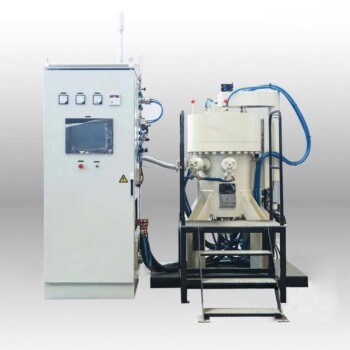
Der Druckluftsinterofen ist eine Hightech-Anlage, die häufig für das Sintern von Hochleistungskeramik verwendet wird. Er kombiniert die Techniken des Vakuumsinterns und des Drucksinterns, um Keramiken mit hoher Dichte und hoher Festigkeit herzustellen.
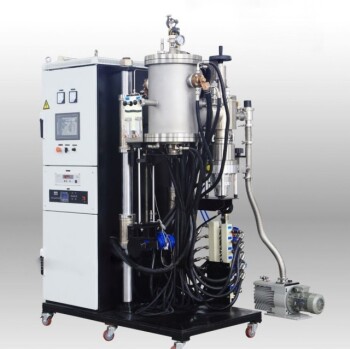
Kleiner Vakuum-Wolframdraht-Sinterofen
Der kleine Vakuum-Wolframdraht-Sinterofen ist ein kompakter experimenteller Vakuumofen, der speziell für Universitäten und wissenschaftliche Forschungsinstitute entwickelt wurde. Der Ofen verfügt über einen CNC-geschweißten Mantel und Vakuumleitungen, um einen leckagefreien Betrieb zu gewährleisten. Elektrische Schnellanschlüsse erleichtern den Standortwechsel und die Fehlerbehebung, und der standardmäßige elektrische Schaltschrank ist sicher und bequem zu bedienen.
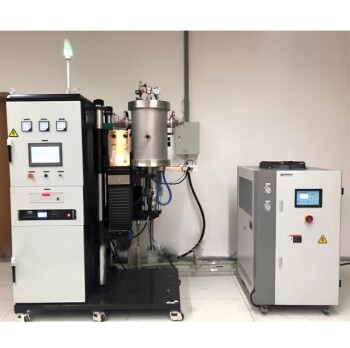
Vakuum-Molybdändraht-Sinterofen
Ein Vakuum-Molybdän-Draht-Sinterofen ist eine vertikale oder Schlafzimmerstruktur, die zum Entnehmen, Hartlöten, Sintern und Entgasen von Metallmaterialien unter Hochvakuum- und Hochtemperaturbedingungen geeignet ist. Es eignet sich auch zur Dehydroxylierungsbehandlung von Quarzmaterialien.
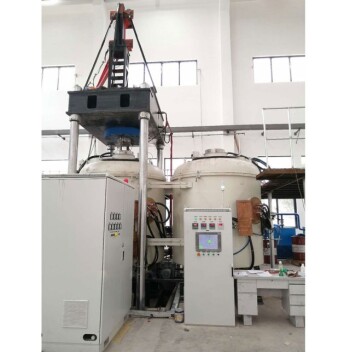
600T Vakuum-Induktions-Heißpressofen
Entdecken Sie den Vakuum-Induktions-Heißpressofen 600T, der für Hochtemperatur-Sinterexperimente im Vakuum oder in geschützten Atmosphären entwickelt wurde. Seine präzise Temperatur- und Druckregelung, der einstellbare Arbeitsdruck und die erweiterten Sicherheitsfunktionen machen es ideal für nichtmetallische Materialien, Kohlenstoffverbundwerkstoffe, Keramik und Metallpulver.
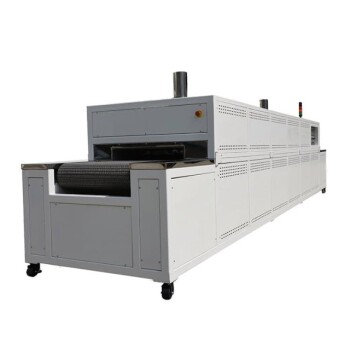
Maschenbandofen mit kontrollierter Atmosphäre
Entdecken Sie unseren KT-MB-Gitterbandsinterofen - perfekt für das Hochtemperatursintern von elektronischen Komponenten und Glasisolatoren. Erhältlich für Umgebungen mit offener oder kontrollierter Atmosphäre.
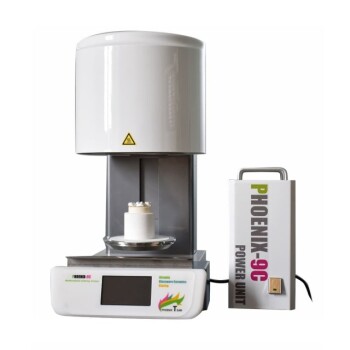
Dental-Sinterofen am Behandlungsstuhl mit Transformator
Erleben Sie erstklassiges Sintern mit dem Chairside-Sinterofen mit Transformator. Einfach zu bedienen, geräuschlose Palette und automatische Temperaturkalibrierung. Jetzt bestellen!
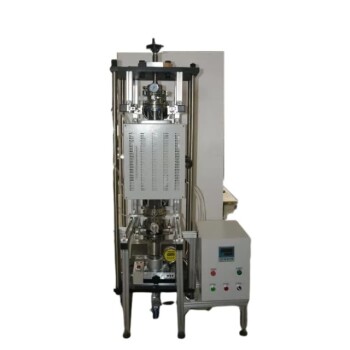
Reduzieren Sie den Formdruck und verkürzen Sie die Sinterzeit mit dem Vakuumrohr-Heißpressofen für hochdichte, feinkörnige Materialien. Ideal für refraktäre Metalle.
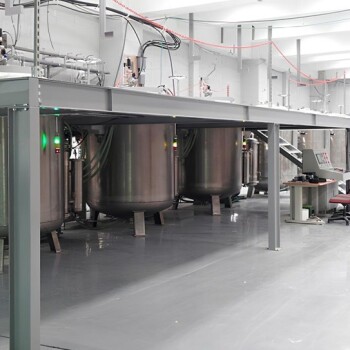
Negativmaterial-Graphitisierungsofen
Der Graphitisierungsofen für die Batterieproduktion hat eine gleichmäßige Temperatur und einen geringen Energieverbrauch. Graphitisierungsofen für negative Elektrodenmaterialien: eine effiziente Graphitisierungslösung für die Batterieproduktion und erweiterte Funktionen zur Verbesserung der Batterieleistung.
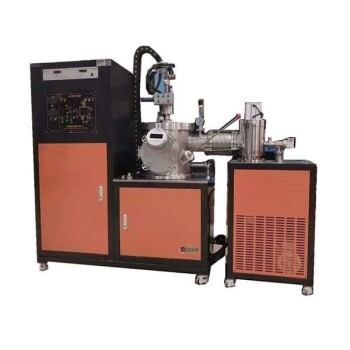
Vakuum-Lichtbogenofen. Induktionsschmelzofen
Entdecken Sie die Leistungsfähigkeit des Vakuum-Lichtbogenofens zum Schmelzen von aktiven und hochschmelzenden Metallen. Hohe Geschwindigkeit, bemerkenswerter Entgasungseffekt und frei von Verunreinigungen. Jetzt mehr erfahren!
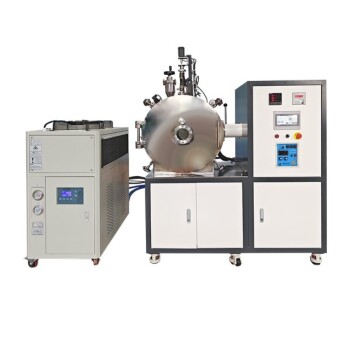
Vakuum-Induktionsschmelzofen im Labormaßstab
Mit unserem Vakuum-Induktionsschmelzofen erhalten Sie eine präzise Legierungszusammensetzung. Ideal für die Luft- und Raumfahrt, die Kernenergie und die Elektronikindustrie. Bestellen Sie jetzt für effektives Schmelzen und Gießen von Metallen und Legierungen.
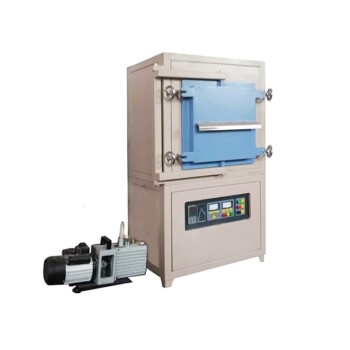
1700℃ Ofen mit kontrollierter Atmosphäre
KT-17A Ofen mit kontrollierter Atmosphäre: 1700℃ Heizung, Vakuumversiegelungstechnologie, PID-Temperaturregelung und vielseitiger TFT-Smart-Touchscreen-Controller für Labor- und Industrieanwendungen.
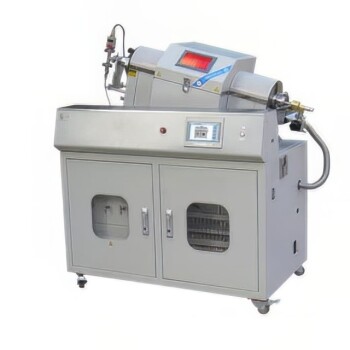
Schräge Rotationsrohrofenmaschine für plasmaunterstützte chemische Abscheidung (PECVD).
Wir stellen unseren geneigten rotierenden PECVD-Ofen für die präzise Dünnschichtabscheidung vor. Profitieren Sie von der automatischen Anpassung der Quelle, der programmierbaren PID-Temperaturregelung und der hochpräzisen MFC-Massendurchflussmesser-Steuerung. Integrierte Sicherheitsfunktionen sorgen für Sicherheit.
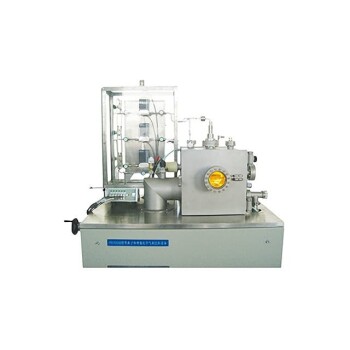
Beschichtungsanlage mit plasmaunterstützter Verdampfung (PECVD)
Verbessern Sie Ihr Beschichtungsverfahren mit PECVD-Beschichtungsanlagen. Ideal für LED, Leistungshalbleiter, MEMS und mehr. Beschichtet hochwertige feste Schichten bei niedrigen Temperaturen.
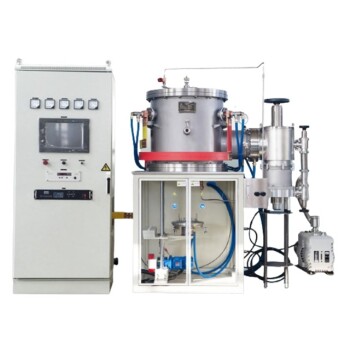
Erleben Sie den ultimativen Ofen für feuerfestes Metall mit unserem Wolfram-Vakuumofen. Kann 2200℃ erreichen und eignet sich perfekt zum Sintern von Hochleistungskeramik und hochschmelzenden Metallen. Bestellen Sie jetzt für hochwertige Ergebnisse.
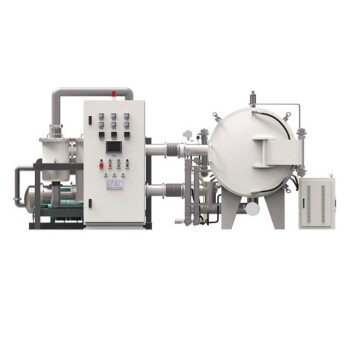
Horizontaler Hochtemperatur-Graphitisierungsofen
Horizontaler Graphitisierungsofen: Bei diesem Ofentyp sind die Heizelemente horizontal angeordnet, was eine gleichmäßige Erwärmung der Probe ermöglicht. Es eignet sich gut zum Graphitisieren großer oder sperriger Proben, die eine präzise Temperaturkontrolle und Gleichmäßigkeit erfordern.
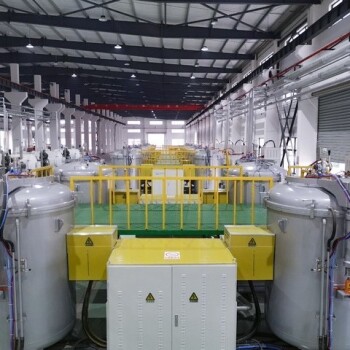
Vertikaler Hochtemperatur-Graphitisierungsofen
Vertikaler Hochtemperatur-Graphitisierungsofen zur Karbonisierung und Graphitisierung von Kohlenstoffmaterialien bis zu 3100 °C. Geeignet für die geformte Graphitisierung von Kohlenstofffaserfilamenten und anderen in einer Kohlenstoffumgebung gesinterten Materialien. Anwendungen in der Metallurgie, Elektronik und Luft- und Raumfahrt zur Herstellung hochwertiger Graphitprodukte wie Elektroden und Tiegel.
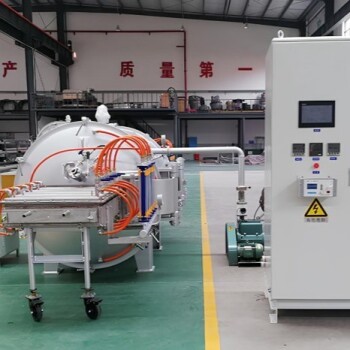
Kontinuierlicher Graphitierungsofen
Der Hochtemperatur-Graphitisierungsofen ist eine professionelle Ausrüstung zur Graphitisierungsbehandlung von Kohlenstoffmaterialien. Es handelt sich um eine Schlüsselausrüstung für die Herstellung hochwertiger Graphitprodukte. Es verfügt über eine hohe Temperatur, einen hohen Wirkungsgrad und eine gleichmäßige Erwärmung. Es eignet sich für verschiedene Hochtemperaturbehandlungen und Graphitierungsbehandlungen. Es wird häufig in der Metallurgie-, Elektronik-, Luft- und Raumfahrtindustrie usw. eingesetzt.
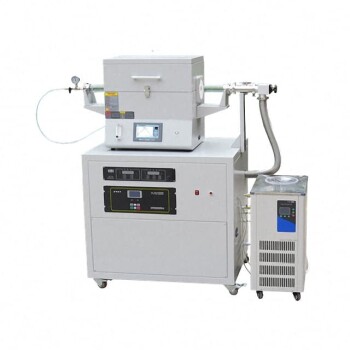
CVD-Rohrofen mit geteilter Kammer und Vakuumstation CVD-Maschine
Effizienter CVD-Ofen mit geteilter Kammer und Vakuumstation für intuitive Probenkontrolle und schnelles Abkühlen. Bis zu 1200℃ Höchsttemperatur mit präziser MFC-Massendurchflussregelung.
Ähnliche Artikel
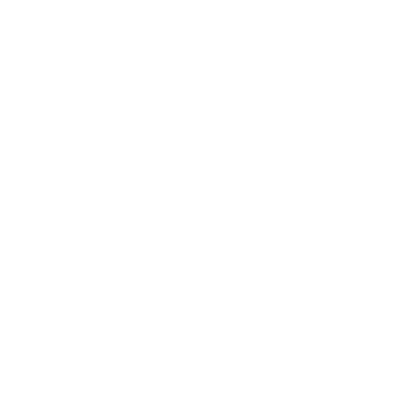
Spark Plasma Sintering Furnace: Der ultimative Leitfaden für SPS-Öfen
Entdecken Sie die Welt der Spark Plasma Sintering Furnaces (SPS). Dieser umfassende Leitfaden deckt alles ab, von den Vorteilen und Anwendungen bis hin zu Verfahren und Ausrüstung. Erfahren Sie, wie SPS-Öfen Ihren Sinterbetrieb revolutionieren können.
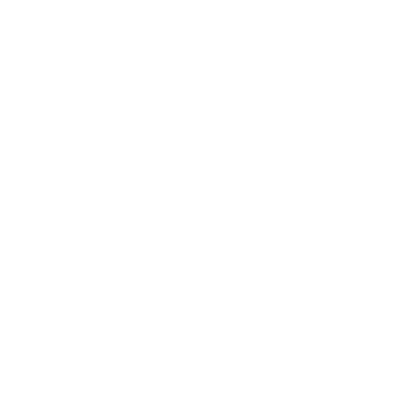
Erforschung des Spark Plasma Sintering Furnace (SPS): Technologie, Anwendungen und Vorteile
Tauchen Sie ein in den umfassenden Leitfaden zum Spark Plasma Sintering Furnace (SPS), der die Technologie, die Anwendungen in der Materialwissenschaft und die wesentlichen Vorteile gegenüber herkömmlichen Sinterverfahren behandelt.
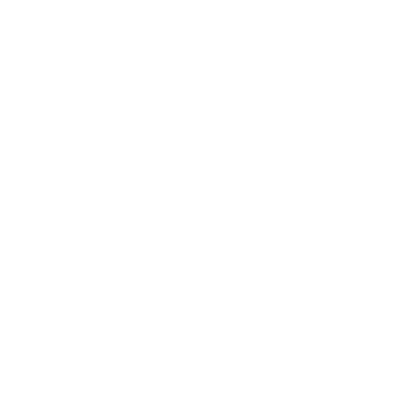
Erforschung der fortschrittlichen Möglichkeiten von Spark Plasma Sintering (SPS) Öfen
Tauchen Sie ein in die Welt der Spark Plasma Sintering (SPS)-Öfen, ihre innovative Technologie und ihre Anwendungen in der Materialwissenschaft. Erfahren Sie, wie SPS-Öfen den Sinterprozess mit hoher Geschwindigkeit, Effizienz und Präzision revolutionieren.
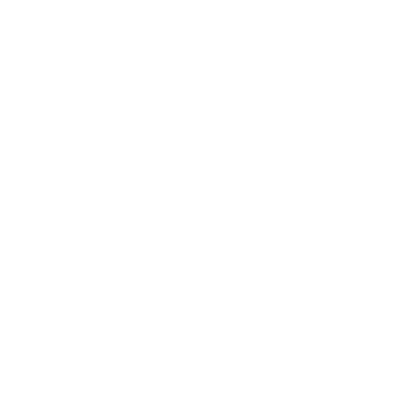
Umfassender Leitfaden für Spark Plasma Sintering Furnaces: Anwendungen, Merkmale und Vorteile
Entdecken Sie die fortschrittlichen Funktionen und Anwendungen von Spark Plasma Sintering Furnaces (SPS) in der Materialwissenschaft. Erfahren Sie, wie die SPS-Technologie schnelles, effizientes und vielseitiges Sintern für verschiedene Materialien ermöglicht.
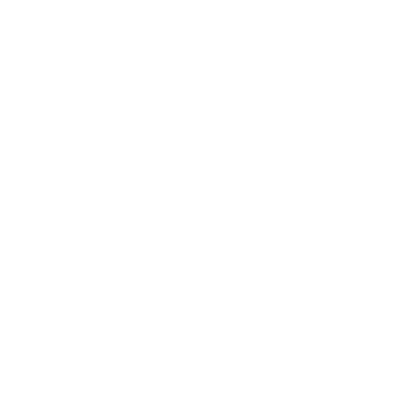
Die Vorteile von Öfen mit kontrollierter Atmosphäre für Sinter- und Glühprozesse
Sie sind wichtig, um Oxidation zu verhindern, das Kontaminationsrisiko zu verringern und die Eigenschaften der behandelten Materialien zu verbessern.
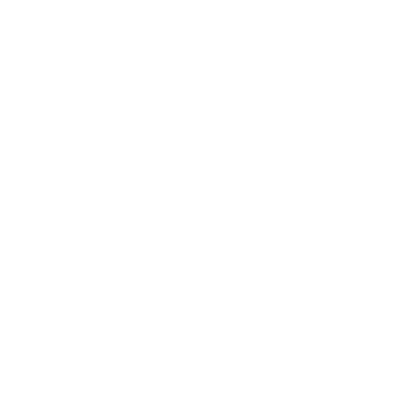
Gesättigte Kalomel-Referenzelektroden verstehen: Zusammensetzung, Einsatzmöglichkeiten und Überlegungen
Entdecken Sie den ausführlichen Leitfaden über gesättigte Kalomel-Referenzelektroden, einschließlich ihrer Zusammensetzung, Vorteile, Nachteile und Anwendungen. Ideal für Forscher und Labortechniker.
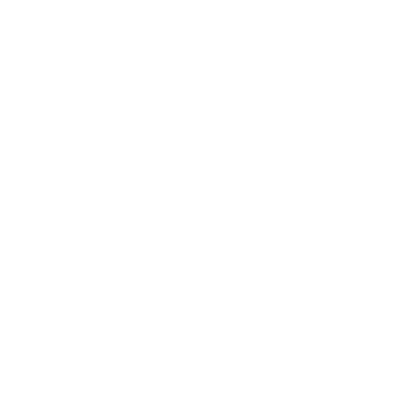
Dental-Sinteröfen: Der Einfluss auf die Qualität und Haltbarkeit der Restauration
Dental-Sinteröfen spielen eine entscheidende Rolle im Herstellungsprozess von Zahnkronen und anderen Restaurationen.
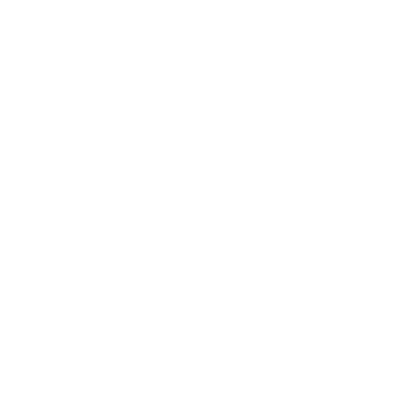
Eine eingehende Analyse der Heißpresstechnologie und ihrer Anwendungen
Heißpressen ist ein pulvermetallurgisches Verfahren mit hohem Druck und niedriger Verformungsrate, mit dem Pulver oder Pulverpresslinge bei hohen Temperaturen geformt werden, um Sinter- und Kriechprozesse auszulösen. Dabei werden durch die gleichzeitige Anwendung von Wärme und Druck harte und spröde Materialien hergestellt.
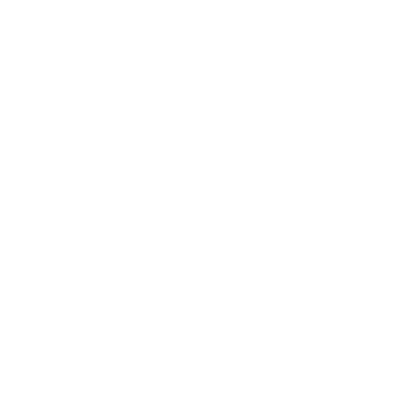
Der ultimative Leitfaden zum Vakuum-Drucksinterofen: Vorteile, Anwendungen und Arbeitsprinzip
Entdecken Sie die Vorteile, Anwendungen und das Funktionsprinzip des Vakuum-Drucksinterofens. Erfahren Sie, wie das Vakuumsintern saubere, glänzende Teile mit einer unglaublichen Designflexibilität und einer schnellen Durchlaufzeit erzeugt und wie es in der Lehre, der wissenschaftlichen Forschung und der Produktion eingesetzt wird. Erfahren Sie mehr über die präzise Einstellung und Überwachung der Prozessparameter und die Vorteile des Sinterns unter Vakuum und Druck. Erfahren Sie, wie sich der Vakuumsinterofen perfekt für Sinteranwendungen bei höheren Temperaturen und für das Sintern extrem reaktiver Materialien eignet.
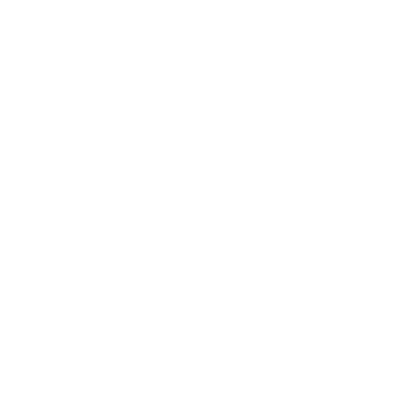
Die PECVD-Methode verstehen
PECVD ist ein plasmaunterstütztes chemisches Gasphasenabscheidungsverfahren, das häufig bei der Herstellung dünner Schichten für verschiedene Anwendungen eingesetzt wird.
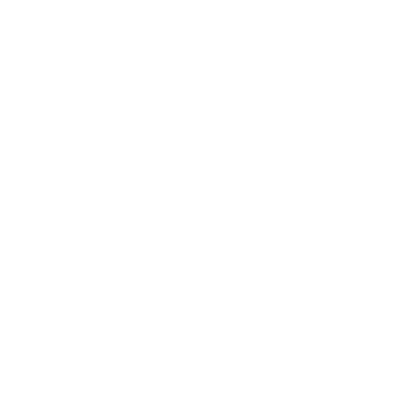
Eine vergleichende Untersuchung von Verdampfungs- und Sputtertechniken bei der Dünnschichtabscheidung
Die beiden am häufigsten verwendeten Techniken zur Dünnschichtabscheidung sind Aufdampfen und Sputtern.
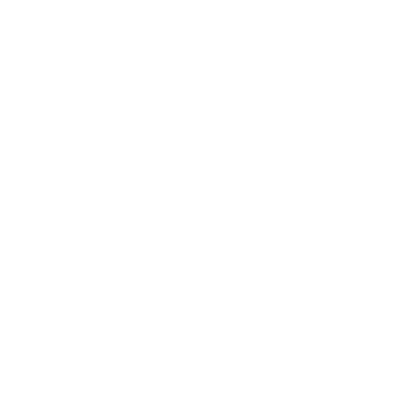
Die neuesten Fortschritte bei Zirkonoxid-Sinteröfen für Dentalanwendungen
Zirkonoxid-Sinteröfen wurden entwickelt, um Zahnärzten die Möglichkeit zu geben, Zahnrestaurationen mit höchster Präzision und Genauigkeit herzustellen.