Sputtern ist ein weit verbreitetes Verfahren zur Abscheidung von Dünnschichten, wobei die Dicke der abgeschiedenen Schicht in der Regel zwischen Angström und Mikron liegt.Die maximal erreichbare Schichtdicke hängt von mehreren Faktoren ab, u. a. von der Sputterzeit, der dem Target zugeführten Leistung, den Materialeigenschaften und den Prozessbedingungen.Obwohl das Sputtern vielseitig ist und gleichmäßige Beschichtungen erzeugen kann, gibt es Herausforderungen wie die Verunreinigung des Films, Temperaturbeschränkungen und Einschränkungen bei der genauen Kontrolle der Dicke.Diese Faktoren wirken sich gemeinsam auf die praktische Obergrenze der Schichtdicke bei Sputtering-Anwendungen aus.
Die wichtigsten Punkte werden erklärt:
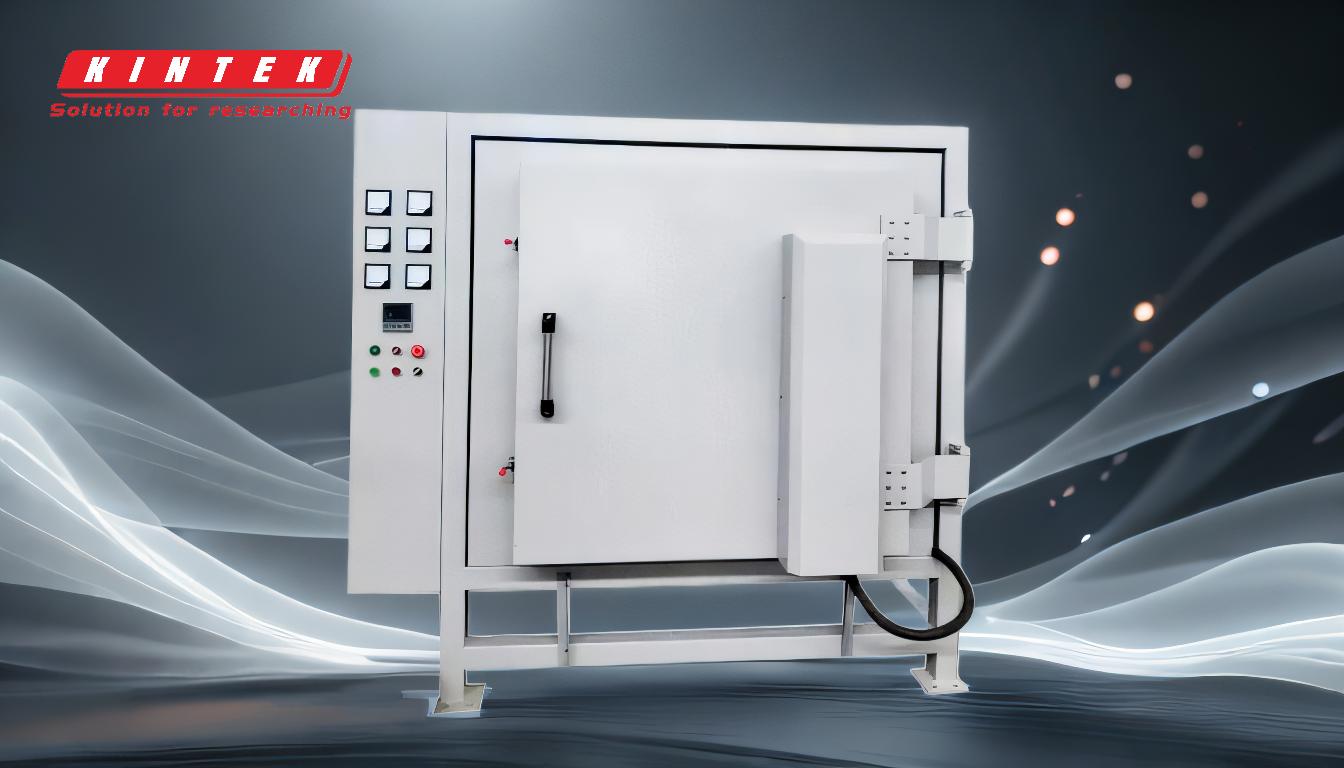
-
Typischer Dickenbereich beim Sputtern:
- Durch Sputtern werden Schichten mit einer Dicke von Angström bis zu Mikrometern .
- Dieser Bereich eignet sich für Anwendungen, die dünne Schichten erfordern, wie z. B. Halbleiter, optische Beschichtungen und Schutzschichten.
-
Faktoren, die die maximale Schichtdicke beeinflussen:
- Sputtering Zeit:Längere Abscheidungszeiten führen im Allgemeinen zu dickeren Schichten, aber dies wird durch praktische Erwägungen wie die Produktionseffizienz begrenzt.
- Auf das Target aufgebrachte Leistung:Höhere Leistungsstufen erhöhen die Sputterrate und ermöglichen dickere Ablagerungen, aber eine zu hohe Leistung kann zu Überhitzung und Verunreinigung führen.
- Materialeigenschaften:Die Schmelztemperatur und die Sputterausbeute des Targetmaterials wirken sich darauf aus, wie leicht es abgeschieden werden kann und wie dick die Schicht werden kann.
- Energie der Beschichtungspartikel:Partikel mit höherer Energie (von einigen zehn bis zu Tausenden von Elektronenvolt) können zu dickeren und dichteren Schichten beitragen.
-
Herausforderungen bei der Erreichung der maximalen Schichtdicke:
- Filmverschmutzung:Verunreinigungen aus dem Target oder der Umgebung können in den Film diffundieren und seine Qualität und Dicke einschränken.
- Temperaturbedingte Einschränkungen:Hohe Temperaturen während der Abscheidung können unerwünschte Spannungen während der Abkühlung verursachen, die die Integrität des Films beeinträchtigen.
- Gleichmäßigkeit und Reinheit:Mit zunehmender Schichtdicke wird es immer schwieriger, eine gleichmäßige Dicke und hohe Reinheit zu erreichen.
-
Praktische Beschränkungen:
- Kühlsysteme:Die Notwendigkeit von Kühlsystemen zur Steuerung der Wärmeentwicklung verringert die Produktionsraten und erhöht die Energiekosten.
- Auswahl des Materials:Materialien mit sehr hohen Schmelzpunkten oder geringer Sputterausbeute lassen sich nur schwer in dicken Schichten abscheiden.
- Bedeckung der Seitenwand:Bei Anwendungen, die einen Abhebeprozess erfordern, kann die Tendenz des Sputterns, sich an den Seitenwänden abzulagern, eine präzise Dickenkontrolle erschweren.
-
Anwendungen und gewünschte Schichtdicke:
- Konforme Beschichtungen:Sputtern ist ideal für Anwendungen, die gleichmäßige Beschichtungen auf komplexen Geometrien erfordern, bei denen die Kontrolle der Schichtdicke entscheidend ist.
- Geschichtete Strukturen:Mehrere Materialien können schichtweise aufgebracht werden, wobei die Dicke jeder Schicht sorgfältig kontrolliert wird, um spezifische funktionale Anforderungen zu erfüllen.
-
Schlussfolgerung zur maximalen Schichtdicke:
- Durch Sputtern können zwar theoretisch Schichten mit einer Dicke von bis zu mehreren Mikrometern abgeschieden werden, doch in der Praxis schränken Verunreinigungen, Temperaturmanagement und Probleme mit der Gleichmäßigkeit oft die erreichbare Dicke ein.
- Die maximale Schichtdicke hängt in hohem Maße von der jeweiligen Anwendung, dem Material und den Prozessparametern ab, so dass es wichtig ist, diese Faktoren für jeden Anwendungsfall zu optimieren.
Zusammenfassend lässt sich sagen, dass die maximale Schichtdicke beim Sputtern durch eine Kombination von Prozessparametern, Materialeigenschaften und praktischen Einschränkungen beeinflusst wird.Die Technik ist zwar vielseitig und ermöglicht die Herstellung von Schichten im Bereich von Angström bis zu Mikron, aber um dickere Schichten zu erreichen, müssen diese sorgfältig optimiert und die damit verbundenen Herausforderungen berücksichtigt werden.
Zusammenfassende Tabelle:
Aspekt | Details |
---|---|
Typischer Dickenbereich | Angström bis Mikrometer |
Schlüsselfaktoren | Sputtering-Zeit, Leistung, Materialeigenschaften und Energie der Beschichtungspartikel |
Herausforderungen | Filmverschmutzung, Temperaturbeschränkungen, Gleichmäßigkeit und Reinheit |
Praktische Beschränkungen | Kühlsysteme, Materialauswahl und Seitenwandabdeckung |
Anwendungen | Halbleiter, optische Beschichtungen, konforme Beschichtungen und geschichtete Strukturen |
Optimieren Sie Ihren Sputtering-Prozess für maximale Dicke. Kontaktieren Sie unsere Experten noch heute !