Das Verfahren der Dünnfilm-Tauchbeschichtung umfasst vier Hauptphasen: Eintauchen, Verweilen, Herausziehen und Trocknen.Bei diesem Verfahren wird eine dünne Schicht auf ein Substrat aufgebracht, indem es in eine Lösung getaucht und dann mit kontrollierter Geschwindigkeit herausgezogen wird.Das Verfahren wird häufig eingesetzt, um Oberflächeneigenschaften wie Leitfähigkeit, Verschleißfestigkeit, Korrosionsbeständigkeit und optische Eigenschaften je nach den Anforderungen der Anwendung zu verändern.Bei der Dünnschichtabscheidung werden im Allgemeinen dünne Schichten auf Substraten mit verschiedenen Techniken erzeugt und abgeschieden, darunter chemische und physikalische Abscheidungsverfahren.Das Tauchbeschichtungsverfahren ist eine einfache, aber wirksame Methode, um gleichmäßige dünne Schichten mit kontrollierter Dicke und Eigenschaften zu erzeugen.
Die wichtigsten Punkte werden erklärt:
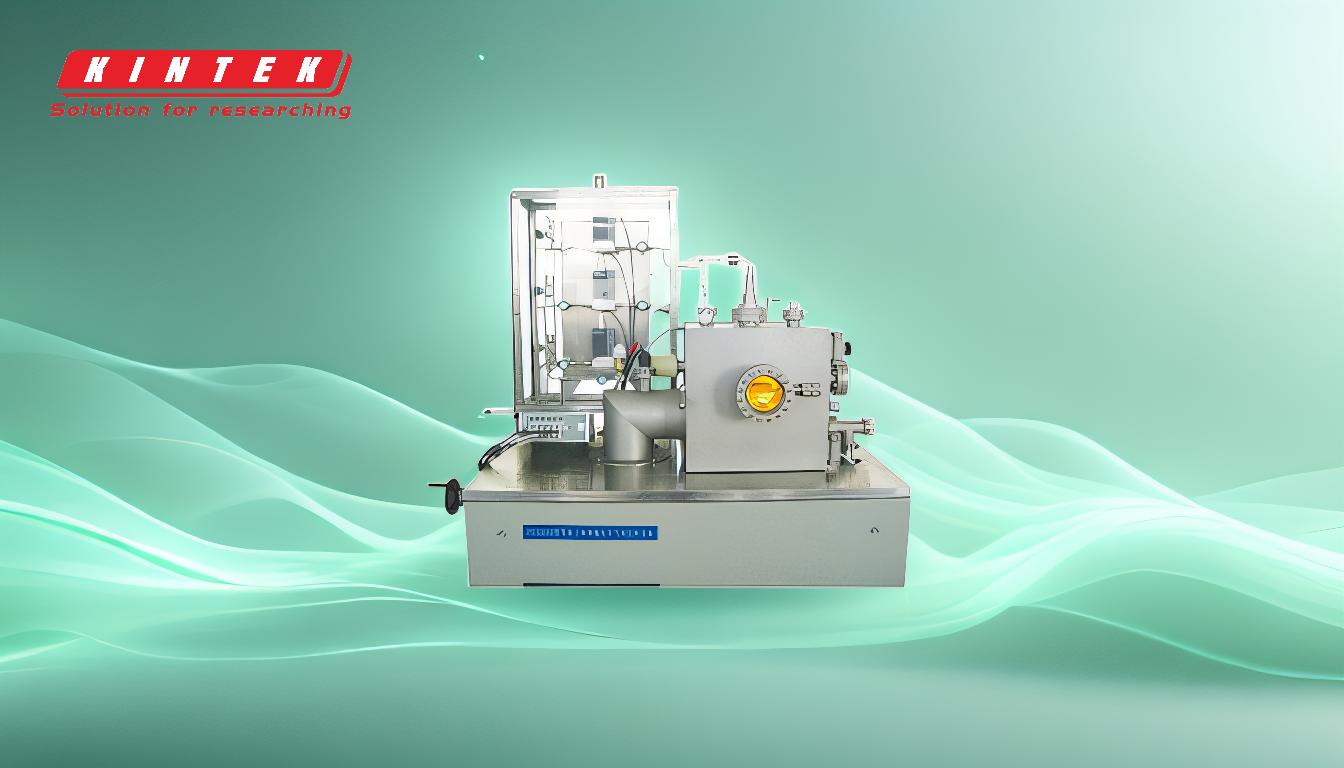
-
Stufen der Dünnfilm-Tauchbeschichtung:
- Eintauchen:Das Substrat wird mit kontrollierter Geschwindigkeit in die Beschichtungslösung getaucht.Dies gewährleistet einen gleichmäßigen Kontakt zwischen dem Substrat und der Lösung.
- Wohnung:Nach dem Eintauchen wird das Substrat für eine bestimmte Zeit in der Lösung gehalten, damit das Beschichtungsmaterial gut haften kann.
- Entnahme:Das Substrat wird dann mit kontrollierter Geschwindigkeit aus der Lösung herausgezogen.Die Entnahmegeschwindigkeit bestimmt die Dicke der Beschichtung; langsamere Geschwindigkeiten führen zu dickeren Schichten.
- Trocknung:Das beschichtete Substrat wird getrocknet, häufig unter kontrollierten Umgebungsbedingungen, um die Schicht zu verfestigen und die Haftung zu gewährleisten.
-
Zweck der Dünnschichtabscheidung:
- Die Abscheidung von Dünnschichten wird zur Veränderung der Oberflächeneigenschaften von Substraten verwendet, z. B. zur Verbesserung der Leitfähigkeit, der Verschleißfestigkeit, der Korrosionsbeständigkeit oder der optischen Eigenschaften.
- Sie ist in Branchen wie Elektronik, Optik und Werkstofftechnik weit verbreitet, um die Leistung von Komponenten zu verbessern.
-
Arten der Dünnschichtabscheidung:
- Chemische Abscheidung:Es handelt sich um eine chemische Reaktion an der Substratoberfläche, die zur Bildung einer festen Schicht führt.Beispiele sind die chemische Gasphasenabscheidung (CVD).
- Physikalische Abscheidung:Verwendung mechanischer, elektromechanischer oder thermodynamischer Verfahren zur Abscheidung dünner Schichten.Beispiele sind Sputtern, thermisches Verdampfen und Ionenstrahlabscheidung.
-
Schlüsselfaktoren, die die Tauchbeschichtung beeinflussen:
- Rückzugsgeschwindigkeit:Bestimmt die Dicke der Beschichtung.Langsamere Geschwindigkeiten führen zu dickeren Schichten, da die Lösung länger auf dem Substrat bleibt.
- Viskosität der Lösung:Lösungen mit höherer Viskosität führen in der Regel zu dickeren Beschichtungen.
- Trocknungsbedingungen:Eine kontrollierte Temperatur und Luftfeuchtigkeit während des Trocknens sind entscheidend, um Defekte wie Rissbildung oder ungleichmäßige Trocknung zu vermeiden.
-
Anwendungen der Dünnfilm-Tauchbeschichtung:
- Optische Beschichtungen:Zur Herstellung von Antireflexions- oder Reflexionsschichten auf Glas oder Linsen.
- Schützende Beschichtungen:Wird auf Metalle oder andere Materialien aufgetragen, um die Korrosions- oder Verschleißfestigkeit zu erhöhen.
- Elektronische Komponenten:Wird zur Abscheidung von leitenden oder isolierenden Schichten in Halbleiterbauelementen verwendet.
-
Vorteile der Tauchbeschichtung:
- Einfachheit und Kosteneffizienz im Vergleich zu anderen Beschichtungsmethoden.
- Fähigkeit, komplexe Formen und große Oberflächen gleichmäßig zu beschichten.
- Kontrolle der Schichtdicke durch Anpassung der Abzugsgeschwindigkeit und der Lösungseigenschaften.
-
Herausforderungen und Überlegungen:
- Das Erreichen einer gleichmäßigen Dicke auf unregelmäßig geformten Substraten kann eine Herausforderung sein.
- Das Verfahren kann eine genaue Kontrolle der Umgebungsbedingungen (z. B. Temperatur, Feuchtigkeit) erfordern, um Defekte zu vermeiden.
- Beschränkung auf bestimmte Materialien und Lösungen, die stabile Beschichtungen bilden können.
Durch das Verständnis der Phasen und Faktoren, die bei der Dünnfilm-Tauchbeschichtung eine Rolle spielen, können Hersteller den Prozess optimieren, um die gewünschten Filmeigenschaften für verschiedene Anwendungen zu erzielen.Dieses Verfahren ist besonders wertvoll wegen seiner Einfachheit, Vielseitigkeit und der Fähigkeit, hochwertige Beschichtungen auf einer Vielzahl von Substraten herzustellen.
Zusammenfassende Tabelle:
Aspekt | Einzelheiten |
---|---|
Stadien | Eintauchen, Verweilen, Entziehen, Trocknen |
Zweck | Veränderung von Oberflächeneigenschaften (Leitfähigkeit, Verschleißfestigkeit, Optik usw.) |
Arten der Abscheidung | Chemisch (z. B. CVD), physikalisch (z. B. Sputtern, thermische Verdampfung) |
Schlüsselfaktoren | Entnahmegeschwindigkeit, Viskosität der Lösung, Trocknungsbedingungen |
Anwendungen | Optische Beschichtungen, Schutzschichten, elektronische Bauteile |
Vorteile | Kostengünstige, gleichmäßige Beschichtungen, Kontrolle der Schichtdicke |
Herausforderungen | Gleichmäßigkeit bei unregelmäßigen Formen, präzise Umweltkontrolle erforderlich |
Optimieren Sie Ihren Dünnfilm-Tauchbeschichtungsprozess - Kontaktieren Sie noch heute unsere Experten für maßgeschneiderte Lösungen!