Die thermodynamische Triebkraft für die Sinterung ist in erster Linie die Verringerung der Oberflächenenergie, die eintritt, wenn die Oberfläche der Teilchen abnimmt und die Festkörper-Festkörper-Grenzflächen die Festkörper-Dampf-Grenzflächen ersetzen.Dieser Prozess wird durch die Tendenz des Systems angetrieben, einen niedrigeren Energiezustand zu erreichen.Die Krümmungsgradienten, die Oberflächenspannung und die Grenzflächenenergien spielen eine entscheidende Rolle bei der Erleichterung der atomaren Bewegung durch thermisch aktivierte Diffusionsmechanismen.Faktoren wie Temperatur, Partikelgröße und -zusammensetzung beeinflussen außerdem die Kinetik und die Ergebnisse der Sinterung.Letztendlich führt das Sintern zu einer Verdichtung und zu mikrostrukturellen Veränderungen, die zu einem stabileren und energieärmeren Materialzustand führen.
Die wichtigsten Punkte werden erklärt:
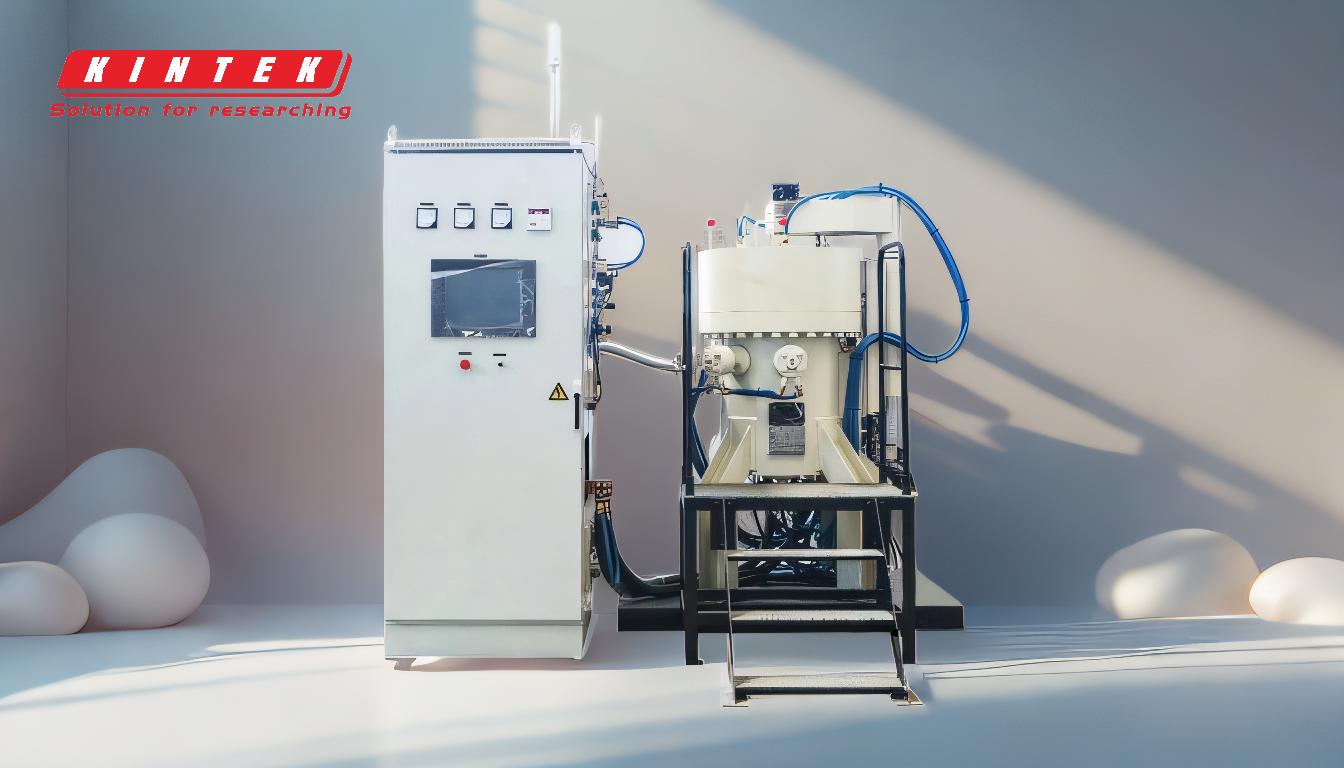
-
Reduktion der Oberflächenenergie:
- Die wichtigste thermodynamische Antriebskraft für das Sintern ist die Verringerung der Oberflächenenergie.Die Partikel in einem Pulversystem haben aufgrund ihres großen Oberflächen-Volumen-Verhältnisses eine hohe Oberflächenenergie.
- Mit fortschreitender Sinterung werden die Feststoff-Dampf-Grenzflächen durch Feststoff-Feststoff-Grenzflächen ersetzt, die eine geringere Energie aufweisen.Diese Verringerung der Oberflächenenergie führt das System in einen stabileren Zustand.
-
Krümmungsgradienten und Oberflächenspannung:
- Krümmungsgradienten zwischen den Teilchen führen zu Unterschieden im chemischen Potenzial, die die Diffusion von Atomen aus Bereichen mit hoher Krümmung (hoher Energie) in Bereiche mit niedriger Krümmung (niedriger Energie) vorantreiben.
- Die Oberflächenspannung wirkt als treibende Kraft für die Bewegung von Metallatomen und erleichtert die Umverteilung von Material und die Bildung von Verengungen zwischen den Teilchen.
-
Grenzflächenenergien:
- Der Ersatz von energiereichen Feststoff-Dampf-Grenzflächen durch energieärmere Feststoff-Feststoff-Grenzflächen verringert die gesamte freie Energie des Systems.
- Diese Energiereduzierung ist ein Schlüsselfaktor für die Verdichtung und mikrostrukturelle Entwicklung während des Sinterns.
-
Thermisch aktivierte Diffusionsmechanismen:
- Die Sinterung wird durch Festkörperdiffusionsmechanismen gesteuert, die thermisch aktiviert werden.Höhere Temperaturen erhöhen die Beweglichkeit der Atome und beschleunigen den Sinterprozess.
- Instrumente wie das Linseis-Stößeldilatometer werden zur Quantifizierung dieser Mechanismen und zur Modellierung des Sinterverhaltens eingesetzt.
-
Faktoren, die die Sinterung beeinflussen:
- Temperatur:Bestimmt die Kinetik der Sinterung und die endgültigen Materialeigenschaften.Höhere Temperaturen verbessern im Allgemeinen die Diffusion und Verdichtung.
- Aufheizrate:Beeinflusst die Verdichtungsgeschwindigkeit und die Entwicklung des Gefüges.
- Druck:Angewandter Druck kann die Umstrukturierung der Partikel fördern und die Porosität beseitigen, was zu einer schnelleren Verdichtung führt.
- Partikelgröße:Kleinere Partikel haben eine höhere Oberflächenenergie und sintern aufgrund ihrer größeren Oberfläche leichter.
- Zusammensetzung:Homogene Zusammensetzungen begünstigen eine bessere Verdichtung und ein einheitlicheres Gefüge.
-
Mikrostrukturelle Veränderungen:
- Während des Sinterns entwickelt sich die Mikrostruktur, da sich die Partikel verbinden und die Poren schrumpfen oder sich schließen.Dies führt zu einer erhöhten Dichte und verbesserten mechanischen Eigenschaften.
- Das endgültige Mikrogefüge wird durch die Sinterbedingungen und die ursprünglichen Eigenschaften des Pulvers beeinflusst.
Wenn man diese wichtigen Punkte versteht, kann man den Sinterprozess besser steuern, um die gewünschten Materialeigenschaften zu erreichen und die Leistung der gesinterten Bauteile zu optimieren.
Zusammenfassende Tabelle:
Hauptaspekt | Beschreibung |
---|---|
Verringerung der Oberflächenenergie | Wichtigste treibende Kraft; ersetzt hochenergetische Feststoff-Dampf-Grenzflächen durch Feststoff-Feststoff-Grenzflächen. |
Krümmungsgradienten | Treiben die atomare Diffusion von hochenergetischen zu niederenergetischen Bereichen an. |
Grenzflächenenergien | Festkörper-Grenzflächen mit niedrigerer Energie verringern die gesamte freie Energie. |
Diffusionsmechanismen | Thermisch aktiviert; höhere Temperaturen erhöhen die Beweglichkeit der Atome. |
Beeinflussende Faktoren | Temperatur, Heizrate, Druck, Partikelgröße und Zusammensetzung. |
Mikrostrukturelle Veränderungen | Führt zu Verdichtung, Porenschrumpfung und verbesserten mechanischen Eigenschaften. |
Optimieren Sie Ihren Sinterprozess mit Expertenwissen. Kontaktieren Sie uns noch heute !