Das Sputtern ist zwar eine weit verbreitete Technik für die Abscheidung dünner Schichten, hat jedoch einige bemerkenswerte Nachteile, die sich auf ihre Effizienz, Kosten und Eignung für bestimmte Anwendungen auswirken können.Zu diesen Nachteilen gehören niedrige Abscheideraten, hohe Substrattemperaturen, Schwierigkeiten bei der Integration mit Lift-off-Verfahren und Schwierigkeiten bei der Kontrolle der Reinheit und des Wachstums der Schichten.Außerdem können Sputteranlagen teuer sein, und das Verfahren kann Verunreinigungen in das Substrat einbringen.Das Verständnis dieser Einschränkungen ist entscheidend für eine fundierte Entscheidung bei der Auswahl einer Abscheidungsmethode.
Die wichtigsten Punkte werden erklärt:
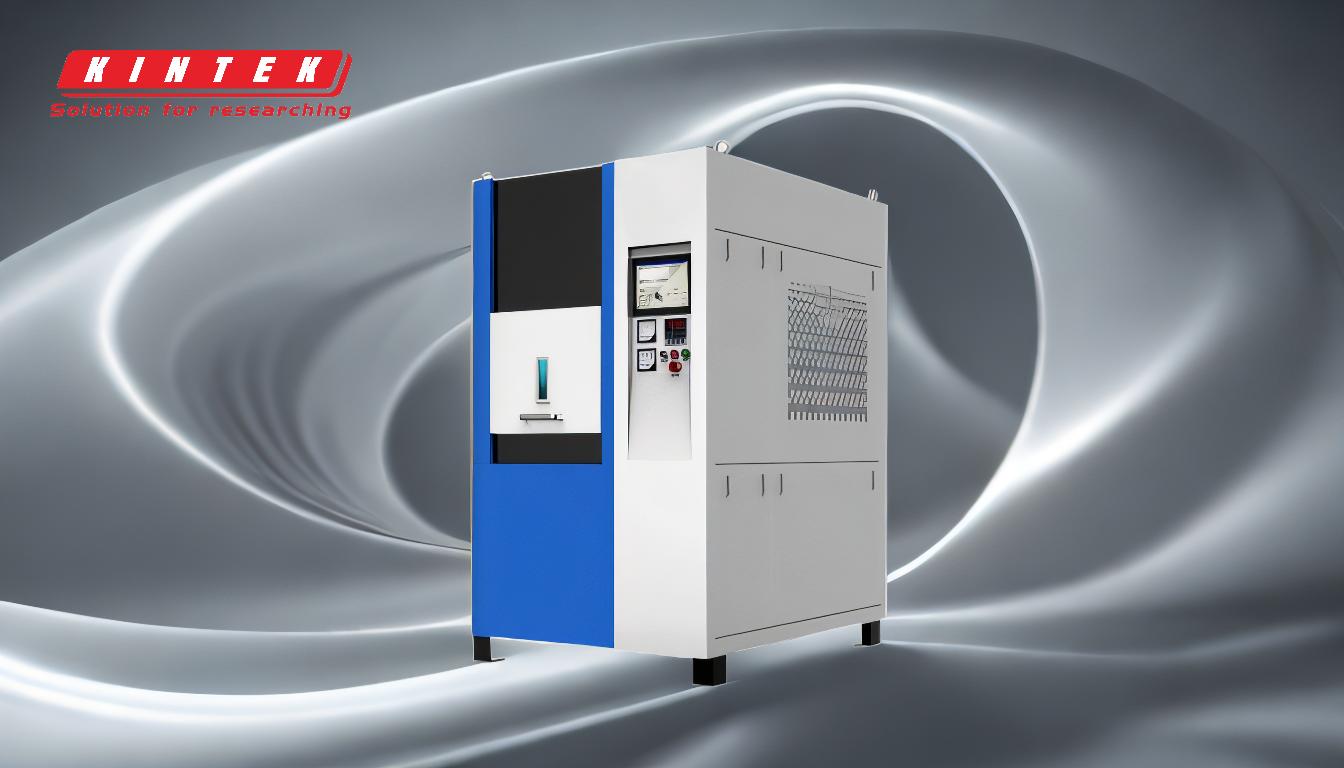
-
Niedrige Ablagerungsraten:
- Beim Sputtern sind die Abscheideraten im Allgemeinen niedriger als bei anderen Verfahren wie der thermischen Verdampfung.Dies kann besonders problematisch sein, wenn mit Materialien wie SiO2 gearbeitet wird, bei denen die Abscheidungsrate relativ langsam ist.
- Die niedrige Abscheidungsrate kann zu längeren Bearbeitungszeiten führen, was für Fertigungsumgebungen mit hohem Durchsatz nicht ideal ist.
-
Hohe Substraterwärmung Effekte:
- Während des Sputtering-Prozesses wird eine beträchtliche Menge an Energie in Form von Wärme auf das Substrat übertragen.Dies kann zu einem Anstieg der Substrattemperatur führen, was für temperaturempfindliche Materialien oder Substrate nachteilig sein kann.
- Hohe Substrattemperaturen können auch zu unerwünschten thermischen Spannungen oder zum Abbau organischer Materialien führen, wodurch die Palette der Materialien, die effektiv gesputtert werden können, eingeschränkt wird.
-
Schwierige Kombination mit Lift-Off-Prozessen:
- Die Integration des Sputterns in die für die Filmstrukturierung verwendeten Lift-off-Verfahren ist schwierig.Durch den diffusen Transport der gesputterten Atome ist es schwierig, eine vollständige Abschattung zu erreichen, was zu Kontaminationsproblemen führen kann.
- Diese Einschränkung kann die Herstellung strukturierter Schichten erschweren und zusätzliche Schritte oder alternative Abscheidungsmethoden erfordern, um die gewünschten Strukturen zu erreichen.
-
Verunreinigungen und Kontamination:
- Beim Sputtern herrscht im Vergleich zum Verdampfen ein geringeres Vakuum, was das Risiko erhöht, dass Verunreinigungen in das Substrat gelangen.Gasförmige Verunreinigungen können im Plasma aktiviert werden, was das Risiko einer Verunreinigung der Schicht weiter erhöht.
- Inerte Sputtergase wie Argon können ebenfalls zu Verunreinigungen in der wachsenden Schicht werden und die Eigenschaften und die Leistung der Schicht beeinträchtigen.
-
Hohe Kapital- und Betriebskosten:
- Sputtering-Anlagen sind oft teuer und erfordern erhebliche Investitionen.Außerdem kann das Verfahren hohe Betriebskosten verursachen, da spezielle Targets, Wartung und Energieverbrauch erforderlich sind.
- Der ineffiziente Materialeinsatz und die Notwendigkeit, die während des Prozesses erzeugte Wärme abzuführen, können die Kosten weiter erhöhen.
-
Herausforderungen bei der Kontrolle des schichtweisen Wachstums:
- Die aktive Kontrolle des schichtweisen Wachstums ist beim Sputtern schwieriger als bei anderen Verfahren wie der gepulsten Laserabscheidung.Dies kann eine präzise Kontrolle der Schichtdicke und -zusammensetzung erschweren.
- Die Komplexität der Steuerung der Gaszusammensetzung bei der reaktiven Kathodenzerstäubung stellt eine weitere Schwierigkeit dar, da eine unsachgemäße Steuerung zu einer Vergiftung des Targets und uneinheitlichen Schichteigenschaften führen kann.
-
Beschränkungen des Materials:
- Einige Materialien, insbesondere organische Feststoffe, werden durch Ionenbeschuss während des Sputterprozesses leicht abgebaut.Dies schränkt die Palette der Materialien ein, die mit dem Sputtering-Verfahren effektiv abgeschieden werden können.
- Außerdem kann die Auswahl der Beschichtungsmaterialien durch ihre Schmelztemperaturen eingeschränkt sein, was die Vielseitigkeit des Sputterverfahrens weiter einschränkt.
-
Komplexe Ausrüstung und Wartung:
- Sputtering-Systeme können sehr komplex sein und erfordern Hochdruckgeräte und spezielle Komponenten.Diese Komplexität kann zu erhöhten Wartungsanforderungen und potenziellen Ausfallzeiten führen.
- Die Notwendigkeit einer benutzerseitigen Wartung und die Beschränkungen der Prozessparameter können ebenfalls zu den betrieblichen Herausforderungen des Sputterns beitragen.
Zusammenfassend lässt sich sagen, dass das Sputtern zwar eine vielseitige und weit verbreitete Abscheidungstechnik ist, aber auch einige Nachteile mit sich bringt, die sorgfältig abgewogen werden müssen.Dazu gehören niedrige Abscheideraten, hohe Substrataufheizung, Schwierigkeiten bei der Integration mit Lift-off-Verfahren, Risiken von Verunreinigungen und Kontamination, hohe Kosten, Herausforderungen bei der Wachstumskontrolle, Materialbeschränkungen und komplexe Ausrüstungsanforderungen.Das Verständnis dieser Nachteile ist für die Auswahl der geeigneten Abscheidungsmethode für bestimmte Anwendungen von wesentlicher Bedeutung.
Zusammenfassende Tabelle:
Benachteiligung | Wichtigste Auswirkung |
---|---|
Niedrige Abscheideraten | Längere Verarbeitungszeiten, ungeeignet für die Fertigung mit hohem Durchsatz. |
Hohe Substraterwärmung | Nachteilig für temperaturempfindliche Materialien, verursacht thermischen Stress. |
Schwierigkeiten bei Lift-Off-Prozessen | Erschwert die Filmstrukturierung und führt zu Verunreinigungsproblemen. |
Verunreinigungen und Kontaminationen | Erhöhtes Risiko der Filmverunreinigung aufgrund des niedrigeren Vakuumbereichs. |
Hohe Investitions- und Betriebskosten | Teure Ausrüstung, hoher Wartungs- und Energieverbrauch. |
Herausforderungen bei der Wachstumskontrolle | Es ist schwierig, das Wachstum Schicht für Schicht präzise zu kontrollieren. |
Einschränkungen bei den Materialien | Begrenzte Auswahl an Materialien aufgrund von Problemen mit der Zersetzung und der Schmelztemperatur. |
Komplexe Ausrüstung und Wartung | Erfordert spezielle Komponenten, was zu längeren Ausfallzeiten führt. |
Benötigen Sie Hilfe bei der Auswahl der richtigen Abscheidungsmethode? Kontaktieren Sie noch heute unsere Experten für maßgeschneiderte Lösungen!