Bei der Kunststoffpyrolyse handelt es sich um einen Prozess, der Kunststoffabfälle in wertvolle Produkte wie Pyrolyseöl, -gas und Kohle umwandelt. Der in diesem Prozess verwendete Reaktortyp spielt eine entscheidende Rolle bei der Bestimmung der Effizienz, Skalierbarkeit und Eignung für bestimmte Kunststoffarten. Zu den gängigen Reaktoren gehören Wirbelschichtreaktoren, Festbettreaktoren und Zyklonreaktoren, die jeweils für unterschiedliche Pyrolyseprozesse wie schnelle oder langsame Pyrolyse ausgelegt sind. Diese Reaktoren bestehen aus hochtemperaturbeständigen Materialien wie Q245R- und Q345R-Stahl und gewährleisten Haltbarkeit und Wärmeübertragungseffizienz. Die Wahl des Reaktors hängt von Faktoren wie der Art des Ausgangsmaterials, den gewünschten Produkten und den Prozessanforderungen ab.
Wichtige Punkte erklärt:
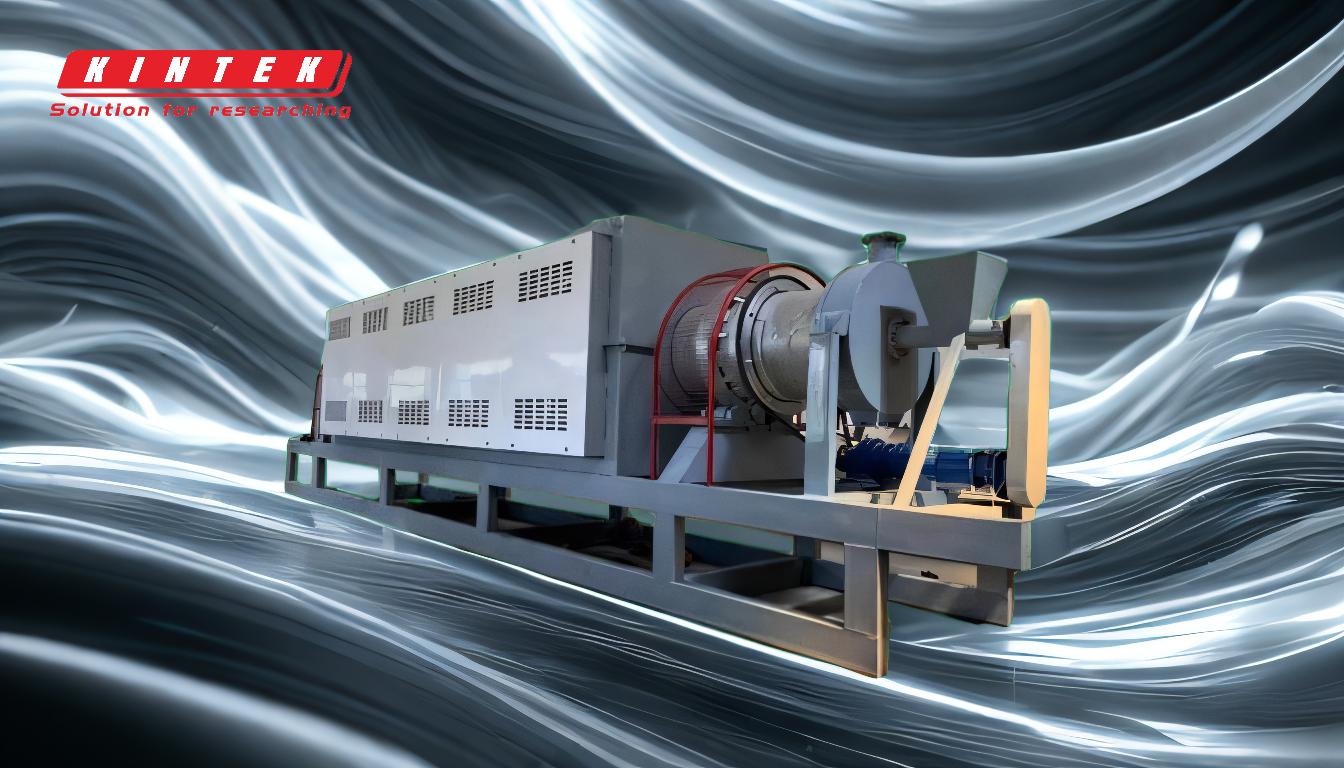
-
Arten von Reaktoren in der Kunststoffpyrolyse:
-
Wirbelschichtreaktoren:
- Diese Reaktoren suspendieren Kunststoffpartikel in einem Gas oder einer Flüssigkeit und sorgen so für eine gleichmäßige Erwärmung und eine effiziente Wärmeübertragung.
- Aufgrund ihrer Fähigkeit, hohe Aufheizraten und kurze Verweilzeiten zu bewältigen, eignen sie sich ideal für die schnelle Pyrolyse.
- Zu den Untertypen gehören sprudelnde Wirbelschichtpyrolysatoren und zirkulierende Wirbelschichtbetten, die eine verbesserte Kontrolle über die Wärmeübertragung und den Umgang mit dem Ausgangsmaterial bieten.
-
Festbettreaktoren:
- Diese Reaktoren verwenden ein stationäres Materialbett und eignen sich daher für langsame Pyrolyseprozesse.
- Sie sind einfacher in Design und Betrieb, weisen jedoch möglicherweise Einschränkungen bei der Wärmeübertragungseffizienz und Skalierbarkeit auf.
-
Zyklonreaktoren:
- Diese Reaktoren nutzen Zentrifugalkräfte zur Trennung und Verarbeitung von Materialien, wodurch sie sich effektiv für die Handhabung feiner Partikel eignen und einen hohen Durchsatz gewährleisten.
- Sie werden häufig in Verbindung mit anderen Reaktortypen verwendet, um die Gesamtsystemeffizienz zu verbessern.
-
Wirbelschichtreaktoren:
-
Materialeignung:
- Pyrolysereaktoren können ein breites Spektrum an Kunststoffen verarbeiten, darunter HDPE, LDPE, PP, PS und PC.
- Allerdings sind Kunststoffe wie PVC und PET aufgrund ihrer chemischen Zusammensetzung nicht geeignet, da sie bei der Pyrolyse schädliche Gase wie Chlor freisetzen können.
-
Konstruktion und Haltbarkeit:
- Reaktoren bestehen typischerweise aus hochtemperaturbeständigen Materialien wie Q245R- und Q345R-Stahl.
- Diese Materialien gewährleisten eine Lebensdauer von 5–8 Jahren und behalten die Effizienz der Wärmeübertragung auch unter extremen Bedingungen bei.
-
Prozessschritte in der Kunststoffpyrolyse:
- Der Prozess beginnt mit der Zerkleinerung und Trocknung von Kunststoffabfällen, gefolgt von der Vorverarbeitung zur Entfernung nichtplastischer Verunreinigungen.
- Beim Pyrolyseschritt wird der Kunststoff im Reaktor erhitzt, um ihn in Öl, Gas und Kohle zu zerlegen.
- Zu den Schritten nach der Pyrolyse gehören die Destillation und Reinigung des Pyrolyseöls, gefolgt von Lagerung und Versand.
-
Vorteile verschiedener Reaktortypen:
- Wirbelschichtreaktoren: Hohe Wärmeübertragungseffizienz, kurze Verweilzeit und Eignung für schnelle Pyrolyse.
- Festbettreaktoren: Einfaches Design und Betrieb, ideal für langsame Pyrolyse.
- Zyklonreaktoren: Effektiv zur Handhabung feiner Partikel und zur Verbesserung des Systemdurchsatzes.
Durch das Verständnis der verschiedenen Reaktortypen und ihrer spezifischen Anwendungen können Gerätekäufer fundierte Entscheidungen zur Optimierung ihrer Kunststoffpyrolyseprozesse treffen.
Übersichtstabelle:
Reaktortyp | Hauptmerkmale | Am besten für |
---|---|---|
Wirbelschicht | Hohe Wärmeübertragung, kurze Verweilzeit, bewältigt hohe Heizraten | Schnelle Pyrolyse |
Festes Bett | Einfaches Design, stationäres Bett, einfache Bedienung | Langsame Pyrolyse |
Zyklon | Zentrifugalkraft, verarbeitet feine Partikel, hoher Durchsatz | Feinpartikelverarbeitung |
Sind Sie bereit, Ihren Kunststoffpyrolyseprozess zu optimieren? Kontaktieren Sie noch heute unsere Experten für maßgeschneiderte Lösungen!