Das Sputtern ist zwar eine weit verbreitete Technik für die Abscheidung von Dünnschichten, hat jedoch einige bemerkenswerte Nachteile, die sich auf ihre Effizienz, Kosten und Eignung für bestimmte Anwendungen auswirken können.Zu diesen Nachteilen gehören niedrige Abscheideraten, eine hohe Erwärmung des Substrats, Schwierigkeiten bei der Kombination mit Lift-off-Verfahren, Kontaminationsrisiken und hohe Investitionskosten.Darüber hinaus ist das Sputtern bei Isoliermaterialien und organischen Feststoffen weniger effektiv und erfordert häufig komplexe Anlagen und eine sorgfältige Kontrolle der Prozessparameter.Das Verständnis dieser Einschränkungen ist für die Käufer von Anlagen und Verbrauchsmaterialien entscheidend, um fundierte Entscheidungen treffen zu können.
Die wichtigsten Punkte werden erklärt:
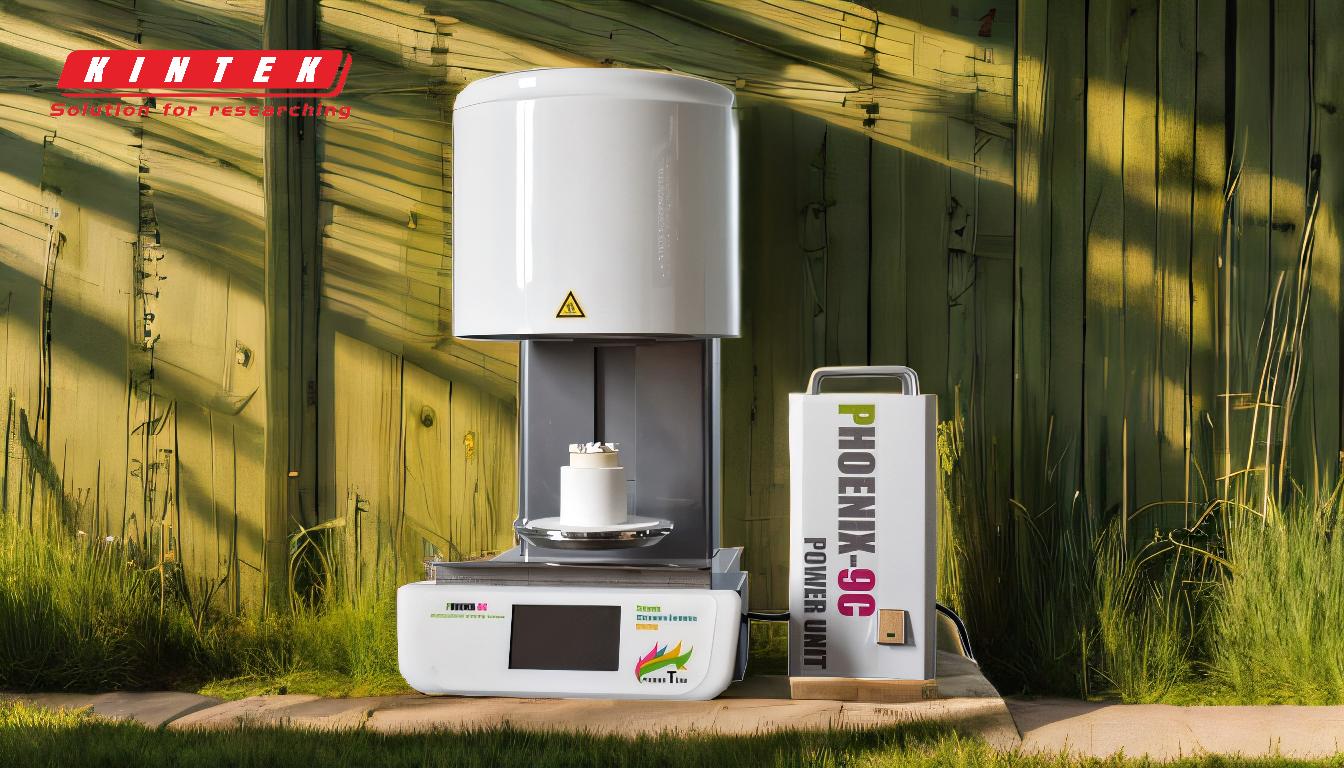
-
Niedrige Ablagerungsraten:
- Beim Sputtern sind die Abscheideraten in der Regel niedriger als bei anderen Verfahren wie der thermischen Verdampfung.Dies kann ein erheblicher Nachteil sein, wenn ein hoher Durchsatz erforderlich ist.
- Zum Beispiel haben Materialien wie SiO2 besonders niedrige Abscheidungsraten, was die Produktionsprozesse verlangsamen kann.
-
Hohe Substraterwärmung Effekte:
- Beim Sputtern entsteht viel Wärme, was zu hohen Substrattemperaturen führen kann.Dies kann bei temperaturempfindlichen Materialien problematisch sein oder wenn eine präzise thermische Kontrolle erforderlich ist.
- Hohe Substrattemperaturen können auch zu thermischer Belastung führen und die Qualität der abgeschiedenen Schicht beeinträchtigen.
-
Schwierigkeiten mit isolierenden Materialien:
- Das Sputtern ist für isolierende Materialien nicht gut geeignet, da sie Ladungen ansammeln können, was zu Lichtbogenbildung und anderen Problemen führt, die den Abscheidungsprozess stören.
- Diese Einschränkung macht den Einsatz alternativer Methoden oder zusätzlicher Geräte erforderlich, um isolierende Materialien effektiv zu behandeln.
-
Herausforderungen bei der Kombination mit Lift-Off-Verfahren:
- Aufgrund des diffusen Transports beim Sputtern ist es schwierig, eine vollständige Abschattung zu erreichen, die für Lift-off-Prozesse bei der Strukturierung von Schichten unerlässlich ist.
- Dies kann zu Kontaminationsproblemen führen und die Strukturierung von dünnen Schichten erschweren.
-
Kontaminationsrisiken:
- Beim Sputtern herrscht im Vergleich zum Verdampfen ein geringeres Vakuum, was das Risiko erhöht, dass Verunreinigungen in das Substrat gelangen.
- Gasförmige Verunreinigungen können im Plasma aktiviert werden, was das Risiko einer Filmverunreinigung weiter erhöht.
-
Hohe Investitionskosten:
- Die für das Sputtern erforderliche Ausrüstung ist oft komplex und teuer, was zu hohen Anfangskosten führt.
- Auch die Wartungs- und Betriebskosten können erheblich sein und die Gesamtkosten in die Höhe treiben.
-
Materialverschlechterung:
- Organische Feststoffe und andere empfindliche Materialien können durch den Ionenbeschuss während des Sputtering-Prozesses leicht abgebaut werden.
- Dies schränkt die Palette der Materialien ein, die durch Sputtern effektiv abgeschieden werden können.
-
Komplexe Ausrüstung und Prozesskontrolle:
- Sputtersysteme erfordern häufig Hochdruckgeräte und eine sorgfältige Kontrolle der Prozessparameter, wie z. B. der Gaszusammensetzung bei der reaktiven Sputterabscheidung.
- Die Komplexität der Ausrüstung und die Notwendigkeit einer präzisen Steuerung können die Schwierigkeiten und Kosten des Betriebs erhöhen.
-
Ineffizienter Materialeinsatz:
- Sputtertargets sind oft teuer, und das Verfahren kann im Hinblick auf den Materialverbrauch ineffizient sein.
- Der größte Teil der auf das Target auftreffenden Energie wird zu Wärme, die abgeführt werden muss, was die Ineffizienz noch verstärkt.
-
Fragen der Gleichmäßigkeit:
- Die Verteilung des Abscheidungsflusses beim Sputtern ist oft ungleichmäßig, was den Einsatz beweglicher Vorrichtungen erfordert, um eine gleichmäßige Schichtdicke zu erreichen.
- Dies kann den Abscheidungsprozess erschweren und die Qualität der fertigen Schicht beeinträchtigen.
Wenn die Käufer diese Nachteile kennen, können sie besser beurteilen, ob das Sputtern die richtige Wahl für ihre spezifischen Bedürfnisse ist, und gegebenenfalls alternative Methoden prüfen.
Zusammenfassende Tabelle:
Benachteiligung | Beschreibung |
---|---|
Niedrige Abscheideraten | Langsamer im Vergleich zu Methoden wie der thermischen Verdampfung, insbesondere bei Materialien wie SiO2. |
Hohe Substraterwärmung | Erzeugt beträchtliche Hitze, die thermischen Stress verursacht und temperaturempfindliche Materialien beeinträchtigt. |
Schwierigkeiten mit Isolatoren | Isoliermaterialien sammeln Ladung an, was zu Lichtbögen und Prozessunterbrechungen führt. |
Herausforderungen im Lift-Off-Prozess | Diffuser Transport erschwert die Filmstrukturierung und erhöht das Kontaminationsrisiko. |
Verunreinigungsrisiken | Geringerer Vakuumbereich erhöht Verunreinigungen; Plasma aktiviert gasförmige Verunreinigungen. |
Hohe Investitionskosten | Komplexe und teure Anlagen mit erheblichen Wartungs- und Betriebskosten. |
Zersetzung von Materialien | Organische Feststoffe und empfindliche Materialien werden durch den Ionenbeschuss abgebaut. |
Komplexe Ausrüstung und Kontrolle | Erfordert Hochdruckgeräte und eine präzise Steuerung der Parameter, was den Betrieb erschwert. |
Ineffiziente Materialnutzung | Teure Ziele und Energieineffizienz, da die meiste Energie in Wärme umgewandelt wird. |
Probleme mit der Gleichmäßigkeit | Ein ungleichmäßiges Abscheidungsflussmittel erfordert bewegliche Vorrichtungen für eine gleichmäßige Schichtdicke. |
Benötigen Sie Hilfe bei der Auswahl des richtigen Verfahrens zur Dünnschichtabscheidung? Kontaktieren Sie noch heute unsere Experten für maßgeschneiderte Lösungen!