Das Sputtern ist zwar eine weit verbreitete Technik für die Abscheidung dünner Schichten, hat jedoch einige bemerkenswerte Einschränkungen, die sich auf die Effizienz, die Kosten und die Qualität der abgeschiedenen Schichten auswirken. Zu diesen Einschränkungen gehören Probleme wie die Verunreinigung der Schichten, niedrige Abscheideraten, hoher Energieverbrauch, Schwierigkeiten bei der Kontrolle der Schichtdicke und Probleme bei der Materialauswahl. Darüber hinaus kann das Verfahren aufgrund des Bedarfs an Spezialausrüstung und -wartung teuer sein, und es ist möglicherweise nicht für alle Arten von Materialien oder Anwendungen geeignet. Das Verständnis dieser Einschränkungen ist entscheidend für die Optimierung des Sputterverfahrens und die Auswahl der geeigneten Abscheidungsmethode für bestimmte Anforderungen.
Die wichtigsten Punkte werden erklärt:
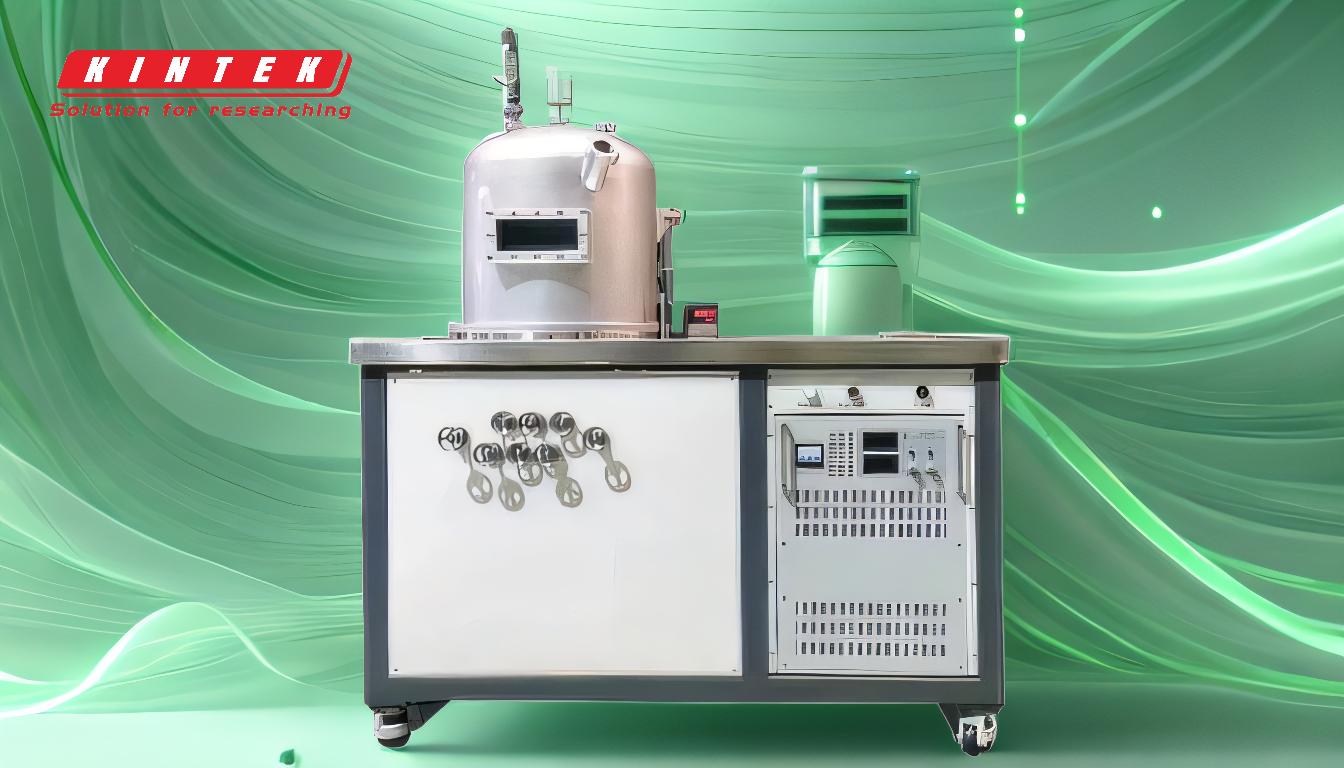
-
Filmverschmutzung:
- Verunreinigungen aus Ausgangsmaterialien: Während des Sputterprozesses können Verunreinigungen aus den Ausgangsmaterialien in die Schicht diffundieren und zu Verunreinigungen führen. Dies ist besonders problematisch, wenn die Ausgangsmaterialien flüchtige Verunreinigungen enthalten, die verdampfen und sich auf dem Substrat ablagern.
- Gasförmige Schadstoffe: Das beim Sputtern verwendete Plasma kann gasförmige Verunreinigungen aktivieren, die dann in die wachsende Schicht eingearbeitet werden, was das Risiko einer Verunreinigung weiter erhöht.
- Inertes Gas Verunreinigungen: Inerte Sputtergase, wie z. B. Argon, können ebenfalls zu Verunreinigungen in der Schicht werden, wenn sie nicht wirksam aus der Beschichtungskammer entfernt werden.
-
Niedrige Ablagerungsraten:
- Im Vergleich zur thermischen Verdampfung: Sputtern hat im Allgemeinen niedrigere Abscheideraten als thermische Verdampfungstechniken. Dies kann zu längeren Bearbeitungszeiten führen, die für Produktionsumgebungen mit hohem Durchsatz möglicherweise nicht geeignet sind.
- Ungleichmäßiger Ablagerungsfluss: Die Verteilung der gesputterten Atome ist oft ungleichmäßig, was den Einsatz beweglicher Vorrichtungen oder anderer Methoden erfordert, um eine gleichmäßige Schichtdicke auf dem Substrat zu erreichen.
-
Energieverbrauch und Wärmemanagement:
- Hohe Energiekosten: Ein erheblicher Teil der auf das Target auftreffenden Energie wird in Wärme umgewandelt, die wirksam abgeführt werden muss, um Schäden an den Geräten zu vermeiden und die Prozessstabilität zu erhalten. Dies macht den Einsatz von Kühlsystemen erforderlich, die den Energieverbrauch und die Betriebskosten erhöhen.
- Anforderungen an das Kühlsystem: Der Bedarf an Kühlsystemen erhöht nicht nur die Energiekosten, sondern senkt auch die Gesamtproduktionsrate, da das System regelmäßig abkühlen muss, um eine Überhitzung zu vermeiden.
-
Kontrolle über die Filmdicke:
- Schwierigkeit beim schichtweisen Wachstum: Im Vergleich zu anderen Abscheidungsmethoden wie der gepulsten Laserabscheidung ist das Sputtern für ein präzises schichtweises Wachstum weniger effektiv. Dies macht es schwierig, die Schichtdicke genau zu kontrollieren, insbesondere bei komplexen Mehrschichtstrukturen.
- Diffuser Transport von gesputterten Atomen: Die diffuse Natur des gesputterten Atomtransports macht es schwierig, eine vollständige Abschattung zu erreichen, die für bestimmte Schichtstrukturierungstechniken wie Lift-off-Verfahren erforderlich ist.
-
Materialauswahl und Zielkosten:
- Beschränkungen aufgrund der Schmelztemperatur: Die Auswahl der Beschichtungsmaterialien wird häufig durch ihre Schmelztemperaturen eingeschränkt. Materialien mit sehr hohen Schmelzpunkten eignen sich möglicherweise nicht für das Sputtern, da sie einen höheren Energieeinsatz erfordern und zu einem erhöhten Kontaminationsrisiko führen können.
- Teure Ziele: Sputtertargets sind oft teuer, und der Materialeinsatz kann ineffizient sein, da nicht das gesamte gesputterte Material auf das Substrat aufgebracht wird. Diese Ineffizienz erhöht die Gesamtkosten des Prozesses.
-
Prozessparameter und Wartung:
- Hohe Betriebsdrücke: Herkömmliche Sputtering-Verfahren arbeiten in der Regel mit höheren Drücken, was zu Problemen wie der Permeation durch Elastomerdichtungen und Schwierigkeiten bei der Aufrechterhaltung einer stabilen Vakuumumgebung führen kann.
- Benutzerdefinierte Wartung: Der Sputterprozess erfordert eine regelmäßige Wartung, die sowohl zeit- als auch kostenaufwändig sein kann. Die Notwendigkeit einer benutzerseitigen Wartung erhöht die betriebliche Komplexität und kann die Gesamteffizienz des Prozesses beeinträchtigen.
-
Herausforderungen beim reaktiven Sputtern:
- Kontrolle der Gaszusammensetzung: Bei der reaktiven Kathodenzerstäubung muss die Gaszusammensetzung sorgfältig kontrolliert werden, um eine Vergiftung des Targets zu verhindern, bei der das Targetmaterial mit dem reaktiven Gas reagiert und eine Verbindung bildet, die die Zerstäubungsrate verringert und die Schichtqualität beeinträchtigt.
- Fragen der Homogenität: Bei großen rechteckigen Kathoden (größer als 1 Meter) kann es schwierig sein, eine gleichmäßige Plasmadichte und folglich eine gleichmäßige Schichtdickenverteilung zu erreichen. Diese Ungleichmäßigkeit kann zu Schwankungen der Schichteigenschaften auf dem Substrat führen.
Zusammenfassend lässt sich sagen, dass das Sputtern zwar ein vielseitiges und weit verbreitetes Verfahren zur Abscheidung von Dünnschichten ist, dass es aber auch seine Grenzen hat. Dazu gehören Probleme im Zusammenhang mit der Verunreinigung der Schichten, niedrige Abscheidungsraten, hoher Energieverbrauch, Schwierigkeiten bei der Kontrolle der Schichtdicke und Herausforderungen bei der Materialauswahl. Außerdem kann das Verfahren aufgrund des Bedarfs an Spezialausrüstung und Wartung teuer sein. Das Verständnis dieser Einschränkungen ist für die Optimierung des Sputterprozesses und die Auswahl der geeigneten Abscheidungsmethode für bestimmte Anwendungen von wesentlicher Bedeutung.
Zusammenfassende Tabelle:
Begrenzung | Wichtige Details |
---|---|
Filmverschmutzung | Verunreinigungen durch Ausgangsstoffe, gasförmige Verunreinigungen, Verunreinigungen durch Inertgas. |
Niedrige Ablagerungsraten | Langsamer als thermische Verdampfung, ungleichmäßiger Ablagerungsfluss. |
Hoher Energieverbrauch | Erhebliche Wärmeentwicklung, erfordert Kühlsysteme, erhöht die Betriebskosten. |
Kontrolle über die Filmdicke | Schwierigkeiten beim schichtweisen Wachstum, diffuser Transport der gesputterten Atome. |
Auswahl des Materials | Begrenzt durch Schmelztemperaturen, teure Ziele, ineffiziente Materialverwendung. |
Prozess-Parameter | Hohe Betriebsdrücke, benutzerseitige Wartung, komplexe Betriebsanforderungen. |
Herausforderungen beim reaktiven Sputtern | Kontrolle der Gaszusammensetzung, Gleichmäßigkeitsprobleme bei großen Kathoden. |
Benötigen Sie Hilfe bei der Optimierung Ihres Sputtering-Prozesses? Kontaktieren Sie unsere Experten noch heute für maßgeschneiderte Lösungen!