Das Sputtern ist zwar eine weit verbreitete Technik zur Abscheidung von Dünnschichten, hat aber einige bemerkenswerte Nachteile.Dazu gehören hohe Investitionskosten, relativ niedrige Abscheidungsraten für bestimmte Materialien, die Anfälligkeit für Schichtverunreinigungen und Schwierigkeiten bei der Kontrolle der Schichtdicke.Darüber hinaus kann das Sputtern empfindliche Materialien wie organische Feststoffe durch Ionenbeschuss schädigen und erfordert eine komplexe Ausrüstung und Wartung.Das Verfahren stößt auch bei der Materialauswahl und der Integration mit anderen Techniken wie Lift-off-Verfahren an Grenzen.Aufgrund dieser Nachteile ist das Sputtern für bestimmte Anwendungen weniger geeignet, insbesondere wenn Präzision, Kosteneffizienz oder Materialkompatibilität entscheidend sind.
Die wichtigsten Punkte erklärt:
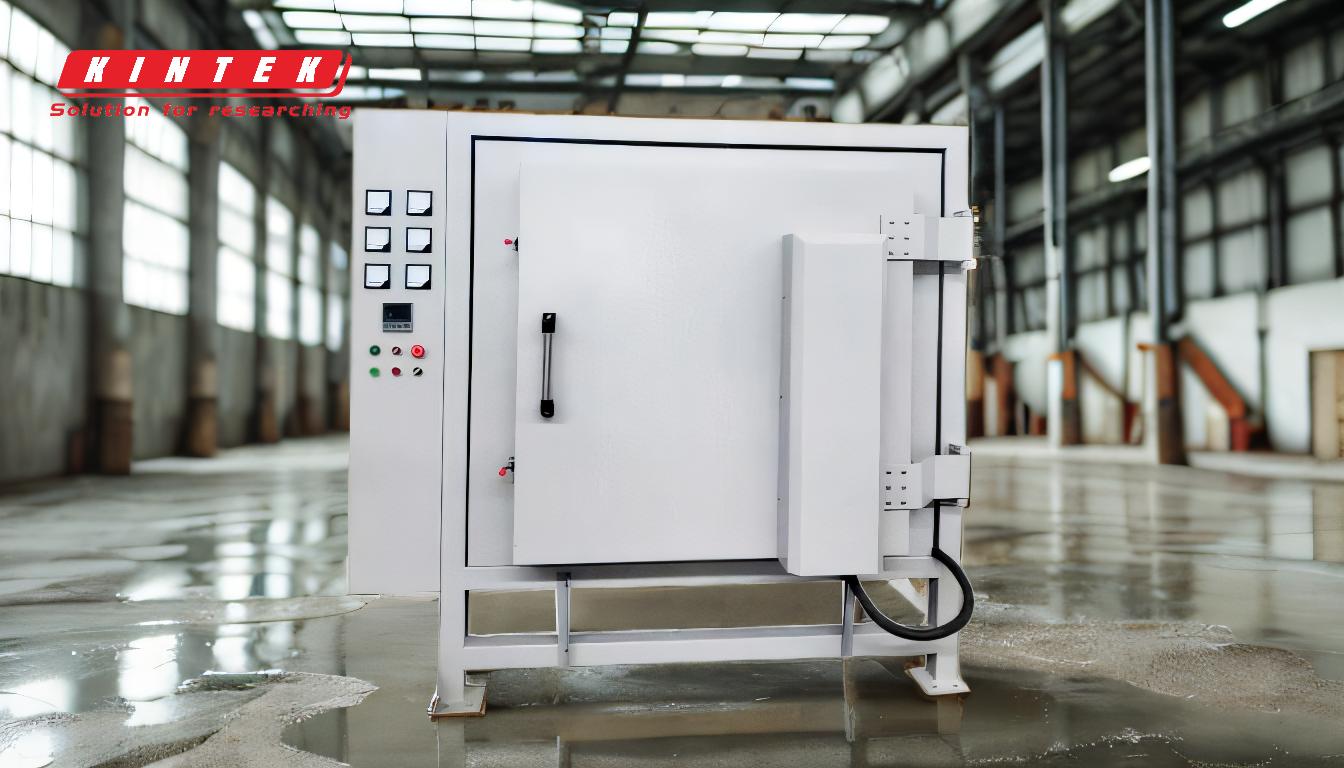
-
Hohe Kapitalkosten:
- Sputtering-Anlagen sind komplex und erfordern erhebliche Investitionen in Hochdruckgeräte und Vakuumsysteme.Dies macht die Ersteinrichtung kostenintensiv, was für kleinere Betriebe oder Forschungslabors ein Hindernis darstellen kann.
-
Niedrige Ablagerungsraten:
- Bei bestimmten Materialien wie SiO2 sind die Abscheideraten beim Sputtern im Vergleich zu anderen Verfahren wie dem Aufdampfen relativ niedrig.Dies kann zu längeren Bearbeitungszeiten und einem geringeren Durchsatz führen, was die Gesamteffizienz beeinträchtigt.
-
Filmverschmutzung:
- Beim Sputtern besteht eine größere Tendenz zur Einbringung von Verunreinigungen in das Substrat als beim Verdampfen.Dies liegt daran, dass beim Sputtern ein geringerer Vakuumbereich herrscht, so dass Verunreinigungen aus den Ausgangsmaterialien oder den Sputtergasen in die Schicht diffundieren können.
-
Materialverschlechterung:
- Einige Materialien, insbesondere organische Feststoffe, sind anfällig für eine Zersetzung durch Ionenbeschuss während des Sputterprozesses.Dies schränkt die Palette der Materialien ein, die mit dieser Technik effektiv abgeschieden werden können.
-
Temperaturanstieg des Substrats:
- Das Sputtering-Verfahren kann zu einem erheblichen Anstieg der Substrattemperatur führen, was für temperaturempfindliche Materialien oder Substrate schädlich sein kann.Dies macht zusätzliche Kühlsysteme erforderlich, wodurch die Energiekosten steigen und die Produktionsraten sinken.
-
Schwierige Kontrolle der Filmdicke:
- Die genaue Kontrolle der Schichtdicke ist beim Sputtern eine Herausforderung.Dies kann bei Anwendungen, die sehr gleichmäßige oder spezifische Schichteigenschaften erfordern, eine kritische Einschränkung darstellen.
-
Herausforderungen bei der Integration von Lift-Off-Prozessen:
- Sputtern lässt sich nur schwer mit Lift-off-Verfahren kombinieren, die zur Strukturierung von Schichten verwendet werden.Die diffuse Transportcharakteristik des Sputterns macht eine vollständige Abschattung unmöglich, was zu Kontaminationsproblemen führt und die Herstellung strukturierter Schichten erschwert.
-
Beschränkungen bei der Materialauswahl:
- Die Auswahl der Beschichtungsmaterialien beim Sputtern ist durch ihre Schmelztemperaturen begrenzt.Hochschmelzende Werkstoffe eignen sich unter Umständen nicht für das Sputtern, was den Anwendungsbereich einschränkt.
-
Wartung und Betriebskomplexität:
- Sputtering-Systeme erfordern eine regelmäßige Wartung und eine sorgfältige Kontrolle der Prozessparameter.Dies erhöht die Komplexität des Betriebs und kann zu Ausfallzeiten führen, die die Produktivität beeinträchtigen.
-
Einführung von Verunreinigungen aus Sputtering-Gasen:
- Inerte Sputtergase, wie z. B. Argon, können zu Verunreinigungen in der wachsenden Schicht führen.Dies ist besonders problematisch bei Anwendungen, die hochreine Schichten erfordern, wie z. B. bei der Halbleiterherstellung.
Zusammenfassend lässt sich sagen, dass das Sputtern zwar eine vielseitige und weit verbreitete Abscheidungstechnik ist, ihre Nachteile - von hohen Kosten und niedrigen Abscheideraten bis hin zu Verunreinigungen und Materialabbau - sie jedoch für bestimmte Anwendungen weniger geeignet machen.Die Kenntnis dieser Einschränkungen ist entscheidend für die Auswahl der geeigneten Abscheidungsmethode auf der Grundlage der spezifischen Projektanforderungen.
Zusammenfassende Tabelle:
Benachteiligung | Beschreibung |
---|---|
Hohe Investitionskosten | Komplexe Geräte und Vakuumsysteme erfordern erhebliche Anfangsinvestitionen. |
Niedrige Abscheideraten | Langsamere Abscheidung für Materialien wie SiO2 im Vergleich zu Aufdampfverfahren. |
Filmkontamination | Größere Anfälligkeit für Verunreinigungen aufgrund geringerer Vakuumbereiche. |
Materialverschlechterung | Organische Feststoffe werden unter Ionenbeschuss abgebaut, was die Materialverträglichkeit einschränkt. |
Temperaturanstieg des Substrats | Wärmeempfindliche Materialien erfordern möglicherweise zusätzliche Kühlsysteme. |
Schwierige Kontrolle der Schichtdicke | Herausforderungen beim Erreichen einer präzisen und gleichmäßigen Schichtdicke. |
Integration mit Lift-Off-Prozessen | Aufgrund des diffusen Transports schwer mit Lift-Off-Verfahren zu kombinieren. |
Beschränkungen bei der Materialauswahl | Hochschmelzende Materialien sind möglicherweise nicht für das Sputtern geeignet. |
Wartung und Betriebskomplexität | Erfordert regelmäßige Wartung und sorgfältige Kontrolle der Prozessparameter. |
Einführung von Verunreinigungen durch Gase | Inertgase wie Argon können in hochreinen Filmen zu Verunreinigungen werden. |
Benötigen Sie Hilfe bei der Auswahl der richtigen Abscheidungstechnik? Kontaktieren Sie noch heute unsere Experten um die beste Lösung für Ihr Projekt zu finden!