Das Sputtering-Verfahren ist zwar für die Abscheidung von Dünnschichten weit verbreitet, hat jedoch mehrere Einschränkungen, die sich auf seine Effizienz, Kosten und die Qualität der abgeschiedenen Schichten auswirken können.Zu diesen Einschränkungen gehören eine mögliche Verunreinigung der Schichten durch Verunreinigungen, hohe Investitions- und Betriebskosten, niedrige Abscheideraten für bestimmte Materialien, Schwierigkeiten bei der Kontrolle der Schichtdicke und Probleme bei der Integration mit anderen Verfahren wie dem Lift-off-Verfahren.Außerdem kann das Verfahren komplexe Anlagen und Kühlsysteme erfordern, was die Energiekosten weiter in die Höhe treiben und die Produktionsraten verringern kann.Die Kenntnis dieser Einschränkungen ist entscheidend für die Auswahl der geeigneten Abscheidungsmethode für bestimmte Anwendungen.
Die wichtigsten Punkte werden erklärt:
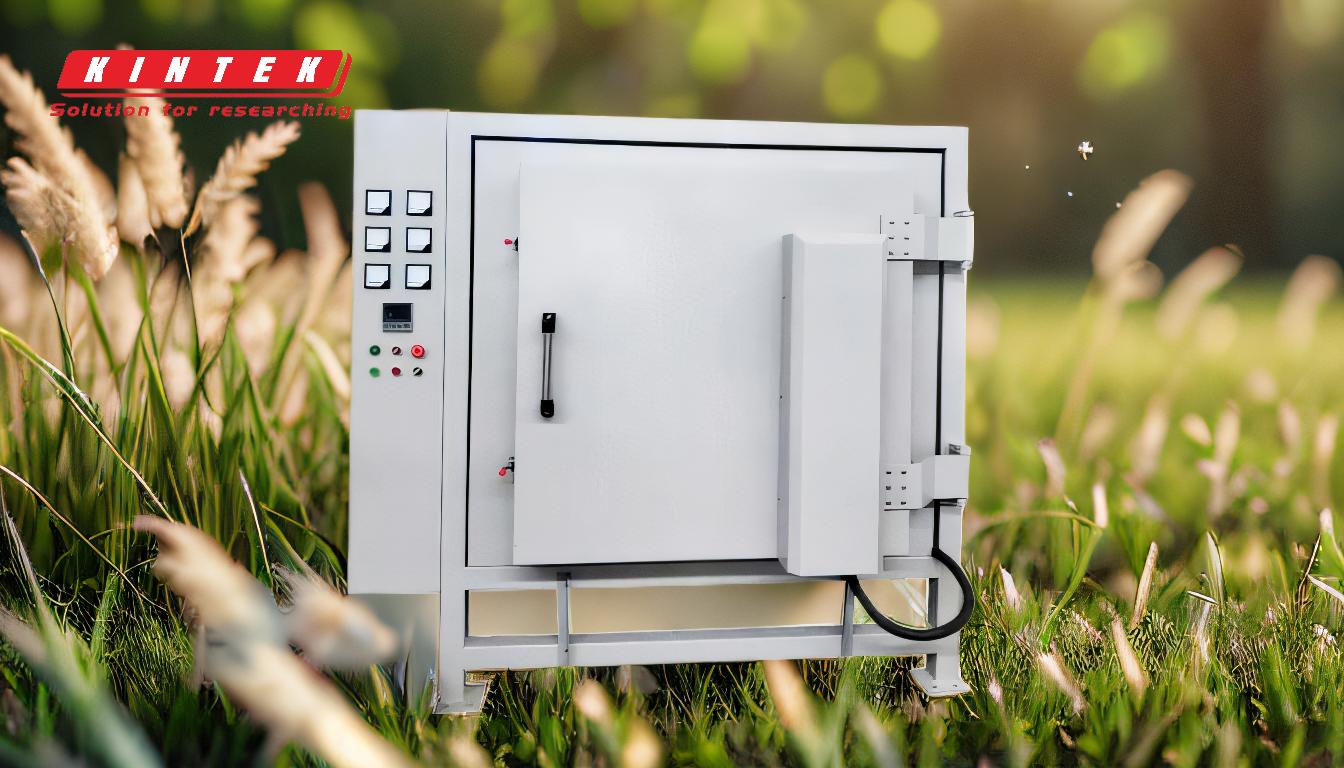
-
Filmverschmutzung:
- Ursache: Verunreinigungen aus den Ausgangsmaterialien können während des Sputterprozesses in die Schicht diffundieren und zu Verunreinigungen führen.
- Auswirkungen: Diese Verunreinigung kann die Qualität der abgeschiedenen Schicht beeinträchtigen und ihre elektrischen, optischen oder mechanischen Eigenschaften beeinträchtigen.
- Beispiel: Inerte Sputtergase können als Verunreinigungen in die wachsende Schicht eingebettet werden, was die Kontaminationsprobleme weiter verschärft.
-
Hohe Investitions- und Betriebskosten:
- Komplexität der Ausrüstung: Das Sputtern erfordert eine hochentwickelte Ausrüstung, einschließlich Hochdruckgeräten und Kühlsystemen, die in der Anschaffung und Wartung teuer sind.
- Energiekosten: Der Bedarf an Kühlsystemen erhöht nicht nur den Energieverbrauch, sondern verringert auch die Gesamtproduktionsrate, wodurch das Verfahren weniger kosteneffizient wird.
-
Niedrige Abscheideraten:
- Materialabhängigkeit: Bestimmte Materialien, wie z. B. SiO2, haben relativ niedrige Abscheidungsraten beim Sputtern, was die Produktion verlangsamen kann.
- Auswirkungen auf die Produktion: Niedrige Abscheideraten können eine erhebliche Einschränkung in hochvolumigen Produktionsumgebungen darstellen, in denen der Durchsatz entscheidend ist.
-
Schwierige Kontrolle der Schichtdicke:
- Probleme mit der Präzision: Sputterverfahren haben oft Probleme mit der präzisen Steuerung der Schichtdicke, die für Anwendungen, die gleichmäßige dünne Schichten erfordern, entscheidend ist.
- Schicht-für-Schicht-Wachstum: Die aktive Steuerung des schichtweisen Wachstums ist im Vergleich zu anderen Abscheidungsmethoden, wie z. B. der gepulsten Laserabscheidung, eine größere Herausforderung.
-
Herausforderungen bei der Materialauswahl:
- Einschränkungen bei der Schmelztemperatur: Die Auswahl der Beschichtungsmaterialien ist durch ihre Schmelztemperaturen begrenzt, da Materialien mit sehr hohen Schmelzpunkten möglicherweise nicht für das Sputtern geeignet sind.
- Zersetzung von organischen Feststoffen: Einige Materialien, insbesondere organische Feststoffe, neigen unter Ionenbeschuss zur Zersetzung, was ihre Verwendung in Sputterprozessen einschränkt.
-
Integration mit Lift-Off-Prozessen:
- Probleme mit der Abschattung: Die diffuse Transportcharakteristik des Sputterns macht eine vollständige Abschattung unmöglich, was die Integration mit Lift-off-Prozessen, die zur Strukturierung von Schichten verwendet werden, erschwert.
- Kontaminationsrisiken: Dies kann zu Kontaminationsproblemen führen, insbesondere wenn versucht wird, präzise Muster oder Strukturen auf dem Substrat zu erzeugen.
-
Temperaturanstieg des Substrats:
- Thermische Effekte: Der Sputterprozess kann einen erheblichen Anstieg der Substrattemperatur verursachen, was die Eigenschaften des Substrats oder der abgeschiedenen Schicht beeinträchtigen kann.
- Anfälligkeit für Verunreinigungsgase: Hohe Substrattemperaturen können den Prozess auch anfälliger für Verunreinigungen durch Fremdgase machen.
-
Vakuum-Anforderungen:
- Geringerer Vakuumbereich: Das Sputtern arbeitet im Vergleich zur Verdampfung in einem geringeren Vakuumbereich, was die Wahrscheinlichkeit erhöht, dass Verunreinigungen in das Substrat gelangen.
- Vergleich mit der Verdampfung: Dadurch ist das Sputtern weniger geeignet für Anwendungen, bei denen eine extrem hohe Reinheit erforderlich ist.
Die Kenntnis dieser Einschränkungen ist für die Optimierung des Sputterverfahrens und die Auswahl der am besten geeigneten Abscheidungstechnik für bestimmte Anwendungen von wesentlicher Bedeutung.Obwohl das Sputtern viele Vorteile bietet, wie z. B. die Möglichkeit, eine breite Palette von Materialien abzuscheiden und qualitativ hochwertige Schichten herzustellen, müssen diese Einschränkungen sorgfältig berücksichtigt werden, um sicherzustellen, dass die gewünschten Ergebnisse erzielt werden.
Zusammenfassende Tabelle:
Einschränkung | Ursache/Auswirkung |
---|---|
Filmverschmutzung | Verunreinigungen aus dem Ausgangsmaterial verschlechtern die Filmqualität. |
Hohe Investitions- und Betriebskosten | Komplexe Geräte und Kühlsysteme erhöhen die Kosten und verringern die Effizienz. |
Niedrige Abscheideraten | Bestimmte Materialien wie SiO2 haben langsame Abscheidungsraten, was die Produktion beeinträchtigt. |
Schwierige Kontrolle der Schichtdicke | Herausforderungen bei der Herstellung präziser, gleichmäßiger dünner Schichten. |
Herausforderungen bei der Materialauswahl | Begrenzt durch Schmelztemperaturen und Abbau von organischen Feststoffen. |
Integration mit Lift-Off-Verfahren | Abschattungsprobleme und Kontaminationsrisiken erschweren die Strukturierung. |
Temperaturanstieg des Substrats | Thermische Effekte und die Anfälligkeit für Fremdgase beeinflussen die Filmeigenschaften. |
Vakuumanforderungen | Ein geringerer Vakuumbereich erhöht das Risiko von Verunreinigungen im Vergleich zur Verdampfung. |
Benötigen Sie Hilfe bei der Auswahl der richtigen Abscheidungsmethode für Ihre Anwendung? Kontaktieren Sie unsere Experten noch heute!