Das Gleichstromsputtern ist zwar eine weit verbreitete Technik zur Abscheidung von Dünnschichten, hat jedoch einige Einschränkungen, die sich auf ihre Effizienz, Qualität und Anwendbarkeit auswirken können. Zu diesen Einschränkungen gehören Probleme mit isolierenden Materialien, potenzielle Schichtverunreinigungen, geringere Abscheideraten und Schwierigkeiten bei der Kontrolle der Prozessparameter. Darüber hinaus erschweren Probleme wie die Erwärmung des Substrats, Lichtbogenbildung und die Vergiftung des Targets den Prozess zusätzlich. Fortgeschrittene Techniken wie das Magnetronsputtern wurden entwickelt, um einige dieser Probleme zu entschärfen, aber das DC-Sputtern hat immer noch mit inhärenten Problemen zu kämpfen, die seine Effektivität bei bestimmten Anwendungen einschränken.
Die wichtigsten Punkte werden erklärt:
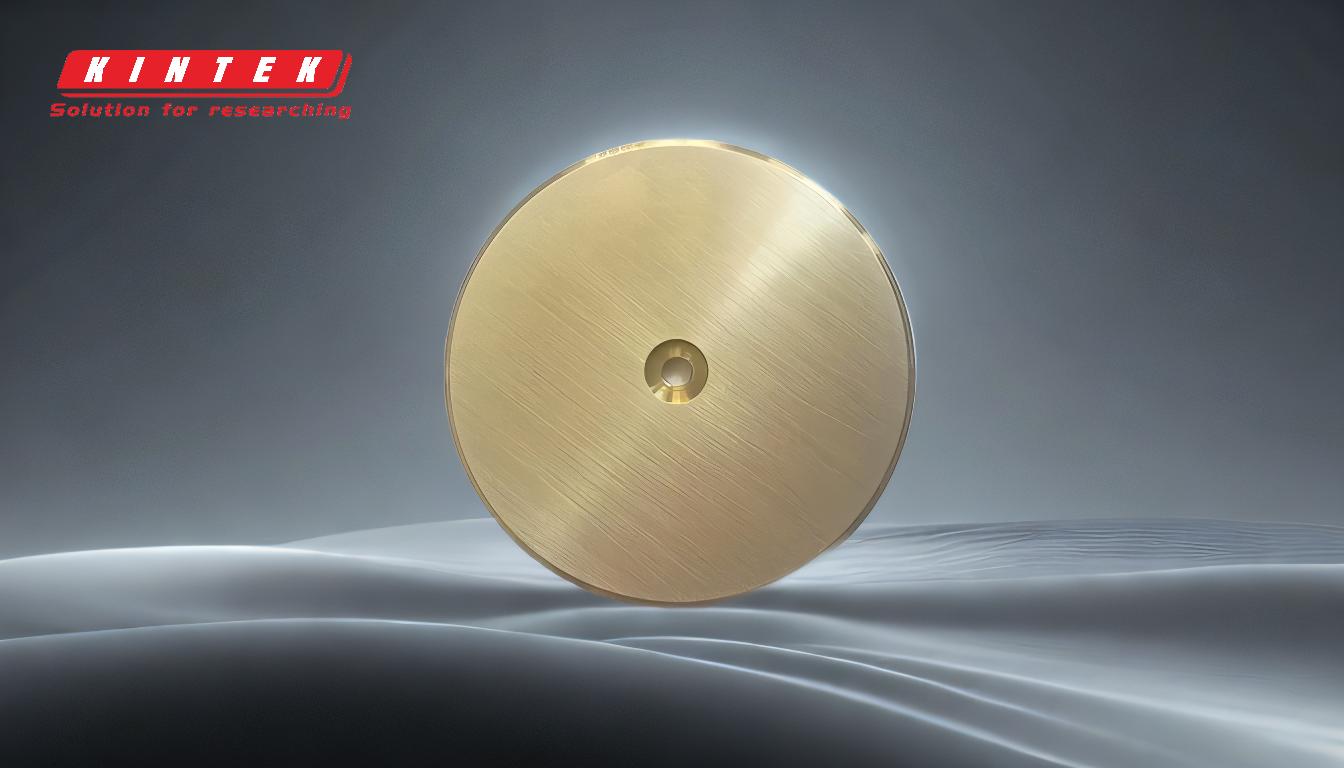
-
Herausforderungen bei Dämmstoffen:
- Aufbau von Ladung: Nicht leitende dielektrische Materialien können im Laufe der Zeit Ladung ansammeln, was zu Lichtbogenbildung oder Targetvergiftung führt. Dies unterbricht den Sputterprozess und kann ihn ganz zum Erliegen bringen.
- Lichtbögen und Schäden an der Stromversorgung: Durch den Aufbau von Ladung können kleine und große Lichtbögen entstehen, die nicht nur die Stromversorgung beschädigen, sondern auch zu einem ungleichmäßigen Atomabtrag aus dem Zielmaterial führen.
-
Filmverschmutzung:
- Verunreinigungsdiffusion: Während des Sputterprozesses können Verunreinigungen aus den Ausgangsmaterialien in die Schicht diffundieren und zu Verunreinigungen führen.
- Beschränkungen der Schmelztemperatur: Die Auswahl der Beschichtungsmaterialien ist durch ihre Schmelztemperaturen begrenzt, was die Bandbreite der Materialien, die effektiv gesputtert werden können, einschränken kann.
-
Niedrigere Ablagerungsraten:
- Plasma-Dichte: Beim DC-Sputtern sind die Plasmadichten im Allgemeinen geringer als bei fortschrittlicheren Techniken wie dem High Power Impulse Magnetron Sputtering (HIPIMS), was zu niedrigeren Abscheideraten führt.
- Gasdichte: Höhere Gasdichten beim DC-Sputtern tragen ebenfalls zu niedrigeren Abscheideraten bei.
-
Prozesskontrolle und Parameterempfindlichkeit:
- Parameter Empfindlichkeit: Die genaue Kontrolle von Prozessparametern wie Gasdruck, Target-Substrat-Abstand und Spannung ist entscheidend für optimale Ergebnisse. Kleine Abweichungen können sich erheblich auf die Qualität der abgeschiedenen Schicht auswirken.
- Hohe Betriebsdrücke: Herkömmliche Sputtering-Verfahren erfordern oft hohe Betriebsdrücke, die die Qualität und Effizienz der Dünnschichtabscheidung beeinträchtigen können.
-
Erwärmung des Substrats:
- Thermische Effekte: Das Sputtering-Verfahren kann zu einer erheblichen Erwärmung des Substrats führen, was bei temperaturempfindlichen Materialien oder Anwendungen unerwünscht sein kann.
-
Anforderungen an das Kühlsystem:
- Energiekosten: Die Notwendigkeit eines Kühlsystems zur Steuerung der Substraterwärmung verringert die Produktionsrate und erhöht die Energiekosten, was das Verfahren weniger effizient und teurer macht.
-
Kontamination der Kammer:
- Nicht-leitende Beschichtungen: Die Zerstäubung dielektrischer Materialien kann die Wände der Vakuumkammer mit nichtleitendem Material beschichten, wodurch elektrische Ladungen eingeschlossen werden und zu Lichtbögen und anderen Qualitätsproblemen führen.
-
Probleme mit Abschirmung und Permeation:
- Elastomer-Dichtungen: Permeation durch Elastomerdichtungen und Probleme im Zusammenhang mit der Abschirmung können den Sputterprozess weiter erschweren und die Gesamtqualität der abgeschiedenen Schicht beeinträchtigen.
Zusammenfassend lässt sich sagen, dass die Gleichstromzerstäubung zwar eine wertvolle Technik für die Abscheidung von Dünnschichten ist, aber nicht ohne Einschränkungen. Diese Herausforderungen erfordern eine sorgfältige Prüfung der Prozessparameter, der Materialauswahl und des Einsatzes fortschrittlicher Techniken, um einige der inhärenten Probleme zu entschärfen. Das Verständnis dieser Einschränkungen ist entscheidend für die Optimierung des Sputterprozesses und die Herstellung hochwertiger Dünnschichten.
Zusammenfassende Tabelle:
Begrenzung | Zentrale Herausforderungen |
---|---|
Isolierende Materialien | Ladungsaufbau, Lichtbogenbildung und Schäden an der Stromversorgung |
Filmverschmutzung | Verunreinigungsdiffusion, Schmelztemperaturbeschränkungen |
Niedrigere Ablagerungsraten | Niedrige Plasmadichte, hohe Gasdichte |
Prozesskontrolle | Parameterempfindlichkeit, hohe Betriebsdrücke |
Erwärmung des Substrats | Thermische Auswirkungen auf temperaturempfindliche Materialien |
Anforderungen an das Kühlsystem | Erhöhte Energiekosten und verringerte Produktionsraten |
Kontamination der Kammer | Nicht leitende Beschichtungen, die zu Lichtbogenbildung und Qualitätsproblemen führen |
Abschirmung und Permeation | Komplikationen bei der Permeation und Abschirmung von Elastomerdichtungen |
Benötigen Sie Hilfe bei der Optimierung Ihres Dünnschicht-Beschichtungsprozesses? Kontaktieren Sie unsere Experten noch heute für maßgeschneiderte Lösungen!