Das Doppelschneckencompoundieren ist ein wichtiger Prozess in der Polymer- und Materialwissenschaft, der zum Mischen, Vermengen und Homogenisieren von Materialien zu einem einheitlichen Produkt eingesetzt wird.Das Verfahren umfasst mehrere aufeinanderfolgende Schritte, von denen jeder zur endgültigen Qualität des gemischten Materials beiträgt.Zu diesen Schritten gehören Zuführen, Schmelzen, Fördern, Mischen, Entlüften und Extrudieren.Jeder Schritt wird sorgfältig kontrolliert, um optimale Materialeigenschaften wie Konsistenz, Homogenität und Leistung zu gewährleisten.Im Folgenden werden die wichtigsten Schritte im Detail erläutert, um ein umfassendes Verständnis des Doppelschnecken-Compoundierverfahrens zu vermitteln.
Schlüsselpunkte erklärt:
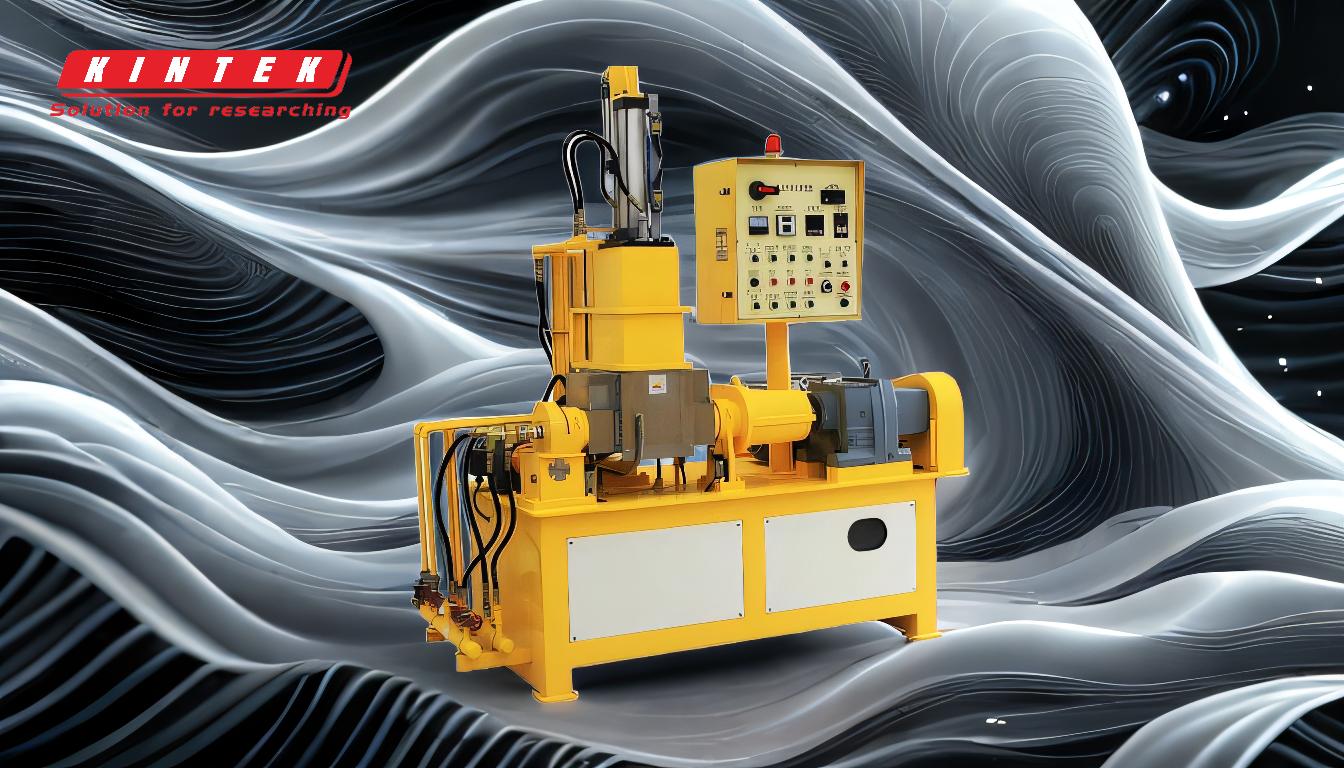
-
Fütterung
- Zweck:Einführen der Rohstoffe in den Doppelschneckenextruder.
-
Verfahren:Feststoffe (Polymere, Additive, Füllstoffe usw.) werden dem Extruder mit volumetrischen oder gravimetrischen Dosierern zugeführt.
- Volumetrische Dosierer messen das Material nach Volumen, während gravimetrische Dosierer das Gewicht messen und so eine präzise Steuerung der Zufuhrrate gewährleisten.
-
Überlegungen:
- Die ordnungsgemäße Beschickung sorgt für einen gleichmäßigen Materialfluss und verhindert Unterbrechungen im Aufbereitungsprozess.
- In dieser Zone erfolgt die Entlüftung und Verdichtung von Materialien mit geringer Dichte, um das Material für die nachfolgenden Schritte vorzubereiten.
-
Schmelzen
- Zweck:Umwandlung fester Materialien in einen geschmolzenen Zustand, um das Mischen und Verarbeiten zu erleichtern.
-
Prozess:Das Material wird durch die Zylinderheizung und die von den rotierenden Schnecken erzeugte mechanische Scherung erhitzt.
- Die Schnecken sind mit speziellen Geometrien ausgestattet, um die Wärmeübertragung und die Schmelzleistung zu verbessern.
-
Überlegungen:
- Die Temperaturkontrolle ist entscheidend, um eine thermische Zersetzung des Materials zu vermeiden.
- Die Schmelzzone muss ein vollständiges und gleichmäßiges Schmelzen gewährleisten, um ein homogenes Gemisch zu erhalten.
-
Fördern
- Zweck:Transportieren Sie das geschmolzene Material durch den Extruder.
-
Verfahren:Die rotierenden Schnecken bewegen das Material entlang des Zylinders vorwärts.
- Die Schneckenkonstruktion (z. B. Steigung, Gangtiefe) beeinflusst die Förderleistung und die Verweilzeit des Materials.
-
Überlegungen:
- Die Förderung muss gleichmäßig sein, um einen gleichmäßigen Materialfluss zu gewährleisten und Rückstau oder Stagnation zu vermeiden.
- Die richtige Schneckengeometrie gewährleistet einen effizienten Materialtransport ohne übermäßigen Energieverbrauch.
-
Mischen
- Zweck:Erzielung einer einheitlichen Mischung aller Komponenten (Polymere, Additive, Füllstoffe usw.).
-
Verfahren:Das Mischen erfolgt durch distributive und dispersive Mechanismen.
- Beim distributiven Mischen werden die Komponenten gleichmäßig im Material verteilt.
- Dispersives Mischen bricht Agglomerate auf und sorgt für eine feine Dispersion der Zusatzstoffe.
-
Überlegungen:
- Schneckenelemente (z.B. Knetblöcke, Mischelemente) werden auf die spezifischen Mischanforderungen zugeschnitten.
- Mischintensität und -dauer müssen optimiert werden, um die gewünschten Materialeigenschaften ohne übermäßige Scherbeanspruchung zu erreichen.
-
Entlüftung
- Zweck:Entfernen Sie flüchtige Bestandteile, Feuchtigkeit oder eingeschlossene Luft aus dem Material.
-
Prozess:Das Material durchläuft eine Entlüftungszone, in der ein Vakuum oder atmosphärischer Druck angelegt wird, um flüchtige Bestandteile zu entfernen.
- Die Entlüftungsöffnungen sind strategisch platziert, um eine effektive Entfernung unerwünschter Bestandteile zu gewährleisten.
-
Erwägungen:
- Eine ordnungsgemäße Entlüftung verhindert Mängel wie Blasen, Hohlräume oder eine schlechte Oberflächenbeschaffenheit des Endprodukts.
- Die Effizienz der Entlüftung hängt von der Viskosität des Materials, dem Design der Entlüftungsöffnung und dem Vakuumniveau ab.
-
Extrusion
- Zweck:Das homogenisierte Material in die gewünschte Form bringen.
-
Prozess:Das geschmolzene Material wird durch eine Düse gepresst, um Pellets, Stränge oder Profile zu erzeugen.
- Das Design der Düse bestimmt die endgültige Produktgeometrie.
-
Überlegungen:
- Düsendruck und Temperatur müssen kontrolliert werden, um gleichbleibende Produktabmessungen und Qualität zu gewährleisten.
- Kühl- und Schneidsysteme werden nachgeschaltet, um das extrudierte Material zu verfestigen und zu zerkleinern.
Durch die Befolgung dieser Schritte gewährleistet das Doppelschneckencompoundieren die Herstellung hochwertiger, einheitlicher Materialien, die auf spezifische Anwendungen zugeschnitten sind.Jede Stufe ist voneinander abhängig und erfordert eine präzise Steuerung und Optimierung, um die gewünschten Materialeigenschaften und Leistungen zu erzielen.
Zusammenfassende Tabelle:
Schritt | Zweck | Wichtige Überlegungen |
---|---|---|
Fütterung | Einführen von Rohstoffen in den Extruder. | Für gleichmäßigen Durchfluss sorgen; Luft entfernen und Materialien mit geringer Dichte verdichten. |
Schmelzen | Überführen von Feststoffen in einen geschmolzenen Zustand zum Mischen. | Kontrolle der Temperatur, um eine Zersetzung zu vermeiden; Gewährleistung eines gleichmäßigen Schmelzens. |
Fördern | Transportieren Sie geschmolzenes Material durch den Extruder. | Aufrechterhaltung eines gleichmäßigen Flusses; Optimierung der Schneckengeometrie für mehr Effizienz. |
Mischen | Erzielen Sie eine gleichmäßige Mischung der Komponenten. | Verwenden Sie verteilendes und dispersives Mischen; optimieren Sie Intensität und Dauer. |
Entlüftung | Entfernen Sie flüchtige Stoffe, Feuchtigkeit oder eingeschlossene Luft. | Verhindern Sie Defekte wie Blasen; optimieren Sie das Design der Entlüftungsöffnungen und das Vakuumniveau. |
Extrusion | Formung des Materials in die gewünschte Form oder Gestalt. | Steuern Sie den Druck und die Temperatur der Düse und gewährleisten Sie gleichbleibende Produktabmessungen und Qualität. |
Sind Sie bereit, Ihren Doppelschnecken-Compoundierprozess zu optimieren? Kontaktieren Sie noch heute unsere Experten für maßgeschneiderte Lösungen!