Sputtern ist eine vielseitige und weit verbreitete Technik zur Abscheidung von Dünnschichten mit zahlreichen Vorteilen. Es ermöglicht die Abscheidung einer breiten Palette von Materialien, einschließlich solcher mit hohen Schmelzpunkten und niedrigem Dampfdruck, und erzeugt Schichten mit hervorragender Haftung, Gleichmäßigkeit und Reinheit. Das Verfahren ist sehr gut steuerbar und ermöglicht eine präzise Einstellung der Schichteigenschaften und -dicke. Darüber hinaus eignet sich das Sputtern für verschiedene Substrate, arbeitet bei niedrigeren Temperaturen und kann hohe Abscheidungsraten erzielen, ohne die Schichtqualität zu beeinträchtigen. Das Verfahren ist außerdem wartungsfrei und mit Ultrahochvakuumanwendungen kompatibel, was es ideal für fortschrittliche Industrie- und Forschungsanwendungen macht.
Die wichtigsten Punkte werden erklärt:
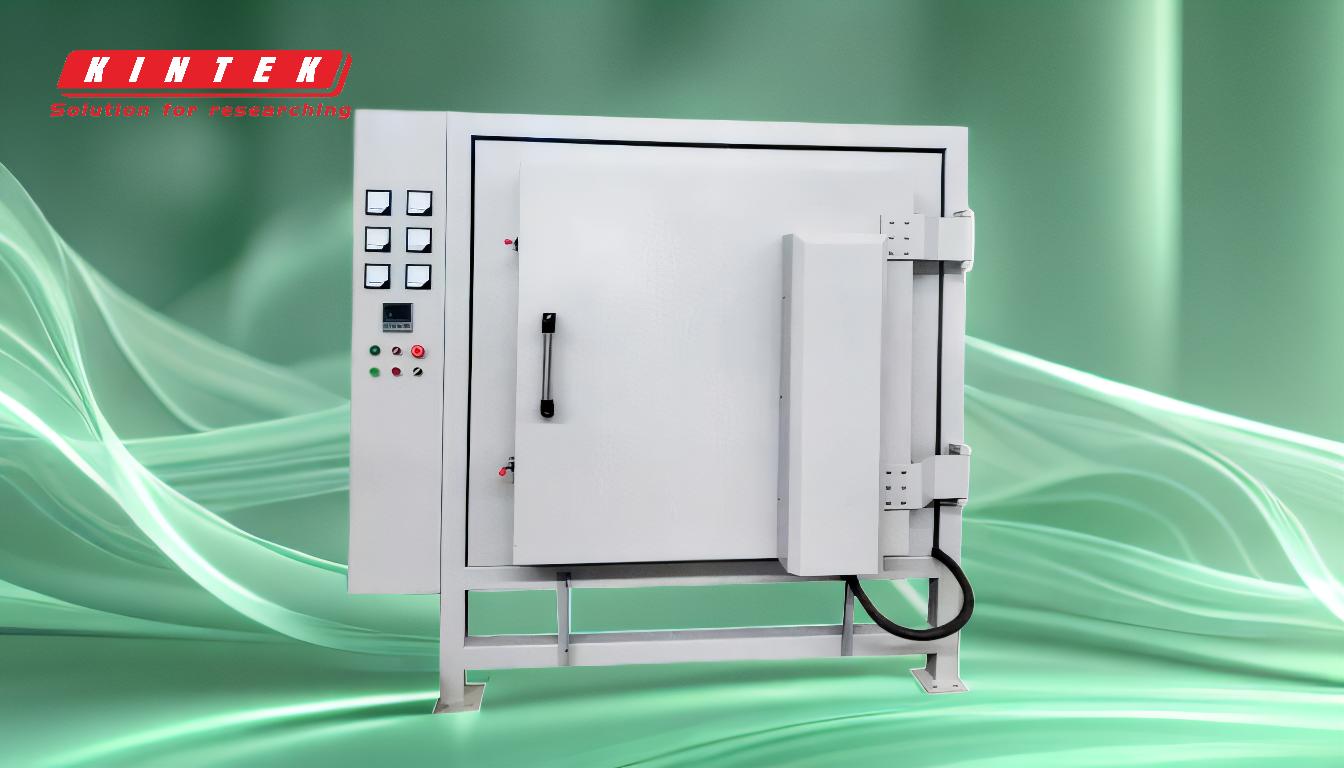
-
Vielseitigkeit bei der Materialabscheidung:
- Durch Sputtern kann praktisch jedes Material abgeschieden werden, einschließlich Metalle, Halbleiter, Isolatoren, Verbindungen und Mischungen. Dadurch eignet es sich für ein breites Spektrum von Anwendungen, von der Elektronik bis zur Optik.
- Sie ist besonders vorteilhaft für Materialien mit hohem Schmelzpunkt und niedrigem Dampfdruck, die sich mit anderen Methoden wie der Verdampfung nur schwer abscheiden lassen.
- Beispiel: Materialien wie Wolfram und Keramik, die einen hohen Schmelzpunkt haben, können leicht gesputtert werden.
-
Ausgezeichnete Filmhaftung:
- Die gesputterten Atome haben eine hohe kinetische Energie, was ihre Haftung auf dem Substrat erhöht. Dies führt zu stärkeren Bindungen und zur Bildung einer Diffusionsschicht an der Grenzfläche.
- Eine bessere Haftung ist entscheidend für Anwendungen, bei denen mechanische Haltbarkeit und langfristige Stabilität erforderlich sind.
- Beispiel: Bei gesputterten Folien ist die Wahrscheinlichkeit, dass sie sich ablösen oder delaminieren, geringer als bei aufgedampften Folien.
-
Hohe Reinheit und Dichte des Films:
- Das Sputtering-Verfahren vermeidet Verunreinigungen durch Verdampfungsquellen und führt zu Schichten mit hoher Reinheit und Dichte.
- Bei gesputterten Schichten werden weniger Pinholes und Defekte beobachtet, was sie ideal für Anwendungen macht, die hochwertige Beschichtungen erfordern.
- Beispiel: Gesputterte Schichten werden aufgrund ihrer hohen Reinheit häufig in der Halbleiterherstellung verwendet.
-
Präzise Kontrolle über Filmdicke und Gleichmäßigkeit:
- Die Schichtdicke kann durch die Einstellung des Zielstroms präzise gesteuert werden, was Reproduzierbarkeit und Gleichmäßigkeit über große Flächen gewährleistet.
- Dieses Maß an Kontrolle ist für Anwendungen wie optische Beschichtungen und Mikroelektronik unerlässlich.
- Beispiel: Sputtern wird verwendet, um gleichmäßige Antireflexionsschichten auf Linsen und Displays zu erzeugen.
-
Fähigkeit zur Einlagerung komplexer Materialien:
- Durch Sputtern können Elemente, Legierungen und Verbindungen, einschließlich reaktiver Materialien, abgeschieden werden, indem reaktive Gase in den Prozess einbezogen werden.
- Auf diese Weise lassen sich maßgeschneiderte Folien mit spezifischen Eigenschaften wie Härte, Leitfähigkeit oder optischen Merkmalen herstellen.
- Beispiel: Reaktives Sputtern wird zur Abscheidung von Titannitrid (TiN) für verschleißfeste Beschichtungen verwendet.
-
Niedertemperaturabscheidung:
- Das Sputtern kann bei niedrigeren Temperaturen durchgeführt werden und eignet sich daher für temperaturempfindliche Substrate wie Kunststoffe und organische Stoffe.
- Dadurch wird die Anwendbarkeit auf Branchen wie flexible Elektronik und biomedizinische Geräte erweitert.
- Beispiel: Sputtern wird zur Abscheidung dünner Schichten auf Polymersubstraten für flexible Displays verwendet.
-
Präzision auf molekularer Ebene:
- Das Verfahren ermöglicht eine präzise Kontrolle auf molekularer Ebene, so dass makellose Grenzflächen geschaffen und die Eigenschaften des Films eingestellt werden können.
- Dies ist entscheidend für fortgeschrittene Anwendungen in der Nanotechnologie und der Materialwissenschaft.
- Beispiel: Das Sputtern wird zur Herstellung von Mehrschichtstrukturen in Quantengeräten verwendet.
-
Hohe Ablagerungsraten und Skalierbarkeit:
- Das Sputtern bietet hohe Abscheideraten ohne Dickenbeschränkungen und eignet sich daher für die industrielle Produktion.
- Das Verfahren kann für die gleichmäßige Beschichtung großer Flächen skaliert werden, was für Anwendungen wie Solarpaneele und Architekturglas von Vorteil ist.
- Beispiel: Sputtern wird verwendet, um transparente leitfähige Oxide (TCO) auf großen Glasscheiben abzuscheiden.
-
Wartungsfrei und vakuumtauglich:
- Sputtersysteme sind wartungsfrei und mit Ultrahochvakuum-Umgebungen kompatibel und gewährleisten einen sauberen und zuverlässigen Betrieb.
- Dies ist besonders wichtig für Anwendungen in der Luft- und Raumfahrt, in der Halbleiterindustrie und in Forschungslabors.
- Beispiel: Das Sputtern wird bei der Herstellung von Dünnschicht-Solarzellen im Vakuum eingesetzt.
-
Verbesserte Oberflächenmorphologie:
- Durch Sputtern entstehen Schichten mit hervorragender morphologischer Qualität, einschließlich geringerer Rauheit und kontrollierter Korngröße.
- Dies ist vorteilhaft für Anwendungen, bei denen die Glätte der Oberfläche und die Stöchiometrie entscheidend sind.
- Beispiel: Sputtern wird eingesetzt, um glatte, hochwertige Beschichtungen für optische Komponenten zu erzeugen.
-
Reduzierte Eigenspannungen:
- Der Abscheidungsprozess bei niedrigen oder mittleren Temperaturen minimiert die Restspannungen auf dem Substrat und bewahrt dessen strukturelle Integrität.
- Dies ist vorteilhaft für empfindliche Substrate oder Anwendungen, die mechanische Stabilität erfordern.
- Beispiel: Sputtern wird verwendet, um dünne Schichten auf Siliziumwafern abzuscheiden, ohne spannungsbedingte Defekte zu verursachen.
-
In-Situ-Reinigung und Ablagerung:
- Sputtersysteme können Substrate reinigen und Beschichtungen in derselben Vakuumkammer abscheiden, was die Effizienz und die Schichtqualität verbessert.
- Dadurch wird die Verschmutzung reduziert und eine bessere Haftung gewährleistet.
- Beispiel: Die In-situ-Reinigung wird bei der Herstellung von magnetischen Speichermedien eingesetzt, um die Leistung zu verbessern.
Zusammenfassend lässt sich sagen, dass das Sputtern eine einzigartige Kombination aus Vielseitigkeit, Präzision und Qualität bietet, die es zu einer bevorzugten Wahl für eine breite Palette von Industrie- und Forschungsanwendungen macht. Die Fähigkeit, komplexe Materialien abzuscheiden, die Schichteigenschaften zu kontrollieren und unter verschiedenen Bedingungen zu arbeiten, sorgt dafür, dass es in der fortschrittlichen Fertigung und Technologieentwicklung weiterhin relevant bleibt.
Zusammenfassende Tabelle:
Vorteil | Hauptvorteil |
---|---|
Vielseitigkeit bei der Materialabscheidung | Ablagerung von Metallen, Halbleitern, Isolatoren und Verbindungen mit hohem Schmelzpunkt. |
Ausgezeichnete Filmhaftung | Starke Bindungen und Diffusionsschichten gewährleisten Haltbarkeit und Stabilität. |
Hohe Reinheit und Dichte des Films | Kontaminationsfreie Filme mit weniger Defekten, ideal für die Halbleiterherstellung. |
Präzise Kontrolle über die Dicke | Der einstellbare Zielstrom gewährleistet eine gleichmäßige, reproduzierbare Schichtdicke. |
Niedertemperaturabscheidung | Geeignet für temperaturempfindliche Substrate wie Kunststoffe und organische Stoffe. |
Hohe Ablagerungsraten | Skalierbar für die industrielle Produktion ohne Dickenbeschränkung. |
Wartungsfreier Betrieb | Kompatibel mit Ultrahochvakuum-Umgebungen für saubere, zuverlässige Leistung. |
Sind Sie daran interessiert, Sputtering für Ihr nächstes Projekt zu nutzen? Kontaktieren Sie unsere Experten noch heute um mehr zu erfahren!