Der Unterschied zwischen Einschnecken- und Doppelschneckenextrudern liegt vor allem in der Konstruktion, der Funktionalität und der Anwendungseignung.Einschneckenextruder sind einfacher und kostengünstiger, ideal für einfache Extrusionsaufgaben.Doppelschneckenextruder hingegen bieten bessere Misch-, Compoundier- und Durchsatzmöglichkeiten und eignen sich daher besser für die Verarbeitung komplexer Materialien und die Produktion großer Mengen.Nachstehend finden Sie eine detaillierte Aufschlüsselung der wichtigsten Unterschiede und ihrer Auswirkungen.
Die wichtigsten Punkte werden erklärt:
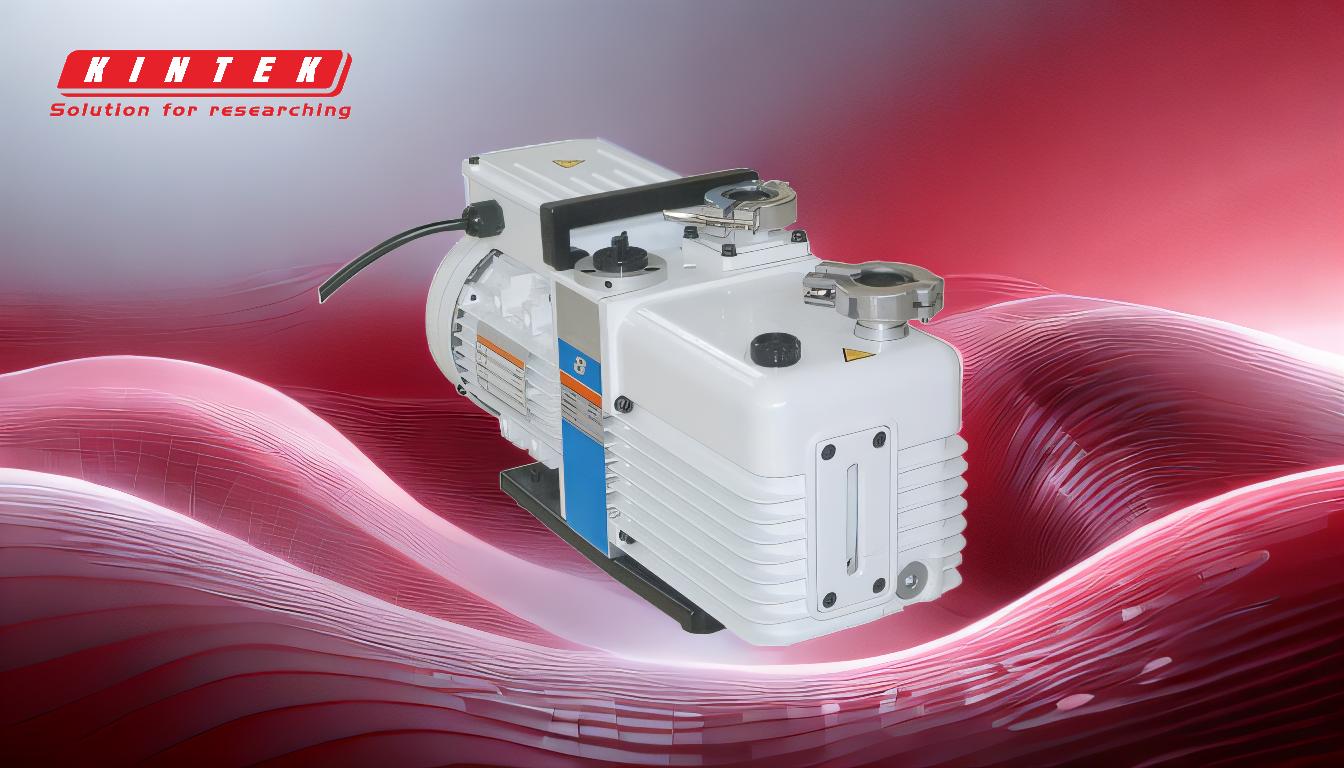
-
Aufbau und Mechanismus:
-
Einschneckenextruder:
- Eine einzelne rotierende Schnecke in einem Zylinder transportiert, schmilzt und drückt das Material durch die Düse.
- Die Schneckenkonstruktion ist relativ einfach und weist weniger bewegliche Teile auf, was Wartung und Betrieb erleichtert.
-
Doppelschneckenextruder:
- Mit zwei ineinandergreifenden Schnecken, die sich entweder gleichsinnig (in dieselbe Richtung) oder gegensinnig (in entgegengesetzte Richtungen) drehen.
- Die Doppelschneckenkonstruktion bietet eine bessere Kontrolle über Materialfluss, Scherung und Mischung.
-
Einschneckenextruder:
-
Mischen und Compounding-Fähigkeiten:
-
Einschneckenextruder:
- Begrenzte Mischfähigkeit aufgrund der Einschneckenkonstruktion, daher weniger geeignet für Anwendungen, die eine präzise Materialmischung erfordern.
- Geeignet für einfachere Aufgaben wie das Schmelzen und Formen von Polymeren.
-
Doppelschneckenextruder:
- Bietet hervorragende Misch- und Compoundierfähigkeiten aufgrund der ineinandergreifenden Schnecken, die mehrere Scherzonen erzeugen und die Materialinteraktion verbessern.
- Ideal für Anwendungen, die ein präzises Mischen von Additiven, Füllstoffen oder mehreren Polymeren erfordern.
-
Einschneckenextruder:
-
Durchsatz und Produktivität:
-
Einschneckenextruder:
- Hat im Allgemeinen eine geringere Durchsatzkapazität und eignet sich daher weniger für die Produktion großer Mengen.
- Kostengünstiger für kleine oder weniger anspruchsvolle Betriebe.
-
Doppelschnecken-Extruder:
- Bietet eine höhere Durchsatzkapazität und ermöglicht eine höhere Produktivität und Effizienz.
- Besser geeignet für die Produktion in großem Maßstab und die Verarbeitung komplexer Materialien.
-
Einschneckenextruder:
-
Material Vielseitigkeit:
-
Einschneckenextruder:
- Am besten geeignet für die Verarbeitung von Standardpolymeren und Materialien, die keine umfangreiche Mischung oder Compoundierung erfordern.
-
Doppelschneckenextruder:
- Kann ein breiteres Spektrum an Materialien verarbeiten, einschließlich hitzeempfindlicher Polymere, Verbundstoffe und Materialien, die eine präzise Rezepturkontrolle erfordern.
-
Einschneckenextruder:
-
Kosten und Wartung:
-
Einschneckenextruder:
- Geringere Anschaffungskosten und einfachere Wartung durch weniger Komponenten und einfaches Design.
-
Doppelschneckenextruder:
- Höhere Anfangsinvestitionen und komplexere Wartung aufgrund des Doppelschneckenmechanismus und der erweiterten Funktionen.
-
Einschneckenextruder:
-
Anwendungen:
-
Einschneckenextruder:
- Wird häufig bei grundlegenden Extrusionsverfahren wie der Rohr-, Platten- und Folienherstellung verwendet.
-
Doppelschnecken-Extruder:
- Bevorzugt für fortschrittliche Anwendungen wie Compounding, reaktive Extrusion und die Verarbeitung von Spezialmaterialien.
-
Einschneckenextruder:
Zusammenfassend lässt sich sagen, dass die Wahl zwischen Einschnecken- und Doppelschneckenextrudern von den spezifischen Anforderungen der jeweiligen Anwendung abhängt.Einschneckenextruder sind kostengünstig und für einfachere Aufgaben geeignet, während sich Doppelschneckenextruder bei der Verarbeitung komplexer Materialien und der Produktion großer Mengen auszeichnen.Das Verständnis dieser Unterschiede ist entscheidend für die Auswahl der richtigen Ausrüstung, um die Produktionsziele und Materialanforderungen zu erfüllen.
Zusammenfassende Tabelle:
Blickwinkel | Einschnecken-Extruder | Doppelschneckenextruder |
---|---|---|
Konstruktion und Mechanismus | Einzelne rotierende Schnecke; einfachere Konstruktion, weniger bewegliche Teile | Zwei ineinandergreifende Schnecken; bessere Kontrolle über Materialfluss, Scherung und Mischung |
Mischen und Compoundieren | Begrenzte Mischfähigkeit; geeignet für einfache Aufgaben | Hervorragendes Mischen und Compoundieren; ideal für präzises Mischen von Zusatzstoffen oder Polymeren |
Durchsatz | Geringere Durchsatzkapazität; kosteneffizient für kleine Betriebe | Höhere Durchsatzkapazität; besser geeignet für die Produktion großer Mengen |
Material Vielseitigkeit | Am besten geeignet für Standardpolymere und einfache Materialien | Geeignet für hitzeempfindliche Polymere, Verbundstoffe und komplexe Formulierungen |
Kosten und Wartung | Geringere Anschaffungskosten; einfachere Wartung | Höhere Anfangsinvestitionen; komplexere Wartung |
Anwendungen | Grundlegende Extrusionsverfahren (z. B. Rohr-, Platten- und Folienherstellung) | Fortgeschrittene Anwendungen (z. B. Compounding, reaktive Extrusion, Spezialmaterialien) |
Benötigen Sie Hilfe bei der Auswahl des richtigen Extruders für Ihre Anwendung? Kontaktieren Sie noch heute unsere Experten für eine persönliche Beratung!