Das Sputtern ist ein äußerst vielseitiges und effizientes Verfahren zur Abscheidung von Dünnschichten mit zahlreichen Vorteilen gegenüber anderen Methoden. Es bietet eine bessere Haftung, eine höhere kinetische Energie der abgeschiedenen Atome und die Möglichkeit, Materialien mit hohen Schmelzpunkten abzuscheiden. Das Verfahren ist reproduzierbar, automatisierbar und mit einer breiten Palette von Materialien kompatibel, darunter Kunststoffe, organische Stoffe, Glas und Metalle. Das Sputtern ermöglicht Präzision auf molekularer Ebene, was makellose Grenzflächen und einstellbare Schichteigenschaften ermöglicht. Darüber hinaus unterstützt es die reaktive Abscheidung, das epitaktische Wachstum und die gleichzeitige beidseitige Beschichtung und ist damit für fortschrittliche Anwendungen geeignet. Seine Kosteneffizienz, der Betrieb bei niedrigen Temperaturen und die Wartungsfreiheit machen es für Industrie- und Forschungsanwendungen noch attraktiver.
Die wichtigsten Punkte erklärt:
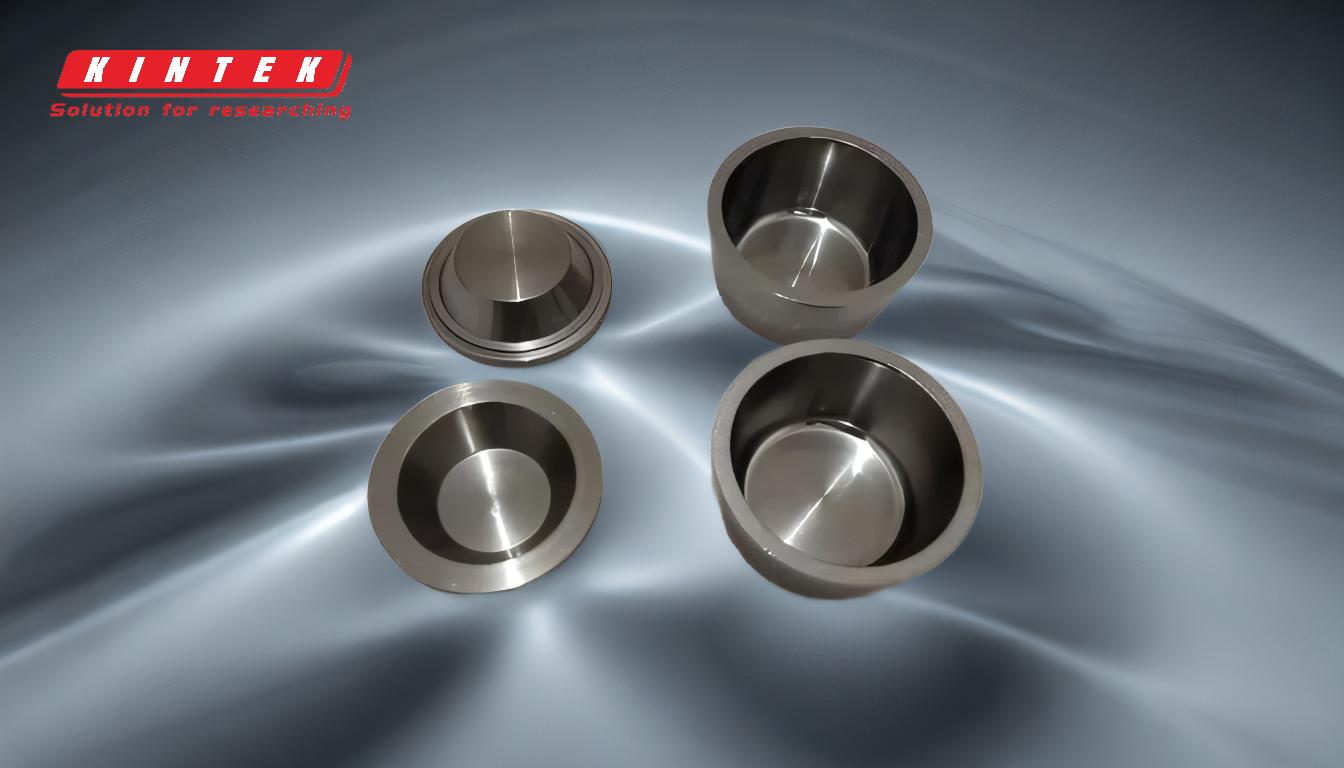
-
Hervorragende Adhäsion und kinetische Energie:
- Durch Sputtern ausgestoßene Atome besitzen eine wesentlich höhere kinetische Energie als aufgedampfte Materialien, was zu einer stärkeren Haftung auf Substraten führt. Dies gewährleistet dauerhafte und zuverlässige dünne Schichten, selbst auf schwierigen Oberflächen.
-
Vielseitigkeit bei der Beschichtungsausrichtung:
- Das Sputtern kann sowohl in Bottom-up- als auch in Top-down-Konfigurationen durchgeführt werden, was Flexibilität bei der Beschichtung komplexer Geometrien bietet und eine gleichmäßige Abdeckung gewährleistet.
-
Abscheidung von Materialien mit hohem Schmelzpunkt:
- Materialien mit sehr hohen Schmelzpunkten, die sich nur schwer oder gar nicht verdampfen lassen, können problemlos gesputtert werden. Dies erweitert die Palette der Materialien, die abgeschieden werden können, einschließlich hochschmelzender Metalle und Keramiken.
-
Reproduzierbarkeit und Automatisierung:
- Das Sputtern bietet eine hervorragende Reproduzierbarkeit und eine einfachere Prozessautomatisierung im Vergleich zu Verfahren wie E-Beam oder thermisches Verdampfen. Dies macht es ideal für die Herstellung hoher Stückzahlen und gleichbleibender Schichtqualität.
-
Reaktive Abscheidung für optische Schichten:
- Durch Oxidation oder Nitrierung der gesputterten Metallionen können durch Sputtern Oxid- oder Nitridschichten mit präziser Zusammensetzung erzeugt werden, die sich für optische Beschichtungen und andere Spezialanwendungen eignen.
-
Niedertemperaturbetrieb:
- Durch Sputtern kann eine breite Palette von Materialien, einschließlich Kunststoffen und organischen Stoffen, bei niedrigeren Temperaturen beschichtet werden. Dadurch werden thermische Schäden an empfindlichen Substraten minimiert.
-
Präzision auf molekularer Ebene:
- Das Verfahren ermöglicht eine Kontrolle auf atomarer Ebene, so dass makellose Grenzflächen zwischen den Materialien geschaffen und die Filmeigenschaften durch präzise Steuerung der Prozessparameter fein abgestimmt werden können.
-
Starke Filmhaftung und Stufenabdeckung:
- Gesputterte Schichten weisen eine starke Haftung und eine hervorragende Stufen- oder Durchkontaktierung auf und eignen sich daher für Mikroelektronik- und Halbleiteranwendungen.
-
Doppelseitige Beschichtung:
- Bei geeigneter mechanischer Konfiguration kann durch Sputtern eine gleichzeitige doppelseitige Beschichtung erfolgen, was die Prozesseffizienz und den Durchsatz erhöht.
-
Kompatibilität mit reaktiven Gasen und Ultrahochvakuum:
- Das Sputtern ist mit reaktiven Gasen kompatibel und kann unter Ultrahochvakuumbedingungen durchgeführt werden, was fortschrittliche Prozesse wie Epitaxiewachstum und hochreine Schichtabscheidung ermöglicht.
-
Kosteneffizienz:
- Im Vergleich zu anderen Abscheidungsmethoden ist das Sputtern relativ kostengünstig, was es zu einer attraktiven Option sowohl für die Forschung als auch für industrielle Anwendungen macht.
-
Gleichmäßige Schichten und hohe Packungsdichte:
- Gesputterte Schichten sind gleichmäßiger und haben eine höhere Packungsdichte, selbst bei niedrigen Temperaturen, was eine gleichbleibende Leistung und Haltbarkeit gewährleistet.
-
Breite Materialkompatibilität:
- Sputtern eignet sich für eine breite Palette von Materialien, einschließlich verschiedener Mischungen und Legierungen, und bietet im Vergleich zur thermischen Verdampfung mehr Flexibilität bei der Materialauswahl.
-
Wartungsfreier Betrieb:
- Das Verfahren ist wartungsfrei, was Ausfallzeiten und Betriebskosten reduziert und langfristige Zuverlässigkeit gewährleistet.
-
Verbesserte Prozesseffizienz:
- Merkmale wie die Schleuse am Ein- und Ausgang der Kammer verbessern die Prozesseffizienz und machen das Sputtern zu einer praktischen Wahl für Umgebungen mit hohem Durchsatz.
Zusammenfassend lässt sich sagen, dass das Sputtern ein äußerst anpassungsfähiges, präzises und kosteneffizientes Verfahren für die Abscheidung von Dünnschichten ist, das zahlreiche Vorteile für eine Vielzahl von Anwendungen bietet, von der Mikroelektronik bis zu optischen Beschichtungen und darüber hinaus.
Zusammenfassende Tabelle:
Vorteil | Beschreibung |
---|---|
Hervorragende Adhäsion | Die höhere kinetische Energie gewährleistet eine starke Haftung, selbst auf schwierigen Oberflächen. |
Vielseitigkeit bei der Beschichtungsausrichtung | Kann komplexe Geometrien in Bottom-up- oder Top-down-Konfigurationen beschichten. |
Materialien mit hohem Schmelzpunkt | Beschichtet mühelos Materialien wie hochschmelzende Metalle und Keramiken. |
Reproduzierbarkeit und Automatisierung | Ideal für die Herstellung hoher Stückzahlen mit gleichbleibender Schichtqualität. |
Reaktive Abscheidung | Erzeugt präzise Oxid- oder Nitridschichten für optische Beschichtungen. |
Betrieb bei niedrigen Temperaturen | Beschichtet Kunststoffe und organische Stoffe ohne thermische Schädigung. |
Präzision auf molekularer Ebene | Ermöglicht makellose Grenzflächen und einstellbare Schichteigenschaften. |
Starke Stufenbedeckung | Geeignet für Mikroelektronik- und Halbleiteranwendungen. |
Doppelseitige Beschichtung | Gleichzeitige Beschichtung erhöht die Effizienz und den Durchsatz. |
Kompatibilität mit reaktiven Gasen | Unterstützt fortschrittliche Prozesse wie Epitaxiewachstum und hochreine Abscheidung. |
Kosteneffizienz | Erschwinglich im Vergleich zu anderen Abscheidungsmethoden. |
Gleichmäßige Schichten | Gewährleistet gleichbleibende Leistung und Haltbarkeit. |
Breite Materialkompatibilität | Funktioniert mit verschiedenen Mischungen und Legierungen und bietet Flexibilität bei der Materialauswahl. |
Wartungsfrei | Reduziert Ausfallzeiten und Betriebskosten. |
Erhöhte Prozesseffizienz | Der Ein- und Ausgang der Schleusenkammer verbessert den Durchsatz in hochvolumigen Umgebungen. |
Sind Sie bereit, die Sputtering-Beschichtung für Ihre Projekte zu nutzen? Kontaktieren Sie uns noch heute um mehr zu erfahren!