DC-Sputtern ist eine weit verbreitete Technik der physikalischen Gasphasenabscheidung (PVD) zur Erzeugung dünner Schichten auf Substraten.Bei diesem Verfahren wird eine Gleichspannung an ein leitfähiges Zielmaterial in einer Niederdruck-Inertgasumgebung, in der Regel Argon, angelegt.Bei dem Verfahren wird das Gas ionisiert, um ein Plasma zu erzeugen, das Ionen auf das Target beschleunigt.Diese Ionen kollidieren mit dem Target und stoßen Atome aus, die sich auf einem nahegelegenen Substrat ablagern und einen dünnen Film bilden.Das Gleichstromsputtern wird wegen seiner Einfachheit, Kosteneffizienz und hohen Abscheidungsraten bevorzugt und eignet sich daher für Branchen wie Halbleiter, Optik und Schmuck.Besonders effektiv ist es bei leitfähigen Materialien wie Metallen.
Die wichtigsten Punkte werden erklärt:
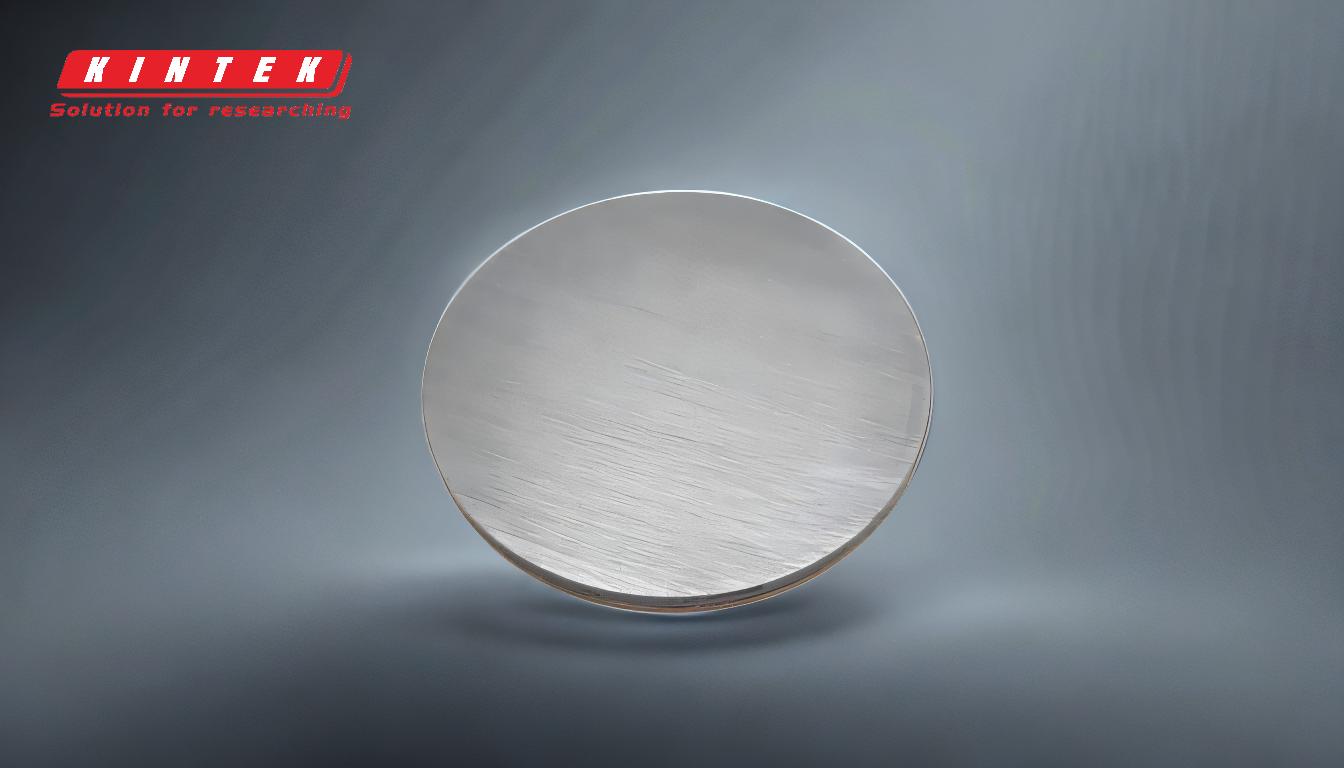
-
Grundprinzip des DC-Sputterns:
- Das DC-Sputtern ist ein PVD-Verfahren, bei dem ein leitfähiges Zielmaterial in einer Vakuumkammer mit ionisierten Gasteilchen (in der Regel Argon) beschossen wird.
- Es wird eine Gleichspannung angelegt, die ein Plasma erzeugt, das die Gasatome ionisiert.
- Diese Ionen werden auf das Target beschleunigt und stoßen Atome von dessen Oberfläche ab, die sich dann auf einem Substrat ablagern und einen dünnen Film bilden.
-
Vakuum Umgebung:
- Das Verfahren findet in einer Vakuumkammer statt, um eine Verunreinigung durch Luft oder andere Gase zu verhindern.
- Das Vakuum gewährleistet eine gleichmäßige Abscheidung und ermöglicht eine präzise Steuerung des Sputterprozesses.
-
Inertgas und Plasmabildung:
- Ein inertes Gas, in der Regel Argon, wird bei niedrigem Druck (1-100 mTorr) in die Kammer eingeleitet.
- Die angelegte Gleichspannung ionisiert das Gas und erzeugt ein Plasma aus positiv geladenen Ionen und freien Elektronen.
-
Mechanismus des Sputterns:
- Positiv geladene Argon-Ionen werden auf das negativ geladene Target beschleunigt.
- Beim Aufprall wird Energie auf die Zielatome übertragen, so dass sie von der Oberfläche abgestoßen (gesputtert) werden.
- Diese ausgestoßenen Atome wandern durch die Kammer und lagern sich auf dem Substrat ab.
-
Abscheidung von Dünnschichten:
- Die gesputterten Atome kondensieren auf dem Substrat und bilden einen dünnen Film.
- Das Verfahren eignet sich aufgrund der niedrigen Temperatur der gesputterten Partikel für wärmeempfindliche Substrate wie Kunststoffe.
-
Vorteile des DC-Sputterns:
- Einfach und kostengünstig im Vergleich zu anderen PVD-Verfahren.
- Hohe Abscheidungsraten für leitfähige Materialien wie reine Metalle (z. B. Fe, Cu, Ni).
- Geeignet für die Produktion in großem Maßstab und große Substrate.
-
Anwendungen:
- Weit verbreitet in Branchen wie Halbleiter, optische Beschichtungen und Schmuck.
- Ideal für die Abscheidung von leitenden und metallischen Dünnschichten.
-
Beschränkungen:
- In erster Linie für leitende Zielmaterialien geeignet.
- Nicht leitende Materialien erfordern alternative Techniken wie das HF-Sputtern.
Wenn man diese Schlüsselpunkte versteht, kann man die Effizienz und Vielseitigkeit des DC-Sputterns bei der Herstellung hochwertiger dünner Schichten für verschiedene industrielle Anwendungen schätzen.
Zusammenfassende Tabelle:
Aspekt | Einzelheiten |
---|---|
Verfahren | Beim DC-Sputtern wird ein leitfähiges Target in einer Vakuumkammer mit Inertgas verwendet. |
Grundprinzip | Ionisierte Gasteilchen beschießen das Ziel und schleudern Atome auf ein Substrat. |
Umgebung | Niederdruck-Vakuumkammer mit Argon-Gas. |
Vorteile | Kostengünstig, hohe Abscheideraten, geeignet für leitfähige Materialien. |
Anwendungen | Halbleiter, optische Beschichtungen, Schmuck. |
Beschränkungen | Nur effektiv für leitfähige Materialien; nicht leitfähige erfordern RF-Sputtern. |
Entdecken Sie, wie das DC-Sputtern Ihre Dünnschichtprozesse verbessern kann. Kontaktieren Sie unsere Experten noch heute !