Argon wird aufgrund seiner einzigartigen Eigenschaften, die es ideal für das Verfahren machen, häufig beim Magnetronsputtern eingesetzt.Es ist ein inertes Gas, d. h. es reagiert nicht mit dem Targetmaterial oder anderen Elementen, was einen sauberen und unkontaminierten Abscheidungsprozess gewährleistet.Das relativ hohe Atomgewicht von Argon ermöglicht eine effiziente Übertragung der kinetischen Energie bei Kollisionen im Plasma, was für den Ausstoß von Atomen aus dem Zielmaterial entscheidend ist.Außerdem ist Argon kostengünstig und in hoher Reinheit erhältlich, was es zu einer praktischen Wahl für industrielle Anwendungen macht.Seine Inertheit verhindert außerdem unerwünschte chemische Reaktionen und gewährleistet die Integrität der abgeschiedenen Dünnschicht.
Die wichtigsten Punkte erklärt:
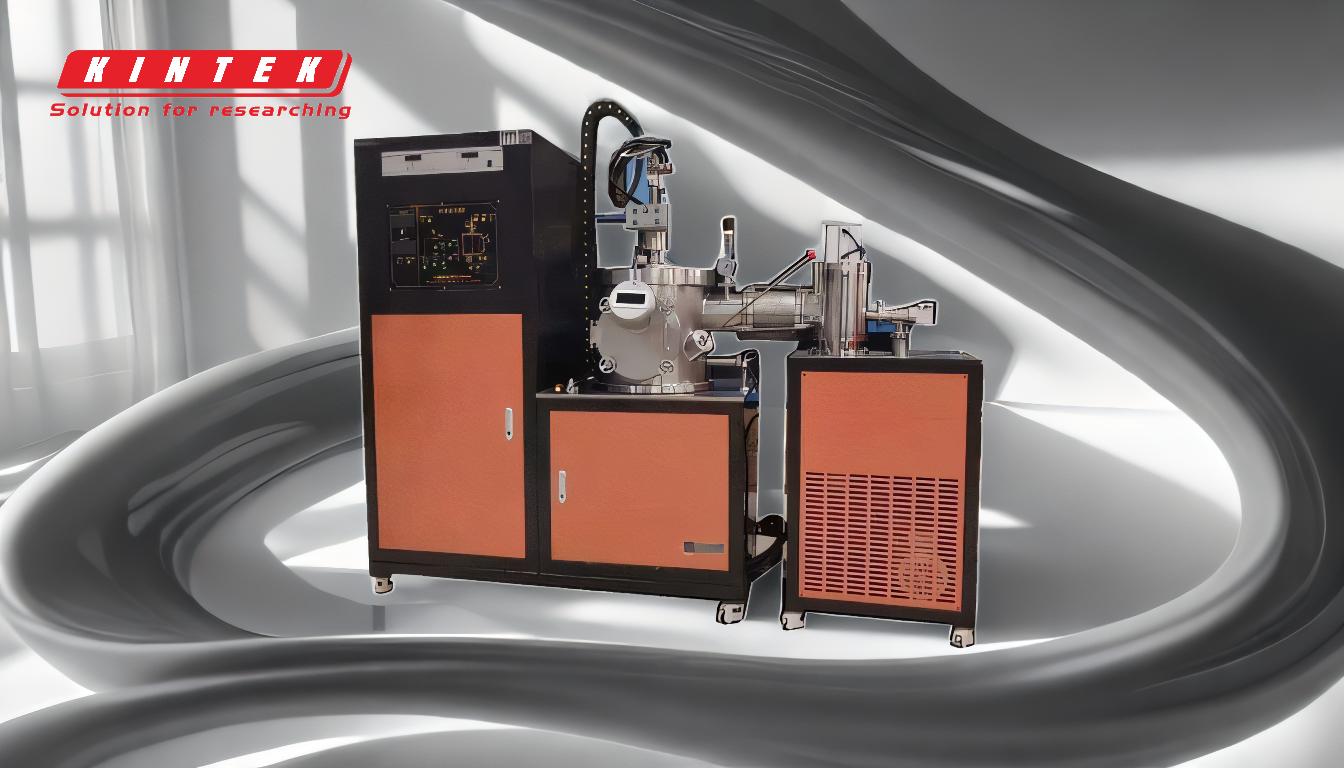
-
Inerte Natur von Argon:
- Argon ist ein Edelgas, d. h. es ist chemisch inert und reagiert nicht mit dem Targetmaterial oder anderen Elementen in der Zerstäubungskammer.
- Diese Inertheit gewährleistet, dass der Abscheidungsprozess sauber und frei von Verunreinigungen bleibt, was für die Herstellung hochwertiger Dünnschichten entscheidend ist.
- Reaktive Gase wie Sauerstoff könnten unerwünschte chemische Reaktionen mit dem Zielmaterial hervorrufen und die Zusammensetzung der abgeschiedenen Schicht verändern.
-
Hohe Sputtering-Rate:
- Argon hat im Vergleich zu anderen Inertgasen ein relativ hohes Atomgewicht, wodurch es die kinetische Energie bei hochenergetischen Kollisionen im Plasma besser übertragen kann.
- Diese hohe Energieübertragung ist für den effizienten Ausstoß von Atomen aus dem Zielmaterial unerlässlich und führt zu einer höheren Sputterrate.
- Die Effizienz von Argon beim Sputtern macht es zur bevorzugten Wahl gegenüber anderen Gasen, auch wenn andere Edelgase wie Krypton (Kr) und Xenon (Xe) ebenfalls verwendet werden können.
-
Kosteneffizienz und Verfügbarkeit:
- Argon ist im Vergleich zu anderen Inertgasen relativ preiswert, was es zu einer kostengünstigen Option für industrielle Anwendungen macht.
- Außerdem ist es in hoher Reinheit leicht erhältlich, was für die Gewährleistung konsistenter und zuverlässiger Sputterprozesse wichtig ist.
- Die Kombination aus niedrigen Kosten und hoher Verfügbarkeit macht Argon zu einer praktischen Wahl für groß angelegte Fertigungsprozesse.
-
Ionisierung und Plasmabildung:
- Beim Magnetronsputtern wird Argongas ionisiert, so dass ein Plasma entsteht.Die hochenergetischen Kollisionen im Plasma ionisieren die Argonatome und erzeugen positiv geladene Ionen.
- Diese Ionen werden dann in Richtung des Zielmaterials beschleunigt, wo sie mit der Oberfläche kollidieren und Atome aus dem Ziel ausstoßen.
- Die ausgestoßenen Atome kondensieren dann auf dem Substrat und bilden einen dünnen Film.Die Fähigkeit von Argon, effizient zu ionisieren und ein stabiles Plasma zu bilden, ist für den Sputterprozess entscheidend.
-
Vermeidung von unerwünschten Reaktionen:
- Die Verwendung von Argon gewährleistet, dass der Sputterprozess frei von unerwünschten chemischen Reaktionen ist, die bei der Verwendung reaktiver Gase auftreten könnten.
- Dies ist besonders wichtig bei der Abscheidung von Materialien, die empfindlich auf Oxidation oder andere chemische Veränderungen reagieren.
- Durch die Verwendung von Argon können die Hersteller sicherstellen, dass die abgeschiedene Schicht die gewünschten Eigenschaften und die Zusammensetzung beibehält.
-
Vergleich mit anderen Gasen:
- Zwar können auch andere Edelgase wie Krypton und Xenon für das Sputtern verwendet werden, doch sind sie im Allgemeinen teurer und weniger leicht verfügbar als Argon.
- Argon bietet ein ausgewogenes Verhältnis zwischen Wirksamkeit und Kosten und ist daher das am häufigsten verwendete Gas beim Magnetronsputtern.
- Die Wahl des Gases kann auch von den spezifischen Anforderungen des Beschichtungsprozesses abhängen, z. B. von der Notwendigkeit eines höheren Energietransfers oder der Vermeidung bestimmter chemischer Reaktionen.
Zusammenfassend lässt sich sagen, dass Argon aufgrund seiner Inertheit, hohen Sputterrate, Kosteneffizienz und Verfügbarkeit die ideale Wahl für das Magnetronsputtern ist.Seine Fähigkeit, ein stabiles Plasma zu bilden und unerwünschte chemische Reaktionen zu verhindern, gewährleistet einen sauberen und effizienten Abscheidungsprozess, der für die Herstellung hochwertiger dünner Schichten in verschiedenen industriellen Anwendungen unerlässlich ist.
Zusammenfassende Tabelle:
Die wichtigsten Vorteile von Argon beim Magnetronsputtern |
---|
Inerte Natur - Verhindert unerwünschte chemische Reaktionen und gewährleistet eine saubere Abscheidung. |
Hohe Sputtering-Rate - Effiziente Energieübertragung für schnelleren Atomausstoß. |
Kostengünstig - Erschwinglich und in hoher Reinheit weithin verfügbar. |
Stabile Plasmabildung - Gewährleistet eine gleichmäßige und zuverlässige Dünnschichtabscheidung. |
Verhindert Kontamination - Bewahrt die Integrität der Schicht durch Vermeidung von Oxidation. |
Möchten Sie Ihren Magnetron-Sputter-Prozess optimieren? Kontaktieren Sie noch heute unsere Experten um mehr über die Verwendung von Argon für die hochwertige Dünnschichtabscheidung zu erfahren!