Die Dicke der Sputterbeschichtung reicht in der Regel von Angström bis zu Mikrometern, abhängig von der jeweiligen Anwendung und den Prozessparametern.Die Dicke wird von Faktoren wie der Sputterzeit, der auf das Target angewandten Leistung, den Materialeigenschaften und den Prozessbedingungen wie Vakuumdruck und Abstand zwischen Target und Probe beeinflusst.Die Beschichtungen können ein- oder mehrlagig sein, wobei die Materialien auf der Grundlage ihrer Leitfähigkeit, Korngröße und Sekundärelektronenemissionseigenschaften ausgewählt werden.Das Verfahren ist in hohem Maße anpassbar und ermöglicht eine genaue Kontrolle über die Dicke und Qualität der abgeschiedenen Schicht.
Die wichtigsten Punkte erklärt:
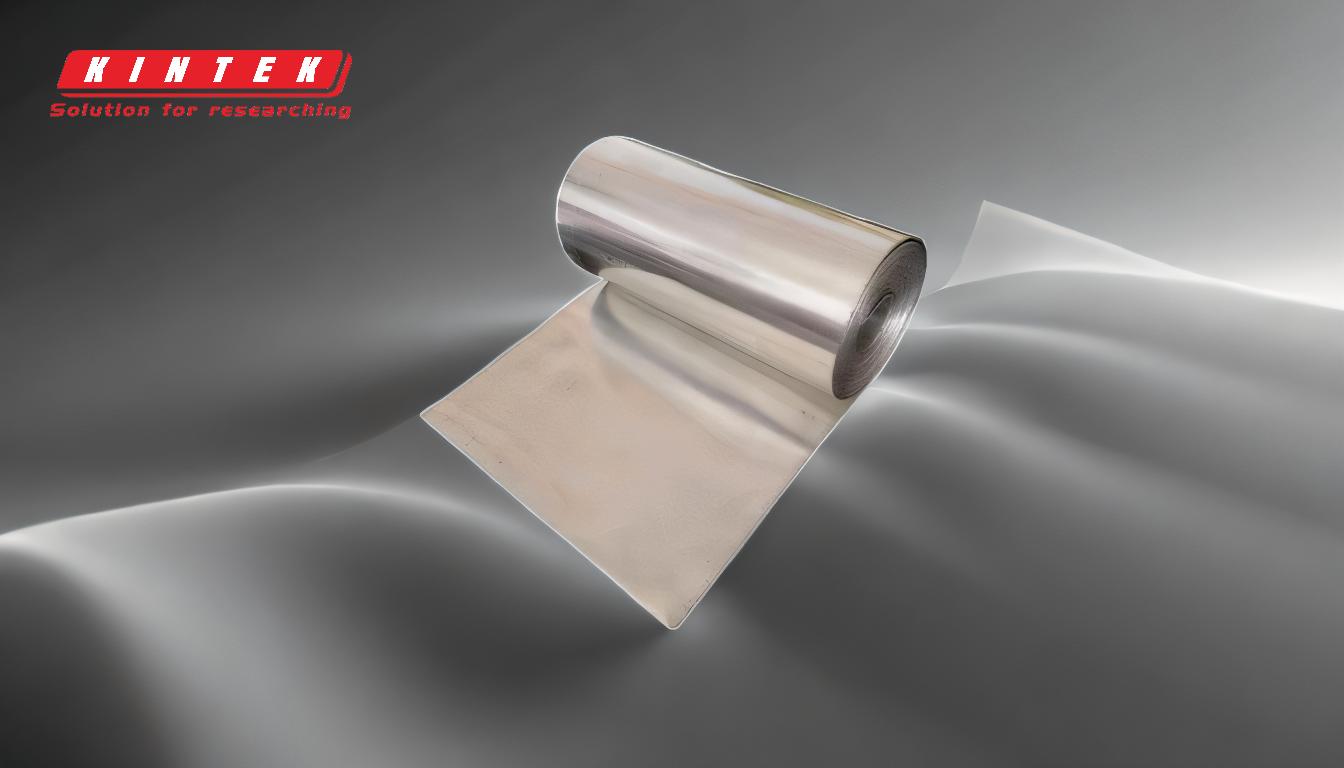
-
Typischer Dickenbereich:
- Sputterbeschichtungen reichen im Allgemeinen von Angström (Å) bis Mikrometer (µm) .
- Angström (Å):1 Å = 0,1 Nanometer (nm).Dieser Bereich wird für ultradünne Beschichtungen verwendet, die häufig in Anwendungen eingesetzt werden, die eine hohe Präzision erfordern, z. B. in der Halbleiterherstellung oder der Nanotechnologie.
- Mikrometer (µm):1 µm = 1000 nm.Dieser Bereich wird für dickere Beschichtungen verwendet, wie z. B. bei Schutzschichten oder optischen Beschichtungen.
-
Faktoren, die die Schichtdicke beeinflussen:
- Sputtering Zeit:Je länger der Zerstäubungsprozess dauert, desto dicker ist die Beschichtung.Dies ist eine direkte Beziehung, da mit der Zeit mehr Material abgeschieden wird.
- Auf das Ziel angewandte Leistung:Höhere Leistungsstufen erhöhen die Energie der gesputterten Partikel, was zu einer höheren Abscheiderate und potenziell dickeren Schichten führt.
- Materialeigenschaften:Die Masse und das Energieniveau der Beschichtungspartikel beeinflussen, wie sie sich auf dem Substrat ablagern.Schwerere Materialien oder Partikel mit höherer Energie können mehr Material pro Zeiteinheit abscheiden.
-
Prozessbedingungen:
- Unterdruck:Ein geringerer Druck in der Probenkammer kann zu einer kontrollierteren und gleichmäßigeren Abscheidung führen.
- Abstand zwischen Ziel und Probe:Ein kürzerer Abstand kann die Abscheiderate erhöhen, während ein längerer Abstand zu gleichmäßigeren Schichten führen kann.
- Sputtergas:Die Art des verwendeten Gases (z. B. Argon) kann die Energie und Richtung der gesputterten Partikel beeinflussen.
-
Einschichtige vs. mehrschichtige Beschichtungen:
- Einstoffliche Beschichtungen:Diese sind einfach, mit einer einheitlichen Schicht aus einem Material.Die Schichtdicke wird durch die Sputtering-Parameter gesteuert.
- Mehrschichtige Beschichtungen:Dabei handelt es sich um abwechselnde Schichten aus verschiedenen Materialien.Jede Schicht kann je nach den gewünschten Eigenschaften (z. B. Leitfähigkeit, Reflexionsvermögen oder Haltbarkeit) eine unterschiedliche Dicke haben.Die Gesamtdicke ergibt sich aus der Summe der einzelnen Schichten.
-
Auswahl des Materials:
-
Materialien wie
Gold/Palladium (Au/Pd)
,
Platin (Pt)
und
Silber (Ag)
werden aufgrund ihrer spezifischen Eigenschaften häufig verwendet:
- Leitfähigkeit:Unverzichtbar für Anwendungen wie die Elektronenmikroskopie, wo die Beschichtung Elektrizität leiten muss, um Aufladung zu verhindern.
- Korngröße:Kleinere Korngrößen können zu glatteren Beschichtungen führen, die für hochauflösende Bilder wichtig sind.
- Sekundäre Elektronenemission:Diese Eigenschaft ist entscheidend für die Verstärkung des Signals bei Techniken wie der Rasterelektronenmikroskopie (REM).
-
Materialien wie
Gold/Palladium (Au/Pd)
,
Platin (Pt)
und
Silber (Ag)
werden aufgrund ihrer spezifischen Eigenschaften häufig verwendet:
-
Schlüsselparameter, die den Sputter-Beschichtungsprozess beeinflussen:
- Sputterstrom und -spannung:Diese steuern die Energie und die Geschwindigkeit der Partikelemission vom Target.
- Druck in der Probenkammer:In der Regel ist ein Hochvakuum erforderlich, um Verunreinigungen zu minimieren und die Abscheidungsumgebung zu kontrollieren.
- Targetdicke und Material:Die Eigenschaften des Targets beeinflussen die Sputterrate und die Qualität der abgeschiedenen Schicht.
- Material der Probe:Das Trägermaterial kann die Haftfestigkeit und die endgültigen Eigenschaften der Beschichtung beeinflussen.
-
Anwendungen und Anpassungen:
- Präzision Anwendungen:In Bereichen wie der Halbleiterherstellung müssen die Beschichtungen unter Umständen extrem dünn (Angström) und gleichmäßig sein.
- Schützende Beschichtungen:Für Anwendungen, die eine lange Lebensdauer erfordern, können dickere Beschichtungen (Mikrometer) verwendet werden.
- Optische Beschichtungen:Dabei handelt es sich oft um mehrschichtige Strukturen, um bestimmte Reflexions- oder Durchlässigkeitseigenschaften zu erreichen.
Zusammenfassend lässt sich sagen, dass die Dicke von Sputterschichten sehr variabel ist und von einer Reihe von Faktoren abhängt, darunter Prozessparameter, Materialeigenschaften und die spezifische Anwendung.Die Fähigkeit, diese Faktoren zu kontrollieren, ermöglicht die Herstellung von Beschichtungen, die präzise Anforderungen erfüllen, sei es für ultradünne Schichten in der Nanotechnologie oder dickere, haltbarere Beschichtungen in industriellen Anwendungen.
Zusammenfassende Tabelle:
Aspekt | Einzelheiten |
---|---|
Dickenbereich | Angström (Å) bis Mikrometer (µm) |
Wichtige Einflussfaktoren | Sputterzeit, Leistung, Materialeigenschaften, Vakuumdruck und Abstand |
Beschichtungsarten | Einlagig oder mehrlagig |
Gängige Materialien | Gold/Palladium, Platin, Silber |
Anwendungen | Halbleiterherstellung, Schutzschichten, optische Beschichtungen |
Benötigen Sie präzise Sputterbeschichtungen für Ihre Anwendung? Kontaktieren Sie noch heute unsere Experten um loszulegen!