Das HF-Sputtern ist zwar eine weit verbreitete Technik für die Dünnschichtabscheidung, hat jedoch einige bemerkenswerte Nachteile, die sich auf ihre Effizienz, Kosten und Anwendbarkeit in verschiedenen Szenarien auswirken können. Zu diesen Nachteilen gehören niedrige Abscheideraten, hohe Anlagen- und Betriebskosten, Schwierigkeiten bei der Erzielung gleichmäßiger Schichten und Probleme im Zusammenhang mit der Wärmeentwicklung und Verunreinigung. Das Verständnis dieser Einschränkungen ist für die Käufer von Anlagen und Verbrauchsmaterialien entscheidend, um fundierte Entscheidungen treffen zu können.
Die wichtigsten Punkte werden erklärt:
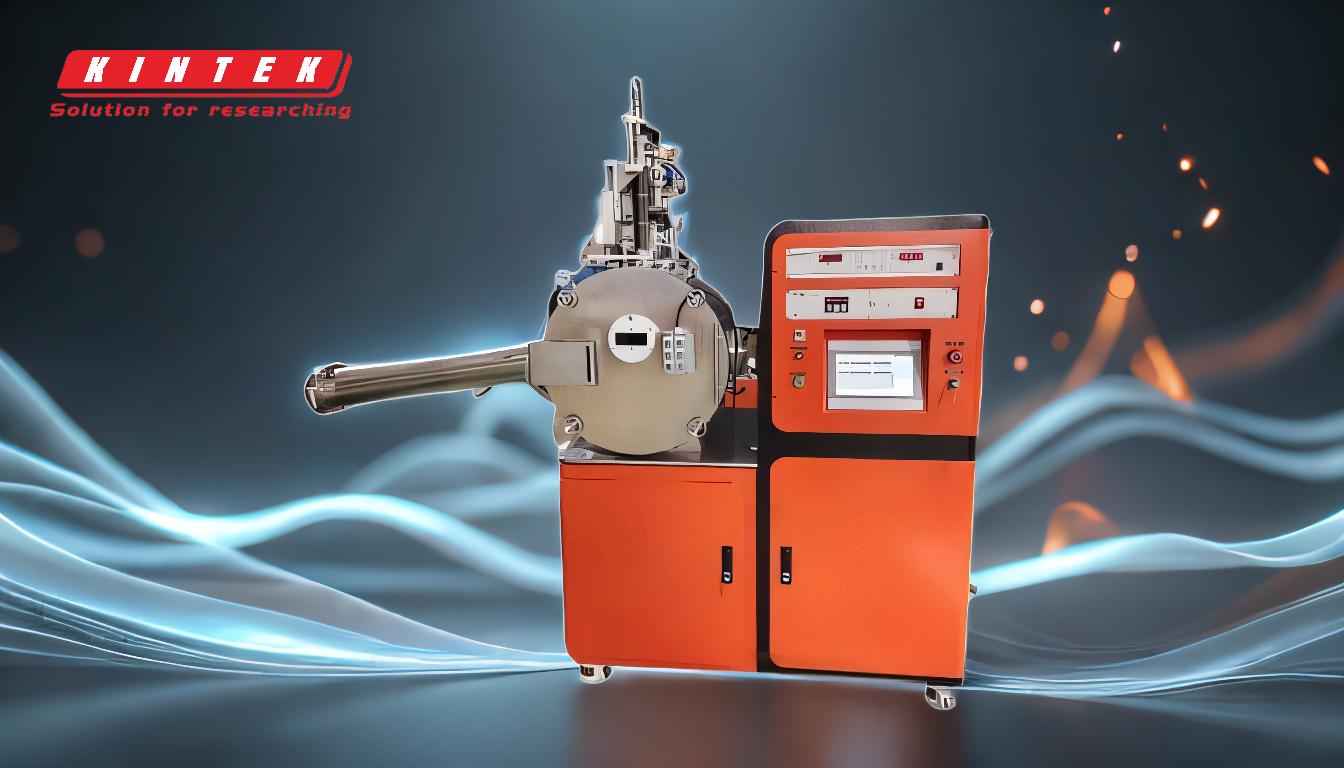
-
Niedrige Ablagerungsraten:
- Beim RF-Sputtern sind die Abscheideraten oft sehr niedrig, insbesondere bei bestimmten Materialien wie SiO2. Dadurch kann sich die Zeit, die zum Erreichen der gewünschten Schichtdicke erforderlich ist, erheblich verlängern, so dass das Verfahren im Vergleich zu anderen Abscheidungsmethoden wie der thermischen Verdampfung weniger effizient ist.
- Die langsame Abscheidegeschwindigkeit kann in Fertigungsumgebungen mit hohem Durchsatz, in denen Zeiteffizienz entscheidend ist, einen Engpass darstellen.
-
Hohe Kapital- und Betriebskosten:
- HF-Sputtersysteme erfordern teure HF-Stromversorgungen und zusätzliche Impedanzanpassungsschaltungen, die zu hohen Anfangsinvestitionen beitragen.
- Die Notwendigkeit spezieller Geräte, wie Sputterkanonen mit starken Dauermagneten, um magnetischen Streufeldern von ferromagnetischen Zielen entgegenzuwirken, erhöht die Systemkosten weiter.
- Die Betriebskosten sind auch deshalb höher, weil für die Erzeugung der Funkwellen mehr Energie benötigt wird, was zu einem höheren Energieverbrauch führt.
-
Komplexität und Wartung:
- Die Komplexität der RF-Sputteranlagen, einschließlich der Hochdruckgeräte und hochentwickelten Stromversorgungen, macht den Betrieb und die Wartung des Systems schwieriger.
- Das Verfahren reagiert empfindlich auf externe Faktoren wie magnetische Streufelder, die den Sputterprozess stören können und zusätzliche Maßnahmen zur Stabilisierung des Systems erforderlich machen.
-
Wärmeerzeugung und Wärmemanagement:
- Ein erheblicher Teil der auf das Target auftreffenden Energie wird zu Wärme, die wirksam abgeführt werden muss, um eine Überhitzung zu vermeiden und die Prozessstabilität zu erhalten.
- Eine Überhitzung kann zu einer thermischen Beanspruchung sowohl des Targets als auch des Substrats führen, was möglicherweise Schäden verursacht oder die Qualität der abgeschiedenen Schicht beeinträchtigt.
-
Herausforderungen in Bezug auf Gleichmäßigkeit und Haftung:
- Das Erreichen einer gleichmäßigen Schichtdicke, insbesondere auf komplexen Strukturen wie Turbinenschaufeln, kann aufgrund der ungleichmäßigen Verteilung des Abscheidungsflusses schwierig sein.
- Um eine gleichmäßige Beschichtung zu gewährleisten, müssen unter Umständen Vorrichtungen bewegt oder zusätzliche Schritte durchgeführt werden, was die Komplexität und die Kosten erhöht.
- Vor allem bei dicken Beschichtungen können aufgrund höherer Eigenspannungen Haftungsprobleme auftreten.
-
Verunreinigung Kontamination:
- Das RF-Sputtern arbeitet im Vergleich zum Verdampfen in einem geringeren Vakuumbereich, was das Risiko erhöht, dass Verunreinigungen in das Substrat gelangen.
- Gasförmige Verunreinigungen können im Plasma aktiviert werden, wodurch sich das Risiko einer Filmkontamination weiter erhöht.
- Bei der reaktiven Kathodenzerstäubung ist eine präzise Steuerung der Gaszusammensetzung erforderlich, um eine Vergiftung des Targets zu verhindern, was den Prozess noch komplexer macht.
-
Materialverschlechterung und Ineffizienz:
- Einige Materialien, insbesondere organische Feststoffe, sind anfällig für eine Zersetzung durch Ionenbeschuss während des Sputterprozesses.
- Sputtertargets sind oft teuer, und das Verfahren kann in Bezug auf den Materialverbrauch ineffizient sein, was zu höheren Kosten für Verbrauchsmaterialien führt.
-
Herausforderungen bei der Filmstrukturierung:
- Die Kombination von RF-Sputtern und Lift-off-Verfahren zur Schichtstrukturierung ist aufgrund der diffusen Transporteigenschaft des Sputterns schwierig, was eine vollständige Abschattung unmöglich macht.
- Dies kann zu Verunreinigungsproblemen führen und die Herstellung von strukturierten Filmen erschweren.
Zusammenfassend lässt sich sagen, dass das HF-Sputtern zwar eine vielseitige und weit verbreitete Technik ist, aber auch einige Nachteile aufweist, die sich auf ihre Effizienz, Kosten und Anwendbarkeit auswirken können. Dazu gehören niedrige Abscheideraten, hohe Investitions- und Betriebskosten, Komplexität der Anlagen und der Prozesssteuerung, Herausforderungen bei der Erzielung gleichmäßiger und haftender Beschichtungen sowie das Risiko von Verunreinigungen und Materialverschlechterung. Das Verständnis dieser Einschränkungen ist eine wesentliche Voraussetzung für fundierte Entscheidungen bei der Beschaffung von Anlagen und Verbrauchsmaterialien.
Zusammenfassende Tabelle:
Nachteil | Beschreibung |
---|---|
Niedrige Ablagerungsraten | Langsame Abscheidung, insbesondere bei Materialien wie SiO2, was die Effizienz beeinträchtigt. |
Hohe Kapital- und Betriebskosten | Teure HF-Netzteile, Spezialgeräte und erhöhter Energieverbrauch. |
Komplexität und Wartung | Empfindlich gegen äußere Faktoren, erfordert fortgeschrittene Stabilisierungsmaßnahmen. |
Wärmeerzeugung | Eine beträchtliche Wärmeproduktion erfordert ein wirksames Wärmemanagement. |
Probleme mit Gleichmäßigkeit und Haftung | Schwierigkeiten bei der Erzielung gleichmäßiger Beschichtungen, insbesondere bei komplexen Strukturen. |
Verunreinigung Kontamination | Höheres Risiko der Einbringung von Verunreinigungen aufgrund des geringeren Vakuumbereichs. |
Materialverschlechterung | Organische Materialien können sich durch den Ionenbeschuss während des Sputterns zersetzen. |
Herausforderungen bei der Filmstrukturierung | Die Kombination mit Lift-off-Verfahren ist schwierig, was zu Kontaminationsrisiken führt. |
Benötigen Sie Hilfe bei der Auswahl des richtigen Verfahrens zur Dünnschichtabscheidung? Kontaktieren Sie unsere Experten noch heute für maßgeschneiderte Lösungen!