Diamantähnliche Kohlenstoffbeschichtungen (DLC) bestehen hauptsächlich aus Kohlenstoffatomen, die in einer Kombination aus sp3- (diamantähnlich) und sp2-Bindungen (graphitähnlich) angeordnet sind.Diese Beschichtungen sind bekannt für ihre hohe Härte, ihren niedrigen Reibungskoeffizienten und ihre hervorragende Leistung in korrosiven Umgebungen.Das Verfahren zur Herstellung von DLC-Beschichtungen umfasst die Verwendung von Kohlenwasserstoffen, d. h. Verbindungen aus Wasserstoff und Kohlenstoff.Diese Elemente werden in eine Plasmaumgebung eingebracht, wo sie sich auf der Oberfläche des Substrats rekombinieren und die Beschichtung bilden.Die einzigartigen Eigenschaften von DLC-Beschichtungen machen sie ideal für Anwendungen, die verbesserte Gleiteigenschaften und Haltbarkeit erfordern.
Die wichtigsten Punkte werden erklärt:
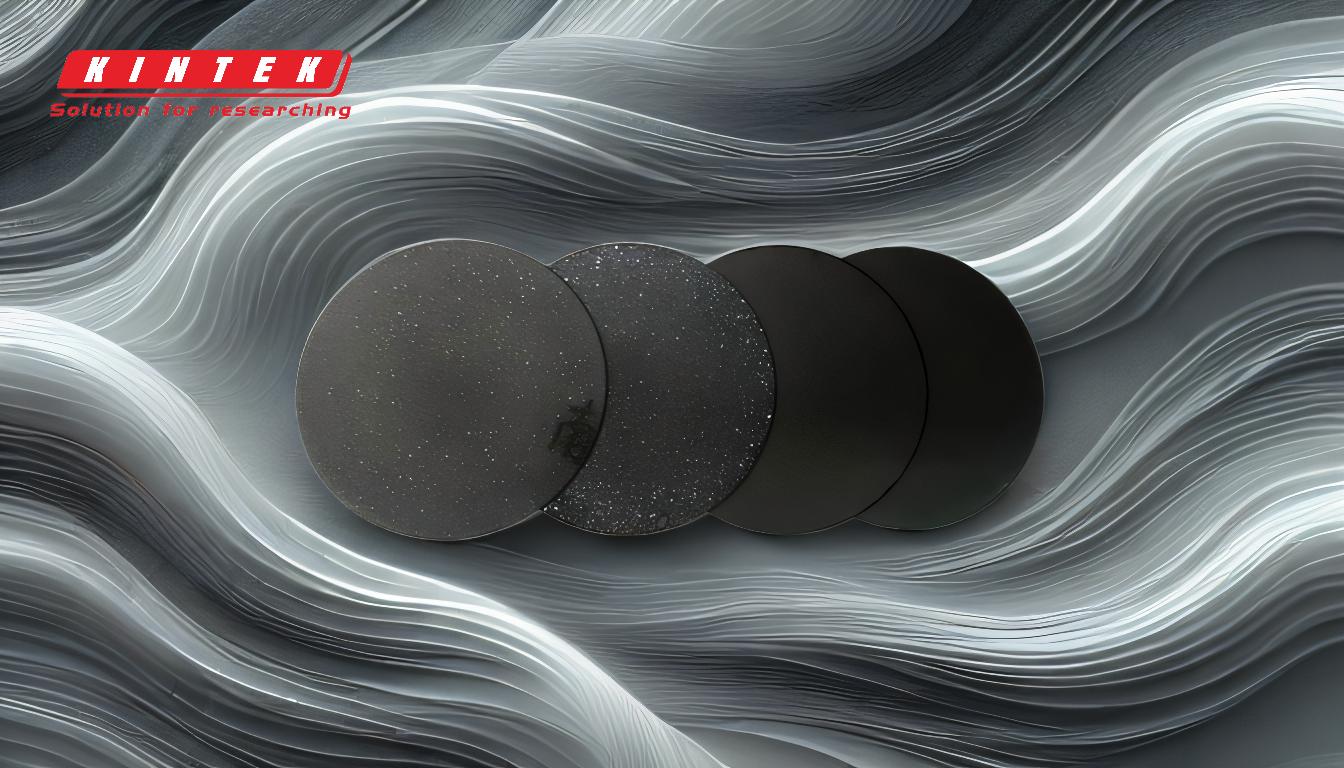
-
Zusammensetzung von DLC-Beschichtungen:
- Kohlenstoffbindungen: DLC-Beschichtungen zeichnen sich durch das Vorhandensein von sp3- (diamantähnlichen) und sp2-Bindungen (graphitähnlichen) Kohlenstoffverbindungen aus.Die sp3-Bindungen tragen zur Härte und Haltbarkeit der Beschichtung bei, während die sp2-Bindungen für einen geringeren Reibungskoeffizienten sorgen, wodurch sich die Beschichtung für Gleitanwendungen eignet.
- Kohlenwasserstoffe: Bei der Herstellung von DLC-Beschichtungen werden Kohlenwasserstoffe verwendet, also Verbindungen aus Wasserstoff und Kohlenstoff.Diese Kohlenwasserstoffe werden in eine Plasmaumgebung eingebracht, wo sie sich zersetzen und auf der Substratoberfläche rekombinieren, um die Beschichtung zu bilden.
-
Eigenschaften von DLC-Beschichtungen:
- Hohe Härte: Die sp3-Kohlenstoffbindungen in DLC-Schichten verleihen ihnen eine Härte, die mit der von Diamant vergleichbar ist.Dies macht DLC-Beschichtungen äußerst verschleiß- und abriebfest.
- Niedriger Reibungskoeffizient: Das Vorhandensein von sp2-Kohlenstoffbindungen in DLC-Beschichtungen führt zu einem niedrigen Reibungskoeffizienten, was bei Anwendungen mit gleitenden oder sich bewegenden Teilen von Vorteil ist.
- Korrosionsbeständigkeit: DLC-Beschichtungen weisen eine hervorragende Leistung in korrosiven Umgebungen auf und eignen sich daher für den Einsatz in Industrien, in denen die Komponenten rauen Bedingungen ausgesetzt sind.
-
Anwendung von DLC-Beschichtungen:
- Substrate: DLC-Beschichtungen können auf eine Vielzahl von Substraten aufgebracht werden, darunter Metalle (z. B. Edelstahl und Aluminium), Kunststoffe, Glas und Keramiken.Dank ihrer Vielseitigkeit können DLC-Beschichtungen in einer Vielzahl von Branchen eingesetzt werden.
- Branchen: Aufgrund ihrer einzigartigen Eigenschaften werden DLC-Beschichtungen häufig in Branchen wie der Automobil-, Luft- und Raumfahrt- sowie der Elektronikindustrie eingesetzt.Sie sind besonders wertvoll bei Anwendungen, bei denen die Komponenten hohem Verschleiß und Reibung ausgesetzt sind, wie z. B. bei Motorenteilen, Schneidwerkzeugen und elektronischen Komponenten.
-
Vergleich mit anderen Beschichtungsmaterialien:
- PVD-Beschichtungen: Während PVD-Beschichtungen (Physical Vapor Deposition) eine Vielzahl von Materialien wie Titan, Zirkonium und Gold enthalten können, sind DLC-Beschichtungen vor allem für ihre Zusammensetzung auf Kohlenstoffbasis und ihre einzigartigen Eigenschaften bekannt.PVD-Beschichtungen werden häufig zu dekorativen Zwecken oder zur Verbesserung der Oberflächeneigenschaften von Materialien verwendet, während DLC-Beschichtungen vor allem wegen ihrer mechanischen Eigenschaften geschätzt werden.
- CVD-Beschichtungen: CVD-Beschichtungen (Chemical Vapor Deposition) können Materialien wie Siliziumverbindungen, Kohlenstoff und Fluorkohlenstoffe enthalten.Während CVD-Beschichtungen auf bestimmte Leistungsziele zugeschnitten werden können, zeichnen sich DLC-Beschichtungen durch ihre Kombination aus hoher Härte und geringer Reibung aus, wodurch sie sich besonders für anspruchsvolle mechanische Anwendungen eignen.
-
Zukünftige Trends und Verbesserungen:
- Dotierung: Die Eigenschaften von DLC-Beschichtungen können durch Dotierung der Oberfläche mit anderen Materialien weiter verbessert werden.Durch die Zugabe von Silizium oder anderen Elementen kann die Beschichtung für bestimmte Leistungsziele funktionalisiert werden, z. B. für eine erhöhte Verschleißfestigkeit oder eine verbesserte thermische Stabilität.
- Fortschrittliche Anwendungen: Da die Industrie weiterhin höhere Anforderungen an die Leistungsfähigkeit von Materialien stellt, werden DLC-Beschichtungen wahrscheinlich vermehrt in fortschrittlichen Anwendungen zum Einsatz kommen, z. B. bei der Entwicklung von elektronischen Geräten der nächsten Generation, von Hochleistungskomponenten für die Automobilindustrie und von Luft- und Raumfahrtsystemen.
Zusammenfassend lässt sich sagen, dass DLC-Beschichtungen in erster Linie aus Kohlenstoffatomen bestehen, die in einer Kombination aus sp3- und sp2-Bindungen angeordnet sind, wobei während des Beschichtungsvorgangs Kohlenwasserstoffe hinzugefügt werden.Diese Beschichtungen bieten eine einzigartige Kombination aus hoher Härte, geringer Reibung und Korrosionsbeständigkeit, was sie für eine breite Palette industrieller Anwendungen ideal macht.Die Möglichkeit, DLC-Beschichtungen durch Dotierung und andere Techniken weiter zu verbessern, stellt sicher, dass sie auch in Zukunft eine entscheidende Rolle bei der Entwicklung fortschrittlicher Materialien und Komponenten spielen werden.
Zusammenfassende Tabelle:
Aspekt | Einzelheiten |
---|---|
Zusammensetzung | Kohlenstoffatome mit sp3- (diamantartig) und sp2-Bindungen (graphitartig). |
Eigenschaften | Hohe Härte, geringe Reibung und Korrosionsbeständigkeit. |
Anwendungen | Automobilindustrie, Luft- und Raumfahrt, Elektronik und mehr. |
Substrate | Metalle, Kunststoffe, Glas und Keramiken. |
Zukünftige Erweiterungen | Dotierung mit Silizium oder anderen Elementen zur Leistungssteigerung. |
Erfahren Sie, wie DLC-Beschichtungen Ihre Komponenten verbessern können. Kontaktieren Sie uns noch heute !