Extrusion und Coextrusion sind beides Fertigungsverfahren zur Herstellung von Kunststoffprodukten, die sich jedoch in ihrer Komplexität und Anwendung unterscheiden. Bei der Standardextrusion wird festes Kunststoffgranulat geschmolzen und durch eine Düse gepresst, um eine kontinuierliche Form wie Rohre, Schläuche oder Platten herzustellen. Bei der Co-Extrusion hingegen werden mehrere Extruder eingesetzt, um verschiedene Materialien in einem einzigen Produkt zu kombinieren, wodurch geschichtete oder gekapselte Strukturen entstehen. Dies ermöglicht eine verbesserte Funktionalität, wie z. B. verbesserte Barriereeigenschaften, Festigkeit oder ästhetisches Erscheinungsbild. Während die Extrusion bei Produkten aus einem einzigen Material einfacher und kostengünstiger ist, eignet sich die Co-Extrusion ideal für Anwendungen, die mehrere Materialeigenschaften in einem Produkt erfordern.
Die wichtigsten Punkte erklärt:
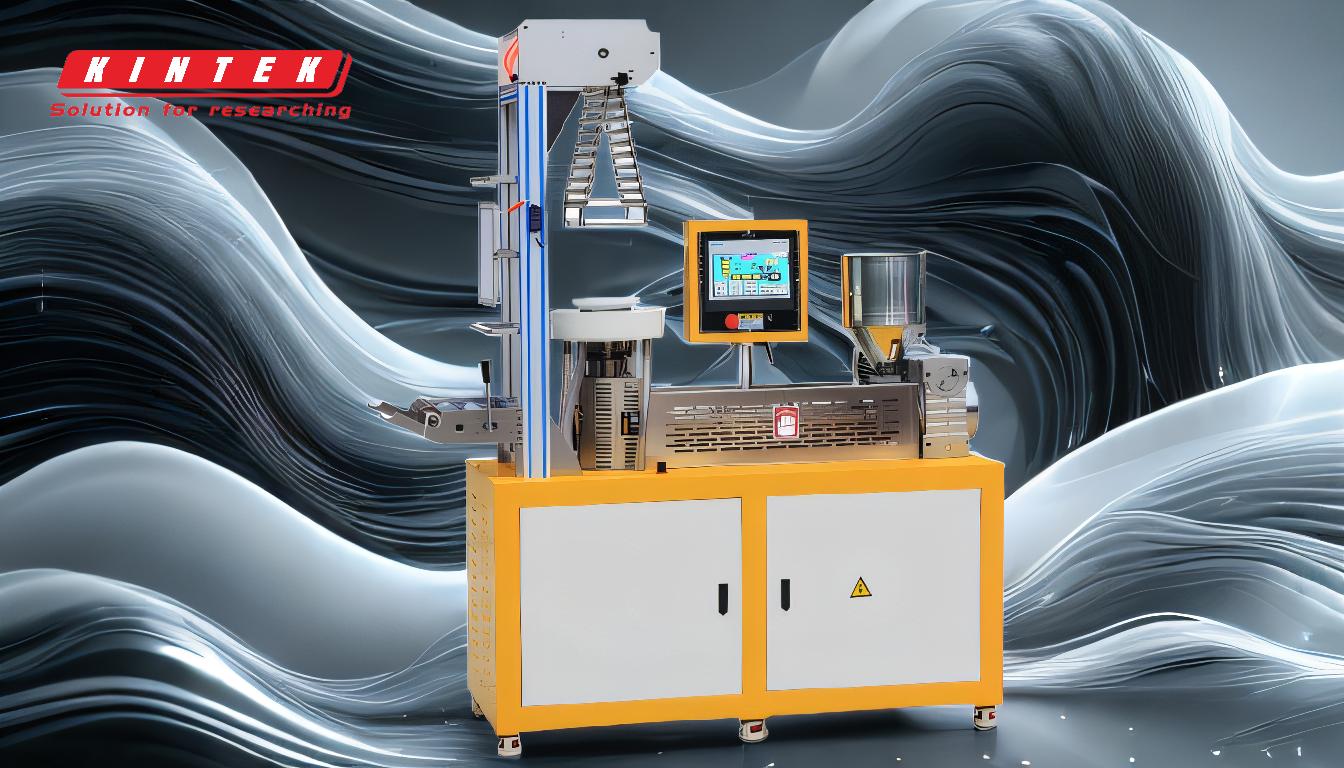
-
Prozess-Übersicht:
- Extrusion: Bei der Standardextrusion wird ein festes Kunststoffgranulat durch Schwerkraft in eine Formvorrichtung geleitet. Kompressionsschnecken schmelzen das Granulat, und der geschmolzene Kunststoff wird durch eine Düse gepresst, um eine kontinuierliche Form zu erzeugen. Dieses Verfahren wird für Produkte aus einem einzigen Material wie Rohre, Schläuche und Platten verwendet.
- Co-Extrusion: Bei der Co-Extrusion arbeiten mehrere Extruder gleichzeitig. Jeder Extruder verarbeitet ein anderes Material, das dann in einer Düse zu einem einzigen Produkt mit mehreren Schichten oder eingekapselten Komponenten kombiniert wird. Dies wird für Produkte verwendet, die mehrere Materialeigenschaften erfordern, wie z. B. Lebensmittelverpackungen mit Barriereschichten.
-
Material Verwendung:
- Extrusion: Verwendet eine einzige Art von Kunststoffmaterial. Das Verfahren ist einfach und daher kosteneffizient für die Herstellung einheitlicher Produkte.
- Co-Extrusion: Es werden mehrere Materialien verwendet, darunter verschiedene Kunststoffarten oder sogar Kombinationen von Kunststoff mit anderen Materialien wie Klebstoffen oder Sperrschichten. Dadurch sind komplexere und funktionellere Produktdesigns möglich.
-
Anwendungen:
- Extrusion: Wird häufig für Produkte wie PVC-Rohre, Kunststoffplatten und Profile verwendet. Sie ist ideal für Anwendungen, bei denen ein einziges Material ausreicht.
- Co-Extrusion: Wird für Anwendungen verwendet, die mehrere Materialeigenschaften erfordern, wie z. B. mehrschichtige Lebensmittelverpackungen, Automobilteile mit unterschiedlichen Oberflächen- und Kernmaterialien und medizinische Schläuche mit Sperrschichten.
-
Vorteile und Beschränkungen:
-
Extrusion:
- Vorteile : Einfachheit, Kosteneffizienz und hohe Produktionsraten für Produkte aus einem einzigen Material.
- Beschränkungen : Begrenzt auf Produkte aus einem einzigen Material, die möglicherweise nicht den Anforderungen für komplexere Anwendungen entsprechen.
-
Co-Extrusion:
- Vorteile : Die Möglichkeit, verschiedene Materialien zu kombinieren, verbessert die Funktionalität und Leistung des Produkts. Dazu können verbesserte Barriereeigenschaften, Festigkeit und Ästhetik gehören.
- Beschränkungen : Komplexer und teurer, da mehrere Extruder und eine präzise Steuerung des Materialflusses und der Schichtung erforderlich sind.
-
Extrusion:
-
Ausrüstung und Einrichtung:
- Extrusion: Erfordert einen einzelnen Extruder, eine Düse und einen Kühlkreislauf System. Die Einrichtung ist relativ einfach und kann leicht für die Produktion großer Mengen skaliert werden.
- Co-Extrusion: Erfordert mehrere Extruder, von denen jeder für ein anderes Material zuständig ist, und eine komplexe Düse, die diese Materialien zu einem einzigen Produkt zusammenfügen kann. Die Einrichtung ist komplexer und erfordert eine präzise Steuerung, um die richtige Materialschichtung und -bindung zu gewährleisten.
-
Qualität und Leistung:
- Extrusion: Erzeugt einheitliche Produkte mit gleichbleibenden Eigenschaften. Allerdings sind die Eigenschaften auf die des verwendeten Materials beschränkt.
- Co-Extrusion: Ermöglicht die Herstellung von Produkten mit maßgeschneiderten Eigenschaften, wie z. B. erhöhte Festigkeit, Flexibilität oder Barriereleistung. Dies macht es für anspruchsvollere Anwendungen geeignet.
Zusammenfassend lässt sich sagen, dass die Extrusion ein einfacheres und kostengünstigeres Verfahren für Produkte aus einem einzigen Material ist, während die Co-Extrusion die Möglichkeit bietet, durch die Kombination mehrerer Materialien komplexere und funktionellere Produkte herzustellen. Die Wahl zwischen den beiden Verfahren hängt von den spezifischen Anforderungen des herzustellenden Produkts ab.
Zusammenfassende Tabelle:
Blickwinkel | Extrusion | Co-Extrusion |
---|---|---|
Verfahren | Ein Extruder, ein Material, einfaches Verfahren | Mehrere Extruder, mehrere Materialien, komplexer Schichtaufbau |
Werkstoffe | Einzelner Kunststofftyp | Mehrere Materialien (z. B. Kunststoffe, Klebstoffe, Sperrschichten) |
Anwendungen | Rohre, Schläuche, Platten, Profile | Mehrschichtige Lebensmittelverpackungen, Automobilteile, medizinische Schläuche |
Vorteile | Kostengünstig, hohe Produktionsraten, Einfachheit | Verbesserte Funktionalität (z. B. Barriereeigenschaften, Festigkeit, Ästhetik) |
Beschränkungen | Begrenzt auf Produkte aus einem einzigen Material | Komplexer, teurer, erfordert präzise Kontrolle |
Ausrüstung | Einzelner Extruder, Düse, Kühlsystem | Mehrere Extruder, komplexe Düse, präzise Steuerung der Schichtung |
Qualität | Einheitliche Produkte mit gleichbleibenden Eigenschaften | Maßgeschneiderte Eigenschaften (z. B. Festigkeit, Flexibilität, Barriereleistung) |
Benötigen Sie Hilfe bei der Entscheidung zwischen Extrusion und Co-Extrusion für Ihr Projekt? Kontaktieren Sie noch heute unsere Experten !