PVD-Beschichtung (Physical Vapor Deposition) und Pulverbeschichtung sind zwei unterschiedliche Technologien zur Oberflächenbehandlung, die zur Verbesserung der Haltbarkeit, des Aussehens und der Funktionalität von Materialien eingesetzt werden.Bei der PVD-Beschichtung werden dünne Schichten von Werkstoffen wie Metallen, Legierungen und Keramiken in einer Vakuumkammer bei hohen Temperaturen aufgetragen, wodurch dichte, haltbare und umweltfreundliche Beschichtungen entstehen.Bei der Pulverbeschichtung hingegen werden organische Polymerpulver durch elektrostatische Aufladung bei niedrigeren Temperaturen aufgebracht, was eine breite Palette von Farben und Oberflächen zu geringeren Kosten ermöglicht.Während PVD-Beschichtungen haltbarer sind und sich für Hochleistungsanwendungen eignen, sind Pulverbeschichtungen kostengünstiger und vielseitiger für ästhetische Zwecke.
Die wichtigsten Punkte erklärt:
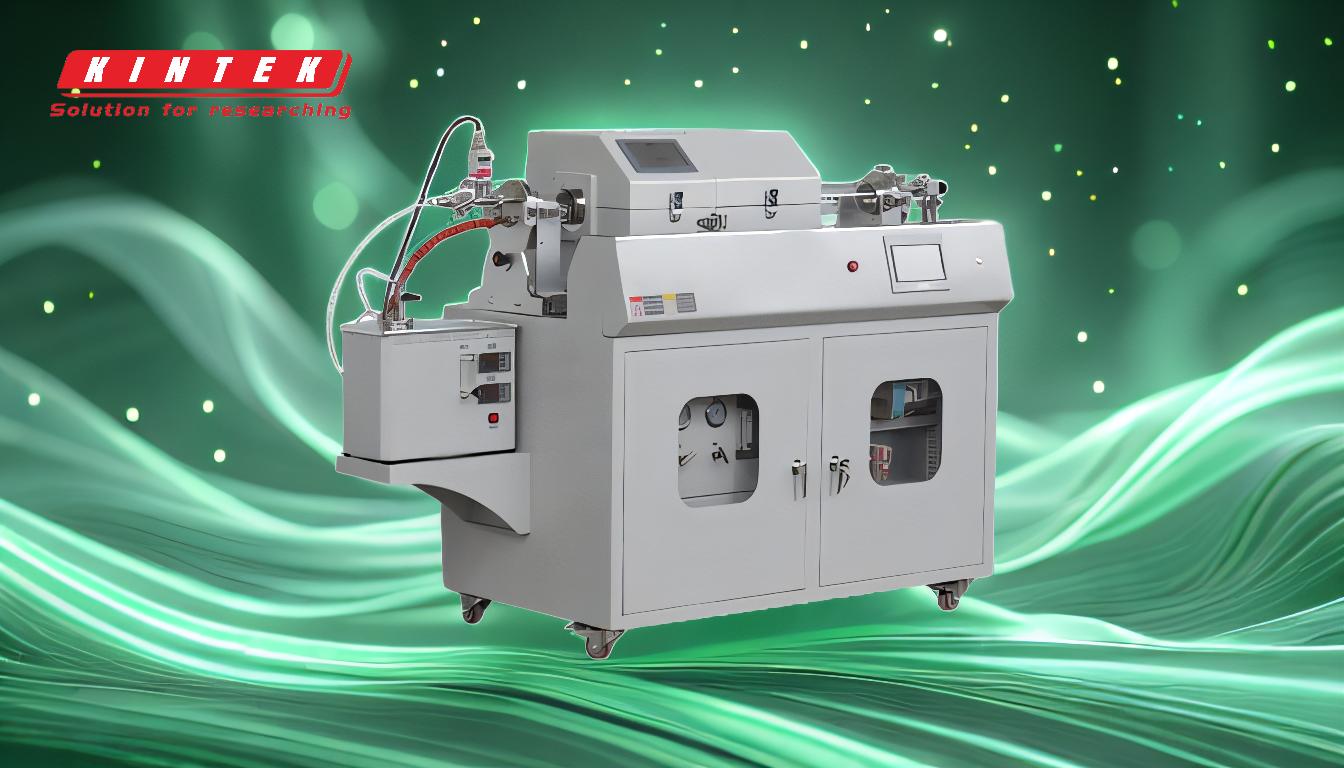
-
Prozess und Ausrüstung:
- PVD-Beschichtung:Erfordert eine spezielle Ausrüstung, einschließlich einer großen Vakuumkammer.Das Verfahren umfasst hohe Temperaturen und die physikalische Verdampfung von Materialien, die dann auf das Substrat aufgebracht werden.
- Pulverbeschichtung:Nutzt eine elektrostatische Aufladung, um pulverförmige Polymere auf die Oberfläche aufzutragen.Es arbeitet bei niedrigeren Temperaturen und erfordert keine Vakuumumgebung.
-
Material-Kompatibilität:
- PVD-Beschichtung:Kann eine Vielzahl von Materialien abscheiden, darunter Metalle, Legierungen und Keramiken.Dadurch eignet es sich für Anwendungen, die eine hohe Haltbarkeit und spezifische Materialeigenschaften erfordern.
- Pulverbeschichtung:Begrenzt auf organische Polymere, was die Verwendung auf Anwendungen beschränkt, bei denen ästhetische Qualitäten und Korrosionsbeständigkeit wichtiger sind als mechanische Beständigkeit.
-
Beschichtungsdicke und Dauerhaftigkeit:
- PVD-Beschichtung:Erzeugt extrem dünne Beschichtungen im Bereich von 0,5 bis 5 Mikrometern.Diese Beschichtungen sind dicht, gleichmäßig und äußerst haltbar, was sie ideal für Anwendungen mit hoher Beanspruchung macht.
- Pulverbeschichtung:Führt in der Regel zu dickeren Beschichtungen im Vergleich zu PVD.Sie sind zwar weniger dicht und haltbar, bieten aber eine hervorragende Korrosionsbeständigkeit und eine große Vielfalt an Oberflächenbehandlungen.
-
Umweltverträglichkeit:
- PVD-Beschichtung:Umweltfreundlicher, da keine Abfälle oder schädlichen Gase entstehen.Das Verfahren ist sauberer und entspricht einer nachhaltigen Herstellungspraxis.
- Pulverbeschichtung:Obwohl im Vergleich zu flüssigen Beschichtungen nur wenig Abfall anfällt, werden immer noch organische Polymere verwendet, was sich auf die Umwelt auswirken kann.
-
Kosten und Anwendung:
- PVD-Beschichtung:Im Allgemeinen teurer aufgrund der speziellen Ausrüstung und des komplexen Verfahrens.Es wird bei Hochleistungsanwendungen eingesetzt, bei denen Haltbarkeit und spezifische Materialeigenschaften entscheidend sind.
- Pulverbeschichtung:Weniger kostspielig und vielseitiger, mit einer breiten Palette an Farben und Oberflächen.Es wird häufig für ästhetische Zwecke und für Anwendungen verwendet, bei denen die Kosten einen wichtigen Faktor darstellen.
-
Temperatur-Anforderungen:
- PVD-Beschichtung:Erfordert hohe Temperaturen, was die Art der Substrate, die ohne Schaden beschichtet werden können, einschränken kann.
- Pulverbeschichtung:Das Verfahren arbeitet bei niedrigeren Temperaturen und eignet sich daher für ein breiteres Spektrum von Materialien, einschließlich hitzeempfindlicher Werkstoffe.
Zusammenfassend lässt sich sagen, dass die Wahl zwischen PVD-Beschichtung und Pulverbeschichtung von den spezifischen Anforderungen der Anwendung abhängt, einschließlich Faktoren wie Haltbarkeit, Materialverträglichkeit, Umweltauswirkungen und Kosten.Die PVD-Beschichtung ist ideal für hochleistungsfähige, langlebige Anwendungen, während die Pulverbeschichtung besser für kostengünstige, ästhetische Oberflächen geeignet ist.
Zusammenfassende Tabelle:
Blickwinkel | PVD-Beschichtung | Pulverbeschichtung |
---|---|---|
Verfahren | Hochtemperaturabscheidung in einer Vakuumkammer | Elektrostatischer Auftrag von Polymerpulvern bei niedrigeren Temperaturen |
Material-Kompatibilität | Metalle, Legierungen, Keramiken | Organische Polymere |
Dicke der Beschichtung | 0,5 bis 5 Mikrometer (dünn, dicht, dauerhaft) | Dickere Beschichtungen (weniger dicht, ausgezeichnete Korrosionsbeständigkeit) |
Langlebigkeit | Sehr haltbar, ideal für stark beanspruchte Anwendungen | Weniger haltbar, besser für ästhetische Oberflächen |
Umweltverträglichkeit | Keine Abfälle oder schädlichen Gase, umweltfreundlich | Minimaler Abfall, aber mit organischen Polymeren |
Kosten | Teuer aufgrund der speziellen Ausrüstung und des Verfahrens | Kostengünstig, vielseitig für ästhetische Zwecke |
Temperatur | Hohe Temperaturen, begrenzte Substratverträglichkeit | Niedrigere Temperaturen, geeignet für hitzeempfindliche Materialien |
Sie sind sich noch nicht sicher, welche Beschichtung für Ihre Bedürfnisse die richtige ist? Kontaktieren Sie noch heute unsere Experten für eine persönliche Beratung!