Ein Kalzinator ist ein spezielles Wärmebehandlungsgerät, das vor allem in der Industrie und der Metallurgie eingesetzt wird, um Materialien bei hohen Temperaturen unterhalb ihres Schmelzpunktes zu erhitzen. Sein Hauptzweck besteht darin, flüchtige Verunreinigungen wie Wasser, Kohlendioxid oder Schwefeldioxid aus Metallerzen oder anderen Substanzen zu entfernen. Dieser als Kalzinierung bezeichnete Prozess ist in Branchen wie der Zementherstellung von entscheidender Bedeutung, wo Kalkstein kalziniert wird, um Klinker, einen wichtigen Bestandteil von Beton, herzustellen. Darüber hinaus werden Kalzinieranlagen zur Trocknung, Oxidation und chemischen Umwandlung eingesetzt, was sie zu vielseitigen Werkzeugen in der Materialverarbeitung macht. Sie arbeiten in Hochtemperaturumgebungen, häufig in Drehrohröfen, und sind für das Erreichen der gewünschten Materialeigenschaften und -reinheit unerlässlich.
Die wichtigsten Punkte werden erklärt:
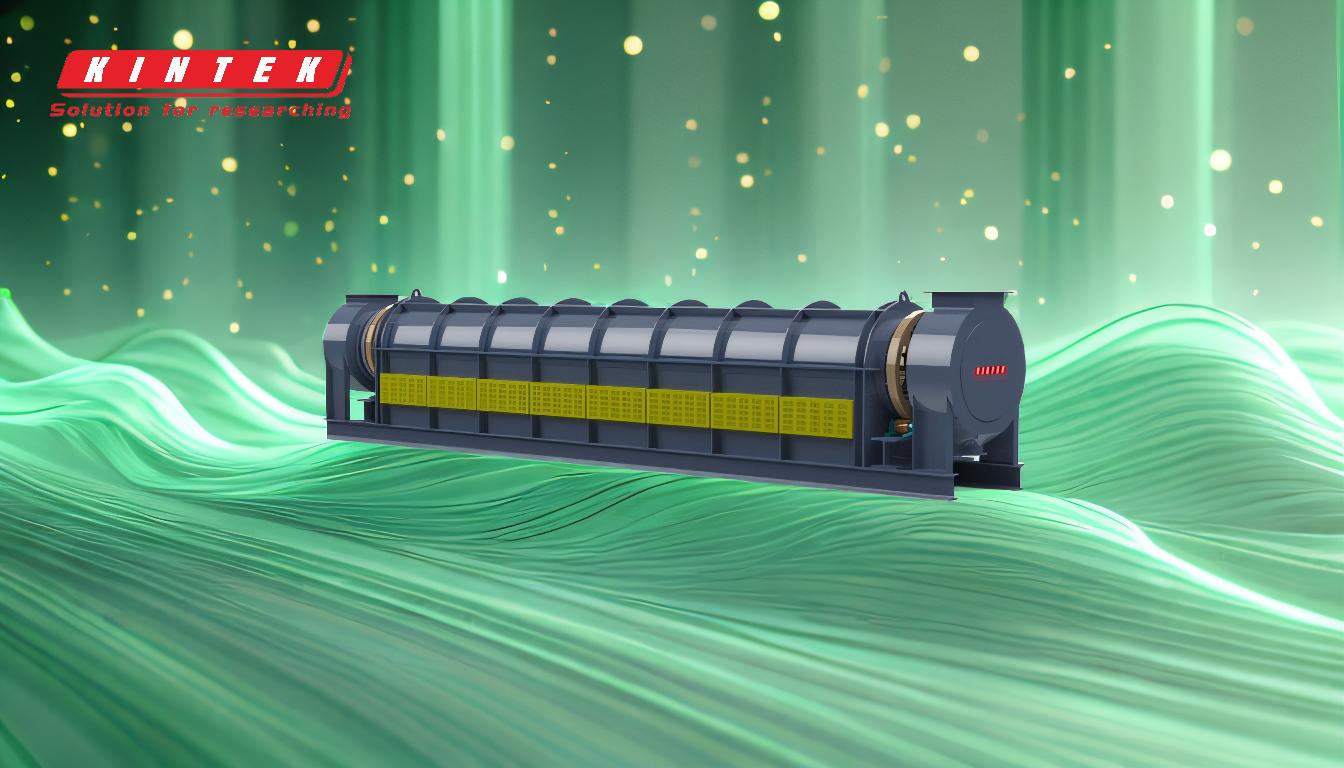
-
Definition und Zweck der Kalzinierung:
- Das Kalzinieren ist ein thermischer Prozess, bei dem Materialien unter Anwesenheit von wenig Luft oder Sauerstoff auf hohe Temperaturen (unterhalb ihres Schmelzpunkts) erhitzt werden.
- Der Hauptzweck besteht darin, flüchtige Verunreinigungen wie Feuchtigkeit, Kohlendioxid oder Schwefeldioxid aus Metallerzen oder anderen Stoffen zu entfernen.
- Dieser Prozess ist entscheidend für die Reinigung von Materialien und deren Vorbereitung für die weitere industrielle Nutzung.
-
Anwendungen von Kalzinieranlagen:
- Entfernen von Wasser: Kalziniermittel werden eingesetzt, um die absorbierte Feuchtigkeit aus den Materialien zu vertreiben und so Trockenheit und Stabilität zu gewährleisten.
- Eliminierung flüchtiger Inhaltsstoffe: Sie entfernen flüchtige Verbindungen wie Kohlendioxid oder Schwefeldioxid, die die Materialeigenschaften beeinträchtigen können.
- Oxidation: Kalzinatoren können einen Stoff ganz oder teilweise oxidieren und so seine chemische Zusammensetzung für bestimmte Anwendungen verändern.
- Zementherstellung: Eine der häufigsten Anwendungen ist die Kalzinierung von Kalkstein zur Herstellung von Klinker, einem wichtigen Bestandteil der Zementherstellung.
-
Rolle in industriellen Prozessen:
- Kalzinatoren sind ein wesentlicher Bestandteil pyrometallurgischer Prozesse, bei denen hohe Temperaturen zur Gewinnung und Reinigung von Metallen aus Erzen verwendet werden.
- Sie werden auch bei chemischen Umwandlungen, der Verbrennung von organischen Stoffen und der thermischen Desorption eingesetzt, was sie in verschiedenen Branchen vielseitig einsetzbar macht.
-
Funktionsweise von Drehrohröfen:
- Drehrohröfen, die häufig als Kalzinieranlagen verwendet werden, sind so konzipiert, dass sie Ultrahochtemperaturumgebungen für kontinuierliche oder diskontinuierliche Prozesse bereitstellen.
- Sie fungieren als Wärmetauscher, Trockner, Kalzinator und Verbrennungsanlage und eignen sich daher für eine Vielzahl von thermischen Verarbeitungsaufgaben.
- In der Zementherstellung erleichtern Drehrohröfen das Kalzinieren von Kalkstein und setzen die chemischen Reaktionen in Gang, die zur Bildung von Klinker erforderlich sind.
-
Bedeutung in der Klinkerproduktion:
- Bei der Zementherstellung vermischen sich im Kalzinator vorgewärmtes Rohmehl und Brennstoff in einem heißen Luftstrom, um die Kalzinierungsreaktion einzuleiten.
- Diese Reaktion ist der erste Schritt zur Herstellung von Klinker, der dann zu Zement gemahlen wird.
-
Vielseitigkeit und Anpassungsfähigkeit:
- Kalzinieranlagen lassen sich an verschiedene Materialien und Verfahren anpassen, darunter Trocknen, Sintern, Reduktionsrösten und Verbrennung.
- Ihre Fähigkeit, bei hohen Temperaturen zu arbeiten und unterschiedliche Materialien zu verarbeiten, macht sie in Branchen wie Metallurgie, chemische Verarbeitung und Bauwesen unverzichtbar.
Durch die Kenntnis dieser wichtigen Punkte können Einkäufer von Geräten und Verbrauchsmaterialien die Rolle von Kalzinieranlagen in ihren spezifischen industriellen Anwendungen besser einschätzen und fundierte Entscheidungen über deren Einsatz und Wartung treffen.
Zusammenfassende Tabelle:
Hauptaspekt | Beschreibung |
---|---|
Definition | Ein thermisches Verfahren zur Entfernung flüchtiger Verunreinigungen bei hohen Temperaturen. |
Primärer Zweck | Reinigen von Materialien durch Entfernen von Wasser, CO₂ oder SO₂. |
Anwendungen | Trocknung, Oxidation, chemische Umwandlungen und Zementherstellung. |
Rolle in der Industrie | Unverzichtbar in der Pyrometallurgie, Zementherstellung und chemischen Verarbeitung. |
Funktionsweise in Drehrohröfen | Hochtemperaturumgebungen für kontinuierliche oder diskontinuierliche Prozesse. |
Vielseitigkeit | Geeignet für Trocknung, Sinterung, Reduktionsröstung und Verbrennung. |
Sind Sie bereit, Ihre Materialverarbeitung mit einem Kalzinator zu optimieren? Kontaktieren Sie noch heute unsere Experten um mehr zu erfahren!