CVD (Chemical Vapor Deposition) und PVD (Physical Vapor Deposition) sind zwei weit verbreitete Verfahren zur Abscheidung von Dünnschichten, die jeweils ihre eigenen Vorteile und Einschränkungen haben.Die Wahl zwischen CVD und PVD hängt von der jeweiligen Anwendung, den Materialanforderungen und den betrieblichen Zwängen ab.CVD eignet sich besser für Anwendungen, die gleichmäßige Beschichtungen in komplexen Geometrien und Hochtemperaturumgebungen erfordern, während PVD ideal für temperaturempfindliche Materialien und Anwendungen ist, die schnellere Abscheidungsraten benötigen.Im Folgenden werden die wichtigsten Unterschiede, Vorteile und Grenzen beider Verfahren erläutert, um zu ermitteln, welches Verfahren für bestimmte Anwendungsfälle besser geeignet ist.
Die wichtigsten Punkte erklärt:
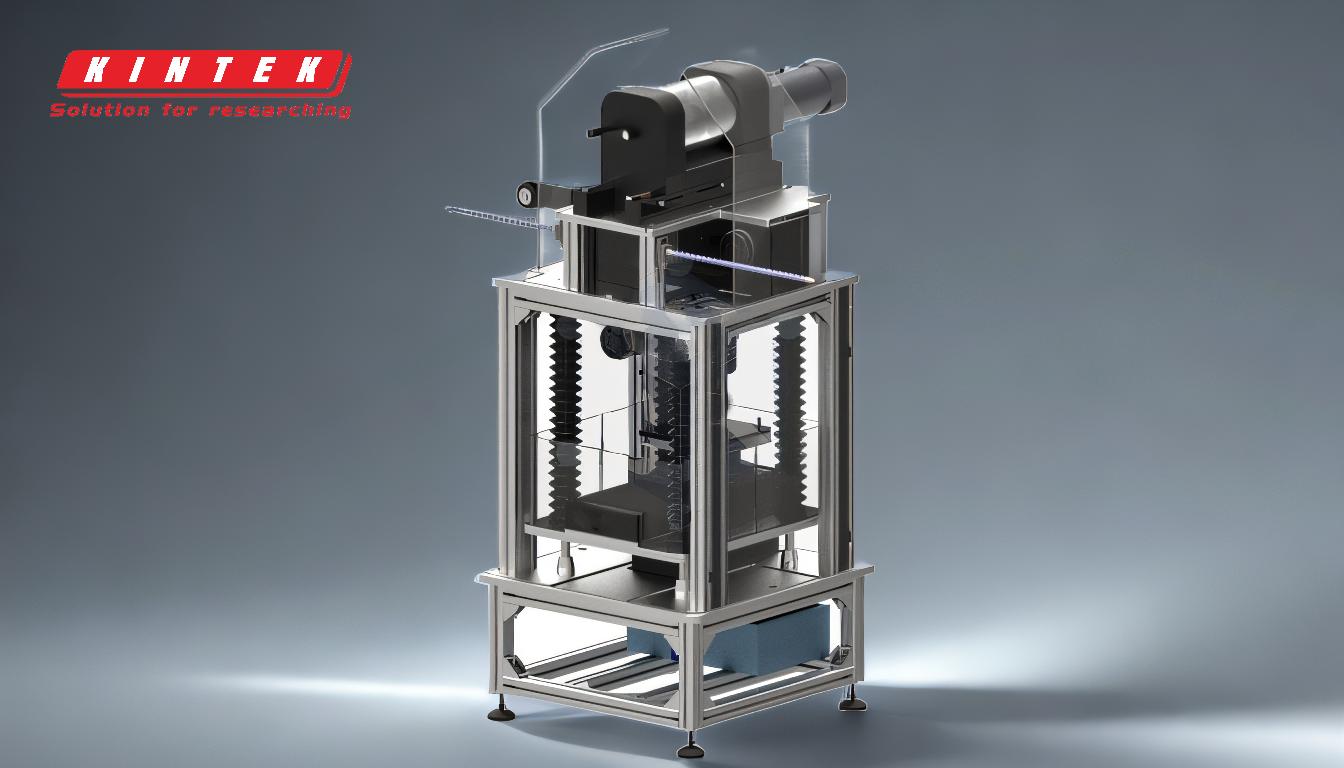
-
Mechanismus der Ablagerung:
- CVD:Es handelt sich um chemische Reaktionen zwischen gasförmigen Vorläufern und der Substratoberfläche, wobei eine feste Beschichtung entsteht.Dieses Verfahren ist multidirektional und ermöglicht eine gleichmäßige Beschichtung auch bei komplexen Geometrien und tiefen Löchern.
- PVD:Physikalische Verfahren wie Sputtern oder Verdampfen, um feste Materialien auf das Substrat aufzubringen.Es handelt sich um ein Sichtlinienverfahren, was bedeutet, dass es für die Beschichtung schattiger Bereiche oder komplexer Formen weniger effektiv ist.
-
Betriebstemperaturen:
- CVD:Das Verfahren arbeitet bei höheren Temperaturen (450°C bis 1050°C) und ist daher für temperaturempfindliche Materialien wie bestimmte Polymere oder niedrigschmelzende Substrate nicht geeignet.
- PVD:Arbeitet bei niedrigeren Temperaturen (250°C bis 450°C) und ist damit die bessere Wahl für temperaturempfindliche Materialien.
-
Bereich der Beschichtungsmaterialien:
- CVD:Hauptsächlich für die Abscheidung von Keramiken und Polymeren verwendet.Dabei können flüchtige chemische Verbindungen verwendet werden, die die Abscheidung von Elementen ermöglichen, die sich nur schwer verdampfen lassen.
- PVD:Kann ein breiteres Spektrum an Materialien abscheiden, darunter Metalle, Legierungen und Keramik, und ist damit vielseitiger für verschiedene Anwendungen.
-
Gleichmäßigkeit und Dichte der Beschichtung:
- CVD:Durch den chemischen Reaktionsprozess werden dichtere und gleichmäßigere Beschichtungen erzeugt, die auch bei komplexen Geometrien eine vollständige Abdeckung gewährleisten.
- PVD:Die Beschichtungen sind weniger dicht und weniger gleichmäßig, können aber schneller aufgetragen werden, was sie für Anwendungen geeignet macht, bei denen es auf Geschwindigkeit ankommt.
-
Sichtlinieneinschränkungen:
- CVD:Keine Begrenzung durch Sichtlinieneffekte, so dass die Beschichtung auch in tiefen Löchern, schattigen Bereichen und komplexen Geometrien möglich ist.
- PVD:Begrenzt durch die Sichtlinie, daher weniger effektiv für die Beschichtung komplizierter Formen oder Bereiche, die nicht direkt der Beschichtungsquelle ausgesetzt sind.
-
Energieverbrauch und thermische Begrenzungen:
- CVD:Erfordert hohe Energiekosten für die Erwärmung der Gasphase und des Substrats, was ein Nachteil in Bezug auf die Betriebskosten und die Umweltbelastung sein kann.
- PVD:Arbeitet im Vakuum und bei niedrigeren Temperaturen, wodurch der Energieverbrauch gesenkt wird und es sich besser für temperaturempfindliche Anwendungen eignet.
-
Anwendungen:
- CVD:Wird häufig in der Halbleiterfertigung, der Optoelektronik und bei Anwendungen eingesetzt, die hochreine, gleichmäßige Beschichtungen erfordern.
- PVD:Weit verbreitet in dekorativen Beschichtungen, verschleißfesten Beschichtungen und Anwendungen mit temperaturempfindlichen Materialien.
-
Material Abfall:
- CVD:Es fällt weniger Materialabfall an, da nur der erwärmte Bereich beschichtet wird.Moderne Techniken wie computergesteuerte Laser können die selektive Beschichtung weiter verbessern.
- PVD:Kann aufgrund der Art des physikalischen Abscheidungsverfahrens zu mehr Materialabfall führen.
-
Schichtdicke und Glätte:
- CVD:Erzeugt in der Regel dickere und glattere Schichten, die sich ideal für Anwendungen eignen, die eine hohe Haltbarkeit und Präzision erfordern.
- PVD:Erzeugt dünnere Folien mit geringerer Glätte, geeignet für Anwendungen, bei denen Geschwindigkeit und Vielseitigkeit im Vordergrund stehen.
-
Kosten und Komplexität:
- CVD:Einfacher zu bedienen und keine komplizierte Einrichtung erforderlich, aber die hohen Energiekosten und thermischen Einschränkungen können die Betriebskosten erhöhen.
- PVD:Erfordert eine Vakuumumgebung, was die Komplexität und die Kosten der Einrichtung erhöhen kann, bietet aber schnellere Abscheidungsraten und einen geringeren Energieverbrauch.
Zusammenfassend lässt sich sagen, dass die Wahl zwischen CVD und PVD von den spezifischen Anforderungen der jeweiligen Anwendung abhängt.CVD eignet sich besser für Hochtemperatur- und Präzisionsanwendungen, die gleichmäßige Beschichtungen erfordern, während PVD besser für temperaturempfindliche Materialien und Anwendungen geeignet ist, die schnellere Abscheidungsraten erfordern.Beide Verfahren haben ihre eigenen Vorteile und Grenzen, und die Entscheidung sollte auf einer gründlichen Bewertung der Betriebs- und Materialanforderungen beruhen.
Zusammenfassende Tabelle:
Blickwinkel | CVD | PVD |
---|---|---|
Mechanismus der Abscheidung | Chemische Reaktionen, multidirektional, gleichmäßige Abdeckung | Physikalische Prozesse, Sichtlinie, weniger effektiv bei komplexen Formen |
Betriebstemperaturen | Hoch (450°C bis 1050°C), ungeeignet für temperaturempfindliche Materialien | Niedrig (250°C bis 450°C), ideal für temperaturempfindliche Materialien |
Bereich der Beschichtungsmaterialien | Hauptsächlich Keramiken und Polymere | Metalle, Legierungen, Keramiken, breitere Materialvielfalt |
Gleichmäßigkeit der Beschichtung | Dichtere, gleichmäßigere Beschichtungen | Weniger dichte, weniger gleichmäßige, aber schnellere Abscheidungsraten |
Sichtlinie | Nicht eingeschränkt, wirksam bei komplexen Geometrien | Begrenzt, weniger effektiv für schattige Bereiche |
Energieverbrauch | Hohe Energiekosten aufgrund der hohen Temperaturen | Geringerer Energieverbrauch, arbeitet im Vakuum |
Anwendungen | Halbleiter, Optoelektronik, hochreine Beschichtungen | Dekorative, verschleißfeste, temperaturempfindliche Anwendungen |
Materialabfall | Weniger Abfall, selektive Beschichtungstechniken | Mehr Abfall aufgrund des physikalischen Abscheidungsverfahrens |
Schichtdicke | Dickere, glattere Filme | Dünnere, weniger glatte Folien |
Kosten und Komplexität | Leichtere Einrichtung, höhere Betriebskosten | Komplexer Vakuumaufbau, schnellere Abscheidung, geringere Energiekosten |
Sind Sie noch unsicher, welche Dünnschichtabscheidungstechnik für Ihre Anwendung die richtige ist? Kontaktieren Sie noch heute unsere Experten für eine persönliche Beratung!