CVD-Beschichtungen (Chemical Vapor Deposition) sind in verschiedenen Branchen weit verbreitet, da sie dichte, reine und gleichmäßige Beschichtungen ermöglichen.Die Dicke von CVD-Beschichtungen liegt in der Regel zwischen 5 und 20 Mikrometern, je nach Anwendung und Material.Diese Dicke ist deutlich höher als bei PVD-Beschichtungen (Physical Vapor Deposition), die in der Regel nur 2-5 Mikrometer dick sind.CVD-Beschichtungen sind bekannt für ihre hervorragende Haftung und ihre Fähigkeit, komplexe Geometrien, einschließlich tiefer Löcher und Innenwände, zu beschichten.Allerdings können die hohen Verarbeitungstemperaturen (800-1000 °C) und die daraus resultierenden Zugspannungen beim Abkühlen zu feinen Rissen führen, so dass CVD für unterbrochene Schneidprozesse weniger geeignet ist.Trotz dieser Einschränkungen sind CVD-Beschichtungen sehr abrieb- und verschleißfest, was sie ideal für Anwendungen mit unregelmäßig geformten Werkzeugen und Halbleiterbeschichtungen macht.
Die wichtigsten Punkte erklärt:
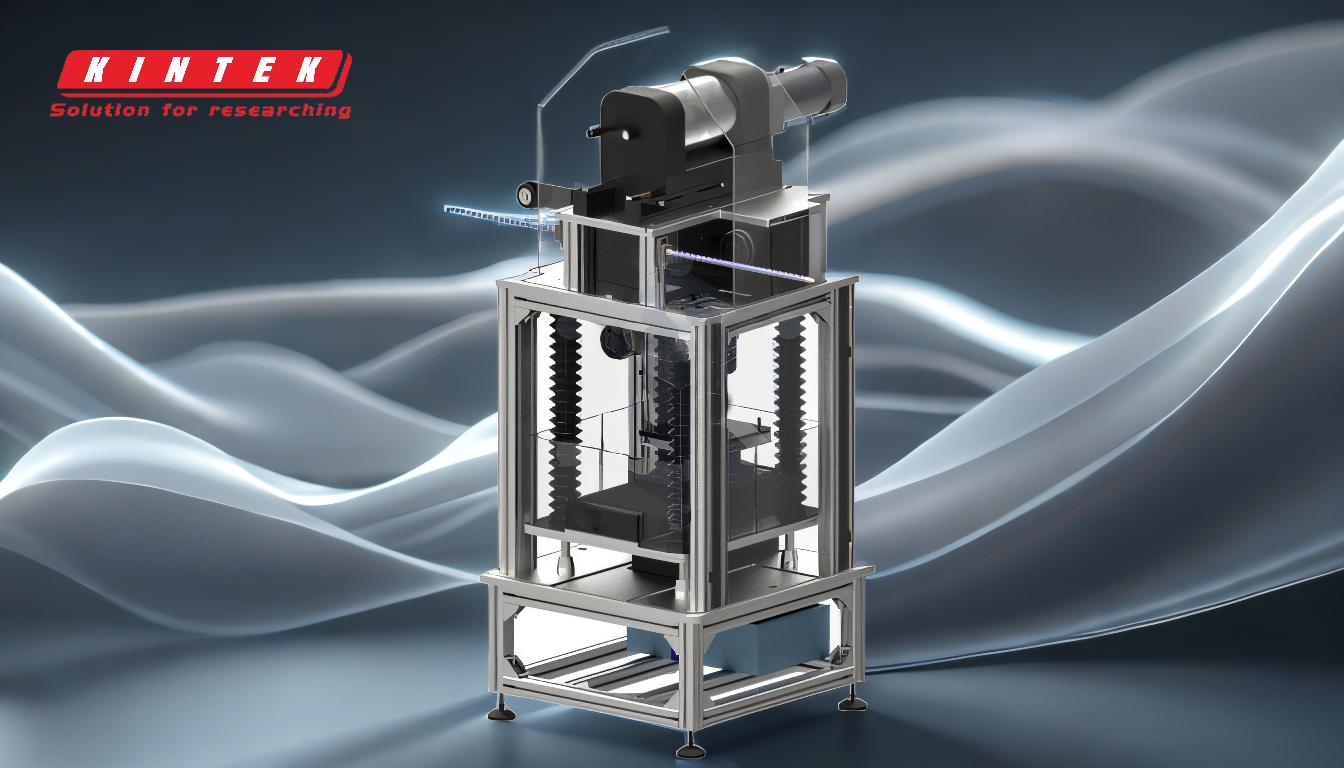
-
Typische Dicken von CVD-Beschichtungen:
- CVD-Beschichtungen sind im Allgemeinen dicker als PVD-Beschichtungen, mit einer typischen Dicke von 5-10 Mikrometer .In einigen Fällen kann sich die Dicke jedoch auf bis zu 10-20 Mikrometer insbesondere für Anwendungen, die eine höhere Haltbarkeit und Verschleißfestigkeit erfordern.
- Diese höhere Schichtdicke ist auf die Art des CVD-Verfahrens zurückzuführen, das die Abscheidung dichter und gleichmäßiger Schichten auf dem Substrat ermöglicht.
-
Vergleich mit PVD-Beschichtungen:
- PVD-Beschichtungen sind in der Regel dünner, sie reichen von 2-5 Mikrometer und werden im Vergleich zu CVD bei niedrigeren Temperaturen aufgebracht.
- Während PVD-Beschichtungen für Anwendungen geeignet sind, bei denen feine Oberflächen und geringere Schichtdicken erforderlich sind, werden CVD-Beschichtungen bevorzugt, weil sie dickere, haltbarere Schichten ergeben, insbesondere in Umgebungen mit hohen Temperaturen und hohem Verschleiß.
-
Auswirkungen von hohen Verarbeitungstemperaturen:
- CVD-Verfahren arbeiten bei sehr hohen Temperaturen, oft zwischen 800-1000 °C was die Anlasstemperatur einiger Materialien wie Schnellarbeitsstahl übersteigen kann.
- Diese hohen Temperaturen können beim Abkühlen zu Zugspannungen führen, die feine Risse in der Beschichtung verursachen.Dies macht CVD weniger geeignet für unterbrochene Schneidprozesse, wie z. B. Fräsen, bei denen die Schnittkraft nicht gleichmäßig und kontinuierlich ist.
-
Adhäsion und Gleichmäßigkeit der Beschichtung:
- CVD-Beschichtungen sind bekannt für ihre hervorragende Haftung auf dem Substrat, da sich die Beschichtung während der chemischen Reaktion mit der Oberfläche verbindet.
- Das Verfahren ist nicht auf die Sichtlinie beschränkt, so dass das Beschichtungsgas alle Bereiche eines Teils erreichen kann, auch tiefe Löcher und Innenwände.Damit ist CVD ideal für die Beschichtung komplexer Geometrien.
-
Anwendungen und Beschränkungen:
- CVD-Beschichtungen sind sehr abrieb- und verschleißfest und eignen sich daher für Anwendungen mit unregelmäßig geformte Werkzeuge wie Bohrer und Schaftfräser.
- Sie werden auch verwendet bei der Herstellung von Halbleiterbeschichtungen für elektrische Geräte.
- Die hohen Verarbeitungstemperaturen und die Möglichkeit der Rissbildung schränken jedoch die beschichtbaren Grundwerkstoffe ein, so dass Werkstoffe mit hoher Temperaturbeständigkeit, wie z. B. Hartmetall, erforderlich sind.
-
Oberflächenbeschaffenheit und Beanspruchung:
- CVD-Beschichtungen haben in der Regel eine etwas rauere Oberfläche im Vergleich zum Substrat, was bei Anwendungen, die ein feines Finish erfordern, von Bedeutung sein kann.
- Die Zugspannung die während der Abkühlung entstehen, können zu feinen Rissen führen, die sich bei äußerer Einwirkung ausbreiten können, so dass sich die Beschichtung ablöst.Dies ist ein kritischer Faktor, der bei Anwendungen mit hoher mechanischer Belastung zu berücksichtigen ist.
Zusammenfassend lässt sich sagen, dass CVD-Beschichtungen eine vielseitige und wirksame Lösung für Anwendungen darstellen, die dicke, dauerhafte und gleichmäßige Beschichtungen erfordern.Allerdings müssen die hohen Verarbeitungstemperaturen und das Potenzial für spannungsbedingte Risse sorgfältig gehandhabt werden, insbesondere bei Anwendungen mit unterbrochenem Schnitt oder hoher mechanischer Belastung.
Zusammenfassende Tabelle:
Aspekt | CVD-Beschichtung Details |
---|---|
Typische Schichtdicke | 5-10 Mikrometer (kann für hohe Haltbarkeit auf 10-20 Mikrometer erweitert werden) |
Vergleich mit PVD | PVD:2-5 Mikrometer; CVD ist dicker und haltbarer |
Verarbeitungstemperatur | 800-1000 °C (hohe Temperaturen können Zugspannungen und feine Risse verursachen) |
Haftung & Gleichmäßigkeit | Hervorragende Haftung; kann komplexe Geometrien beschichten, einschließlich tiefer Löcher und Innenwände |
Anwendungen | Unregelmäßig geformte Werkzeuge, Halbleiterbeschichtungen, Umgebungen mit hohem Verschleiß |
Beschränkungen | Hohe Temperaturen können Risse verursachen; weniger geeignet für unterbrochene Schneidprozesse |
Benötigen Sie dauerhafte Beschichtungen für Ihre Werkzeuge oder Geräte? Kontaktieren Sie noch heute unsere Experten um mehr über CVD-Beschichtungen zu erfahren!