Die Sputterbeschichtung ist zwar in verschiedenen Anwendungen wie der Vorbereitung von REM-Proben und der Abscheidung von Dünnschichten weit verbreitet, hat jedoch mehrere Nachteile, die sich auf ihre Effizienz, die Kosten und die Qualität des Endprodukts auswirken können.Zu diesen Nachteilen gehören Probleme im Zusammenhang mit Verunreinigungen, Materialbeschränkungen, Prozesskomplexität und Anlagenkosten.Das Verständnis dieser Nachteile ist entscheidend für eine fundierte Entscheidung darüber, ob die Sputterbeschichtung die richtige Technik für eine bestimmte Anwendung ist.
Die wichtigsten Punkte erklärt:
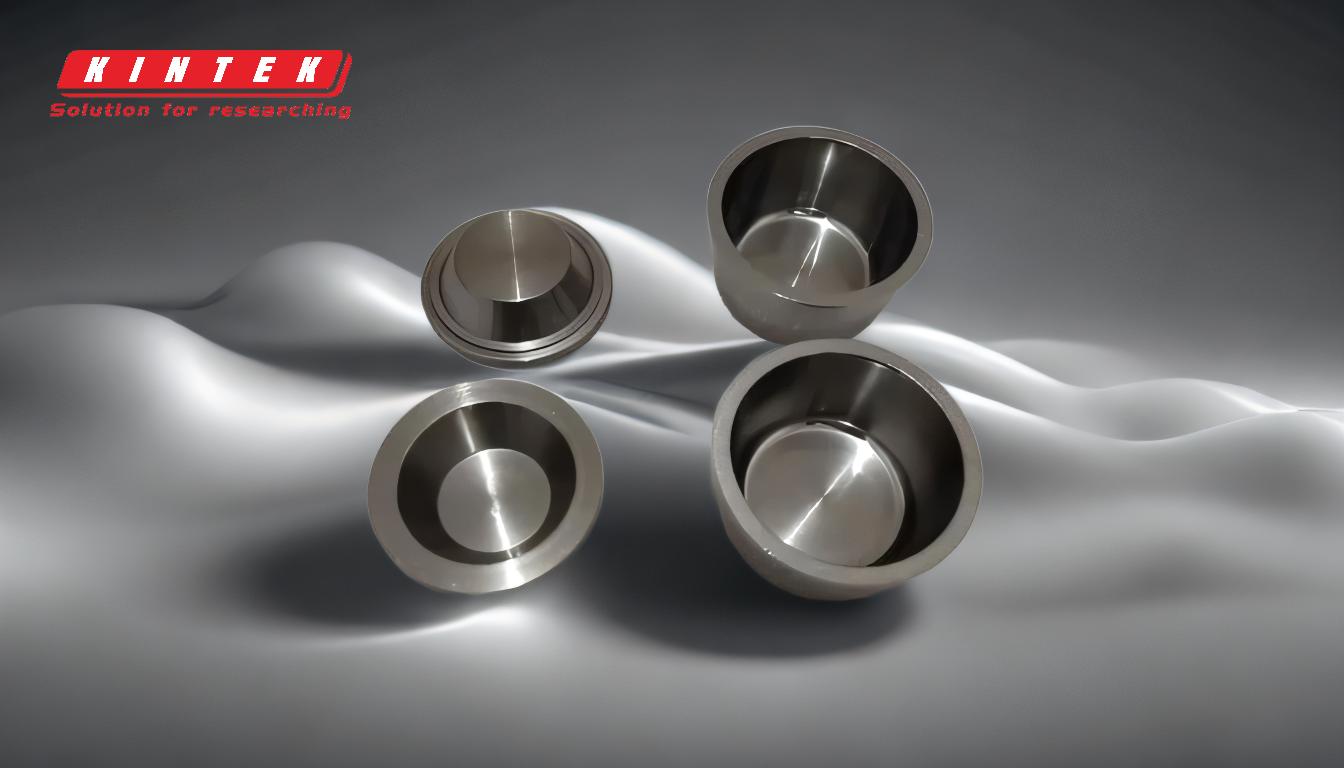
-
Filmverschmutzungs-Risiken:
- Verunreinigungsdiffusion:Während des Sputterprozesses können Verunreinigungen aus dem Zielmaterial oder der Umgebung in die Schicht diffundieren und zu Verunreinigungen führen.Dies ist besonders problematisch bei Anwendungen, die hochreine Schichten erfordern.
- Gasförmige Verunreinigungen:Das Plasma, das beim Sputtern verwendet wird, kann gasförmige Verunreinigungen aktivieren, die dann in den Film eingearbeitet werden, was das Risiko einer Verunreinigung weiter erhöht.
-
Beschränkungen des Materials:
- Beschränkungen der Schmelztemperatur:Die Auswahl der Beschichtungsmaterialien ist durch ihre Schmelztemperaturen begrenzt.Materialien mit sehr hohen Schmelzpunkten eignen sich möglicherweise nicht für die Sputterbeschichtung, was die Palette der verwendbaren Materialien einschränkt.
- Target-Vergiftung beim reaktiven Sputtern:Bei der reaktiven Sputterdeposition muss die Gaszusammensetzung sorgfältig kontrolliert werden, um zu verhindern, dass das Targetmaterial mit dem Gas reagiert, was zu einer Vergiftung des Targets und zu verringerten Abscheideraten führen kann.
-
Prozesskomplexität und -kontrolle:
- Parameter-Optimierung:Die Sputterbeschichtung erfordert eine sorgfältige Optimierung von Parametern wie Druck, Leistung und Gaszusammensetzung.Dies kann zeitaufwändig sein und erfordert unter Umständen erhebliche Fachkenntnisse.
- Layer-by-Layer-Wachstumskontrolle:Im Vergleich zu anderen Abscheidungsmethoden wie der gepulsten Laserabscheidung ist es schwierig, das schichtweise Wachstum präzise zu steuern.Dies kann sich auf die Qualität und Gleichmäßigkeit der Schicht auswirken.
-
Ausrüstung und Betriebskosten:
- Teure Ziele:Sputtertargets sind oft kostspielig, und der Materialeinsatz kann ineffizient sein, was zu höheren Betriebskosten führt.
- Anforderungen an die Kühlung:Ein erheblicher Teil der beim Sputtern eingesetzten Energie wird in Wärme umgewandelt, so dass Kühlsysteme erforderlich sind.Dies erhöht nicht nur die Energiekosten, sondern verringert auch die Produktionsrate.
-
Folienqualität und Gleichmäßigkeit:
- Ungleichmäßiger Abscheidungsfluss:Der Abscheidungsfluss beim Sputtern ist oft ungleichmäßig, was den Einsatz beweglicher Vorrichtungen erfordert, um eine gleichmäßige Schichtdicke zu erreichen.Dies erhöht die Komplexität des Prozesses.
- Veränderte Oberflächentopographie:In einigen Fällen kann die Sputterbeschichtung die Oberflächentopographie der Probe verändern, was bei Anwendungen, bei denen die Unversehrtheit der Oberfläche entscheidend ist, unerwünscht sein kann.
- Verlust des Atomzahl-Kontrasts:Das Beschichtungsmaterial kann die ursprüngliche Oberfläche ersetzen, was zu einem Verlust des Atomzahl-Kontrasts führt, was bei der REM-Bildgebung ein erheblicher Nachteil sein kann.
-
Integration mit anderen Prozessen:
- Lift-Off-Prozess Herausforderungen:Aufgrund des diffusen Transports der gesputterten Atome lässt sich die Sputterdeposition nur schwer mit Lift-off-Verfahren für die Schichtstrukturierung kombinieren.Dies kann zu Verunreinigungsproblemen führen und macht eine vollständige Abschattung unmöglich.
- Inertgas-Verunreinigungen:Inerte Sputtergase können zu Verunreinigungen in der wachsenden Schicht werden und deren Eigenschaften und Leistung beeinträchtigen.
Zusammenfassend lässt sich sagen, dass die Sputter-Beschichtung zwar mehrere Vorteile bietet, wie die Möglichkeit, eine breite Palette von Materialien abzuscheiden und eine gute Haftung zu erzielen, aber auch mit erheblichen Nachteilen verbunden ist.Dazu gehören Verunreinigungsrisiken, Materialbeschränkungen, Prozesskomplexität, hohe Anlagen- und Betriebskosten, Schwierigkeiten bei der Erzielung einer einheitlichen Schichtqualität und Schwierigkeiten bei der Integration mit anderen Verfahren.Eine sorgfältige Abwägung dieser Faktoren ist unerlässlich, wenn man entscheiden will, ob die Sputterbeschichtung die geeignete Technik für eine bestimmte Anwendung ist.
Zusammenfassende Tabelle:
Nachteile der Sputter-Beschichtung | Zentrale Herausforderungen |
---|---|
Risiken der Filmkontamination | Diffusion von Verunreinigungen, gasförmige Verunreinigungen |
Beschränkungen des Materials | Beschränkungen der Schmelztemperatur, Target-Vergiftung |
Prozess-Komplexität | Parameteroptimierung, schichtweise Wachstumskontrolle |
Hohe Ausrüstungskosten | Teure Targets, Kühlungsanforderungen |
Probleme mit der Filmqualität | Ungleichmäßige Ablagerung, veränderte Oberflächentopographie |
Herausforderungen bei der Integration | Schwierigkeiten beim Lift-off-Prozess, Verunreinigungen durch Inertgas |
Benötigen Sie Hilfe bei der Entscheidung, ob die Sputterbeschichtung für Ihre Anwendung geeignet ist? Kontaktieren Sie noch heute unsere Experten für eine maßgeschneiderte Beratung!