Die Sputterdeposition ist zwar in der Dünnfilmbeschichtung weit verbreitet, hat aber einige bemerkenswerte Nachteile, die sich auf die Effizienz, die Kosten und die Eignung für bestimmte Verfahren auswirken können.Dazu gehören Herausforderungen bei der Schichtstrukturierung, Verunreinigungsrisiken, niedrige Sputterraten, ungleichmäßige Abscheidung, hohe Kosten und Energieineffizienz.Darüber hinaus können die Kontrolle der Stöchiometrie und die Steuerung reaktiver Sputterprozesse komplex sein.Das Verständnis dieser Nachteile ist entscheidend für die Auswahl der geeigneten Abscheidungsmethode für bestimmte Anwendungen.
Die wichtigsten Punkte werden erklärt:
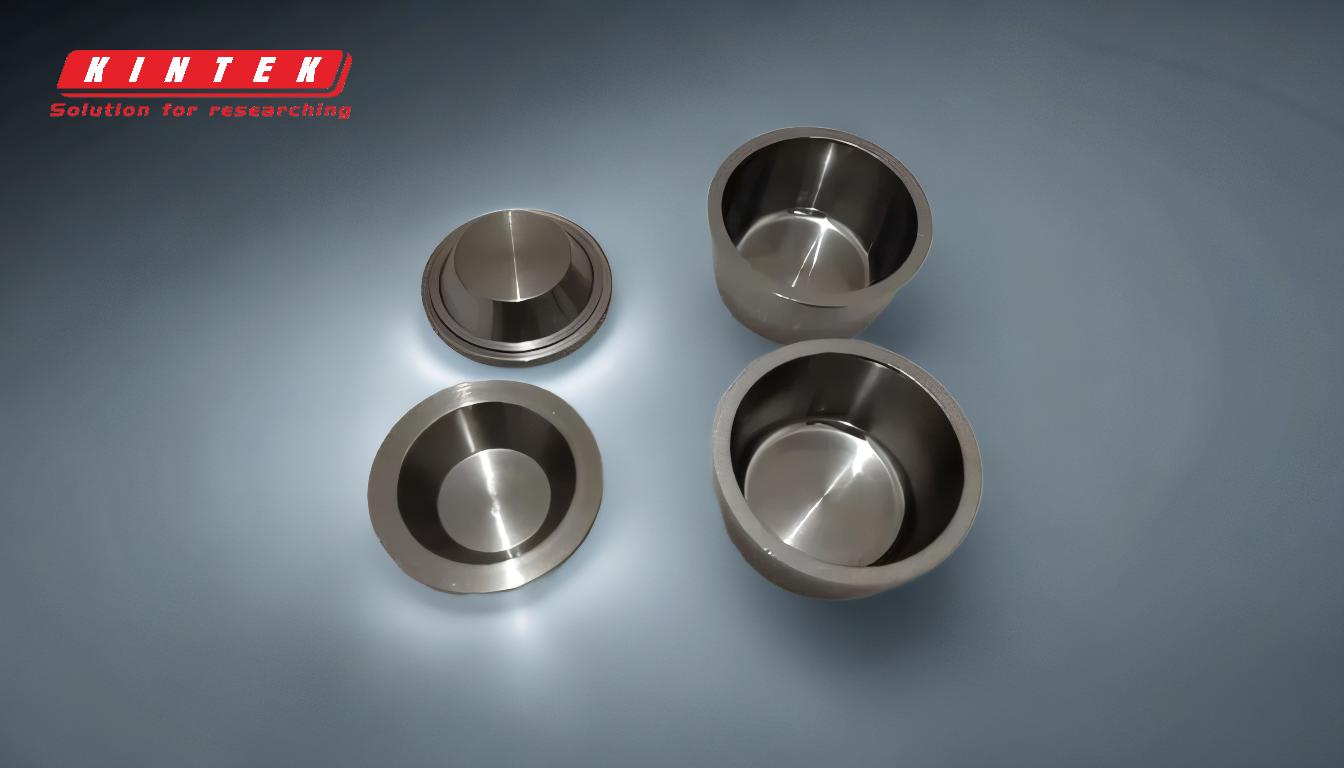
-
Schwierige Kombination mit Lift-Off-Prozessen:
- Aufgrund des diffusen Transports der gesputterten Atome ist die Integration mit Lift-Off-Verfahren schwierig.Dies macht eine vollständige Abschattung unmöglich und führt zu potenziellen Kontaminationsproblemen.Die Seitenwandabdeckung und die Erhitzungseffekte erschweren den Einsatz bei Hebevorgängen zusätzlich und machen ihn für solche Prozesse weniger wünschenswert.
-
Kontaminationsrisiken:
- Durch den Sputterprozess können Verunreinigungen aus den Ausgangsmaterialien in die Schicht eingebracht werden, was zu einer Verunreinigung der Schicht führt.Auch inerte Sputtergase können zu Verunreinigungen in der wachsenden Schicht werden.Außerdem können gasförmige Verunreinigungen im Plasma aktiviert werden, was das Risiko einer Verunreinigung erhöht.
-
Niedrige Sputtering-Raten:
- Bei der Sputterdeposition sind die Sputterraten in der Regel niedriger als bei der thermischen Verdampfung.Dies kann zu langsameren Abscheidungszeiten führen, was für Anwendungen mit hohem Durchsatz nicht unbedingt ideal ist.
-
Ungleichmäßiger Abscheidungsfluss:
- Die Verteilung des Abscheidungsflusses bei der Sputterabscheidung ist oft ungleichmäßig.Um eine gleichmäßige Schichtdicke zu erreichen, müssen bewegliche Vorrichtungen verwendet werden, was den Prozess komplexer und teurer macht.
-
Teure Sputtering-Targets:
- Sputtertargets sind oft teuer, und der Materialeinsatz kann ineffizient sein.Dies trägt zu höheren Gesamtkosten bei, insbesondere wenn seltene oder spezielle Materialien verwendet werden.
-
Energieineffizienz:
- Ein erheblicher Teil der auf das Ziel einfallenden Energie wird in Wärme umgewandelt, die abgeführt werden muss.Diese Energieineffizienz kann zu erhöhten Betriebskosten und dem Bedarf an effektiven Kühlsystemen führen.
-
Herausforderungen bei der Stöchiometriesteuerung:
- Die Kontrolle der Stöchiometrie der abgeschiedenen Schicht kann schwierig sein, insbesondere bei der reaktiven Sputterdeposition.Eine genaue Kontrolle der Gaszusammensetzung ist erforderlich, um eine Vergiftung des Targets zu verhindern und die gewünschten Schichteigenschaften zu erzielen.
-
Komplexität des reaktiven Sputterns:
- Die reaktive Sputterabscheidung ist mit zusätzlichen Schwierigkeiten verbunden, z. B. mit der Notwendigkeit, die Gaszusammensetzung sorgfältig zu kontrollieren, um eine Vergiftung des Targets zu vermeiden.Dies kann den Prozess verkomplizieren und erfordert anspruchsvollere Ausrüstung und Überwachung.
-
Wartung und Beschränkungen der Prozessparameter:
- Das Sputtern wird durch die grundlegenden Gegebenheiten des Vakuumsystems behindert, einschließlich der Beschränkungen bei den Prozessparametern und der Notwendigkeit einer vom Benutzer durchgeführten Wartung.Dies kann die betriebliche Belastung erhöhen und häufigere Eingriffe zur Aufrechterhaltung der Prozessstabilität erforderlich machen.
Die Kenntnis dieser Nachteile ist eine wesentliche Voraussetzung für fundierte Entscheidungen über den Einsatz der Sputterdeposition in verschiedenen Anwendungen.Es bietet zwar eine Reihe von Vorteilen, wie z. B. die Möglichkeit, eine breite Palette von Materialien abzuscheiden und konforme Beschichtungen zu erzielen, doch müssen die Nachteile sorgfältig abgewogen werden, um sicherzustellen, dass die gewählte Methode den spezifischen Anforderungen der Anwendung entspricht.
Zusammenfassende Tabelle:
Benachteiligung | Beschreibung |
---|---|
Herausforderungen des Lift-Off-Prozesses | Schwierige Integration aufgrund von diffusem Atomtransport und Kontaminationsrisiken. |
Verunreinigungs-Risiken | Verunreinigungen durch Ausgangsmaterialien und plasmaaktivierte gasförmige Verunreinigungen. |
Niedrige Sputtering-Raten | Langsamere Abscheidung im Vergleich zur thermischen Verdampfung, was sich auf den Durchsatz auswirkt. |
Ungleichmäßige Abscheidung | Für eine gleichmäßige Schichtdicke sind bewegliche Vorrichtungen erforderlich, was die Komplexität und die Kosten erhöht. |
Teure Targets | Hohe Kosten und ineffiziente Nutzung von Sputtertargets, insbesondere von seltenen Materialien. |
Energieineffizienz | Erhebliche Energieverluste in Form von Wärme, die wirksame Kühlsysteme erfordern. |
Probleme bei der Kontrolle der Stöchiometrie | Schwierige Kontrolle der Schichtzusammensetzung, insbesondere beim reaktiven Sputtern. |
Komplexität des reaktiven Sputterns | Erfordert eine genaue Kontrolle der Gaszusammensetzung, um eine Vergiftung des Targets zu vermeiden. |
Herausforderungen bei der Wartung | Häufige Wartung durch den Benutzer und Einschränkungen der Prozessparameter. |
Benötigen Sie Hilfe bei der Auswahl der richtigen Abscheidungsmethode für Ihre Anwendung? Kontaktieren Sie unsere Experten noch heute!