Spritzgießen ist ein Fertigungsverfahren, bei dem Teile durch Einspritzen von geschmolzenem Material in eine Form hergestellt werden. Das Verfahren ist hocheffizient und kann in vier Hauptphasen unterteilt werden: Schließen, Einspritzen, Kühlen und Auswerfen. Jede Phase spielt eine entscheidende Rolle, wenn es darum geht, dass das Endprodukt den gewünschten Spezifikationen entspricht. Der gesamte Zyklus dauert in der Regel zwischen 2 Sekunden und 2 Minuten, abhängig von der Komplexität des Teils und dem verwendeten Material. Im Folgenden wird jede Phase im Detail erläutert, um ein umfassendes Verständnis des Spritzgießprozesses zu vermitteln.
Die wichtigsten Punkte erklärt:
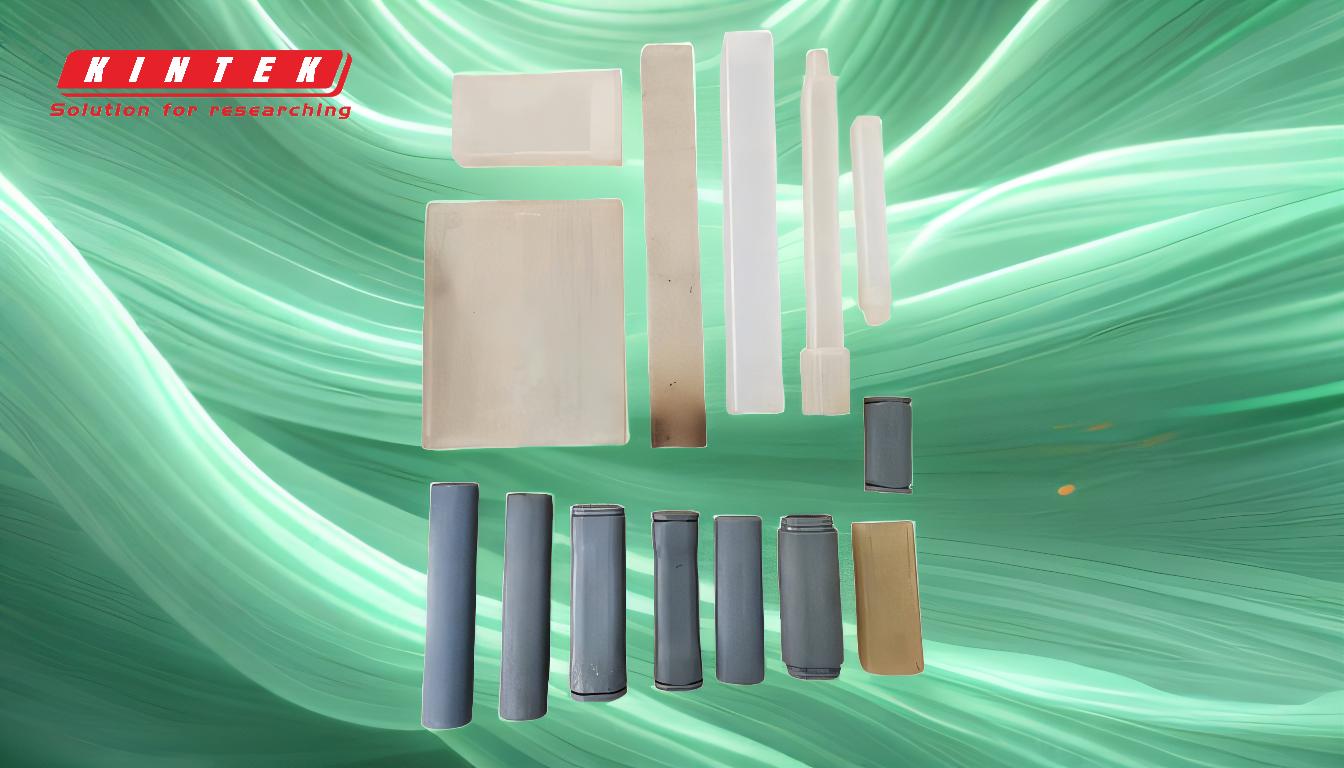
-
Schließphase
- Zweck: In der Schließphase werden die beiden Werkzeughälften miteinander verbunden, um das Einspritzen des geschmolzenen Materials vorzubereiten.
-
Verfahren:
- Die Form besteht aus zwei Hälften: der feststehenden Hälfte (an der Spritzgießmaschine befestigt) und der beweglichen Hälfte (die sich öffnet und schließt).
- Eine Schließeinheit übt Druck aus, um die Formhälften während des Einspritzvorgangs fest zusammenzuhalten.
- Die Schließkraft muss ausreichend sein, um dem Druck des eingespritzten Materials standzuhalten und ein Auslaufen oder Verformen der Form zu verhindern.
- Bedeutung: Eine ordnungsgemäße Schließung gewährleistet, dass die Form geschlossen und stabil bleibt, was für die Herstellung qualitativ hochwertiger Teile mit präzisen Abmessungen entscheidend ist.
-
Einspritzphase
- Zweck: In dieser Phase wird das geschmolzene Material in den Formhohlraum eingespritzt, um das gewünschte Teil zu formen.
-
Verfahren:
- Das Material (in der Regel Kunststoffgranulat) wird in einen beheizten Zylinder eingefüllt, wo es geschmolzen und homogenisiert wird.
- Eine sich hin- und herbewegende Schnecke oder ein Kolben drückt das geschmolzene Material unter hohem Druck in den Formhohlraum.
- Das Material füllt den Hohlraum aus und nimmt die Form der Gussform an.
-
Zu berücksichtigende Faktoren:
- Einspritzdruck, -geschwindigkeit und -temperatur müssen sorgfältig kontrolliert werden, um sicherzustellen, dass das Material die Form vollständig und gleichmäßig ausfüllt.
- Eine Über- oder Unterfüllung der Form kann zu Fehlern wie Verzug, Einfallstellen oder unvollständigen Teilen führen.
- Wichtigkeit: Die Einspritzphase bestimmt die ursprüngliche Form und Integrität des Teils und ist daher ein kritischer Schritt im Prozess.
-
Abkühlphase
- Zweck: Nach dem Füllen der Form muss das Material abkühlen und sich verfestigen, damit es seine Form behält.
-
Verfahren:
- Die Abkühlung beginnt, sobald das Material in die Form gespritzt wird.
- Die Form ist mit Kühlkanälen ausgestattet, durch die ein Kühlmittel (in der Regel Wasser) zirkuliert, um die Wärme abzuleiten.
- Die Abkühlzeit hängt von den Materialeigenschaften, der Bauteildicke und der Formkonstruktion ab.
-
Zu berücksichtigende Faktoren:
- Eine unzureichende Kühlung kann zu Verformungen oder inneren Spannungen im Teil führen.
- Eine zu lange Kühlung kann die Zykluszeit erhöhen und die Produktionseffizienz verringern.
- Wichtigkeit: Eine ordnungsgemäße Kühlung stellt sicher, dass das Teil korrekt erstarrt und die Maßhaltigkeit und strukturelle Integrität erhalten bleibt.
-
Auswerferstufe
- Zweck: Sobald das Teil abgekühlt und verfestigt ist, wird es aus der Form ausgestoßen.
-
Verfahren:
- Die Form öffnet sich, und Auswerferstifte oder -platten drücken das Teil aus dem Formhohlraum.
- Anschließend wird das Teil entweder manuell oder automatisch aus der Maschine entnommen.
-
Zu berücksichtigende Faktoren:
- Das Auswerfen muss sorgfältig durchgeführt werden, um eine Beschädigung des Teils oder der Form zu vermeiden.
- Die richtige Konstruktion der Form, einschließlich der Platzierung der Auswerferstifte, ist entscheidend für einen reibungslosen Ausstoß.
- Wichtigkeit: Mit dem Auswerfen wird der Zyklus abgeschlossen, so dass die Form für den nächsten Spritzguss vorbereitet werden kann.
Zusätzliche Überlegungen für Einkäufer von Ausrüstung und Verbrauchsmaterial:
- Auswahl des Materials: Die Art des verwendeten Materials (z. B. Thermoplaste, duroplastische Polymere) beeinflusst den Formgebungsprozess und die Eigenschaften des Endprodukts.
- Konstruktion der Form: Eine gut konzipierte Form mit geeigneten Kühlkanälen und Ausstoßmechanismen ist für eine effiziente Produktion unerlässlich.
- Maschinenspezifikationen: Die Spritzgießmaschine muss über eine angemessene Schließkraft, einen angemessenen Einspritzdruck und eine ausreichende Kühlkapazität verfügen, um die spezifischen Anforderungen des Teils zu erfüllen.
- Optimierung der Zykluszeit: Die Verkürzung der Zykluszeit bei gleichbleibender Qualität ist der Schlüssel zur Verbesserung der Produktionseffizienz und zur Senkung der Kosten.
Wer diese Phasen und ihre Bedeutung kennt, kann fundierte Entscheidungen zur Optimierung des Spritzgießprozesses für seine spezifischen Anforderungen treffen.
Zusammenfassende Tabelle:
Stufe | Zweck | Schlüsselprozess | Wichtigkeit |
---|---|---|---|
Einspannen | Sichern der Formhälften für die Einspritzung | Aufbringen der Schließkraft, um die Form fest zu halten; verhindert Leckagen oder Verformungen | Gewährleistet die Stabilität der Form und präzise Teileabmessungen |
Einspritzen | Einspritzen von geschmolzenem Material in den Formhohlraum | Material schmelzen, unter hohem Druck in die Form drücken; Druck, Geschwindigkeit und Temperatur kontrollieren | Bestimmt die Form und Integrität des Teils; entscheidend für fehlerfreie Ergebnisse |
Kühlen | Verfestigung des Materials, um die Form zu erhalten | Zirkulieren des Kühlmittels durch die Formkanäle; Steuerung der Kühlzeit je nach Material und Teiledicke | Gewährleistet Maßgenauigkeit und strukturelle Integrität; verhindert Verformung |
Auswerfen | Entfernen des erstarrten Teils aus der Form | Öffnen der Form und Herausdrücken des Teils mit Auswerferstiften/-platten; Sicherstellung eines reibungslosen Ausstoßes | Schließt den Zyklus ab; bereitet die Form für die nächste Einspritzung vor |
Sind Sie bereit, Ihren Spritzgießprozess zu optimieren? Kontaktieren Sie noch heute unsere Experten für maßgeschneiderte Lösungen!