Eine chemische Reaktion im Wirbelbett ist ein Prozess, bei dem ein Fluid (Flüssigkeit oder Gas) mit hoher Geschwindigkeit durch ein festes körniges Material geleitet wird, wodurch die festen Partikel in der Schwebe bleiben und sich wie eine Flüssigkeit verhalten.Auf diese Weise entsteht ein Wirbelbett, das den Wärme- und Stofftransport verbessert und somit hocheffizient für chemische Reaktionen ist.Der Prozess beginnt bei der minimalen Wirbelgeschwindigkeit, bei der die Kraft der Flüssigkeit das Gewicht des Feststoffs ausgleicht.Jenseits dieser Geschwindigkeit dehnt sich das feste Material aus und verwirbelt, wodurch eine dynamische Umgebung für chemische Reaktionen entsteht.Wirbelschichtreaktoren werden aufgrund ihrer Effizienz, ihrer schnellen Reaktionsgeschwindigkeit und ihrer Fähigkeit, große Durchsatzmengen zu bewältigen, in vielen Industriezweigen eingesetzt, z. B. in der Kraftstoffproduktion, der Polymerherstellung und der Abfallbehandlung.
Die wichtigsten Punkte werden erklärt:
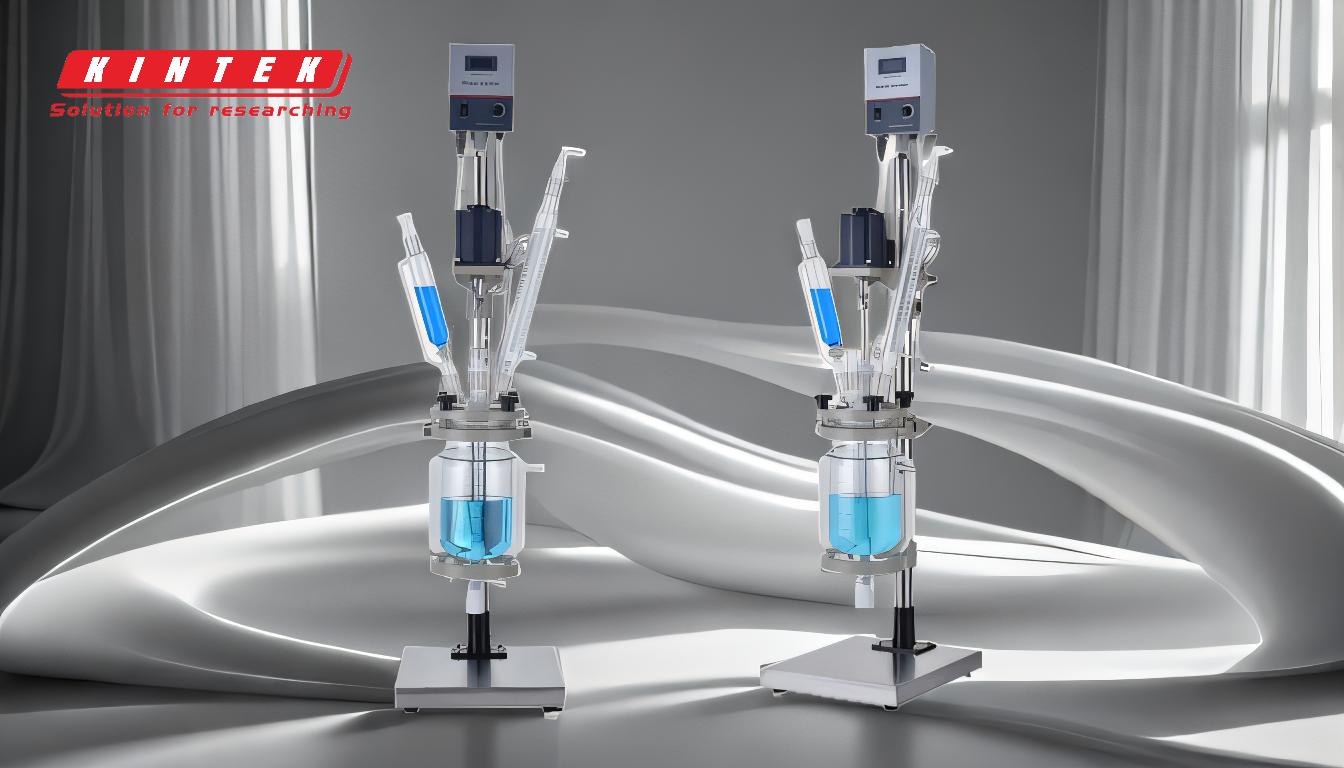
-
Definition der chemischen Wirbelschichtreaktion:
- Bei einer chemischen Reaktion im Wirbelschichtverfahren wird ein Fluid (Gas oder Flüssigkeit) mit hoher Geschwindigkeit durch ein festes körniges Material geleitet, wodurch die festen Partikel in Schwebe gebracht werden und sich wie eine Flüssigkeit verhalten.
- Dieser Prozess beginnt mit der minimalen Fluidisierungsgeschwindigkeit , bei der die Fluidkraft das Gewicht des Feststoffs ausgleicht und ein Wirbelbett entsteht.
-
Mechanismus der Fluidisierung:
- Die Fluidisierung tritt ein, wenn die Flüssigkeitsgeschwindigkeit die minimale Fluidisierungsgeschwindigkeit überschreitet, wodurch sich die Feststoffpartikel ausdehnen und verwirbeln.
- Diese dynamische Umgebung verbessert den Wärme- und Stoffübertragung was ihn für chemische Reaktionen sehr effizient macht.
-
Komponenten eines Wirbelschichtreaktors:
- Material des Bettes:In der Regel werden am Boden des Reaktors inerte Materialien wie Sand verwendet, um die dynamische Stabilität des Fluids zu gewährleisten und die Wärmeübertragung zu unterstützen.
- Flüssigkeit:Ein Gas, häufig reiner Stickstoff, wird am Boden eingeleitet, um eine inerte Atmosphäre aufrechtzuerhalten, unerwünschte chemische Reaktionen zu verhindern und die Partikel zu fluidisieren.
- Wärmeübertragung:Das Bettmaterial überträgt die Wärme effizient auf das Substrat, das chemische Reaktionen durchläuft, und gewährleistet eine gleichmäßige Temperaturverteilung.
-
Typen von Wirbelschichtreaktoren:
- Sprudelnde Wirbelschichtreaktoren:Sie werden mit niedrigeren Gasgeschwindigkeiten betrieben und eignen sich für Prozesse, die eine moderate Wärmeübertragung und Reaktionsgeschwindigkeit erfordern.
- Zirkulierende Wirbelschichtreaktoren:Sie arbeiten mit höheren Gasgeschwindigkeiten, was zu einem höheren Anteil an zermahlener Holzkohle und einem höheren Gehalt an Holzkohle in Produkten wie Bioöl führt.Sie eignen sich für sehr große Durchsätze und verwenden häufig rezirkulierten erhitzten Sand aus einer sekundären Holzkohleverbrennungsanlage.
-
Anwendungen von Wirbelschichtreaktoren:
- Kraftstoffproduktion:Wird bei der Herstellung von Benzin und anderen Kraftstoffen sowie bei der Kohlevergasung verwendet.
- Polymerherstellung:Wird bei der Herstellung von industriell wichtigen Polymeren wie Gummi, Vinylchlorid, Polyethylen, Styrolen und Polypropylen verwendet.
- Behandlung von Abfällen:Einsatz in Wasser- und Abfallbehandlungsverfahren, die im Vergleich zu herkömmlichen Reaktortechnologien sauberere und effizientere Lösungen bieten.
- Bio-Öl-Produktion:Maximierung der Produktion von flüssigen Produkten wie Bioöl durch die Verwendung von inerten Elementen wie Sand, die für die dynamische Stabilität der Flüssigkeit sorgen und die Erwärmung der Biomasse unterstützen.
-
Vorteile von Wirbelschichtreaktoren:
- Schnelle Reaktion und Wärmeübertragung:Die dynamische Umgebung des Wirbelbetts sorgt für schnelle chemische Reaktionen und eine effiziente Wärmeübertragung.
- Breite Kontaktfläche:Das Wirbelbett bietet eine große Kontaktfläche zwischen der Flüssigkeit und den Feststoffpartikeln, wodurch die Reaktionseffizienz erhöht wird.
- Hohe Vergleichsgeschwindigkeit:Die hohe Geschwindigkeit der Flüssigkeit sorgt für eine gleichmäßige Durchmischung und verhindert die Bildung von Hot Spots, was zu einer konstanten Produktqualität führt.
- Skalierbarkeit:Wirbelschichtreaktoren sind in hohem Maße skalierbar, so dass sie sich sowohl für Experimente im Labormaßstab als auch für großtechnische Anwendungen eignen.
-
Herausforderungen und Überlegungen:
- Erosion und Attrition:Die hohe Geschwindigkeit der Flüssigkeit kann zu Erosion und Abrieb der Feststoffpartikel führen, was eine häufige Wartung und den Austausch des Bettmaterials erforderlich macht.
- Gasverteilung:Die Gewährleistung einer gleichmäßigen Gasverteilung ist entscheidend für die Aufrechterhaltung des fluidisierten Zustands und das Erreichen gleichmäßiger Reaktionsraten.
- Temperaturkontrolle:Eine genaue Temperaturkontrolle ist notwendig, um unerwünschte Nebenreaktionen zu vermeiden und die gewünschte Produktqualität zu gewährleisten.
Zusammenfassend lässt sich sagen, dass chemische Reaktionen in Wirbelschichten eine vielseitige und effiziente Methode für die Durchführung chemischer Reaktionen in verschiedenen industriellen Anwendungen sind.Die einzigartigen Eigenschaften von Wirbelschichten, wie z. B. die schnelle Wärme- und Stoffübertragung, die große Kontaktfläche und die Skalierbarkeit, machen sie zu einer attraktiven Wahl für Industrien, die von der Kraftstoffproduktion bis zur Polymerherstellung und Abfallbehandlung reichen.Um die Vorteile von Wirbelschichtreaktoren zu maximieren, ist es jedoch unerlässlich, Herausforderungen wie Erosion, Gasverteilung und Temperaturkontrolle sorgfältig zu berücksichtigen.
Zusammenfassende Tabelle:
Aspekt | Einzelheiten |
---|---|
Definition | Flüssigkeit strömt durch festes, körniges Material, wodurch ein Wirbelbett entsteht. |
Mechanismus | Überschreitet die Mindestfluidisierungsgeschwindigkeit und verbessert den Wärme- und Stoffaustausch. |
Bestandteile | Bettmaterial (z. B. Sand), Flüssigkeit (z. B. Stickstoff) und Wärmeübertragungssystem. |
Typen | Blasenbildende und zirkulierende Wirbelschichtreaktoren. |
Anwendungen | Kraftstoffherstellung, Polymerherstellung, Abfallbehandlung und Bioöl. |
Vorteile | Schnelle Reaktion, großer Kontaktbereich, hohe Geschwindigkeit und Skalierbarkeit. |
Herausforderungen | Erosion, Gasverteilung und Temperaturregelung. |
Sind Sie daran interessiert, Ihre chemischen Prozesse mit Wirbelschichtreaktoren zu optimieren? Kontaktieren Sie noch heute unsere Experten um mehr zu erfahren!