Die Effizienz der Pyrolyse, eines thermischen Zersetzungsprozesses, bei dem organische Materialien in nützliche Produkte wie Gase, Flüssigkeiten und Feststoffe umgewandelt werden, hängt von mehreren Faktoren ab. Dazu gehören die Zusammensetzung des Ausgangsmaterials, die Konstruktion des Reaktors, die Betriebsparameter (Temperatur, Druck, Verweilzeit) und der Feuchtigkeitsgehalt der Biomasse. Die richtige Steuerung dieser Faktoren ist entscheidend für die Maximierung der Umwandlung organischer Materialien in energiereiche Produkte und die Verbesserung der Gesamteffizienz des Prozesses. Darüber hinaus kann die Optimierung der Partikelgröße, der Heizrate und der Reaktorbedingungen die Effizienz der Pyrolyse weiter steigern.
Die wichtigsten Punkte werden erklärt:
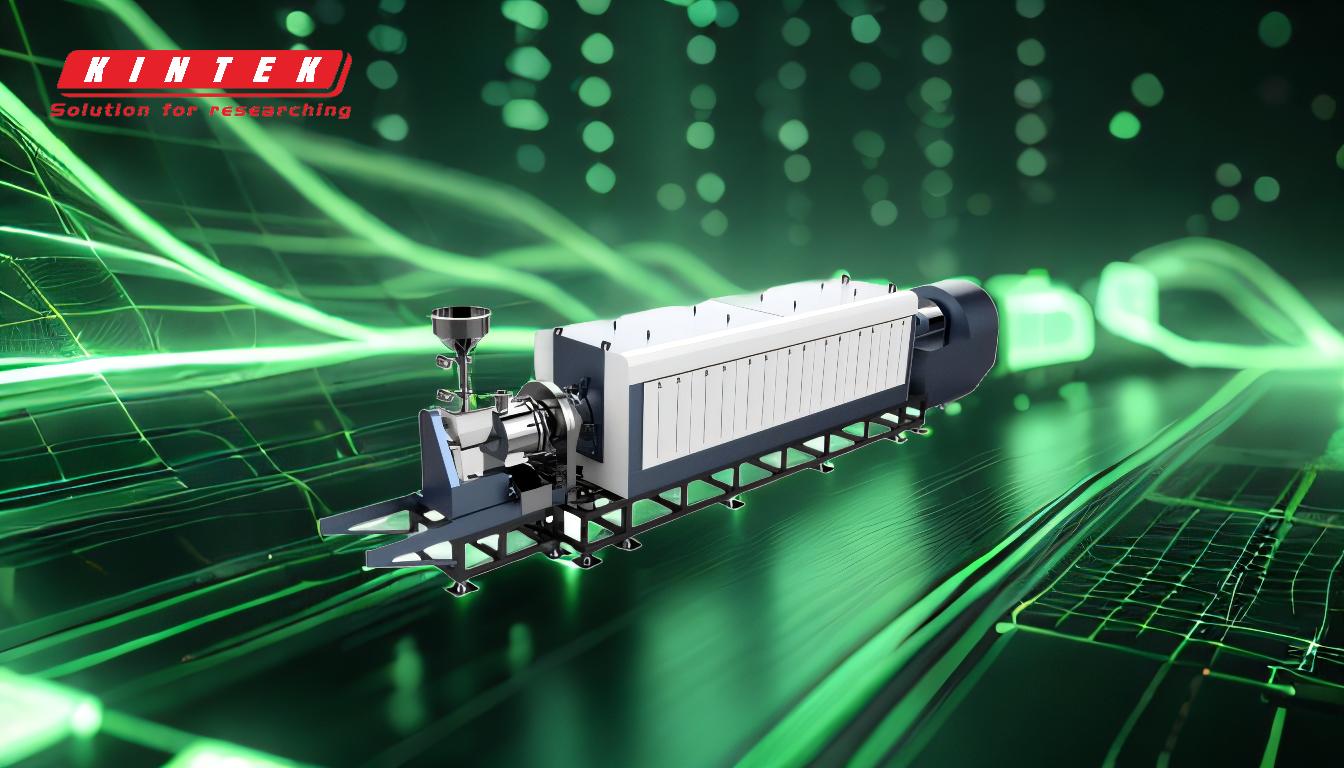
-
Faktoren, die die Effizienz der Pyrolyse beeinflussen
- Zusammensetzung des Rohstoffs: Die Art und die Zusammensetzung des Abfalls oder der Biomasse beeinflussen die Effizienz der Pyrolyse erheblich. Organische Fraktionen werden unterschiedlich abgebaut, und ihre Umwandlung in Gase, Flüssigkeiten oder Feststoffe hängt von ihrer chemischen Struktur ab.
- Feuchtigkeitsgehalt: Ein hoher Feuchtigkeitsgehalt in der Biomasse verringert den Wirkungsgrad, da Energie für das Verdampfen von Wasser verschwendet wird, statt für den Abbau von organischem Material. Für eine höhere Effizienz wird trockenes Ausgangsmaterial bevorzugt.
- Partikelgröße: Kleinere Partikelgrößen vergrößern die Oberfläche für die Wärmeübertragung, was zu schnelleren und gleichmäßigeren Pyrolysereaktionen führt.
-
Betriebliche Parameter
- Temperatur: Die Effizienz der Pyrolyse hängt stark von der Temperatur ab. Die optimalen Temperaturen variieren je nach Ausgangsmaterial, liegen aber im Allgemeinen zwischen 400°C und 800°C. Höhere Temperaturen können die Gasausbeute verbessern, aber die Ausbeute an flüssigen oder festen Produkten verringern.
- Aufenthaltsdauer: Die Zeit, die das Material im Reaktor verbringt, beeinflusst den Grad der Zersetzung. Längere Verweilzeiten ermöglichen eine vollständigere Umwandlung, können aber den Durchsatz verringern.
- Druck: Der Betrieb bei angemessenem Druck gewährleistet eine effiziente Wärmeübertragung und Produktbildung. Erhöhte Drücke können bestimmte Reaktionen fördern, aber ein zu hoher Druck kann zu betrieblichen Problemen führen.
-
Reaktordesign und -optimierung
- Reaktortyp: Verschiedene Reaktorkonzepte (z. B. Wirbelschicht, Festbett, Drehrohrofen) haben unterschiedliche Wirkungsgrade. Die Wahl des Reaktors hängt vom Ausgangsmaterial und den gewünschten Endprodukten ab.
- Heizrate: Eine kontrollierte und optimierte Erhitzungsgeschwindigkeit gewährleistet eine effiziente Zersetzung des Ausgangsmaterials. Eine schnelle Erhitzung kann zu einer höheren Ausbeute an flüssigen Produkten führen, während eine langsamere Erhitzung die Erzeugung von Gas oder Holzkohle begünstigt.
- Energierückgewinnung: Effiziente Energierückgewinnungssysteme können die Gesamteffizienz des Prozesses verbessern, indem sie die Wärme aus dem Pyrolyseprozess für andere Prozesse nutzen.
-
Verbesserung der Effizienz der Pyrolyse
- Optimierung der Rohstoffaufbereitung: Vorbehandlungsverfahren wie Trocknung, Zerkleinerung und Sortierung können die Qualität des Ausgangsmaterials verbessern und die Effizienz der Pyrolyse erhöhen.
- Fortgeschrittene Kontrollsysteme: Der Einsatz automatisierter Kontrollsysteme für Temperatur, Druck und Verweilzeit gewährleistet gleichbleibende und optimale Bedingungen.
- Katalytische Pyrolyse: Durch den Einsatz von Katalysatoren können die erforderlichen Reaktionstemperaturen gesenkt und die Ausbeute an bestimmten Produkten, wie Bioöl oder Synthesegas, verbessert werden.
-
Herausforderungen und Überlegungen
- Variabilität der Einsatzstoffe: Eine uneinheitliche Zusammensetzung des Ausgangsmaterials kann zu unvorhersehbaren Pyrolyseergebnissen führen, die angepasste Betriebsstrategien erfordern.
- Energieeinsatz: Der Energiebedarf für die Beheizung des Reaktors und die Aufrechterhaltung optimaler Bedingungen muss mit dem Energieertrag der Pyrolyseprodukte abgeglichen werden.
- Auswirkungen auf die Umwelt: Eine effiziente Pyrolyse minimiert Emissionen und Abfälle, doch kann ein unsachgemäßer Betrieb zur Freisetzung schädlicher Nebenprodukte führen.
-
Anwendungen und Vorteile
- Energieerzeugung: Bei der Pyrolyse werden Abfälle und Biomasse in energiereiche Produkte wie Bioöl, Synthesegas und Biokohle umgewandelt, die zur Stromerzeugung oder als Brennstoff verwendet werden können.
- Abfallwirtschaft: Die Pyrolyse reduziert das Abfallvolumen und wandelt es in wertvolle Ressourcen um, was zu einer Kreislaufwirtschaft beiträgt.
- Kohlenstoff-Sequestrierung: Die bei der Pyrolyse entstehende Biokohle kann zur Verbesserung der Bodengesundheit und zur Bindung von Kohlenstoff verwendet werden, wodurch die Treibhausgasemissionen verringert werden.
Durch das Verständnis und die Optimierung dieser Faktoren kann die Effizienz der Pyrolyse erheblich verbessert werden, was sie zu einer praktikablen und nachhaltigen Lösung für die Abfallwirtschaft und die Energieerzeugung macht.
Zusammenfassende Tabelle:
Faktor | Auswirkungen auf den Wirkungsgrad der Pyrolyse |
---|---|
Zusammensetzung des Rohstoffs | Bestimmt die Umwandlung in Gase, Flüssigkeiten oder Feststoffe auf der Grundlage der chemischen Struktur. |
Feuchtigkeitsgehalt | Ein hoher Feuchtigkeitsgehalt verringert die Effizienz; trockenes Ausgangsmaterial ist vorzuziehen. |
Partikelgröße | Kleinere Partikel vergrößern die Oberfläche und verbessern die Wärmeübertragung und die Gleichmäßigkeit der Reaktion. |
Temperatur | Optimaler Bereich: 400°C-800°C; höhere Temperaturen begünstigen die Gasausbeute, niedrigere Temperaturen begünstigen Flüssigkeiten/Feststoffe. |
Aufenthaltsdauer | Längere Zeiten gewährleisten eine vollständige Zersetzung, können aber den Durchsatz verringern. |
Reaktortyp | Die Wahl hängt vom Ausgangsmaterial und den gewünschten Produkten ab (z. B. Wirbelschicht, Festbett, Drehrohrofen). |
Heizrate | Kontrollierte Geschwindigkeiten gewährleisten eine effiziente Zersetzung; schnelles Erhitzen begünstigt Flüssigkeiten, langsames Erhitzen Gase. |
Katalytische Pyrolyse | Katalysatoren senken die Reaktionstemperaturen und verbessern die Ausbeute an bestimmten Produkten wie Bioöl oder Synthesegas. |
Optimieren Sie Ihren Pyrolyseprozess für maximale Effizienz kontaktieren Sie unsere Experten noch heute !