Das Sputter-Beschichtungsverfahren ist eine hochentwickelte Technik, um dünne Materialschichten auf ein Substrat aufzubringen.Dabei wird durch die elektrische Aufladung einer Sputterkathode ein Plasma erzeugt, das Material von einer Zieloberfläche ausstößt.Dieses herausgeschleuderte Material wird dann auf ein Substrat gerichtet und bildet eine starke Verbindung auf atomarer Ebene.Das Verfahren wird häufig in Anwendungen wie der Rasterelektronenmikroskopie (REM) eingesetzt, um die Oberflächenleitfähigkeit zu verbessern und Aufladungseffekte zu verringern.Im Folgenden werden die wichtigsten Schritte und Grundsätze des Sputter-Beschichtungsprozesses im Detail erläutert.
Die wichtigsten Punkte werden erklärt:
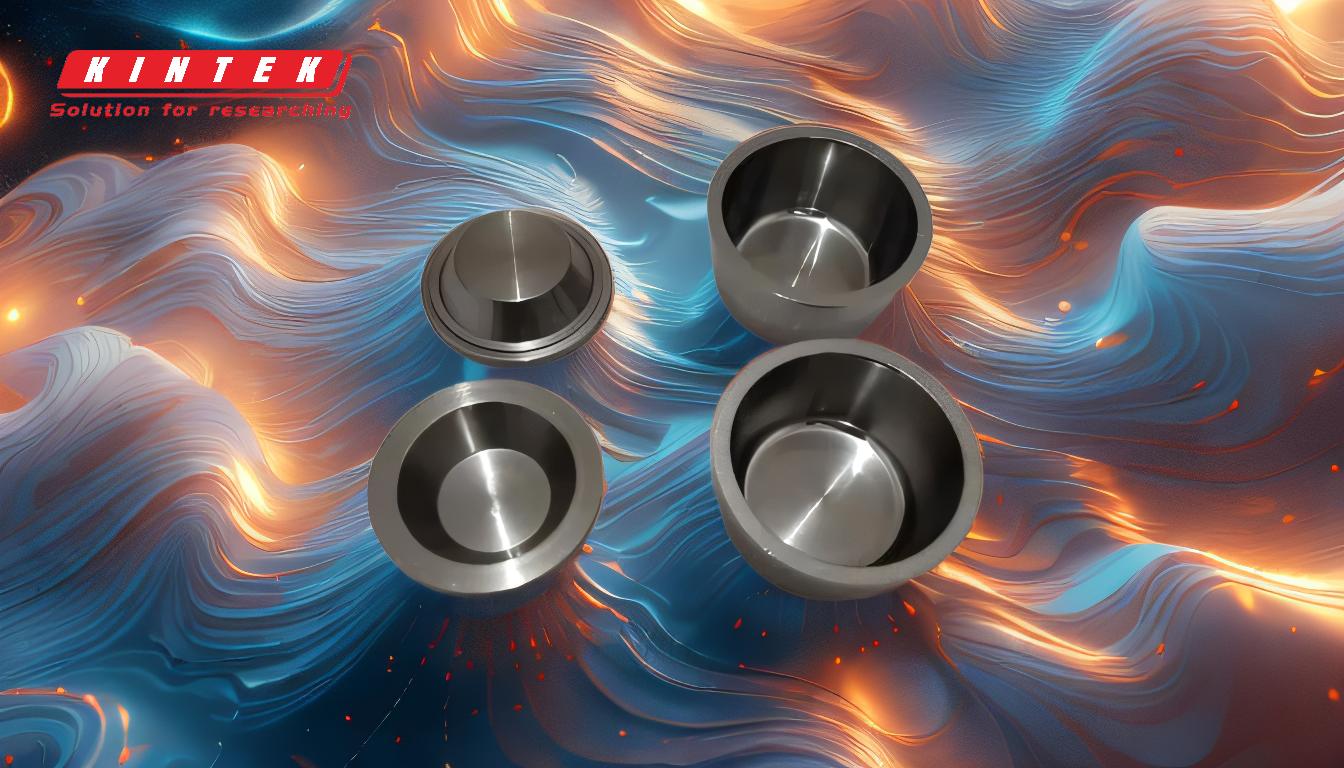
-
Bildung eines Plasmas
- Der Prozess beginnt mit der elektrischen Aufladung einer Sputterkathode, die ein Plasma erzeugt.Dieses Plasma besteht aus Gasatomen (in der Regel Argon), freien Elektronen und positiv geladenen Ionen.
- Das Plasma wird durch Magnetfelder konzentriert und stabilisiert, wodurch eine effiziente und gleichmäßige Zerstäubung des Zielmaterials gewährleistet wird.
-
Zerstäubung des Zielmaterials
- Das Targetmaterial, häufig Gold oder ein anderes leitfähiges Material, wird an die Kathode geklebt oder geklemmt.
- Hochenergetische Ionen aus dem Plasma beschießen die Oberfläche des Targets, wodurch Atome in einem als "Sputtern" bezeichneten Prozess herausgeschleudert werden.
- Magnete werden eingesetzt, um einen stabilen und gleichmäßigen Abtrag des Targetmaterials zu gewährleisten, was für eine gleichbleibende Beschichtungsqualität entscheidend ist.
-
Transport der gesputterten Atome
- Die gesputterten Atome werden durch einen Bereich mit reduziertem Druck (Vakuum) zum Substrat transportiert.
- Diese omnidirektionale Abscheidung gewährleistet, dass die gesputterten Atome die Oberfläche des Substrats gleichmäßig bedecken.
-
Abscheidung und Bindung
- Die mit hoher Energie gesputterten Atome treffen auf das Substrat und bilden eine starke Bindung auf atomarer Ebene.
- Das Ergebnis ist ein dünner, gleichmäßiger Film, der gut auf dem Substrat haftet und dessen Eigenschaften wie Leitfähigkeit und Haltbarkeit verbessert.
-
Anwendungen und Vorteile
- Die Sputterbeschichtung wird in der REM-Technik häufig eingesetzt, um die Sekundärelektronenemission zu verbessern und Aufladungseffekte zu verringern.
- Sie minimiert auch die thermische Schädigung des Substrats und ist daher für empfindliche Proben geeignet.
-
Hauptkomponenten eines Sputter Coaters
- Vakuumkammer: Hält eine Niederdruckumgebung aufrecht, um den Sputterprozess zu erleichtern.
- Zielmaterial: Das abzuscheidende Material, häufig Gold, Platin oder andere leitfähige Metalle.
- Kühlungssysteme: Bewältigung der während des Prozesses erzeugten Wärme, um Schäden an den Geräten und dem Substrat zu vermeiden.
-
Integration der Nanotechnologie
- Bei diesem Verfahren werden feste Materialien in mikroskopisch kleine Partikel umgewandelt, die dann als dünner Film aufgetragen werden.
- Diese Integration der Nanotechnologie gewährleistet eine präzise Kontrolle über die Dicke und Gleichmäßigkeit der Beschichtung.
Wenn man diese Kernpunkte versteht, kann man die Präzision und Komplexität des Sputterbeschichtungsprozesses nachvollziehen.Es ist eine wichtige Technik in der Materialwissenschaft und Mikroskopie, die erhebliche Vorteile bei der Oberflächenmodifizierung und -analyse bietet.
Zusammenfassende Tabelle:
Schritt | Beschreibung |
---|---|
Bildung von Plasma | Elektrisch geladene Kathode erzeugt Plasma (Argongas, Ionen, Elektronen). |
Sputtern des Targets | Hochenergetische Ionen beschießen das Zielmaterial und schleudern Atome zur Abscheidung aus. |
Transport der Atome | Die gesputterten Atome bewegen sich durch ein Vakuum und sorgen für eine gleichmäßige Beschichtung des Substrats. |
Abscheidung und Bindung | Atome bilden starke atomare Bindungen, die einen dünnen, dauerhaften Film auf dem Substrat erzeugen. |
Anwendungen | Verbessert die Bildgebung im REM, reduziert Aufladungseffekte und minimiert thermische Schäden. |
Wichtige Komponenten | Vakuumkammer, Targetmaterial (z. B. Gold) und Kühlsysteme. |
Integration von Nanotechnologie | Verwandelt Materialien in mikroskopisch kleine Partikel für präzise, gleichmäßige Beschichtungen. |
Entdecken Sie, wie die Sputterbeschichtung Ihre Anwendungen verbessern kann. Kontaktieren Sie unsere Experten noch heute !