Die Temperatur in einem Ofen für die Kohlenstoffregeneration liegt je nach Verfahrensstufe typischerweise zwischen 100°C und 800°C.In der ersten Aufheizphase wird die Temperatur innerhalb der ersten 1300 mm des Rohrs von 100 °C auf 750 °C erhöht.In den letzten 1000 mm, der so genannten Einweichzone, kann die Temperatur bis zu 800 °C erreichen.Diese hohe Temperatur ist entscheidend für die Vergasung der pyrolytischen Rückstände durch eine kontrollierte chemische Reaktion mit Wasserdampf, wodurch der Kohlenstoff effektiv regeneriert wird.
Die wichtigsten Punkte werden erklärt:
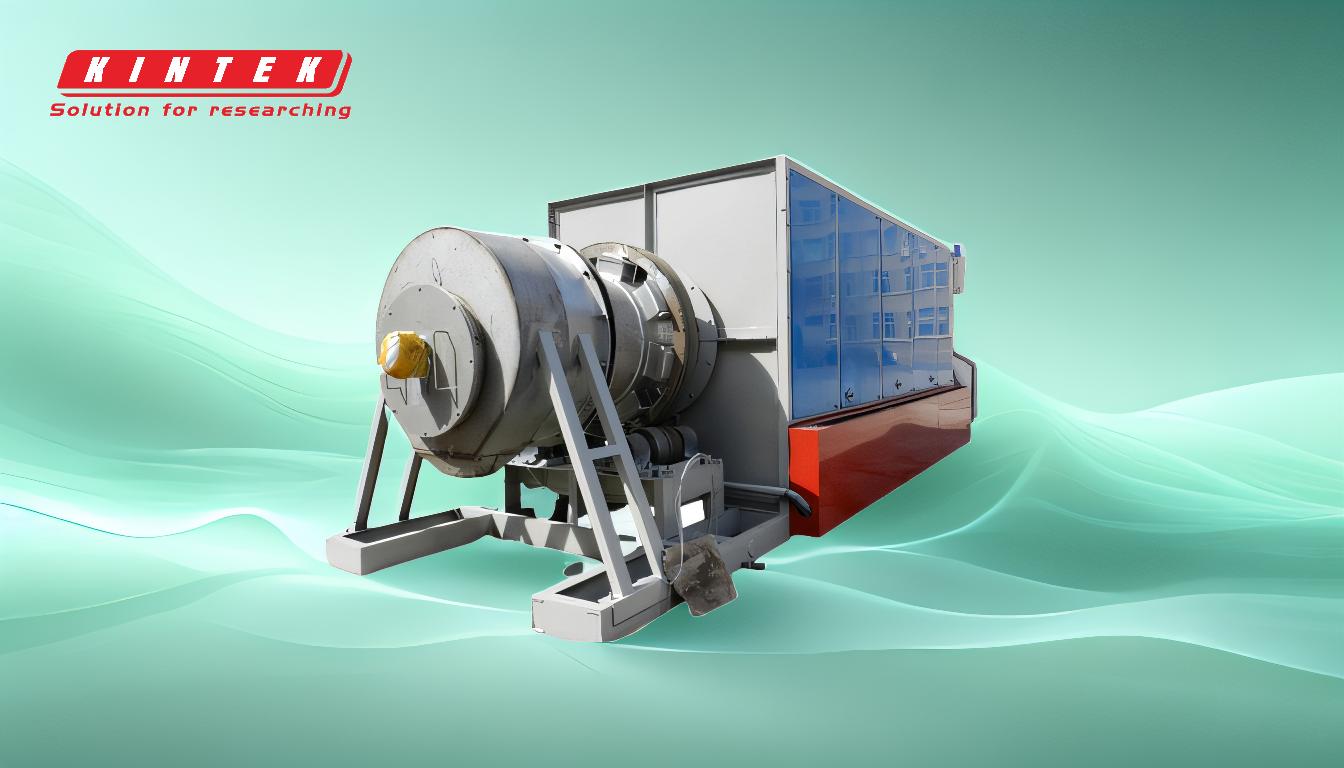
-
Temperaturbereich in der ersten Aufheizphase:
- 100°C bis 750°C:Die Temperatur wird innerhalb der ersten 1300 mm des Ofenrohrs schrittweise von 100°C auf 750°C erhöht.Diese Phase ist entscheidend für die Vorwärmung des Kohlenstoffs und seine Vorbereitung auf die anschließende Hochtemperaturbehandlung.
-
Temperatur in der Einweichzone:
- Bis zu 800°C:In den letzten 1000 mm des Ofenrohrs kann die Temperatur bis zu 800 °C erreichen.Dieser Bereich wird als "Soak-Zone" bezeichnet, in der der Kohlenstoff eine kontrollierte chemische Reaktion mit Wasserdampf eingeht.Die hohe Temperatur ist für die Vergasung der pyrolytischen Rückstände unerlässlich, die ein wichtiger Schritt im Regenerationsprozess ist.
-
Zweck der hohen Temperatur:
- Vergasung von Pyrolyse-Rückständen:Die erhöhte Temperatur in der Durchwärmungszone erleichtert die Vergasung der pyrolytischen Rückstände.Bei diesem Prozess findet eine kontrollierte chemische Reaktion mit Wasserdampf statt, die zum Abbau der Rückstände und zur Regenerierung des Kohlenstoffs beiträgt.Die hohe Temperatur gewährleistet, dass die Reaktion effizient und effektiv abläuft.
-
Kontrollierte chemische Reaktion:
- Wechselwirkung mit Wasserdampf:Die kontrollierte chemische Reaktion mit Wasserdampf bei hohen Temperaturen ist ein entscheidender Aspekt des Kohlenstoffregenerationsprozesses.Diese Reaktion trägt zur Entfernung von Verunreinigungen und zur Regenerierung der Kohle bei, so dass sie für die Wiederverwendung bereit ist.
-
Ofendesign und Temperaturzonen:
- Zonierte Heizung:Der Ofen ist mit spezifischen Temperaturzonen ausgestattet, um sicherzustellen, dass die Kohle allmählich erwärmt und dann den für die Vergasung erforderlichen hohen Temperaturen ausgesetzt wird.Die anfängliche Aufheizphase und die Durchwärmungszone werden sorgfältig kontrolliert, um den Regenerationsprozess zu optimieren.
-
Die Bedeutung der Temperaturkontrolle:
- Präzision beim Heizen:Die genaue Steuerung der Temperatur ist für die erfolgreiche Regenerierung der Kohle entscheidend.Die allmähliche Erhöhung der Temperatur und die Aufrechterhaltung hoher Temperaturen in der Durchwärmungszone sind notwendig, um die gewünschten chemischen Reaktionen zu erreichen und die Qualität der regenerierten Kohle zu gewährleisten.
Zusammenfassend lässt sich sagen, dass die Temperatur in einem Ofen für die Kohlenstoffregeneration sorgfältig kontrolliert wird und je nach Prozessphase variiert.In der ersten Aufheizphase steigt die Temperatur von 100°C auf 750°C, während sie in der Aufheizzone bis zu 800°C erreichen kann.Diese hohen Temperaturen sind für die Vergasung der pyrolytischen Rückstände und die effektive Regeneration des Kohlenstoffs unerlässlich.
Zusammenfassende Tabelle:
Stufe | Temperaturbereich | Zweck |
---|---|---|
Erste Aufheizphase | 100°C bis 750°C | Erwärmt Kohlenstoff vor und bereitet ihn für die Hochtemperaturbehandlung vor. |
Einweichzone (letzte 1000mm) | Bis zu 800°C | Erleichtert die Vergasung von pyrolytischen Rückständen durch kontrollierte Reaktionen. |
Benötigen Sie einen auf Ihr Verfahren zugeschnittenen Ofen zur Kohlenstoffregeneration? Kontaktieren Sie uns noch heute für fachkundige Beratung!