Diamantbeschichtung und keramische Beschichtung sind nicht dasselbe, auch wenn sie in Bezug auf Eigenschaften wie Härte und Haltbarkeit einige Gemeinsamkeiten aufweisen. Diamantbeschichtungen bestehen aus Kohlenstoffatomen, die in einer Diamantkristallstruktur angeordnet sind und eine außergewöhnliche Härte, Wärmeleitfähigkeit und chemische Beständigkeit aufweisen. Keramische Beschichtungen hingegen bestehen in der Regel aus Metalloxiden, Karbiden oder Nitriden und bieten hohe Härte und Verschleißfestigkeit, unterscheiden sich aber in ihrer Zusammensetzung und ihren spezifischen Eigenschaften. Beide werden zu Schutz- und Funktionszwecken eingesetzt, unterscheiden sich aber durch ihre Materialzusammensetzung, Abscheidungsmethoden und Leistungsmerkmale.
Die wichtigsten Punkte werden erklärt:
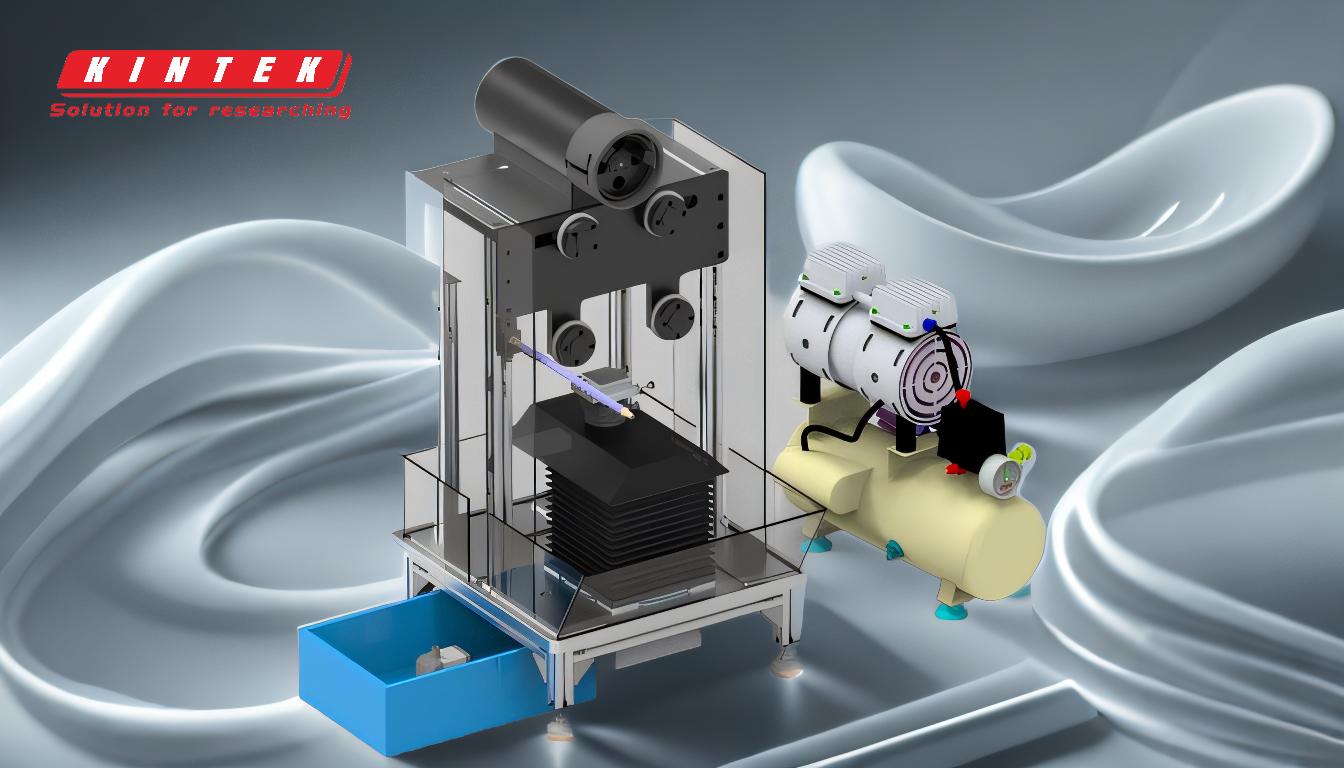
-
Materialzusammensetzung:
- Diamant-Beschichtung: Besteht aus Kohlenstoffatomen, die in einem Diamantkristallgitter angeordnet sind, was ihm eine unvergleichliche Härte und Wärmeleitfähigkeit verleiht. Er ist chemisch inert und verschleißfest.
- Keramische Beschichtung: Hergestellt aus Metalloxiden, Karbiden oder Nitriden (z. B. Aluminiumoxid, Siliziumkarbid oder Titannitrid). Diese Materialien sind hart und haltbar, unterscheiden sich aber in Struktur und Eigenschaften deutlich von Diamant.
-
Eigenschaften:
-
Diamant-Beschichtung:
- Extrem hohe Härte (ähnlich wie bei natürlichem Diamant).
- Hervorragende Wärmeleitfähigkeit, daher geeignet für Anwendungen zur Wärmeableitung.
- Chemisch inert, korrosions- und verschleißbeständig.
-
Keramische Beschichtung:
- Hohe Härte und Verschleißfestigkeit, jedoch im Allgemeinen geringer als Diamant.
- Gute thermische und elektrische Isolationseigenschaften.
- Widerstandsfähig gegen Oxidation und Korrosion, aber nicht so chemisch inert wie Diamant.
-
Diamant-Beschichtung:
-
Ablagerungsmethoden:
- Diamant-Beschichtung: In der Regel durch chemische Abscheidung aus der Gasphase (CVD) oder physikalische Abscheidung aus der Gasphase (PVD). Das Verfahren beinhaltet eine präzise Steuerung der Gasphasenzusammensetzung und der Abscheidungsparameter, um Eigenschaften wie Korngröße und Oberflächenrauhigkeit anzupassen.
- Keramische Beschichtung: Aufgetragen durch Verfahren wie thermisches Spritzen, Plasmaspritzen oder PVD/CVD. Das Verfahren variiert je nach dem spezifischen keramischen Material und den Anwendungsanforderungen.
-
Anwendungen:
- Diamant-Beschichtung: Verwendet in Hochleistungsanwendungen wie Schneidwerkzeugen, verschleißfesten Oberflächen und Kühlkörpern. Seine außergewöhnlichen Eigenschaften machen es ideal für extreme Bedingungen.
- Keramische Beschichtung: Wird häufig in der Luft- und Raumfahrt, in der Automobilindustrie und im verarbeitenden Gewerbe für Verschleißschutz, Wärmedämmschichten und elektrische Isolierung verwendet.
-
Kosten und Zugänglichkeit:
- Diamant-Beschichtung: In der Regel teurer aufgrund der Komplexität des Abscheidungsverfahrens und der hohen Kosten für die Rohstoffe. Es wird für spezielle Anwendungen verwendet, bei denen seine einzigartigen Eigenschaften entscheidend sind.
- Keramische Beschichtung: Kostengünstiger und weithin verfügbar, daher für ein breiteres Spektrum an industriellen Anwendungen geeignet.
Zusammenfassend lässt sich sagen, dass sowohl Diamant- als auch Keramikbeschichtungen zwar eine hohe Härte und Haltbarkeit aufweisen, sich aber in der Materialzusammensetzung, den Eigenschaften, den Beschichtungsmethoden und den Anwendungen unterscheiden. Diamantbeschichtungen sind in Bezug auf Härte und Wärmeleitfähigkeit überlegen, aber sie sind teurer und spezieller. Keramische Beschichtungen hingegen sind vielseitiger und kostengünstiger und eignen sich daher für ein breiteres Spektrum von Anwendungen.
Zusammenfassende Tabelle:
Aspekt | Diamant-Beschichtung | Keramische Beschichtung |
---|---|---|
Materialzusammensetzung | Kohlenstoffatome in einem Diamant-Kristallgitter | Metalloxide, Karbide oder Nitride (z. B. Aluminiumoxid, Siliziumkarbid) |
Eigenschaften |
- Extrem hohe Härte
- Ausgezeichnete Wärmeleitfähigkeit - Chemisch inert |
- Hohe Härte
- Gute thermische/elektrische Isolierung - Widerstandsfähig gegen Oxidation |
Ablagerungsmethoden | CVD oder PVD | Thermisches Spritzen, Plasmaspritzen oder PVD/CVD |
Anwendungen | Schneidwerkzeuge, verschleißfeste Oberflächen, Wärmesenken | Luft- und Raumfahrt, Automobilindustrie, Fertigung (Verschleißschutz, thermische Barrieren) |
Kosten | Teuer und spezialisiert | Kostengünstig und weithin verfügbar |
Benötigen Sie Hilfe bei der Auswahl der richtigen Beschichtung für Ihre Anwendung? Kontaktieren Sie unsere Experten noch heute!