Das Sputtering-Verfahren ist zwar für die Abscheidung von Dünnschichten weit verbreitet, hat aber einige bemerkenswerte Nachteile.Dazu gehören niedrige Abscheideraten, hohe Investitions- und Betriebskosten, das Risiko der Filmverunreinigung und Probleme bei der Materialkompatibilität.Darüber hinaus kann das Sputtern zu ineffizientem Materialeinsatz, ungleichmäßiger Schichtdicke und Schwierigkeiten bei der Integration mit bestimmten Herstellungsverfahren wie Lift-off führen.Das Verfahren erzeugt auch erhebliche Wärme, so dass robuste Kühlsysteme erforderlich sind, und ist bei isolierenden Materialien weniger effektiv.Aufgrund dieser Nachteile ist das Sputtern für bestimmte Anwendungen weniger geeignet, insbesondere für solche, die hohe Präzision, Kosteneffizienz oder Kompatibilität mit empfindlichen Materialien erfordern.
Die wichtigsten Punkte erklärt:
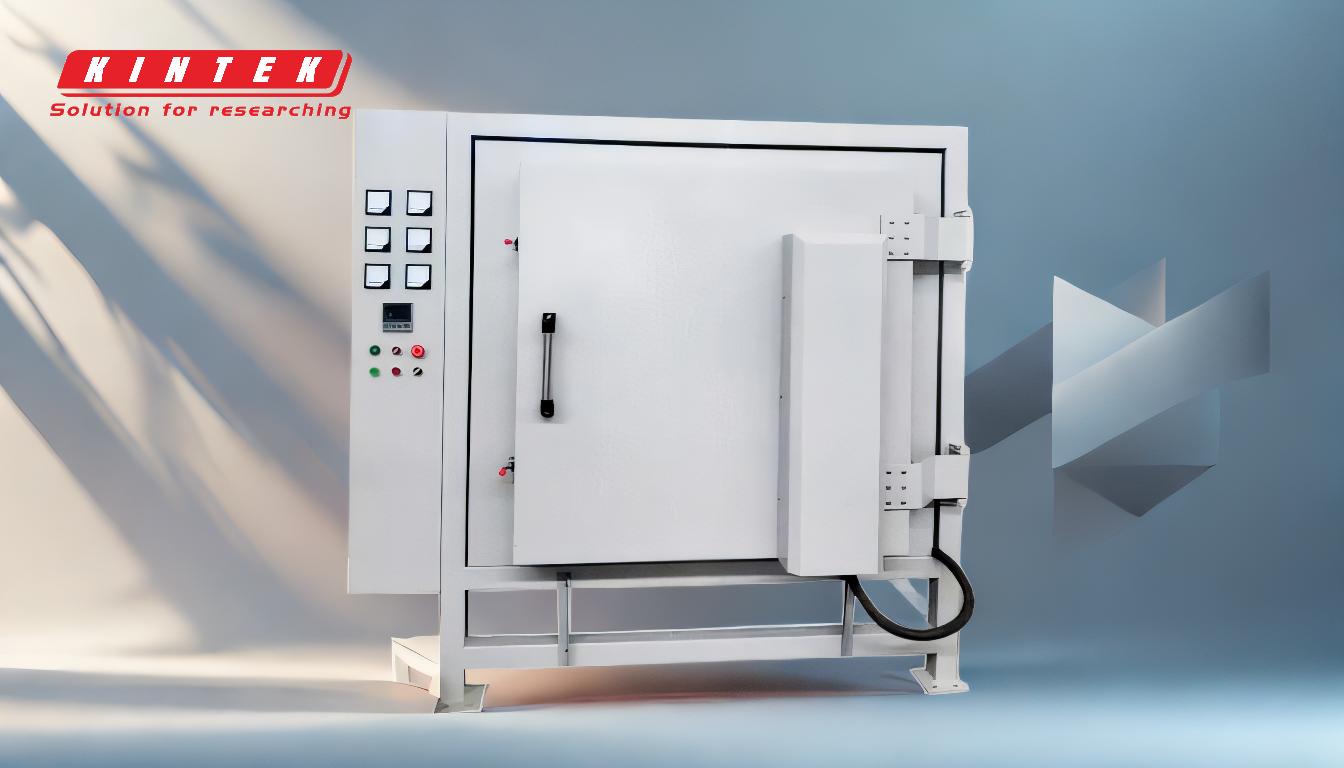
-
Niedrige Abscheideraten
- Im Vergleich zu anderen Verfahren wie der thermischen Verdampfung weist das Sputtern im Allgemeinen geringere Abscheideraten auf.
- Diese Einschränkung ist besonders ausgeprägt bei Materialien wie SiO2, bei denen das Erreichen der gewünschten Schichtdicke zeitaufwändig sein kann.
- Langsame Abscheidungsraten können die Produktionszeit und -kosten erhöhen, was das Sputtern für Anwendungen mit hohem Durchsatz weniger effizient macht.
-
Hohe Kapital- und Betriebskosten
- Sputtering-Anlagen sind teuer und erfordern erhebliche Vorabinvestitionen.
- Auch die Wartungskosten sind hoch, da spezielle Vakuumsysteme und Kühlmechanismen erforderlich sind, um die während des Prozesses entstehende Wärme zu bewältigen.
- Die beim Sputtern verwendeten Targets sind oft kostspielig, und die Materialausnutzung kann ineffizient sein, was die Kosten weiter erhöht.
-
Risiken der Filmkontamination
- Beim Sputtern herrscht im Vergleich zur Verdampfung ein niedrigeres Vakuum, wodurch die Wahrscheinlichkeit steigt, dass Verunreinigungen in das Substrat gelangen.
- Gasförmige Verunreinigungen im Plasma können aktiviert werden, was zu einer Verunreinigung der abgeschiedenen Schicht führt.
- Das reaktive Sputtern erfordert eine genaue Kontrolle der Gaszusammensetzung, um eine Vergiftung des Targets zu vermeiden, was die Komplexität und das Risiko erhöht.
-
Ungleichmäßige Schichtdicke
- Die Verteilung des Abscheidungsflusses beim Sputtern ist oft ungleichmäßig, so dass bewegliche Vorrichtungen verwendet werden müssen, um eine gleichmäßige Schichtdicke zu erreichen.
- Dies macht den Prozess noch komplexer und kann zu einer uneinheitlichen Schichtqualität führen, wenn er nicht sorgfältig gesteuert wird.
-
Wärmeerzeugung und Substraterwärmung
- Der größte Teil der auf das Ziel auftreffenden Energie wird in Wärme umgewandelt, die wirksam abgeführt werden muss, um eine Beschädigung des Substrats oder der Ausrüstung zu verhindern.
- Eine starke Erwärmung des Substrats kann die Arten von Materialien einschränken, die beschichtet werden können, insbesondere solche, die temperaturempfindlich sind.
-
Probleme mit der Materialkompatibilität
- Das Sputtern ist nicht für isolierende Materialien geeignet, da diese Ladungen ansammeln und den Prozess stören können.
- Organische Feststoffe und andere empfindliche Materialien können sich unter Ionenbeschuss zersetzen, was die Palette der Materialien, die effektiv gesputtert werden können, einschränkt.
-
Herausforderungen bei der Integration mit Lift-Off-Prozessen
- Aufgrund des diffusen Transports der gesputterten Atome ist es schwierig, eine vollständige Abschattung zu erreichen, was die Integration des Sputterns mit Lift-Off-Prozessen zur Schichtstrukturierung erschwert.
- Dies kann zu Kontaminationsproblemen führen und die Präzision des Endprodukts verringern.
-
Schwierige aktive Kontrolle des schichtweisen Wachstums
- Im Vergleich zu Verfahren wie der gepulsten Laserabscheidung bietet das Sputtern weniger Kontrolle über das schichtweise Wachstum.
- Diese Einschränkung kann sich auf die Qualität und Gleichmäßigkeit von Mehrschichtfilmen auswirken, insbesondere bei Anwendungen, die eine präzise Kontrolle auf atomarer Ebene erfordern.
-
Verunreinigungen durch Inertgas
- Inerte Sputtergase, wie z. B. Argon, können als Verunreinigungen in der wachsenden Schicht eingeschlossen werden.
- Diese Verunreinigungen können die mechanischen, elektrischen oder optischen Eigenschaften der abgeschiedenen Schicht beeinträchtigen und so deren Leistung beeinträchtigen.
-
Beschränkungen der Prozessparameter
- Das Sputtern wird durch die Gegebenheiten von Vakuumsystemen eingeschränkt, die den Bereich der verwendbaren Prozessparameter begrenzen.
- Dies kann die Vielseitigkeit des Verfahrens einschränken und es weniger anpassungsfähig an spezifische Anwendungsanforderungen machen.
Zusammenfassend lässt sich sagen, dass das Sputtern zwar eine vielseitige und weit verbreitete Technik für die Abscheidung von Dünnschichten ist, ihre Nachteile - wie niedrige Abscheideraten, hohe Kosten, Kontaminationsrisiken und Probleme mit der Materialverträglichkeit - ihre Eignung für bestimmte Anwendungen jedoch einschränken können.Eine sorgfältige Abwägung dieser Nachteile ist bei der Auswahl einer Abscheidungsmethode für bestimmte Industrie- oder Forschungsanforderungen unerlässlich.
Zusammenfassende Tabelle:
Benachteiligung | Wichtige Details |
---|---|
Niedrige Abscheidungsraten | Langsamer als thermische Verdampfung; erhöht die Produktionszeit und die Kosten. |
Hohe Kapital- und Betriebskosten | Teure Ausrüstung, hoher Wartungsaufwand und ineffizienter Materialeinsatz. |
Risiken der Filmkontamination | Niedrigerer Vakuumbereich erhöht das Risiko von Verunreinigungen; reaktives Sputtern erhöht die Komplexität. |
Ungleichmäßige Schichtdicke | Erfordert bewegliche Vorrichtungen; kann zu ungleichmäßiger Filmqualität führen. |
Wärmeentwicklung | Hohe Wärmeentwicklung erfordert robuste Kühlsysteme; schränkt temperaturempfindliche Materialien ein. |
Probleme mit der Materialkompatibilität | Ungeeignet für Isolatoren und empfindliche Materialien; Degradationsrisiken. |
Herausforderungen bei der Integration | Schwierigkeiten mit Lift-off-Prozessen; Verunreinigungs- und Präzisionsprobleme. |
Begrenzte Schicht-für-Schicht-Kontrolle | Geringere Kontrolle im Vergleich zur gepulsten Laserabscheidung; beeinträchtigt die Gleichmäßigkeit der Multilayer. |
Verunreinigungen durch Inertgas | Argon-Verunreinigungen können die Filmeigenschaften beeinträchtigen. |
Beschränkungen der Prozessparameter | Beschränkungen des Vakuumsystems schränken die Vielseitigkeit und Anpassungsfähigkeit ein. |
Benötigen Sie eine bessere Lösung für die Dünnschichtabscheidung? Kontaktieren Sie uns noch heute um Alternativen zu erkunden!