Das Mahlen in einer Kugelmühle ist ein komplexer Prozess, der von zahlreichen Faktoren beeinflusst wird, die die Effizienz, die Partikelgröße und die Gesamtleistung der Mühle bestimmen.Zu den Schlüsselfaktoren gehören die Rotationsgeschwindigkeit, die Größe und Art des Mahlmediums, die Eigenschaften des gemahlenen Materials, der Füllungsgrad der Mühle und die Konstruktionsparameter der Mühle selbst.Diese Faktoren beeinflussen in ihrem Zusammenspiel die Verweilzeit, den Energieverbrauch und die endgültige Partikelgrößenverteilung.Das Verständnis und die Optimierung dieser Variablen ist entscheidend für die Erzielung der gewünschten Mahlergebnisse, sei es für die Herstellung feiner Partikel oder die effiziente Materialverarbeitung.
Die wichtigsten Punkte erklärt:
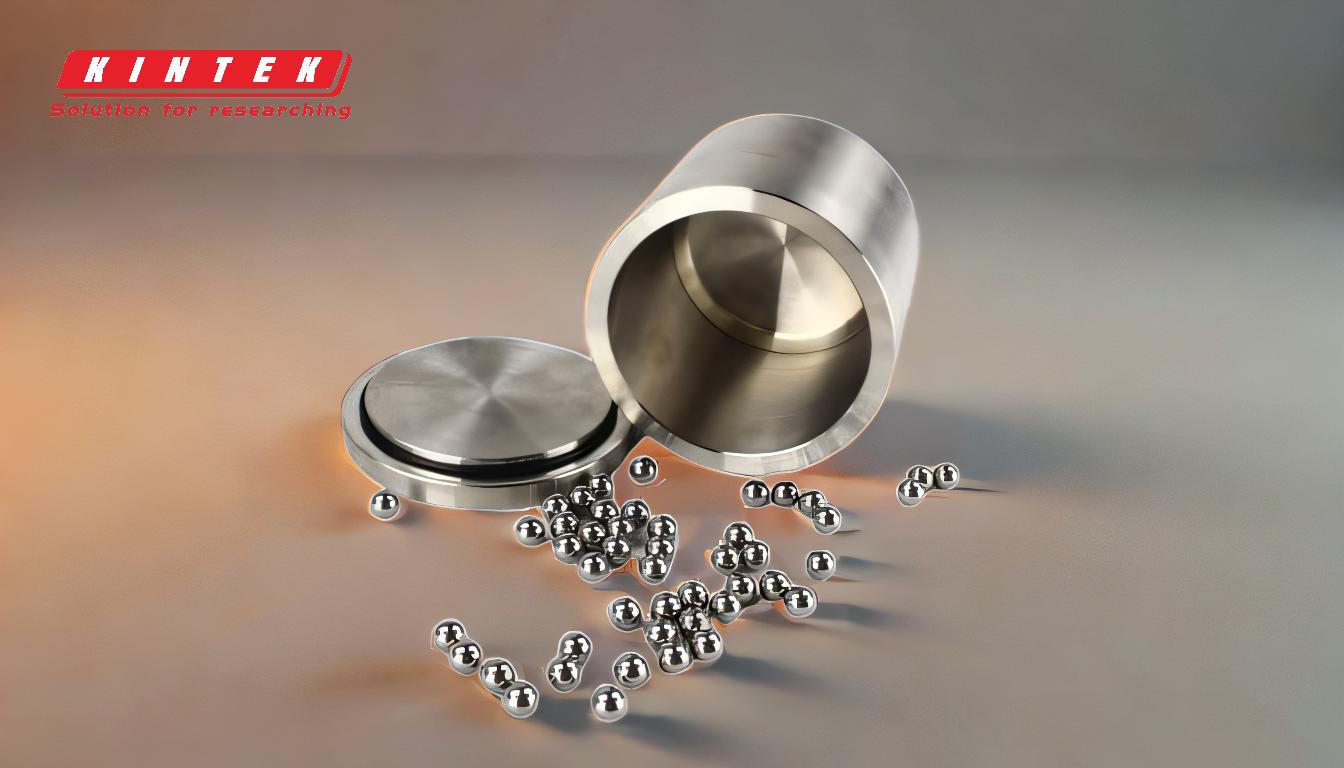
-
Rotationsgeschwindigkeit
- Die Rotationsgeschwindigkeit der Kugelmühle wirkt sich direkt auf die Bewegung der Mahlkörper und des Materials aus.
- Bei optimalen Drehzahlen werden die Kugeln auf eine bestimmte Höhe angehoben und fallen dann kaskadenförmig nach unten, wobei Aufprall- und Scherkräfte für die Zerkleinerung entstehen.
- Ist die Geschwindigkeit zu niedrig, erreichen die Kugeln möglicherweise keine ausreichende Höhe, was die Mahlleistung verringert.
- Ist die Drehzahl zu hoch, können die Kugeln zentrifugieren, an den Wänden haften bleiben und die Mahlwirkung verringern.
- Die kritische Drehzahl (die Drehzahl, bei der die Zentrifugation einsetzt) ist ein wichtiger Parameter, den es zu vermeiden gilt.
-
Größe und Art des Mahlmediums
-
Die Größe der Mahlkugeln wirkt sich auf die Energieübertragung und die Verringerung der Partikelgröße aus.
- Größere Kugeln sind effektiver für die Grobvermahlung, während kleinere Kugeln besser für die Feinvermahlung geeignet sind.
-
Die Dichte und Härte der Mahlkörper beeinflussen die Verschleißrate und die Mahlleistung.
- Härtere Materialien wie Stahl oder Keramik werden für eine längere Lebensdauer und gleichbleibende Leistung bevorzugt.
- Auch die Anzahl der Kugeln spielt eine Rolle: Zu wenige Kugeln verringern die Mahlleistung, während zu viele Kugeln zu Überfüllung und verminderter Schlagenergie führen können.
-
Die Größe der Mahlkugeln wirkt sich auf die Energieübertragung und die Verringerung der Partikelgröße aus.
-
Größe und Art des zu mahlenden Materials
-
Die anfängliche Partikelgröße und die Härte des Materials beeinflussen die Mahlleistung erheblich.
- Härtere Materialien benötigen mehr Energie und Zeit zum Mahlen, während weichere Materialien leichter zu verarbeiten sind.
- Die Zufuhrgeschwindigkeit und die Korngrößenverteilung des Materials müssen optimiert werden, um eine Überlastung der Mühle oder eine ungleichmäßige Vermahlung zu vermeiden.
- Materialien mit hohem Feuchtigkeitsgehalt oder klebrigen Eigenschaften erfordern möglicherweise Anpassungen, um Verstopfungen oder eine verminderte Mahlleistung zu vermeiden.
-
Die anfängliche Partikelgröße und die Härte des Materials beeinflussen die Mahlleistung erheblich.
-
Füllungsgrad der Mühle
- Der Füllungsgrad gibt an, wie viel Prozent des Mühlenvolumens durch das Mahlgut eingenommen werden.
-
Ein optimaler Füllungsgrad gewährleistet eine effiziente Mahlung ohne übermäßigen Energieverbrauch.
- Ein zu niedriger Füllungsgrad verringert die Anzahl der Mahlstöße und senkt die Effizienz.
- Ein zu hoher Füllungsgrad kann zu übermäßigen Kollisionen zwischen den Kugeln führen, was deren Effektivität verringert.
- Der Füllungsgrad wirkt sich auch auf die Verweilzeit des Materials in der Mühle und damit auf die endgültige Partikelgröße aus.
-
Verweilzeit und Aufgabemenge
-
Die Verweilzeit ist die Zeit, die das Material in der Mühle verbringt und die sich direkt auf den Mahlgrad auswirkt.
- Längere Verweilzeiten führen im Allgemeinen zu feineren Partikeln, können aber den Durchsatz verringern.
- Die Aufgabemenge muss auf die Kapazität der Mühle abgestimmt sein, um eine gleichmäßige Vermahlung zu gewährleisten und eine Überlastung zu vermeiden.
- Zur Aufrechterhaltung optimaler Mahlbedingungen ist eine kontinuierliche Überwachung und Anpassung der Aufgabemenge erforderlich.
-
Die Verweilzeit ist die Zeit, die das Material in der Mühle verbringt und die sich direkt auf den Mahlgrad auswirkt.
-
Konstruktionsparameter der Mühle
-
Der Trommeldurchmesser und das Verhältnis von Länge zu Durchmesser (L:D) sind entscheidende Konstruktionsfaktoren.
- Ein optimales L:D-Verhältnis (in der Regel 1,56-1,64) gewährleistet eine effiziente Mahlung und Energienutzung.
- Die Form und Beschaffenheit des Mühleninneren (Panzeroberfläche) beeinflussen die Bewegung der Mahlkörper und des Materials.
- Die richtige Belüftung und der rechtzeitige Abtransport des Mahlguts sind entscheidend, um eine Überhitzung zu vermeiden und die Mahlleistung aufrechtzuerhalten.
-
Der Trommeldurchmesser und das Verhältnis von Länge zu Durchmesser (L:D) sind entscheidende Konstruktionsfaktoren.
-
Physikalisch-chemische Eigenschaften des Aufgabematerials
-
Die chemische Zusammensetzung, die Härte und die Abrasivität des Materials beeinflussen die Schleifleistung.
- Abrasive Materialien können die Schleifkörper schneller abnutzen, so dass sie häufiger ausgetauscht werden müssen.
- Die spezifische Oberfläche und die Korngrößenverteilung des gemahlenen Materials werden durch die Materialeigenschaften beeinflusst.
-
Die chemische Zusammensetzung, die Härte und die Abrasivität des Materials beeinflussen die Schleifleistung.
-
Anzahl der Mahlzyklen
- Um die gewünschte Partikelgröße zu erreichen, können mehrere Mahlzyklen erforderlich sein, insbesondere bei der Feinmahlung.
- Jeder Zyklus erhöht die Verweilzeit und den Energieverbrauch, verbessert aber die Gleichmäßigkeit des Endprodukts.
-
Umwelteinflüsse und betriebliche Faktoren
- Temperatur und Luftfeuchtigkeit können die Mahlleistung beeinträchtigen, insbesondere bei feuchtigkeitsempfindlichen Materialien.
- Eine ordnungsgemäße Wartung und Ausrichtung der Mühle gewährleisten eine gleichbleibende Leistung und reduzieren die Ausfallzeiten.
Durch sorgfältige Kontrolle und Optimierung dieser Faktoren können Betreiber effiziente Mahlprozesse erzielen, den Energieverbrauch senken und qualitativ hochwertiges Mahlgut mit der gewünschten Korngrößenverteilung produzieren.
Zusammenfassende Tabelle:
Faktor | Auswirkung |
---|---|
Geschwindigkeit der Rotation | Beeinflusst die Bewegung der Mahlkörper; eine optimale Drehzahl gewährleistet eine effiziente Mahlung. |
Größe/Typ des Mahlmediums | Größere Kugeln für die Grobvermahlung, kleinere für die Feinvermahlung; die Materialhärte spielt eine Rolle. |
Materialeigenschaften | Härte, Feuchtigkeit und Vorschubgeschwindigkeit beeinflussen die Mahlleistung. |
Füllungsgrad | Ein optimales Verhältnis gewährleistet eine effiziente Zerkleinerung ohne übermäßigen Energieverbrauch. |
Verweilzeit & Vorschubgeschwindigkeit | Längere Verweilzeit = feinere Partikel; ausgewogene Zuführungsrate vermeidet Überlastung. |
Parameter der Mühlenkonstruktion | Der Trommeldurchmesser, das Verhältnis L:D und die innere Beschaffenheit beeinflussen die Mahlleistung. |
Umweltfaktoren | Temperatur, Luftfeuchtigkeit und Wartung wirken sich auf Leistung und Ausfallzeiten aus. |
Optimieren Sie Ihren Kugelmühlenprozess noch heute - Kontaktieren Sie unsere Experten für maßgeschneiderte Lösungen!