PVD-Beschichtungen (Physical Vapor Deposition) bestehen aus einer Vielzahl von Elementen und Verbindungen, die auf bestimmte Leistungsanforderungen zugeschnitten sind.Diese Beschichtungen kombinieren in der Regel Metalle wie Titan, Zirkonium, Aluminium und Gold mit nichtmetallischen Elementen wie Stickstoff, Sauerstoff, Kohlenstoff und Silizium.Die daraus resultierenden Verbindungen wie Nitride, Oxide, Karbide und diamantähnlicher Kohlenstoff (DLC) bieten verbesserte Eigenschaften wie Härte, Verschleißfestigkeit und Korrosionsbeständigkeit.Die Wahl der Bestandteile hängt von der Anwendung ab, wobei spezielle Beschichtungen in Branchen wie der Luft- und Raumfahrt, der Automobilindustrie und der Elektronik verwendet werden.Beim PVD-Verfahren wird ein festes Zielmaterial verdampft, das dann auf einem Substrat kondensiert und eine dünne, haltbare Beschichtung bildet.
Die wichtigsten Punkte erklärt:
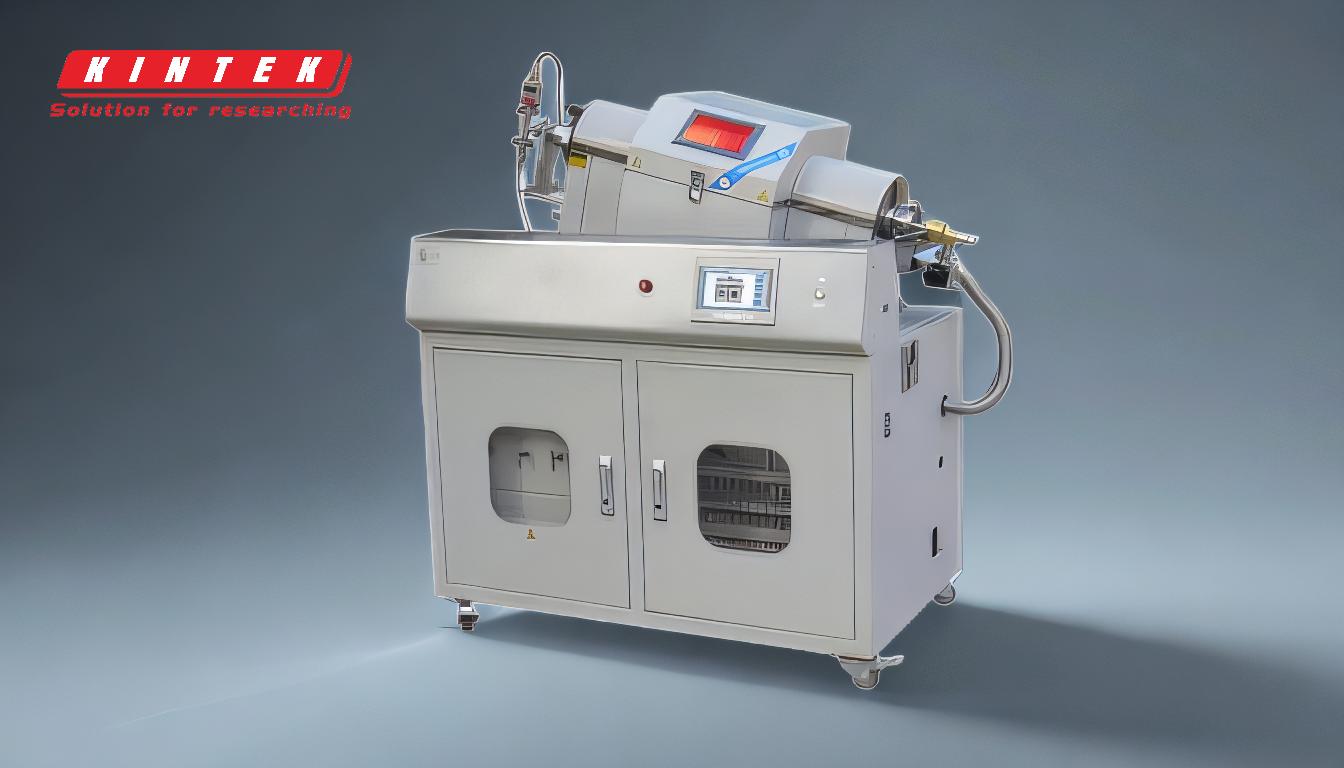
-
Die wichtigsten Bestandteile von PVD-Beschichtungen:
- Metalle:Zu den häufig verwendeten Metallen gehören Titan, Zirkonium, Aluminium, Edelstahl, Kupfer und Gold.Diese Metalle bilden die Grundlage der Beschichtung und tragen zu Eigenschaften wie Härte und Leitfähigkeit bei.
- Nicht-metallische Elemente:Stickstoff, Sauerstoff, Kohlenstoff und Silizium werden häufig mit Metallen kombiniert, um Verbindungen wie Nitride (z. B. Titannitrid), Oxide, Carbide und Silizide zu bilden.
- Spezialisierte Materialien:Materialien wie diamantähnlicher Kohlenstoff (DLC), Graphit und Verbindungen auf Molybdänbasis werden für spezielle Anwendungen verwendet, die extreme Haltbarkeit oder geringe Reibung erfordern.
-
Gängige PVD-Beschichtungsmaterialien:
- Beschichtungen auf Titan-Basis:Titannitrid (TiN) ist eine der am häufigsten verwendeten PVD-Beschichtungen, die für ihre goldene Farbe und hervorragende Verschleißfestigkeit bekannt ist.
- Beschichtungen auf Zirkonium-Basis:Zirkoniumnitrid (ZrN) bietet hohe Härte und Korrosionsbeständigkeit und wird häufig in medizinischen und dekorativen Anwendungen eingesetzt.
- Beschichtungen auf Aluminiumbasis:Aluminiumoxid (Al₂O₃) bietet eine hervorragende thermische und elektrische Isolierung und ist daher für die Elektronik geeignet.
- Diamantähnlicher Kohlenstoff (DLC):DLC-Beschichtungen werden wegen ihrer Härte, geringen Reibung und Biokompatibilität geschätzt und häufig in der Automobil- und Medizinbranche eingesetzt.
- Gold und andere Edelmetalle:Goldbeschichtungen werden in der Luft- und Raumfahrtelektronik wegen ihrer hervorragenden Leitfähigkeit und Korrosionsbeständigkeit eingesetzt.
-
Individuelle Anpassung für spezifische Anwendungen:
-
PVD-Beschichtungen sind in hohem Maße anpassbar und ermöglichen die Kombination verschiedener Elemente, um die gewünschten Eigenschaften zu erzielen.Zum Beispiel:
- Luft- und Raumfahrt:Beschichtungen auf Gold- und Titanbasis werden wegen ihrer Leitfähigkeit und Widerstandsfähigkeit gegen extreme Umgebungsbedingungen verwendet.
- Automobilindustrie:DLC- und Titannitrid-Beschichtungen werden auf Motorkomponenten aufgebracht, um die Verschleißfestigkeit und Reibung zu verringern.
- Medizinische:Zirkoniumnitrid- und DLC-Beschichtungen werden aufgrund ihrer Biokompatibilität und Haltbarkeit für chirurgische Werkzeuge und Implantate verwendet.
-
PVD-Beschichtungen sind in hohem Maße anpassbar und ermöglichen die Kombination verschiedener Elemente, um die gewünschten Eigenschaften zu erzielen.Zum Beispiel:
-
PVD-Beschichtungsprozess:
- Beim PVD-Verfahren wird ein festes Zielmaterial (z. B. Titan oder Gold) in einer Vakuumkammer verdampft.Das verdampfte Material kondensiert dann auf dem Substrat und bildet eine dünne, gleichmäßige Beschichtung.Dieses Verfahren ermöglicht eine genaue Kontrolle über die Zusammensetzung und Dicke der Beschichtung.
-
Substrate für PVD-Beschichtungen:
-
PVD-Beschichtungen können auf eine breite Palette von Substraten aufgebracht werden, darunter:
- Metalle:Rostfreier Stahl, Aluminium und Titan.
- Kunststoffe und Nylon:Wird für dekorative und funktionelle Anwendungen verwendet.
- Keramik und Glas:Häufig beschichtet für verbesserte Haltbarkeit und optische Eigenschaften.
-
PVD-Beschichtungen können auf eine breite Palette von Substraten aufgebracht werden, darunter:
-
Vorteile von PVD-Beschichtungen:
- Dauerhaftigkeit:PVD-Beschichtungen sind äußerst verschleiß-, korrosions- und oxidationsbeständig.
- Vielseitigkeit:Die Möglichkeit, verschiedene Materialien zu kombinieren, ermöglicht maßgeschneiderte Lösungen für verschiedene Branchen.
- Ästhetik:Beschichtungen wie Titannitrid und Gold bieten attraktive Oberflächen für dekorative Anwendungen.
Wer die Inhaltsstoffe und Eigenschaften von PVD-Beschichtungen kennt, kann die am besten geeigneten Materialien für seine spezifischen Anforderungen auswählen und so eine optimale Leistung und Langlebigkeit der beschichteten Komponenten gewährleisten.
Zusammenfassende Tabelle:
Kategorie | Beispiele | Eigenschaften |
---|---|---|
Kernmetalle | Titan, Zirkonium, Aluminium, Gold, rostfreier Stahl, Kupfer | Härte, Leitfähigkeit, Korrosionsbeständigkeit |
Nicht-metallische Elemente | Stickstoff, Sauerstoff, Kohlenstoff, Silizium | Bildet Nitride, Oxide, Karbide, Silizide |
Spezialisierte Materialien | Diamantähnlicher Kohlenstoff (DLC), Graphit, Molybdän-Verbindungen | Extreme Langlebigkeit, geringe Reibung |
Gängige Mischungen | Titannitrid (TiN), Zirkoniumnitrid (ZrN), Aluminiumoxid (Al₂O₃) | Verschleißfestigkeit, Korrosionsbeständigkeit, thermische Isolierung |
Anwendungen | Luft- und Raumfahrt, Automobil, Elektronik, Medizin | Leitfähigkeit, Biokompatibilität, Langlebigkeit, Ästhetik |
Sind Sie bereit, Ihre Komponenten mit PVD-Beschichtungen zu verbessern? Kontaktieren Sie noch heute unsere Experten für maßgeschneiderte Lösungen!