Die chemische Gasphasenabscheidung (Chemical Vapor Deposition, CVD) ist ein in der Materialwissenschaft und der Halbleiterherstellung weit verbreitetes Verfahren zur Abscheidung dünner Schichten.Sie ist jedoch mit einigen Herausforderungen verbunden, darunter hohe Kosten, komplexe Ausrüstungsanforderungen und potenzielle Probleme mit der Qualität und Einheitlichkeit der Schichten.Außerdem ist das Verfahren häufig mit hohen Temperaturen und giftigen Gasen verbunden, was zu Sicherheits- und Umweltproblemen führt.Trotz seiner Vorteile können diese Probleme seine Anwendbarkeit und Effizienz in bestimmten Szenarien einschränken.
Die wichtigsten Punkte werden erklärt:
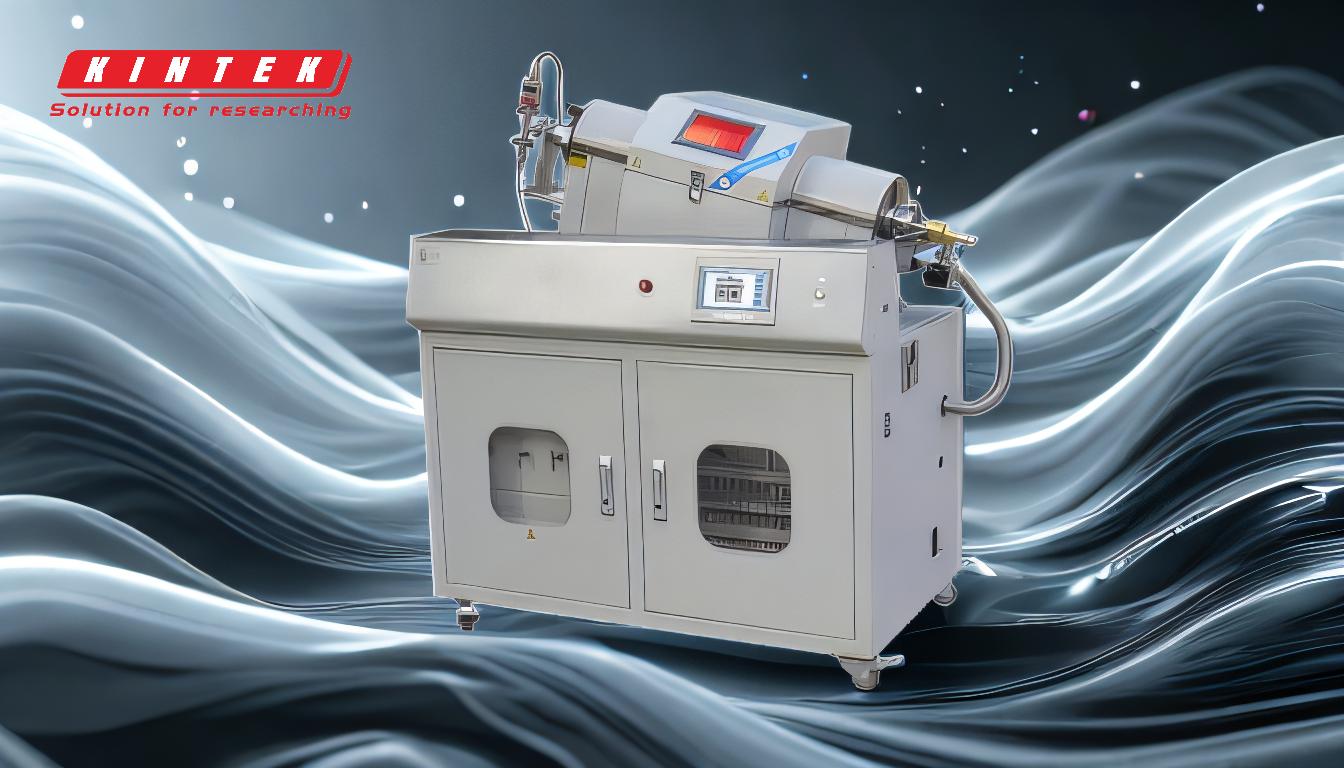
-
Hohe Kosten und komplizierte Ausrüstung:
- CVD erfordert hochentwickelte Anlagen, darunter Vakuumsysteme, Gaszufuhrsysteme und Hochtemperaturöfen.Diese Komponenten sind teuer in der Anschaffung und Wartung.
- Der Prozess umfasst oft mehrere Schritte und eine präzise Steuerung von Parametern wie Temperatur, Druck und Gasdurchsatz, was die Komplexität des Betriebs und die Kosten erhöht.
-
Filmqualität und Gleichmäßigkeit:
- Das Erreichen einer einheitlichen Schichtdicke und -zusammensetzung auf großen Substraten kann eine Herausforderung sein.Schwankungen der Temperatur und des Gasflusses können zu Defekten oder Unregelmäßigkeiten in der abgeschiedenen Schicht führen.
- Verunreinigungen in den Vorläufergasen oder Verschmutzungen in der Kammer können sich ebenfalls auf die Filmqualität auswirken und zu Mängeln oder schlechter Leistung des Endprodukts führen.
-
Anforderungen bei hohen Temperaturen:
- CVD arbeitet in der Regel bei hohen Temperaturen, was die Arten von Substraten, die verwendet werden können, einschränken kann.So sind beispielsweise Materialien mit niedrigem Schmelzpunkt oder solche, die sich bei hohen Temperaturen zersetzen, für CVD nicht geeignet.
- Hohe Temperaturen können auch zu thermischen Spannungen in den abgeschiedenen Schichten führen, die Risse oder Delaminationen verursachen können.
-
Toxische und gefährliche Gase:
- Bei vielen CVD-Verfahren werden giftige, entflammbare oder ätzende Gase wie Silan, Ammoniak oder Wasserstoff verwendet.Der Umgang mit diesen Gasen erfordert strenge Sicherheitsprotokolle und spezielle Ausrüstung, um Unfälle zu vermeiden.
- Die Freisetzung dieser Gase in die Umwelt kann erhebliche Umwelt- und Gesundheitsrisiken mit sich bringen, so dass wirksame Systeme zur Abfallentsorgung und Emissionskontrolle erforderlich sind.
-
Langsame Ablagerungsraten:
- CVD kann im Vergleich zu anderen Dünnschichtabscheidungsverfahren relativ langsame Abscheidungsraten aufweisen.Dies kann ein Nachteil sein, wenn ein hoher Durchsatz erforderlich ist, wie z. B. bei der Großserienfertigung.
- Die langsame Abscheidungsrate kann auch die Gesamtprozesszeit erhöhen, was zu höheren Produktionskosten führt.
-
Begrenzte Skalierbarkeit:
- Die Skalierung von CVD-Prozessen für großflächige Substrate oder die Produktion großer Mengen kann eine Herausforderung sein.Die Aufrechterhaltung einheitlicher Bedingungen auf größeren Flächen wird zunehmend schwieriger, was zu Schwankungen in den Schichteigenschaften führen kann.
- Auch die Komplexität und die Kosten für die Vergrößerung von CVD-Anlagen können für manche Anwendungen unerschwinglich sein.
-
Alternative Techniken:
- Angesichts der Grenzen von CVD sind alternative Techniken wie Kurzweg-Vakuumdestillation werden manchmal für bestimmte Anwendungen in Betracht gezogen.Die Kurzweg-Vakuumdestillation wird beispielsweise zur Abtrennung wärmeempfindlicher Verbindungen bei niedrigeren Temperaturen eingesetzt, wodurch das Risiko des thermischen Abbaus verringert wird.
- Techniken wie die Atomlagenabscheidung (ALD) oder die physikalische Gasphasenabscheidung (PVD) können je nach den spezifischen Anforderungen der Anwendung ebenfalls eingesetzt werden.
Zusammenfassend lässt sich sagen, dass die CVD zwar ein leistungsfähiges Werkzeug für die Dünnschichtabscheidung ist, aber auch erhebliche Herausforderungen mit sich bringt, die sorgfältig gemeistert werden müssen.Hohe Kosten, komplexe Anlagen und Probleme mit der Qualität und Gleichmäßigkeit der Schichten sind einige der Hauptprobleme.Außerdem birgt die Verwendung von giftigen Gasen und hohen Temperaturen Sicherheits- und Umweltrisiken.Alternative Techniken wie Kurzweg-Vakuumdestillation kann in bestimmten Szenarien Vorteile bieten, insbesondere bei hitzeempfindlichen Materialien.
Zusammenfassende Tabelle:
Herausforderung | Beschreibung |
---|---|
Hohe Kosten und komplizierte Ausrüstung | Teure Geräte und eine genaue Kontrolle der Parameter erhöhen die Betriebskosten. |
Filmqualität und Gleichmäßigkeit | Schwankungen der Temperatur und des Gasflusses können zu Defekten oder Inkonsistenzen führen. |
Anforderungen bei hohen Temperaturen | Schränkt die Substratoptionen ein und kann zu thermischen Spannungen in Filmen führen. |
Giftige und gefährliche Gase | Erfordert strenge Sicherheitsprotokolle und Emissionskontrollsysteme. |
Langsame Abscheidungsraten | Ein geringer Durchsatz kann die Produktionszeit und -kosten erhöhen. |
Begrenzte Skalierbarkeit | Es ist schwierig, einheitliche Bedingungen für eine groß angelegte Produktion aufrechtzuerhalten. |
Alternative Techniken | Verfahren wie ALD oder PVD können für bestimmte Anwendungen besser geeignet sein. |
Kämpfen Sie mit CVD-Herausforderungen? Kontaktieren Sie noch heute unsere Experten um bessere Lösungen für Ihre Anforderungen bei der Dünnschichtabscheidung zu finden!