CVD (Chemical Vapor Deposition) und PVD (Physical Vapor Deposition) sind zwei weit verbreitete Verfahren zur Abscheidung von Dünnschichten mit jeweils unterschiedlichen Verfahren, Eigenschaften und Anwendungen.Der Hauptunterschied liegt in ihren Abscheidungsmechanismen:Bei der CVD finden chemische Reaktionen zwischen gasförmigen Ausgangsstoffen und dem Substrat statt, die zu einer festen Beschichtung führen, während bei der PVD physikalische Verfahren wie Verdampfung oder Sputtern zum Einsatz kommen, um das Material ohne chemische Wechselwirkung direkt auf das Substrat aufzubringen.CVD arbeitet bei höheren Temperaturen und erzeugt dichtere, gleichmäßigere Beschichtungen, während PVD bei niedrigeren Temperaturen arbeitet und schnellere Abscheidungsraten mit einer breiteren Palette von Materialien bietet.Beide Verfahren haben einzigartige Vorteile und Einschränkungen, die sie für unterschiedliche industrielle und wissenschaftliche Anwendungen geeignet machen.
Die wichtigsten Punkte werden erklärt:
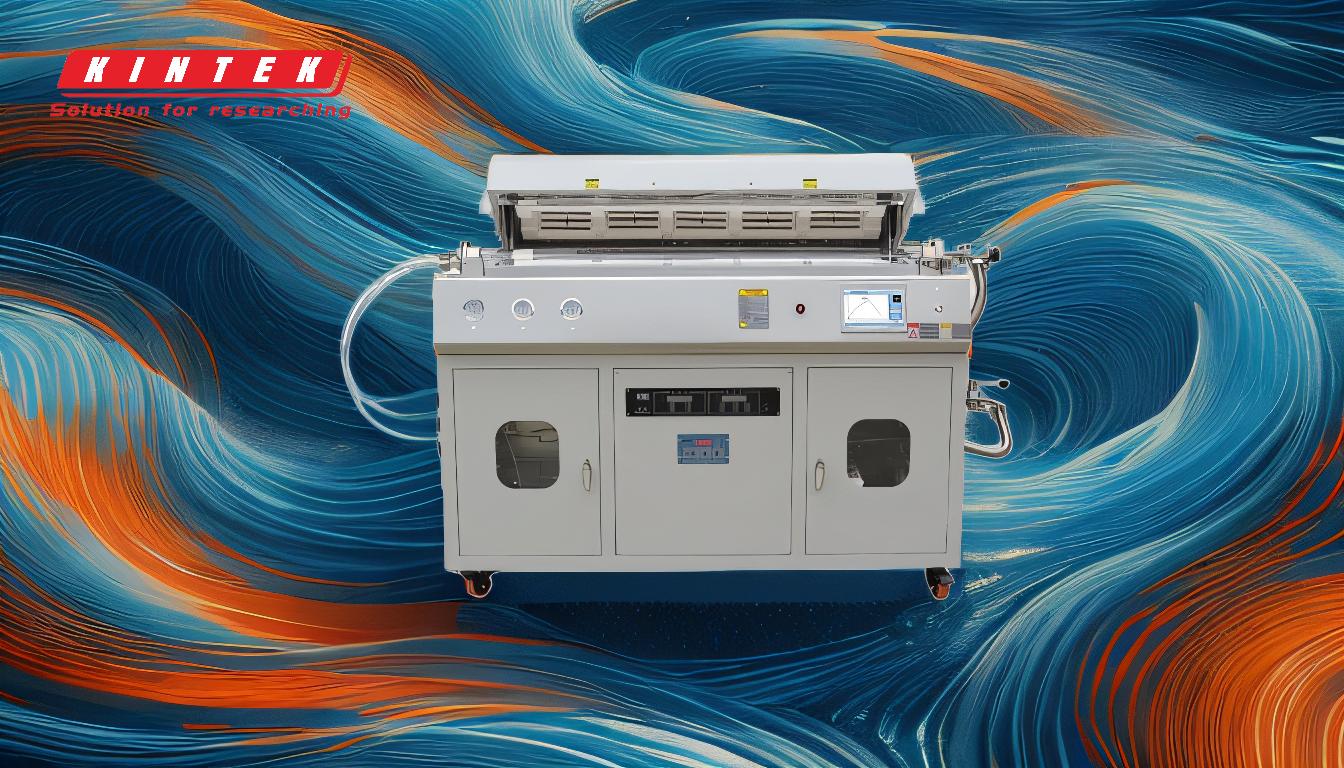
-
Mechanismus der Ablagerung:
- CVD:Es handelt sich um chemische Reaktionen zwischen gasförmigen Vorläufern und dem Substrat.Die gasförmigen Moleküle reagieren auf der Substratoberfläche und bilden eine feste Beschichtung.Dieses Verfahren ist multidirektional und ermöglicht eine gleichmäßige Beschichtung auch bei komplexen Geometrien.
- PVD:Physikalische Verfahren wie Verdampfung oder Sputtern zur Materialabscheidung.Das Material wird von einem festen Target verdampft und kondensiert dann auf dem Substrat.Es handelt sich dabei um ein Sichtlinienverfahren, was bedeutet, dass es für die gleichmäßige Beschichtung komplexer Formen weniger effektiv ist.
-
Anforderungen an die Temperatur:
- CVD:Wird in der Regel bei höheren Temperaturen von 450°C bis 1050°C betrieben.Diese hohe Temperatur ist notwendig, um die chemischen Reaktionen zu erleichtern, die die Beschichtung bilden.
- PVD:Arbeitet bei niedrigeren Temperaturen, normalerweise zwischen 250°C und 450°C.Dadurch ist PVD besser für temperaturempfindliche Substrate geeignet.
-
Beschichtungsmaterialien:
- CVD:Hauptsächlich für die Abscheidung von Keramiken und Polymeren verwendet.Das Verfahren eignet sich gut für die Herstellung hochreiner, dichter und gleichmäßiger Schichten.
- PVD:Es kann ein breiteres Spektrum an Materialien abgeschieden werden, darunter Metalle, Legierungen und Keramiken.Diese Vielseitigkeit macht PVD in verschiedenen Branchen einsetzbar, von der Elektronik bis zu dekorativen Beschichtungen.
-
Merkmale der Beschichtung:
- CVD:Erzeugt dichte, gleichmäßige und glatte Beschichtungen.Die chemischen Reaktionen sorgen für eine starke Haftung und hochwertige Schichten, aber das Verfahren ist langsamer.
- PVD:Im Vergleich zur CVD-Beschichtung ergeben sich weniger dichte und weniger gleichmäßige Schichten.PVD-Beschichtungen lassen sich jedoch schneller auftragen und können für bestimmte Anwendungen kostengünstiger sein.
-
Anwendungen:
- CVD:Weit verbreitet in Branchen, die Hochleistungsbeschichtungen benötigen, wie z. B. die Halbleiterherstellung, wo präzise und gleichmäßige Schichten entscheidend sind.Es wird auch für die Herstellung von Schutzschichten auf Metallen und anderen Materialien verwendet.
- PVD:Wird häufig bei Anwendungen eingesetzt, die dekorative Oberflächen, verschleißfeste Beschichtungen und dünne Filme für die Elektronik erfordern.Seine Fähigkeit, eine breite Palette von Materialien abzuscheiden, macht es vielseitig für verschiedene industrielle Anwendungen einsetzbar.
-
Prozess Umwelt:
- CVD:Wird in der Regel in einer kontrollierten Atmosphäre durchgeführt, in der gasförmige Vorläufer eingeleitet werden und auf der Substratoberfläche reagieren.
- PVD:Wird in einer Vakuumumgebung durchgeführt, um die Verdampfung und Abscheidung des Beschichtungsmaterials zu erleichtern.
-
Vorteile und Beschränkungen:
- CVD:Zu den Vorteilen gehören die hervorragende Gleichmäßigkeit der Beschichtung, die hohe Reinheit und die starke Adhäsion.Zu den Einschränkungen gehören höhere Betriebstemperaturen und langsamere Abscheidungsraten.
- PVD:Zu den Vorteilen gehören niedrigere Betriebstemperaturen, schnellere Abscheidungsraten und die Möglichkeit, eine breite Palette von Materialien zu beschichten.Zu den Einschränkungen gehören weniger gleichmäßige Beschichtungen und Probleme bei der Beschichtung komplexer Geometrien.
Zusammenfassend lässt sich sagen, dass die Wahl zwischen CVD und PVD von den spezifischen Anforderungen der Anwendung abhängt, einschließlich der gewünschten Beschichtungseigenschaften, des Substratmaterials und der betrieblichen Zwänge.Beide Verfahren bieten einzigartige Vorteile und sind in der modernen Fertigung und Materialwissenschaft unverzichtbar.
Zusammenfassende Tabelle:
Aspekt | CVD (Chemische Gasphasenabscheidung) | PVD (Physikalische Gasphasenabscheidung) |
---|---|---|
Mechanismus der Abscheidung | Chemische Reaktionen zwischen gasförmigen Vorläufern und Substrat.Multidirektionale Beschichtung. | Physikalische Verfahren wie Aufdampfen oder Sputtern.Sichtlinienbeschichtung. |
Temperaturbereich | 450°C bis 1050°C | 250°C bis 450°C |
Beschichtungsmaterialien | Hauptsächlich Keramiken und Polymere.Hochreine, dichte und gleichmäßige Beschichtungen. | Metalle, Legierungen und Keramiken.Vielseitig und für eine breite Palette von Materialien geeignet. |
Merkmale der Beschichtung | Dichte, gleichmäßige und glatte Beschichtungen.Starke Adhäsion, aber langsamere Abscheidung. | Weniger dichte und weniger gleichmäßige Beschichtungen.Schnellere Abscheidung und kostengünstiger für bestimmte Anwendungen. |
Anwendungen | Halbleiterherstellung, Schutzbeschichtungen. | Dekorative Beschichtungen, verschleißfeste Beschichtungen und dünne Schichten für die Elektronik. |
Prozessumgebung | Kontrollierte Atmosphäre mit gasförmigen Ausgangsstoffen. | Vakuumumgebung für die Verdampfung und Abscheidung. |
Vorteile | Ausgezeichnete Gleichmäßigkeit, hohe Reinheit und starke Haftung. | Niedrigere Temperaturen, schnellere Abscheidung und Vielseitigkeit des Materials. |
Beschränkungen | Höhere Betriebstemperaturen und langsamere Abscheidungsraten. | Weniger gleichmäßige Beschichtungen und Herausforderungen bei komplexen Geometrien. |
Benötigen Sie Hilfe bei der Entscheidung zwischen CVD und PVD für Ihre Anwendung? Kontaktieren Sie noch heute unsere Experten für eine persönliche Beratung!