Ionen- und Gasnitrieren sind beides Verfahren zur Oberflächenhärtung, die zur Verbesserung der Verschleißfestigkeit, Ermüdungsfestigkeit und Härte von Metallteilen eingesetzt werden.Sie unterscheiden sich jedoch erheblich in Bezug auf Verfahrensmechanik, Effizienz, Kosten und Qualität der Nitrierschicht.Das Ionennitrieren, auch bekannt als Glühionennitrieren, ist ein fortschrittlicheres und moderneres Verfahren, das im Vergleich zum Gasnitrieren schnellere Bearbeitungszeiten, niedrigere Betriebskosten und eine bessere Nitrierschichtqualität bietet.Es nutzt ein elektrisches Hochdruckfeld, um die Stickstoffdiffusion zu beschleunigen, was zu einer kontrollierten und hochwertigen Oberflächenschicht führt.Das Gasnitrierverfahren hingegen beruht auf einer chemischen Reaktion zwischen Ammoniakgas und der Metalloberfläche, die langsamer und weniger effizient ist.Das Ionen-Nitrierverfahren erfordert zwar eine höhere Anfangsinvestition, ist aber aufgrund seiner betrieblichen Vorteile und der besseren Ergebnisse für viele Anwendungen die erste Wahl.
Die wichtigsten Punkte erklärt:
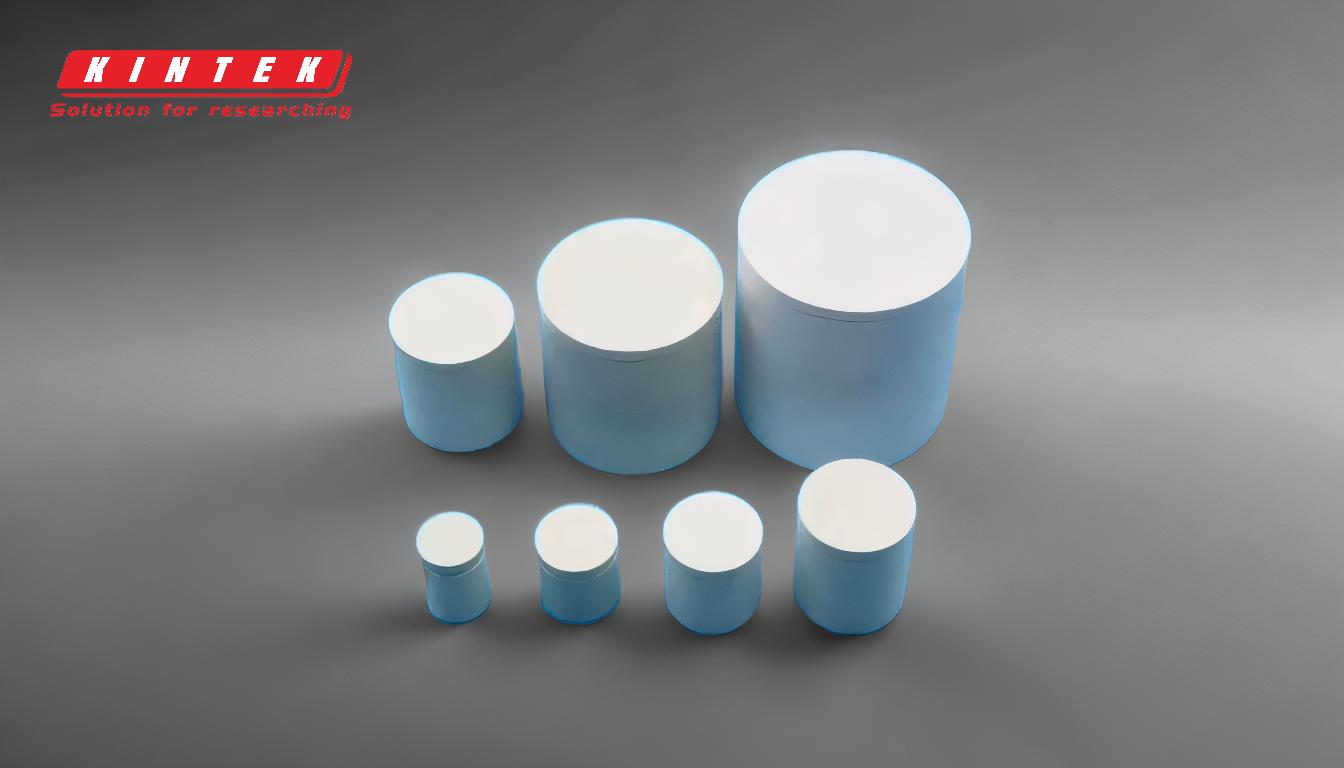
-
Prozessmechanik:
- Ionen-Nitrieren:Bei diesem Verfahren werden die Metallteile in eine Vakuumkammer gebracht, wo ein elektrisches Hochspannungsfeld ein Plasma aus ionisiertem Stickstoffgas erzeugt.Die Stickstoffionen werden auf die Metalloberfläche beschleunigt, wo sie in das Material diffundieren und eine harte Nitridschicht bilden.Mit diesem Verfahren lassen sich der Nitrierprozess und die Eigenschaften der entstehenden Schicht genau steuern.
- Gasnitrieren:Bei diesem Verfahren werden die Metallteile in einer Atmosphäre aus Ammoniakgas erhitzt.Das Ammoniak zersetzt sich an der Metalloberfläche und setzt Stickstoffatome frei, die in das Material diffundieren.Dieses Verfahren ist im Vergleich zum Ionennitrieren langsamer und weniger kontrollierbar.
-
Bearbeitungszeit:
- Ionen-Nitrieren:Das Nitrierverfahren ist wesentlich schneller und dauert in der Regel 3-10 Stunden.Dies ist auf die schnelle Diffusion der Stickstoffatome unter dem Einfluss des elektrischen Hochdruckfeldes zurückzuführen.
- Gasnitrieren:Das Verfahren ist langsamer und erfordert oft längere Zeiten, um eine vergleichbare Nitrierschicht zu erhalten.
-
Betriebskosten:
- Ionen-Nitrieren:Die Betriebskosten betragen etwa 60 % der Kosten für das Gasnitrieren.Dies ist auf die schnelleren Bearbeitungszeiten und den geringeren Energieverbrauch zurückzuführen.
- Gasnitrieren:Höhere Betriebskosten sind mit längeren Bearbeitungszeiten und höherem Energieverbrauch verbunden.
-
Qualität der Nitrierschicht:
- Ionen-Nitrieren:Erzeugt eine nitrierte Schicht mit hoher Zähigkeit, Ermüdungsfestigkeit und Verschleißfestigkeit.Die spröde Weißzementphase (Fe2N) wird innerhalb von 0-0,2 mm kontrolliert, wodurch das Schleifen überflüssig wird.Die Oberflächenhärte kann HV900 (HRC64) erreichen, und die Nitrierschichttiefe kann zwischen 0,09-0,87 mm gesteuert werden.
- Gasnitrieren:Es kann zwar eine harte Oberflächenschicht erzeugt werden, aber die Qualität ist im Allgemeinen schlechter als beim Ionennitrieren.Der Prozess ist weniger kontrollierbar, was zu Schwankungen in der Schichtdicke und den Eigenschaften führt.
-
Teil Verformung:
- Ionen-Nitrieren:Verringert die Verformung des Teils durch schnelles Erhitzen und Abkühlen der Oberfläche, wodurch der Rest des Teils auf einer niedrigen Temperatur (100 °C) gehalten wird.Dadurch werden thermische Spannungen und Verformungen minimiert.
- Gasnitrieren:Höheres Risiko der Verformung von Teilen aufgrund langsamerer Erwärmungs- und Abkühlungsraten, die zu größeren thermischen Spannungen und Verformungen führen können.
-
Erstinvestition:
- Ionen-Nitrieren:Erfordert eine höhere Anfangsinvestition.Ein Ionen-Nitrierofen mit einem Fassungsvermögen von 400 kg kostet zum Beispiel rund 900.000 Yuan.
- Gasnitrieren:Geringere Anfangsinvestitionen, wobei ein Ofen mit ähnlicher Kapazität etwa 40.000 Yuan kostet.
-
Umweltfreundlichkeit und Energieeffizienz:
- Ionen-Nitrieren:Umweltfreundlicher und energieeffizienter durch kürzere Bearbeitungszeiten und geringeren Energieverbrauch.
- Gasnitrieren:Sie sind weniger energieeffizient und können mehr Abgase produzieren, wodurch sie weniger umweltfreundlich sind.
Zusammenfassend lässt sich sagen, dass das Ionen-Nitrierverfahren zwar eine höhere Anfangsinvestition erfordert, aber aufgrund seiner Vorteile in Bezug auf die Verarbeitungsgeschwindigkeit, die Betriebskosten und die Qualität der Nitrierschicht für viele Anwendungen die bessere Wahl darstellt.Das Gasnitrieren ist zwar anfangs günstiger, aber langsamer, weniger effizient und erzeugt eine Nitrierschicht von geringerer Qualität.
Zusammenfassende Tabelle:
Aspekt | Ionen-Nitrierung | Gasnitrieren |
---|---|---|
Prozess-Mechanik | Nutzt ein elektrisches Hochspannungsfeld zur Erzeugung eines Plasmas für die Stickstoffdiffusion. | Die Stickstoffdiffusion beruht auf der Zersetzung von Ammoniakgas. |
Verarbeitungszeit | 3-10 Stunden (schneller aufgrund der schnellen Diffusion). | Langsamer, erfordert oft längere Zeiten für vergleichbare Ergebnisse. |
Betriebskosten | ~60% der Kosten des Gasnitrierens (geringerer Energieverbrauch, schnellere Verarbeitung). | Höher aufgrund längerer Bearbeitungszeiten und höherem Energieaufwand. |
Qualität der Nitrierschicht | Hohe Zähigkeit, Ermüdungsfestigkeit und Verschleißfestigkeit.Kontrollierte Schichtdicke. | Geringere Qualität mit weniger Kontrolle über Schichtdicke und Eigenschaften. |
Verformung der Teile | Geringfügig aufgrund der schnellen Oberflächenerwärmung und -abkühlung. | Höheres Risiko aufgrund langsamerer Erwärmung/Abkühlung. |
Erstinvestition | Höher (z. B. 900.000 Yuan für einen 400-kg-Ofen). | Niedriger (z.B. 40.000 Yuan für einen Ofen mit ähnlicher Kapazität). |
Umweltverträglichkeit | Energieeffizienter und umweltfreundlicher. | Weniger effizient, erzeugt mehr Abgase. |
Möchten Sie die Leistung Ihrer Metallkomponenten verbessern? Kontaktieren Sie uns noch heute um mehr über das Ionennitrieren zu erfahren!