Die Füllphase beim Spritzgießen ist die Anfangsphase des Einspritzzyklus, in der geschmolzenes Material in den Formhohlraum eingespritzt wird.Diese Phase beginnt mit dem Schließen des Werkzeugs und endet, wenn die Kavität zu etwa 95 % gefüllt ist.Die Füllphase ist von entscheidender Bedeutung, da sie die anfängliche Verteilung des Materials in der Form bestimmt, was sich auf die Qualität und Konsistenz des Endprodukts auswirkt.Die ordnungsgemäße Steuerung von Parametern wie Einspritzgeschwindigkeit, Druck und Materialtemperatur während dieser Phase ist entscheidend, um eine vollständige Füllung zu gewährleisten, Fehler zu vermeiden und die gewünschten Produkteigenschaften zu erzielen.
Die wichtigsten Punkte werden erklärt:
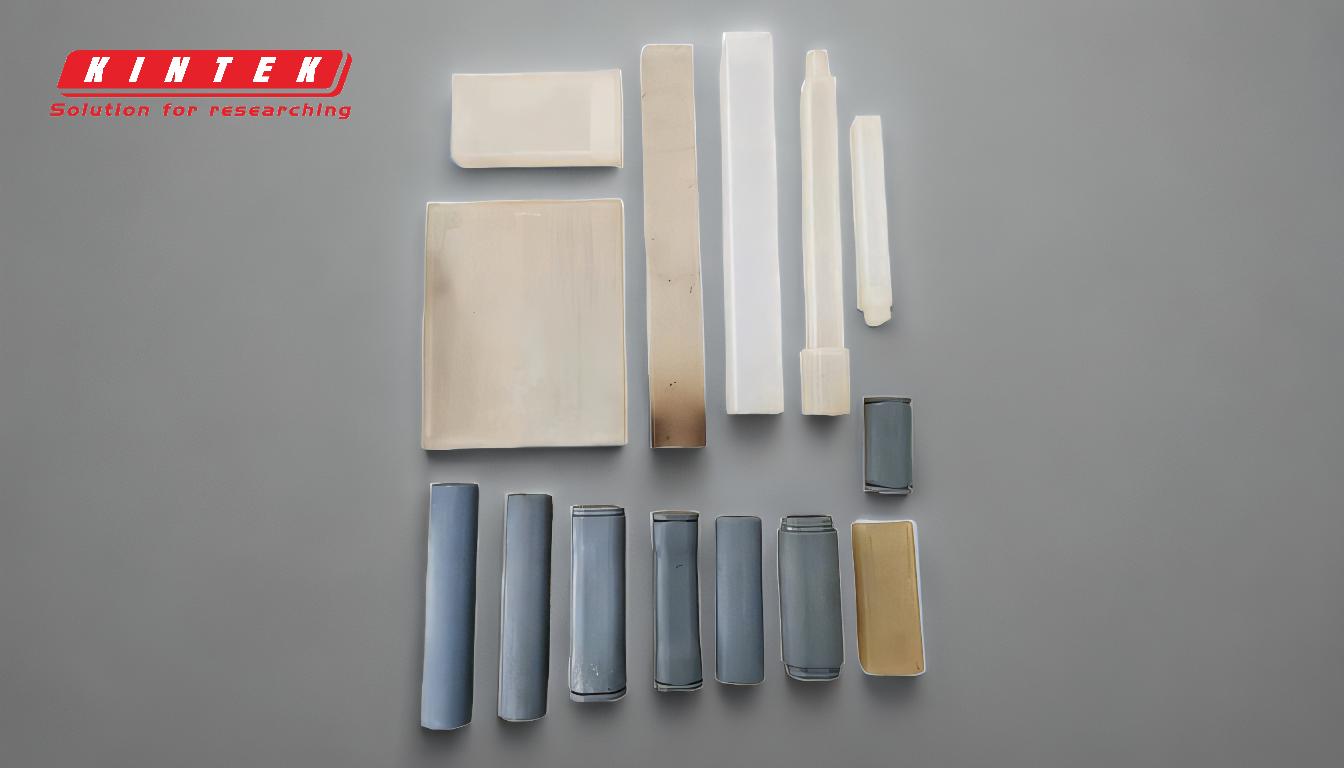
-
Definition und Zweck der Befüllungsphase:
- Die Füllphase ist der erste Schritt im Spritzgießverfahren, bei dem geschmolzenes Material in den Formhohlraum eingespritzt wird.
- Ihr Hauptzweck besteht darin, das Material gleichmäßig in der Form zu verteilen, um die Grundform des Produkts zu bilden.
- Diese Phase bildet die Grundlage für die nachfolgenden Phasen der Verpackung und Kühlung, die die endgültigen Abmessungen und Eigenschaften des Produkts festlegen.
-
Prozess-Ablauf:
- Die Füllphase beginnt mit dem sicheren Schließen der Form, um einen abgedichteten Hohlraum zu schaffen.
- Das geschmolzene Material wird dann unter kontrolliertem Druck und mit kontrollierter Geschwindigkeit in den Hohlraum eingespritzt.
- Die Phase endet, wenn die Kavität zu etwa 95 % gefüllt ist, wobei ein kleiner Teil für die Verpackungsphase verbleibt.
-
Wichtigste Parameter:
- Einspritzgeschwindigkeit:Bestimmt, wie schnell das Material in die Form fließt.Zu schnelles Fließen kann Defekte wie Lufteinschlüsse oder Brandflecken verursachen, während zu langsames Fließen zu einer unvollständigen Füllung führen kann.
- Einspritzdruck:Stellt sicher, dass das Material in alle Bereiche des Formhohlraums gepresst wird.Ein angemessener Druck verhindert kurze Schüsse oder ungleichmäßige Füllung.
- Material Temperatur:Beeinflusst die Viskosität und Fließfähigkeit des geschmolzenen Materials.Eine optimale Temperatur gewährleistet eine gleichmäßige Füllung und verringert das Risiko von Fehlern.
-
Die Bedeutung der Formgestaltung:
- Die Konstruktion der Form, einschließlich der Position des Anschnitts, des Angusssystems und der Entlüftung, spielt eine entscheidende Rolle in der Füllphase.
- Die richtige Platzierung des Anschnitts sorgt für eine gleichmäßige Materialverteilung, während eine angemessene Entlüftung Lufteinschlüsse verhindert und eine vollständige Befüllung gewährleistet.
-
Herausforderungen und Defekte:
- Zu den häufigen Problemen während der Füllphase gehören kurze Schüsse (unvollständige Füllung), Lufteinschlüsse, Bindenähte und Brandflecken.
- Diese Defekte können durch unsachgemäße Parametereinstellungen, schlechtes Formdesign oder Materialunregelmäßigkeiten entstehen.
-
Übergang zur Verpackungsphase:
- Die Abfüllphase geht nahtlos in die Verpackungsphase über, in der zusätzliches Material eingespritzt wird, um die Schrumpfung beim Abkühlen des Materials auszugleichen.
- Dadurch wird sichergestellt, dass das Endprodukt die richtigen Abmessungen und die richtige Dichte aufweist.
Durch das Verständnis und die Optimierung der Füllphase können Hersteller die Produktqualität verbessern, Fehler reduzieren und die Effizienz des Spritzgießprozesses steigern.
Zusammenfassende Tabelle:
Hauptaspekt | Einzelheiten |
---|---|
Zweck | Verteilt das geschmolzene Material gleichmäßig, um die Grundform des Produkts zu formen. |
Prozess-Ablauf | Beginnt mit dem Schließen der Form und endet, wenn die Kavität zu 95 % gefüllt ist. |
Wichtige Parameter | Einspritzgeschwindigkeit, Druck und Materialtemperatur. |
Bedeutung der Werkzeugkonstruktion | Anschnittposition, Angusssystem und Entlüftung gewährleisten eine vollständige Füllung. |
Häufige Defekte | Kurze Schüsse, Lufteinschlüsse, Schweißnähte und Brandflecken. |
Übergang zum Verpacken | Stellt sicher, dass die endgültigen Produktabmessungen und die Dichte erreicht werden. |
Sind Sie bereit, Ihren Spritzgießprozess zu optimieren? Kontaktieren Sie uns noch heute für fachkundige Beratung!