PVD-Beschichtungen (Physical Vapor Deposition) sind für ihre hohe Härte bekannt, die je nach Art der Beschichtung, des Trägermaterials und des verwendeten PVD-Verfahrens zwischen 1500 HV (Vickers-Härte) und 4500 HV liegt.Zum Vergleich: Kohlenstoffstähle haben eine Härte von etwa 250 HV, während nitrierte oder nickel-/verchromte Stähle zwischen 600 HV und 1000 HV liegen.PVD-Beschichtungen wie TiN (Titannitrid) werden besonders wegen ihrer Fähigkeit geschätzt, die Verschleißfestigkeit, Korrosionsbeständigkeit und Haltbarkeit zu verbessern.In einigen Fällen können spezielle Beschichtungen wie DLC (Diamond-Like Carbon) Härtewerte von bis zu 9000 HV erreichen.Die Härte von PVD-Beschichtungen ist ein entscheidender Faktor für ihre Leistung und macht sie für anspruchsvolle Anwendungen in Branchen wie der Automobilindustrie, der Luft- und Raumfahrt und der Medizintechnik geeignet.
Die wichtigsten Punkte erklärt:
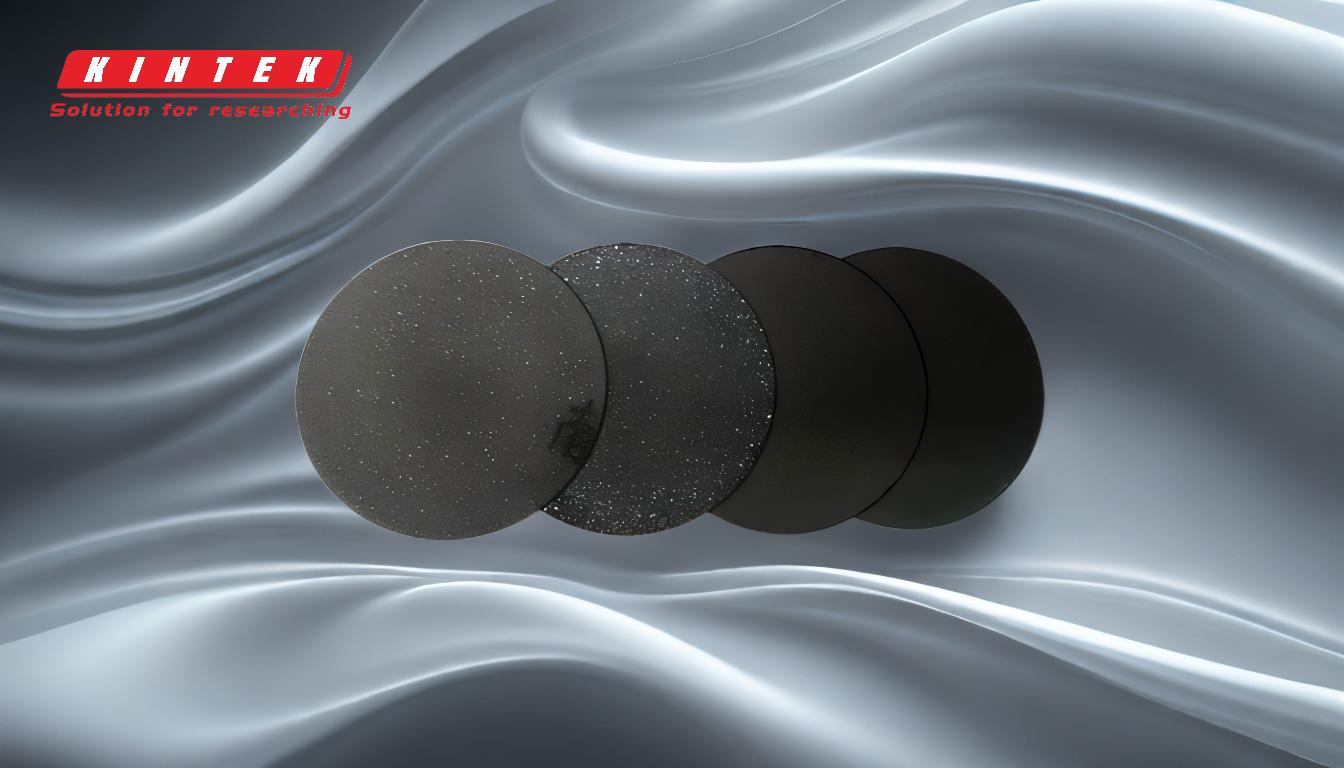
-
Härtebereich von PVD-Beschichtungen:
- PVD-Beschichtungen haben in der Regel einen Härtebereich von 1500 HV bis 4500 HV je nach Beschichtungsmaterial und Verfahren.
- Als Referenz, 900 HV entspricht 67 HRC (Rockwell C) was deutlich härter ist als viele gängige Werkstoffe wie Kohlenstoffstahl (250 HV) oder Nitrierstähle (600-1000 HV).
- Spezialisierte Beschichtungen, wie DLC (Diamond-Like Carbon) können noch höhere Härtewerte erreicht werden, bis zu 9000 HV .
-
Faktoren, die die Härte beeinflussen:
-
Die Härte von PVD-Beschichtungen hängt von mehreren Faktoren ab:
- Beschichtungsmaterial:Verschiedene Materialien (z. B. TiN, TiCN, CrN, DLC) haben unterschiedliche Härtegrade.
- Material des Substrats:Der zugrunde liegende Werkstoff kann die Eigenschaften der Beschichtung beeinflussen.Beispielsweise verbessern TiN-Beschichtungen auf einer Ti-6Al-4V-Legierung die Ermüdungsgrenzen und die Dauerhaftigkeit.
- PVD-Verfahren:Das spezifische PVD-Verfahren (z. B. Sputtern, Bogenverdampfung) und die Fähigkeiten des Bedieners können die Härte der Beschichtung beeinflussen.
- Schichtdicke:PVD-Beschichtungen sind sehr dünn (0,5-5 Mikrometer), aber ihre Härte ist für die Leistung optimiert.
-
Die Härte von PVD-Beschichtungen hängt von mehreren Faktoren ab:
-
Vergleich mit anderen Materialien:
- Kohlenstoffstähle:Sie haben in der Regel eine Härte von etwa 250 HV (25 HRC) .
- Nitrierte oder vernickelte/verchromte Stähle:Bereich zwischen 600 HV und 1000 HV .
- PVD-Beschichtungen:Unter 1500-4500 HV PVD-Beschichtungen sind deutlich härter und eignen sich daher ideal für Anwendungen, die eine hohe Verschleißfestigkeit und Haltbarkeit erfordern.
-
Anwendungen und Vorteile:
- PVD-Beschichtungen werden häufig in Branchen wie der Automobilindustrie, Luft- und Raumfahrt und Medizintechnik aufgrund ihrer hohen Härte, Verschleißfestigkeit und Korrosionsbeständigkeit.
- Sie bieten außerdem geringe Reibung und verbessertes ästhetisches Aussehen wodurch sie sowohl für funktionale als auch für dekorative Zwecke geeignet sind.
-
Härte und Abriebfestigkeit:
- Eine hohe Härte korreliert im Allgemeinen mit verbesserter Verschleißfestigkeit Es besteht kein direkter Zusammenhang zwischen diesen beiden Faktoren.Härtewerte oberhalb der optimalen Schwelle können auf Entkohlung was die Leistung beeinträchtigen kann.
- PVD-Beschichtungen schaffen ein Gleichgewicht zwischen Härte und anderen Eigenschaften wie Zähigkeit und Haftung um eine langfristige Haltbarkeit zu gewährleisten.
-
Spezialisierte Beschichtungen:
- DLC-Beschichtungen:Diese gehören zu den härtesten PVD-Beschichtungen, mit Härtewerten bis zu 9000 HV .Sie werden besonders geschätzt wegen ihrer geringe Reibung und hervorragende Verschleißfestigkeit .
- TiN-Beschichtungen:Häufig verwendet für ihr goldähnliches Aussehen und hoher Härte sind sie ideal für Schneidwerkzeuge, Formen und dekorative Anwendungen.
-
Messung der Härte:
- Die Härte wird in der Regel gemessen mit dem Vickers-Härte (HV) Skala, die für dünne Beschichtungen geeignet ist.Zum Vergleich, Rockwell C (HRC) wird ebenfalls verwendet, wobei 900 HV einem Wert von 67 HRC entspricht.
-
Optimale Härte und Korrosionsbeständigkeit:
- PVD-Beschichtungen erreichen einen optimalen Härtegrad der ihre Korrosionsbeständigkeit Korrosionsbeständigkeit .Eine zu große Härte kann zur Bildung von Hartphasen führen, die die Leistung beeinträchtigen können.
Zusammenfassend lässt sich sagen, dass die Härte von PVD-Beschichtungen eine Schlüsseleigenschaft ist, die sie äußerst langlebig und für anspruchsvolle Anwendungen geeignet macht.Ihre Härte reicht von 1500 HV bis 4500 HV, wobei spezielle Schichten wie DLC bis zu 9000 HV erreichen.Diese außergewöhnliche Härte, kombiniert mit Verschleißfestigkeit, Korrosionsbeständigkeit und geringer Reibung, macht PVD-Beschichtungen in verschiedenen Industriezweigen unschätzbar wertvoll.
Zusammenfassende Tabelle:
Aspekt | Einzelheiten |
---|---|
Härtebereich | 1500-4500 HV (bis zu 9000 HV für DLC-Beschichtungen) |
Vergleich der Materialien | Kohlenstoffstahl: 250 HV; Nitrierstähle: 600-1000 HV |
Wesentliche Vorteile | Hohe Verschleißfestigkeit, Korrosionsbeständigkeit, geringe Reibung und Langlebigkeit |
Anwendungen | Automobil, Luft- und Raumfahrt, Medizin und dekorative Anwendungen |
Spezialisierte Beschichtungen | TiN (Titannitrid), DLC (Diamantähnlicher Kohlenstoff) |
Messung | Vickers-Härte (HV); 900 HV = 67 HRC |
Erfahren Sie, wie PVD-Beschichtungen die Leistung Ihrer Materialien verbessern können. Kontaktieren Sie unsere Experten noch heute !