Ein Drehkalzinator, auch Drehrohrofen genannt, ist ein Gerät zur thermischen Verarbeitung von Materialien, das diese auf hohe Temperaturen erhitzt, um eine chemische Zersetzung oder physikalische Veränderungen zu erreichen.Er besteht aus einem langen, zylindrischen, leicht geneigten Mantel, der sich dreht, um eine gleichmäßige Erwärmung des Materials zu gewährleisten.Bei diesem Verfahren wird das Material in den Ofen gegeben, wo es hohen Temperaturen ausgesetzt wird, die von Brennern oder anderen Wärmequellen erzeugt werden.Während sich das Material durch den Ofen bewegt, wird es kalziniert, was zu einer chemischen Dissoziation (z. B. von Kalziumkarbonat in Kalziumoxid und Kohlendioxid) oder zur Entfernung von gebundener Feuchtigkeit führt.Der Drehrohrofen ist in Branchen wie der Zementherstellung, der Mineralienverarbeitung und der chemischen Industrie weit verbreitet, da er große Mengen verarbeiten, gleichmäßig erhitzen und eine präzise Temperaturregelung ermöglichen kann.
Die wichtigsten Punkte werden erklärt:
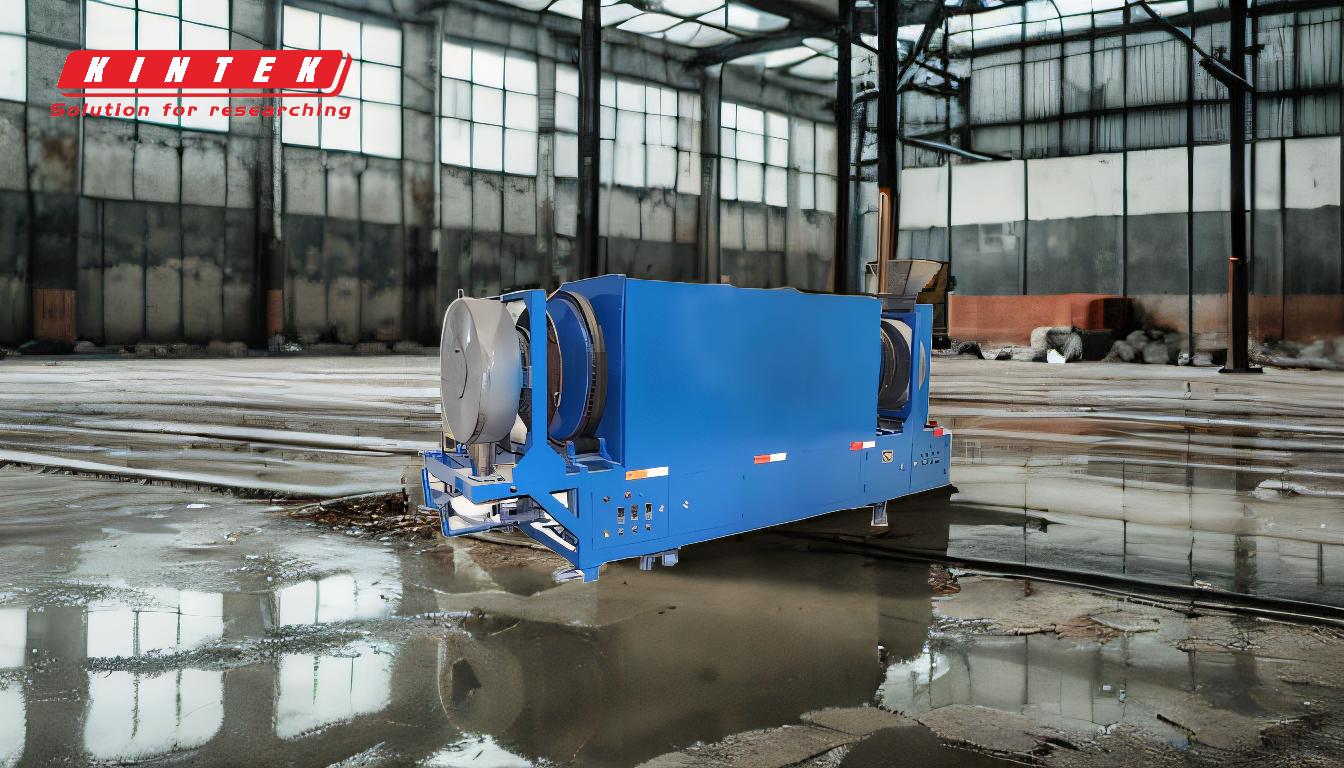
-
Zweck eines Drehrohrofens:
- Ein Rotationskalzinator dient dazu, Materialien auf hohe Temperaturen zu erhitzen, um eine chemische Dissoziation oder physikalische Veränderungen zu bewirken.
- Zu den üblichen Anwendungen gehören die Dissoziation von Kalziumkarbonat (CaCO₃) in Kalziumoxid (CaO) und Kohlendioxid (CO₂) oder die Entfernung von gebundener Feuchtigkeit aus Materialien wie Borax.
- Es ist besonders effektiv bei Materialien mit einer Partikelgröße von 60 mm oder weniger und gewährleistet eine gleichmäßige Erhitzung und eine gleichbleibende Produktqualität.
-
Arbeitsprinzip:
- Der Rotationskalzinator funktioniert durch die Drehung eines langen, zylindrischen Mantels, der leicht geneigt ist.Die Drehung sorgt dafür, dass sich das Material allmählich von der Zufuhrseite zur Abfuhrseite bewegt.
- Intern wird Wärme zugeführt, oft durch Brenner oder andere Wärmequellen, um die erforderlichen hohen Temperaturen zu erreichen.
- Das Material wird für eine bestimmte Dauer auf bestimmten Temperaturen gehalten, die durch chemische und thermische Analysen bestimmt werden, um eine vollständige Dissoziation oder Umwandlung zu gewährleisten.
-
Wichtigste Bestandteile:
- Muschel:Die äußere zylindrische Struktur des Ofens, in der Regel aus Stahl, in der sich das zu verarbeitende Material befindet.
- Feuerfeste Auskleidung:Eine hitzebeständige Auskleidung im Inneren der Schale, die sie vor hohen Temperaturen und chemischen Reaktionen schützt.
- Stützreifen und Rollen:Diese Komponenten tragen das Gewicht der rotierenden Schale und ermöglichen eine reibungslose Drehung.
- Antriebsrad:Ein motorisiertes System, das den Ofen mit einer kontrollierten Geschwindigkeit dreht.
- Interne Wärmetauscher:Vorrichtungen innerhalb des Ofens, die die Wärmeübertragung verbessern und eine gleichmäßige Temperaturverteilung gewährleisten.
-
Prozessablauf:
- Fütterung:Das Material wird am oberen Ende des Schrägmantels in den Drehkalzinator eingeführt.
- Heizung:Während sich der Ofen dreht, bewegt sich das Material nach unten und wird hohen Temperaturen ausgesetzt, die die gewünschten chemischen oder physikalischen Veränderungen bewirken.
- Entladung:Das aufbereitete Material verlässt den Ofen am unteren Ende, bereit für die weitere Verarbeitung oder Verwendung.
-
Vorteile von Drehrohrofenanlagen:
- Einheitliche Heizung:Die Rotation des Ofens sorgt für eine gleichmäßige Wärmeeinwirkung auf das Material und damit für eine gleichbleibende Produktqualität.
- Hoher Durchsatz:Rotationskalzinatoren können große Mengen an Material verarbeiten und eignen sich daher für den Einsatz im industriellen Maßstab.
- Präzise Temperaturregelung:Das System ermöglicht eine genaue Kontrolle der Temperatur und der Verweilzeit und gewährleistet so optimale Ergebnisse.
- Vielseitigkeit:Sie können eine breite Palette von Materialien verarbeiten, darunter Kalkstein, Dolomit, Magnesit und Borax.
-
Anwendungen:
- Zementherstellung:Rotationskalzinatoren werden zur Herstellung von Klinker, einem wichtigen Bestandteil von Zement, durch Kalzinieren von Kalkstein und anderen Rohstoffen eingesetzt.
- Mineralienaufbereitung:Sie werden eingesetzt, um Mineralien wie Kalkstein, Dolomit und Magnesit zu verarbeiten und sie in Oxide oder andere nützliche Verbindungen umzuwandeln.
- Chemische Herstellung:Rotationskalzinatoren werden bei der Herstellung von anorganischen Chemikalien wie Kalzium- und Magnesiumoxid eingesetzt.
- Feuchtigkeitsentzug:Sie werden auch eingesetzt, um Materialien wie Borax die gebundene Feuchtigkeit zu entziehen, damit sie für die Weiterverarbeitung geeignet sind.
-
Betriebliche Erwägungen:
- Temperatur-Profile:Die Temperatur und die Verweilzeit müssen je nach dem zu verarbeitenden Material und dem gewünschten Ergebnis sorgfältig kontrolliert werden.
- Energie-Effizienz:Eine gute Isolierung und Wärmerückgewinnungssysteme sind unerlässlich, um den Energieverbrauch und die Betriebskosten zu minimieren.
- Wartung:Regelmäßige Wartung der feuerfesten Auskleidung, der Stützreifen und des Antriebsgetriebes ist notwendig, um langfristige Zuverlässigkeit und Leistung zu gewährleisten.
Wenn ein Käufer oder Betreiber diese wichtigen Punkte versteht, kann er fundierte Entscheidungen über die Auswahl, den Betrieb und die Wartung eines Rotationskalzinators treffen und so eine optimale Leistung und Effizienz für seine spezifische Anwendung sicherstellen.
Zusammenfassende Tabelle:
Hauptaspekt | Einzelheiten |
---|---|
Zweck | Verursacht chemische Dissoziation oder physikalische Veränderungen in Materialien. |
Arbeitsprinzip | Rotiert einen zylindrischen Mantel, um eine gleichmäßige Erwärmung und einen gleichmäßigen Materialfluss zu gewährleisten. |
Wichtige Komponenten | Mantel, feuerfeste Auskleidung, Stützreifen, Antriebsgetriebe, interne Wärmetauscher. |
Vorteile | Gleichmäßige Erwärmung, hoher Durchsatz, präzise Temperaturregelung, Vielseitigkeit. |
Anwendungen | Zementherstellung, Mineralienverarbeitung, chemische Produktion, Feuchtigkeitsentzug. |
Betriebliche Erwägungen | Temperaturregelung, Energieeffizienz, regelmäßige Wartung. |
Entdecken Sie, wie ein Rotationskalzinator Ihre industriellen Prozesse optimieren kann. Kontaktieren Sie uns noch heute für eine fachkundige Beratung!