Die Partikelgröße spielt im Pyrolyseprozess eine entscheidende Rolle, da sie die Wärmeübertragung, die Reaktionsgeschwindigkeit und die Verteilung der Endprodukte (Gas, Flüssigkeit und Feststoffe) beeinflusst.Kleinere Partikel, in der Regel bis zu 2 mm, ermöglichen eine schnellere und gleichmäßigere Wärmeübertragung, was zu einer schnelleren thermischen Zersetzung und einer höheren Ausbeute an Pyrolyseöl führt.Größere Partikel hingegen können zu einer ungleichmäßigen Erwärmung, langsameren Reaktionsgeschwindigkeiten und einem größeren Anteil an fester Verkohlung führen.Die Partikelgröße wirkt sich auch auf die Verweilzeit und die Effizienz des Pyrolyseprozesses aus und ist damit ein Schlüsselfaktor für die Optimierung der Umwandlung von Biomasse oder Abfall in wertvolle Produkte.
Schlüsselpunkte erklärt:
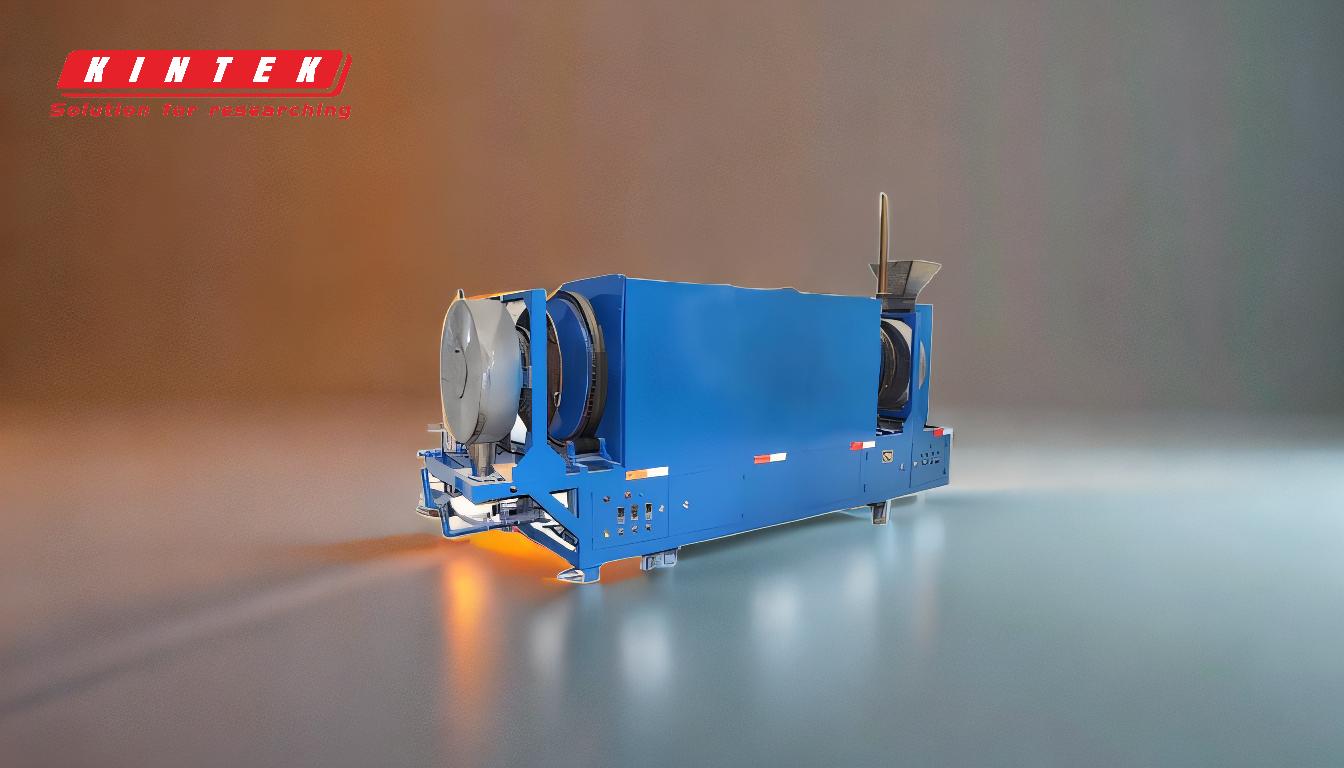
-
Wirkungsgrad der Wärmeübertragung:
- Kleinere Partikel (bis zu 2 mm) bieten eine größere Oberfläche im Verhältnis zu ihrem Volumen, was eine schnelle und gleichmäßige Wärmeübertragung im gesamten Material ermöglicht.
- Dadurch wird sichergestellt, dass das gesamte Partikel die erforderliche Pyrolysetemperatur schnell erreicht, wodurch das Risiko einer unvollständigen Zersetzung minimiert wird.
- Bei größeren Partikeln kann die Wärme langsamer eindringen, was zu einer ungleichmäßigen Erwärmung führt und möglicherweise dazu, dass der Kern des Partikels nicht vollständig verarbeitet wird.
-
Reaktionsgeschwindigkeiten und thermische Zersetzung:
- Kleinere Partikel zersetzen sich aufgrund ihrer größeren Oberfläche und der effizienten Wärmeübertragung schneller.
- Eine schnellere Zersetzung führt zu einer höheren Ausbeute an Pyrolyseöl, da die flüchtigen Verbindungen schneller und effizienter freigesetzt werden.
- Größere Partikel zersetzen sich langsamer, was aufgrund einer unvollständigen Pyrolyse zu einem höheren Anteil an fester Kohle führen kann.
-
Produkt Verteilung:
- Kleinere Partikel begünstigen die Produktion von Pyrolyseöl und nicht kondensierbaren Gasen, da die schnelle Zersetzung mehr flüchtige Stoffe freisetzt.
- Größere Partikel erzeugen tendenziell mehr feste Holzkohle, da die langsamere Zersetzung eine stärkere Verkohlung des Materials ermöglicht.
- Die Partikelgröße beeinflusst auch die Qualität des festen Rückstands, wobei kleinere Partikel in der Regel eine feinere, gleichmäßigere Verkohlung ergeben.
-
Verweilzeit:
- Kleinere Partikel erfordern kürzere Verweilzeiten in der Pyrolysekammer, da sie sich schneller zersetzen.
- Dies kann die Gesamteffizienz des Prozesses verbessern, den Energieverbrauch senken und den Durchsatz erhöhen.
- Größere Partikel können längere Verweilzeiten erfordern, was zu höheren Energiekosten und geringerer Prozesseffizienz führen kann.
-
Prozess-Optimierung:
- Die meisten Pyrolyseverfahren sind für kleine Partikel (bis zu 2 mm) ausgelegt, um die Wärmeübertragung und die Reaktionsgeschwindigkeit zu maximieren.
- Zur Verringerung der Partikelgröße des Ausgangsmaterials sind häufig Vorverarbeitungsschritte wie Schreddern oder Mahlen erforderlich.
- Die Wahl der Partikelgröße sollte auf das jeweilige Pyrolyseverfahren und die gewünschte Produktverteilung zugeschnitten sein.
-
Zusammensetzung und physikalische Struktur des Rohmaterials:
- Die Partikelgröße steht in Wechselwirkung mit anderen Faktoren wie Feuchtigkeitsgehalt, Temperatur und Erhitzungsgeschwindigkeit und beeinflusst den Pyrolyseprozess.
- Bei der Pyrolyse von Biomasse beispielsweise führen kleinere Partikel mit niedrigem Feuchtigkeitsgehalt und hohen Erhitzungsraten zu mehr flüssigen und gasförmigen Produkten.
- Bei der Pyrolyse von Abfällen (z. B. Reifen) kann die Entfernung von Verstärkungsmaterialien (z. B. Stahl und Fasern) während des Schredderns ebenfalls die Partikelgröße und die Pyrolyseergebnisse beeinflussen.
-
Praktische Überlegungen:
- Die Vorverarbeitung zum Erreichen der gewünschten Partikelgröße kann die Gesamtkosten und die Komplexität des Pyrolyseprozesses erhöhen.
- Die optimale Partikelgröße kann je nach Art des Ausgangsmaterials (z. B. Holz, landwirtschaftliche Abfälle, Kunststoffe) und der verwendeten Pyrolysetechnologie variieren.
- Die Abstimmung der Partikelgröße mit anderen Prozessparametern (z. B. Temperatur, Verweilzeit) ist für die Erzielung der gewünschten Produktausbeute und -qualität entscheidend.
Durch sorgfältige Kontrolle der Partikelgröße des Ausgangsmaterials können die Betreiber von Pyrolyseanlagen den Prozess optimieren, um die Produktion der gewünschten Produkte (Öl, Gas oder Holzkohle) zu maximieren und gleichzeitig den Energieverbrauch und die Verarbeitungszeit zu minimieren.Dies macht die Partikelgröße zu einem entscheidenden Faktor bei der Konstruktion und dem Betrieb von Pyrolyseanlagen.
Zusammenfassende Tabelle:
Aspekt | Kleine Partikel (≤2 mm) | Große Partikel |
---|---|---|
Wärmeübertragung | Schnellere, gleichmäßige Wärmeübertragung | Langsamere, ungleichmäßige Erwärmung |
Reaktionsgeschwindigkeit | Schnellere Zersetzung | Langsamere Zersetzung |
Produktverteilung | Höhere Ausbeute an Pyrolyseöl und -gas | Mehr Festkohleproduktion |
Verweilzeit | Kürzere Verweilzeit | Längere Verweilzeit |
Prozess-Effizienz | Höherer Wirkungsgrad, geringerer Energieverbrauch | Geringerer Wirkungsgrad, höhere Energiekosten |
Optimieren Sie Ihren Pyrolyseprozess mit der richtigen Partikelgröße - Kontaktieren Sie noch heute unsere Experten für maßgeschneiderte Lösungen!