Diamantähnliche Kohlenstoffschichten (DLC) sind ultradünne Hochleistungsschichten, die aufgrund ihrer außergewöhnlichen Härte, geringen Reibung und Verschleißfestigkeit in verschiedenen Anwendungen eingesetzt werden.Die Dicke von DLC-Beschichtungen reicht normalerweise von 0,25 Mikrometern (250 Nanometern) bis 5 Mikrometern (5000 Nanometern) je nach Anwendung und Beschichtungsmethode.Diese Beschichtungen werden durch physikalische Gasphasenabscheidung (PVD) aufgebracht, wodurch die Spezifikationen der technischen Teile nur minimal verändert und gleichzeitig ihre Oberflächeneigenschaften verbessert werden.Da DLC-Beschichtungen sehr dünn sind, verbessern sie die Haltbarkeit, verringern die Reibung und erhalten das Erscheinungsbild des Materials, ohne dass es zu einer größeren Masse kommt.
Die wichtigsten Punkte erklärt:
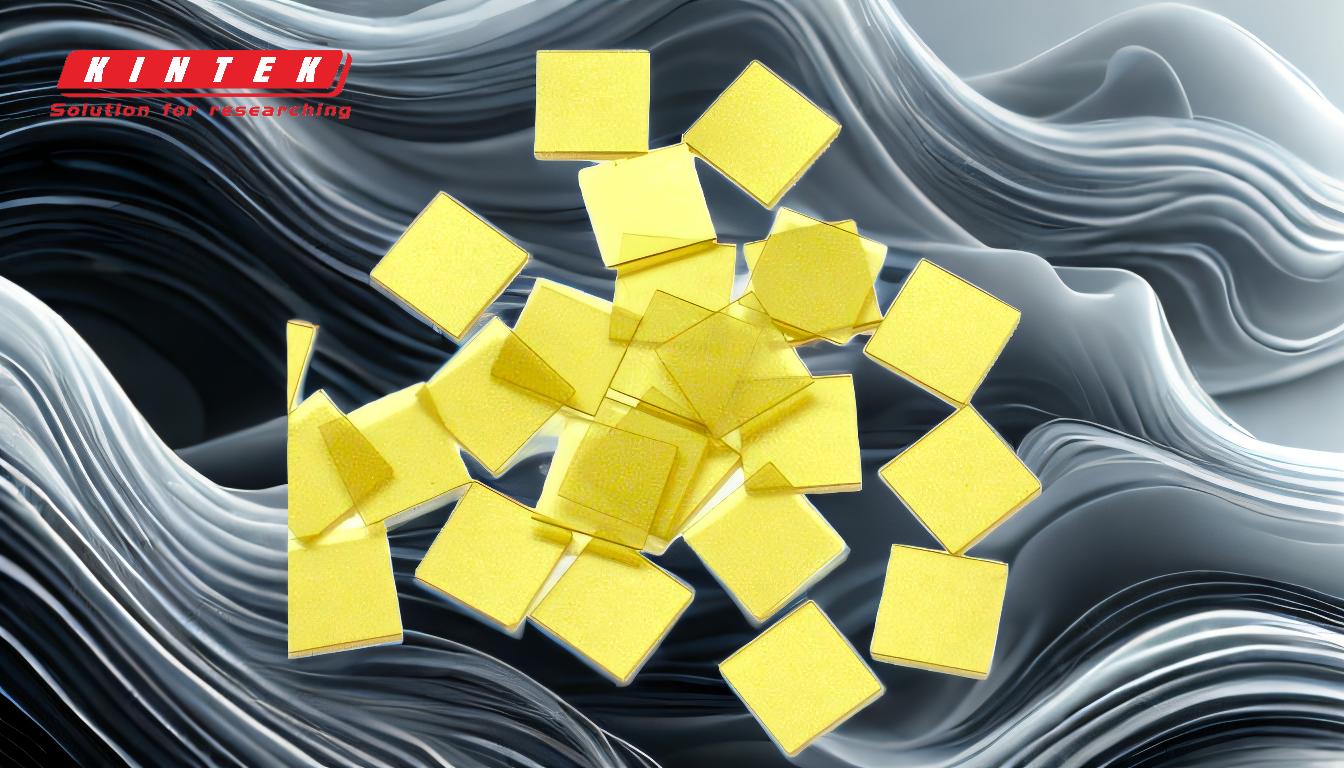
-
Typischer Dickenbereich von DLC-Beschichtungen
- DLC-Beschichtungen sind dünne Schichten, deren Dicke typischerweise zwischen 0,25 Mikrometer bis 5 Mikrometer .
-
Zur Orientierung:
- 1 Mikrometer = 0,001 Millimeter oder 1000 Nanometer.
- Ein rotes Blutkörperchen hat einen Durchmesser von etwa 8 Mikrometern, und ein menschliches Haar ist etwa 80 Mikrometer dick.
- Diese ultradünne Beschaffenheit stellt sicher, dass die Beschichtungen die Abmessungen oder Spezifikationen des darunter liegenden Materials nicht verändern.
-
Anwendungsspezifische Dickenvariationen
-
Die Dicke von DLC-Beschichtungen kann je nach Verwendungszweck variieren:
- Dekorative Anwendungen (z. B. Bleche aus rostfreiem Stahl) werden oft dünnere Beschichtungen verwendet, etwa 0,25 bis 0,5 Mikrometer .
- Funktionelle Anwendungen (z. B. Verschleißschutz, Reibungsminderung) können dickere Beschichtungen erfordern, die von 2 bis 5 Mikrometer .
- Die Wahl der Dicke hängt von Faktoren wie der erforderlichen Haltbarkeit, Härte und Oberflächenbeschaffenheit ab.
-
Die Dicke von DLC-Beschichtungen kann je nach Verwendungszweck variieren:
-
Beschichtungsmethoden und Kontrolle
- DLC-Beschichtungen werden aufgebracht durch Physikalische Gasphasenabscheidung (PVD) Verfahren.
- Der Beschichtungsprozess ermöglicht eine präzise Steuerung der Schichtdicke, der Korngröße und der Oberflächenrauhigkeit durch Anpassung von Parametern wie Gasphasenzusammensetzung und Beschichtungszeit.
- Durch diese individuelle Anpassung wird sichergestellt, dass die Beschichtung die spezifischen Leistungsanforderungen der Anwendung erfüllt.
-
Vorteile von dünnen DLC-Beschichtungen
-
Trotz ihrer geringen Dicke bieten DLC-Schichten erhebliche Vorteile:
- Hohe Härte:Erhöht die Verschleißfestigkeit und Haltbarkeit.
- Geringe Reibung:Verringert den Energieverlust und verbessert die Effizienz der beweglichen Teile.
- Chemische Inertheit:Bietet Widerstand gegen Korrosion und chemischen Abbau.
- Glatte Oberfläche:Verbessert das Erscheinungsbild und verringert die Oberflächenrauhigkeit.
- Diese Eigenschaften machen DLC-Beschichtungen ideal für Anwendungen in Branchen wie der Automobil-, Luft- und Raumfahrtindustrie, der Medizintechnik und der Unterhaltungselektronik.
-
Trotz ihrer geringen Dicke bieten DLC-Schichten erhebliche Vorteile:
-
Vergleich mit anderen Beschichtungen
- DLC-Beschichtungen sind dünner als viele herkömmliche Beschichtungen, bieten aber aufgrund ihrer einzigartigen Eigenschaften eine bessere Leistung.
- Während beispielsweise herkömmliche Hartstoffbeschichtungen wie Chrom oder Titannitrid dicker sein können, bieten DLC-Beschichtungen eine bessere Reibungsreduzierung und Verschleißfestigkeit bei einem Bruchteil der Dicke.
-
Bedeutung der Schichtdicke bei technischen Anwendungen
- Die geringe Dicke von DLC-Beschichtungen ist bei technischen Anwendungen von entscheidender Bedeutung, bei denen es auf die Einhaltung präziser Abmessungen ankommt.
- Dickere Beschichtungen könnten die Passform, Form oder Funktion von Präzisionsbauteilen beeinträchtigen, während DLC-Beschichtungen die Leistung verbessern, ohne diese Faktoren zu beeinträchtigen.
-
Zukünftige Trends in der DLC-Beschichtungstechnologie
- Fortschritte bei den Abscheidetechniken ermöglichen noch dünnere und gleichmäßigere DLC-Beschichtungen, was ihren Einsatz bei Anwendungen im Mikro- und Nanobereich erweitert.
- Die Forschung konzentriert sich auch auf die Optimierung des Abscheidungsprozesses, um die Eigenschaften der Beschichtungen, wie z. B. die Haftfestigkeit und die thermische Stabilität, weiter zu verbessern.
Zusammenfassend lässt sich sagen, dass die Dicke von diamantähnlichen Kohlenstoffschichten ein entscheidender Faktor ist, der ihre Leistung und Eignung für bestimmte Anwendungen bestimmt.Durch sorgfältige Kontrolle des Abscheidungsprozesses können die Hersteller die Dicke der Beschichtung genau auf die Anforderungen ihrer Anwendung abstimmen und so eine optimale Leistung und Haltbarkeit gewährleisten.
Zusammenfassende Tabelle:
Aspekt | Details |
---|---|
Typische Schichtdicke | 0,25 bis 5 Mikrometer |
Anwendungen | Dekorativ (0,25-0,5 Mikron), Funktional (2-5 Mikron) |
Abscheidungs-Methode | Physikalische Gasphasenabscheidung (PVD) |
Wichtigste Vorteile | Hohe Härte, geringe Reibung, chemische Inertheit, glatte Oberfläche |
Branchen | Automobilindustrie, Luft- und Raumfahrt, medizinische Geräte, Unterhaltungselektronik |
Vergleich mit anderen | Dünner als herkömmliche Beschichtungen, überlegene Reibungs- und Verschleißfestigkeit |
Optimieren Sie Ihre Anwendung mit DLC-Beschichtungen - Kontaktieren Sie noch heute unsere Experten für maßgeschneiderte Lösungen!