PVD (Physical Vapor Deposition, physikalische Gasphasenabscheidung) und CVD (Chemical Vapor Deposition, chemische Gasphasenabscheidung) sind zwei weit verbreitete Verfahren zur Dünnschichtbeschichtung, bei denen Materialschichten auf Substrate aufgebracht werden, um deren Eigenschaften zu verbessern.Die Dicke dieser Beschichtungen variiert je nach Anwendung, wobei PVD-Beschichtungen in der Regel zwischen 0,25 und 5 Mikrometer und CVD-Beschichtungen im Allgemeinen dicker sind und zwischen 5 und 10 Mikrometer betragen.Diese Dicken werden sorgfältig ausgewählt, um sicherzustellen, dass die Beschichtungen die gewünschten funktionellen Vorteile bieten, ohne die Spezifikationen der darunter liegenden Teile zu verändern.Die Kenntnis der Schichtdickenbereiche von PVD- und CVD-Beschichtungen ist entscheidend für die Auswahl der geeigneten Beschichtungsmethode für bestimmte Anwendungen, sei es für dekorative Zwecke, Funktionsverbesserungen oder Schutzmaßnahmen.
Die wichtigsten Punkte werden erklärt:
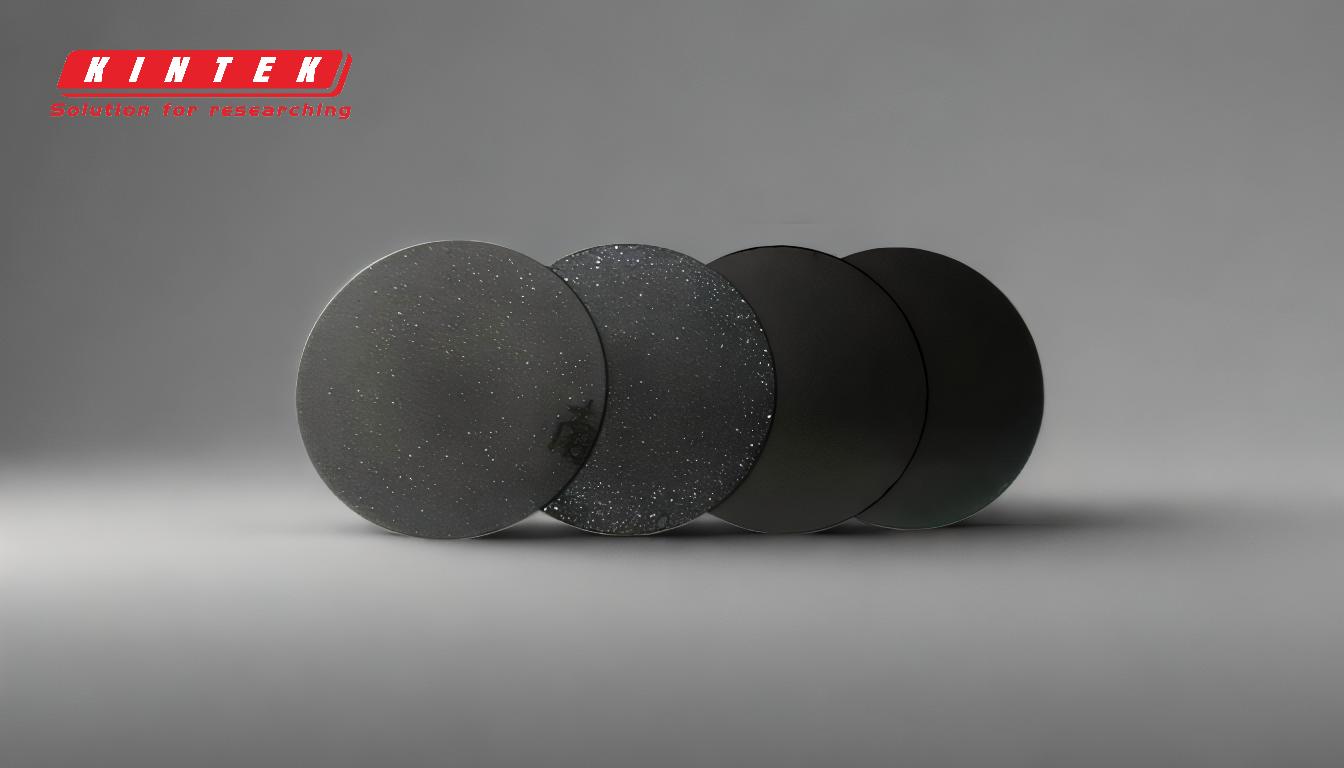
-
PVD-Beschichtungsdicke:
- PVD-Beschichtungen sind dünne Schichten, die in der Regel zwischen 0,25 bis 5 Mikrometer in der Dicke.
-
Die genaue Dicke hängt von der jeweiligen Anwendung ab:
- Dekorative Anwendungen (z. B. Bleche aus rostfreiem Stahl) können dünnere Beschichtungen erfordern, etwa 0,30 Mikrometer .
- Funktionelle Anwendungen (z. B. Verbesserung der Verschleißfestigkeit oder Härte) erfordern häufig dickere Beschichtungen, die von 2 bis 5 Mikrometer .
- PVD-Beschichtungen sind bekannt für ihre Präzision und ihre Fähigkeit, die Spezifikationen von technischen Teilen aufgrund ihrer geringen Dicke einzuhalten.
-
CVD-Beschichtungsdicke:
- CVD-Beschichtungen sind im Allgemeinen dicker als PVD-Beschichtungen, in der Regel zwischen 5 bis 10 Mikrometer .
- Aufgrund ihrer größeren Dicke eignen sich CVD-Beschichtungen für Anwendungen, die eine höhere Haltbarkeit, thermische Stabilität oder chemische Beständigkeit erfordern.
- CVD-Beschichtungen entstehen durch eine chemische Reaktion auf der Substratoberfläche, wodurch dickere und gleichmäßigere Schichten aufgetragen werden können als bei der PVD-Beschichtung.
-
Vergleich von PVD- und CVD-Schichtdicken:
- PVD-Beschichtungen sind dünner (0,25-5 Mikrometer) und werden häufig verwendet, wenn eine genaue Kontrolle der Schichtdicke erforderlich ist, wie bei dekorativen oder hochpräzisen funktionellen Anwendungen.
- CVD-Beschichtungen sind dicker (5-10 Mikrometer) und werden bevorzugt für Anwendungen eingesetzt, bei denen Haltbarkeit und Beständigkeit gegen raue Umgebungsbedingungen entscheidend sind, z. B. bei Industriewerkzeugen oder Hochtemperaturkomponenten.
-
Faktoren, die die Beschichtungsdicke beeinflussen:
- Anforderungen an die Anwendung: Der Verwendungszweck des beschichteten Teils (z. B. dekorativ, funktionell oder schützend) bestimmt die optimale Schichtdicke.
- Material des Substrats: Das zu beschichtende Material kann die erreichbare Dicke und Haftung der Beschichtung beeinflussen.
- Parameter des Beschichtungsprozesses: Variablen wie Temperatur, Druck und Beschichtungszeit können die Dicke und Qualität der Beschichtung beeinflussen.
-
Praktische Auswirkungen der Beschichtungsdicke:
- Dünne PVD-Beschichtungen (0,25-2 Mikrometer): Ideal für Anwendungen, bei denen eine minimale Beeinträchtigung der Abmessungen des Substrats erforderlich ist, wie z. B. in der Feinmechanik oder bei dekorativen Beschichtungen.
- Dickere PVD-Beschichtungen (2-5 Mikrometer): Bieten eine höhere Verschleißfestigkeit und Haltbarkeit und eignen sich daher für funktionelle Anwendungen wie Schneidwerkzeuge oder Automobilkomponenten.
- CVD-Beschichtungen (5-10 Mikrometer): Bieten einen hervorragenden Schutz gegen extreme Bedingungen wie hohe Temperaturen oder korrosive Umgebungen und eignen sich daher für Anwendungen in der Industrie und der Luft- und Raumfahrt.
-
Real-World Kontext:
-
Um die Dicke ins rechte Licht zu rücken:
- 1 Mikron = 0,001 Millimeter .
- A rotes Blutkörperchen ist etwa 8 Mikrometer Durchmesser.
- A menschliches Haar ist etwa 80 Mikrometer im Durchmesser.
- Dieser Vergleich verdeutlicht, wie dünn PVD- und CVD-Beschichtungen sind, trotz ihrer erheblichen Auswirkungen auf die Leistung und Langlebigkeit der beschichteten Teile.
-
Um die Dicke ins rechte Licht zu rücken:
Durch das Verständnis der Schichtdickenbereiche und Anwendungen von PVD- und CVD-Beschichtungen können Einkäufer und Ingenieure fundierte Entscheidungen darüber treffen, welche Beschichtungsmethode für ihre spezifischen Anforderungen am besten geeignet ist.Ganz gleich, ob das Ziel darin besteht, die Ästhetik zu verbessern, die Funktionalität zu erhöhen oder Schutz zu bieten, die Wahl zwischen PVD und CVD hängt von der gewünschten Schichtdicke und den betrieblichen Anforderungen an das beschichtete Teil ab.
Zusammenfassende Tabelle:
Beschichtungsart | Schichtdicke | Wichtigste Anwendungen |
---|---|---|
PVD | 0,25-5 Mikrometer | Dekorativ, funktionell, feinmechanisch |
CVD | 5-10 Mikrometer | Langlebigkeit, thermische Stabilität, industrielle Werkzeuge |
Benötigen Sie Hilfe bei der Auswahl der richtigen Beschichtung für Ihre Anwendung? Kontaktieren Sie noch heute unsere Experten !