Die Partikelgrößenverteilung beim Mahlen wird durch mehrere Faktoren beeinflusst, darunter die Größe und Dichte der Mahlkugeln, die Mahldauer, die Anzahl der Mahlzyklen, die Verweilzeit, die Vorschubgeschwindigkeit, die Rotationsgeschwindigkeit und die Temperatur.Kleinere Mahlkugeln und längere Mahlzeiten führen im Allgemeinen zu kleineren Partikeln, da sie die Häufigkeit der Zusammenstöße und die auf das Material übertragene Energie erhöhen.Die Anzahl der Mahlzyklen und die Verweilzeit wirken sich direkt auf den Grad der Zerkleinerung aus, wobei mehr Zyklen zu feineren Partikeln führen.Darüber hinaus spielen auch die Beschaffenheit des gemahlenen Materials, die Vorschubgeschwindigkeit und die Drehzahl der Mühle eine wichtige Rolle.Die Temperatur kann das Gleichgewicht zwischen Defektbildung und Rekombination beeinflussen, was sich auf die endgültige Korngröße auswirkt.
Die wichtigsten Punkte erklärt:
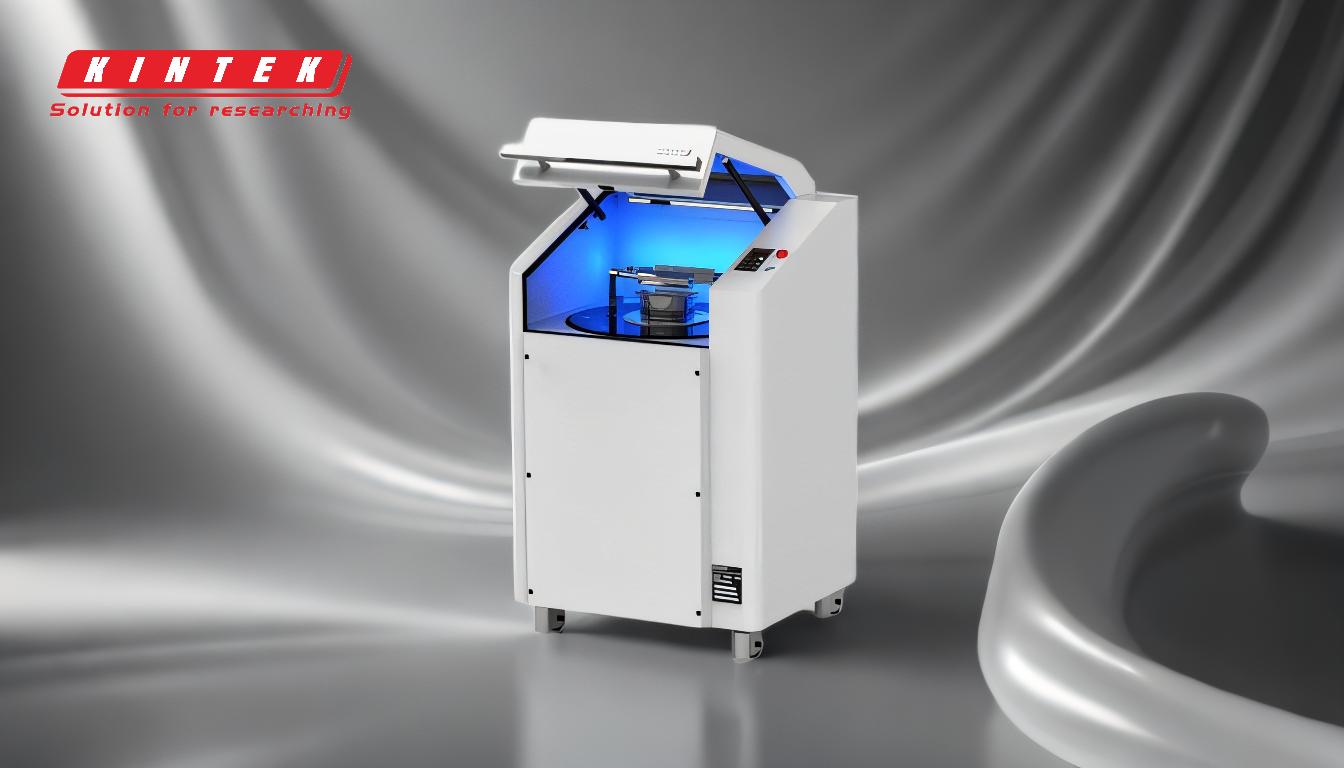
-
Größe und Dichte von Mahlkugeln:
- Erläuterung:Kleinere Mahlkugeln sind effektiver bei der Erzeugung kleinerer Partikel, da sie die Häufigkeit der Zusammenstöße und die auf das Material übertragene Energie erhöhen.Auch die Dichte der Kugeln wirkt sich auf die Aufprallkraft aus, wobei dichtere Materialien eine effektivere Mahlung ermöglichen.
- Einfluss auf die Partikelgröße:Kleinere und dichtere Kugeln führen zu feineren Partikeln aufgrund erhöhter Kollisionsfrequenz und Energieübertragung.
-
Mahldauer und Anzahl der Mahlzyklen:
- Erläuterung:Längere Mahlzeiten und mehr Mahlzyklen ermöglichen mehr Kollisionen und Energieübertragung, was zu einer stärkeren Zerkleinerung führt.Jeder Zyklus trägt zur Erosion größerer Partikel in kleinere Fragmente bei.
- Auswirkungen auf die Partikelgröße:Je länger die Mahldauer und -zyklen sind, desto mehr kleinere Partikel entstehen, da die größeren Partikel nach und nach zerkleinert werden.
-
Verweilzeit:
- Erläuterung:Die Zeit, die das Material in der Mühlenkammer verbringt, beeinflusst den Grad der Zerkleinerung.Längere Verweilzeiten ermöglichen mehr Wechselwirkungen zwischen den Mahlkörpern und dem Material.
- Einfluss auf die Partikelgröße:Längere Verweilzeiten führen in der Regel zu feineren Partikeln, da sie den Mahlkräften stärker ausgesetzt sind.
-
Vorschubgeschwindigkeit und Füllstand im Gefäß:
- Erläuterung:Die Geschwindigkeit, mit der das Material in die Mühle eingespeist wird, und der Füllstand des Materials im Behälter können die Effizienz des Mahlvorgangs beeinflussen.Eine optimale Zuführungsrate gewährleistet eine gleichmäßige Vermahlung, während der Füllstand die Wechselwirkung zwischen dem Material und den Mahlkörpern beeinflusst.
- Einfluss auf die Partikelgröße:Angemessene Vorschubgeschwindigkeiten und Gefäßfüllstände sorgen für eine effiziente Zerkleinerung, die zu einer gleichmäßigeren Korngrößenverteilung führt.
-
Rotationsgeschwindigkeit des Zylinders:
- Erläuterung:Die Geschwindigkeit, mit der sich der Mühlenzylinder dreht, beeinflusst die kinetische Energie der Mahlkugeln und die Häufigkeit der Kollisionen.Höhere Geschwindigkeiten können die auf das Material übertragene Energie erhöhen.
- Auswirkungen auf die Partikelgröße:Höhere Drehzahlen können zu feineren Partikeln führen, da die Kollisionsfrequenz und der Energietransfer erhöht werden.
-
Beschaffenheit des Mahlgutes:
- Erläuterung:Die physikalischen und chemischen Eigenschaften des zu zerkleinernden Materials, wie z. B. Härte und Sprödigkeit, beeinflussen, wie es auf das Mahlen reagiert.Härtere Materialien benötigen möglicherweise mehr Energie, um eine Zerkleinerung zu erreichen.
- Auswirkungen auf die Partikelgröße:Die Beschaffenheit des Materials bestimmt die Leichtigkeit, mit der es gemahlen werden kann, und wirkt sich auf die endgültige Korngrößenverteilung aus.
-
Temperatur:
- Erläuterung:Die Temperatur kann das Gleichgewicht zwischen Defektbildung und Rekombination während des Mahlens beeinflussen.Höhere Temperaturen können die Wiederherstellung von Defekten erleichtern, was sich auf die endgültige Korngröße auswirkt.
- Einfluss auf die Partikelgröße:Die Temperaturkontrolle ist entscheidend für das Erreichen der gewünschten Partikelgröße, da sie die Reaktion des Materials auf die Mahlkräfte beeinflusst.
Wenn man diese Faktoren versteht und optimiert, kann man die gewünschte Partikelgrößenverteilung im Mahlprozess erreichen.Jeder Faktor spielt eine entscheidende Rolle für die Effizienz und Effektivität des Mahlprozesses, und ihr Zusammenspiel bestimmt das Endergebnis.
Zusammenfassende Tabelle:
Faktor | Einfluss auf die Partikelgröße |
---|---|
Größe und Dichte von Mahlkugeln | Kleinere, dichtere Kugeln führen zu feineren Partikeln aufgrund erhöhter Kollisionsfrequenz und Energieübertragung. |
Mahldauer und Zyklen | Längere Mahlzeiten und mehr Zyklen führen zu feineren Partikeln, da größere Fragmente zerkleinert werden. |
Verweilzeit | Längere Verweilzeiten führen zu feineren Partikeln, da sie den Mahlkräften stärker ausgesetzt sind. |
Aufgabemenge und Gefäßfüllstand | Optimale Vorschubgeschwindigkeiten und Gefäßfüllstände gewährleisten eine effiziente Vermahlung und eine gleichmäßige Partikelgröße. |
Rotationsgeschwindigkeit | Höhere Drehzahlen erhöhen die Kollisionsfrequenz und den Energietransfer, wodurch feinere Partikel entstehen. |
Beschaffenheit des Mahlguts | Härte und Sprödigkeit des Materials bestimmen die Leichtigkeit des Mahlens und die endgültige Korngröße. |
Temperatur | Die Temperatur wirkt sich auf die Defektbildung und Rekombination aus und beeinflusst die endgültige Korngröße. |
Benötigen Sie Hilfe bei der Optimierung Ihres Fräsprozesses? Kontaktieren Sie noch heute unsere Experten für maßgeschneiderte Lösungen!