Drehrohröfen sind komplexe Industrieanlagen, die für die Verarbeitung von Materialien bei hohen Temperaturen eingesetzt werden. Ihre Konstruktion und ihr Betrieb werden durch eine Vielzahl von Parametern bestimmt, die eine effiziente und effektive Leistung gewährleisten. Diese Parameter lassen sich grob in Konstruktions-, Struktur- und Betriebsfaktoren unterteilen. Zu den Konstruktionsparametern gehören Materialeigenschaften wie Partikelgröße, Schüttdichte und thermische Eigenschaften, die die Konstruktion des Ofens beeinflussen. Strukturelle Parameter betreffen Komponenten wie den Ofenmantel, die feuerfeste Auskleidung und die Antriebseinheit. Betriebsparameter wie Neigungswinkel, Drehgeschwindigkeit und Temperaturprofile bestimmen die Leistung des Ofens im Betrieb. Das Verständnis dieser Parameter ist entscheidend für die Optimierung der Effizienz des Ofens und die Erzielung der gewünschten Prozessergebnisse.
Schlüsselpunkte erklärt:
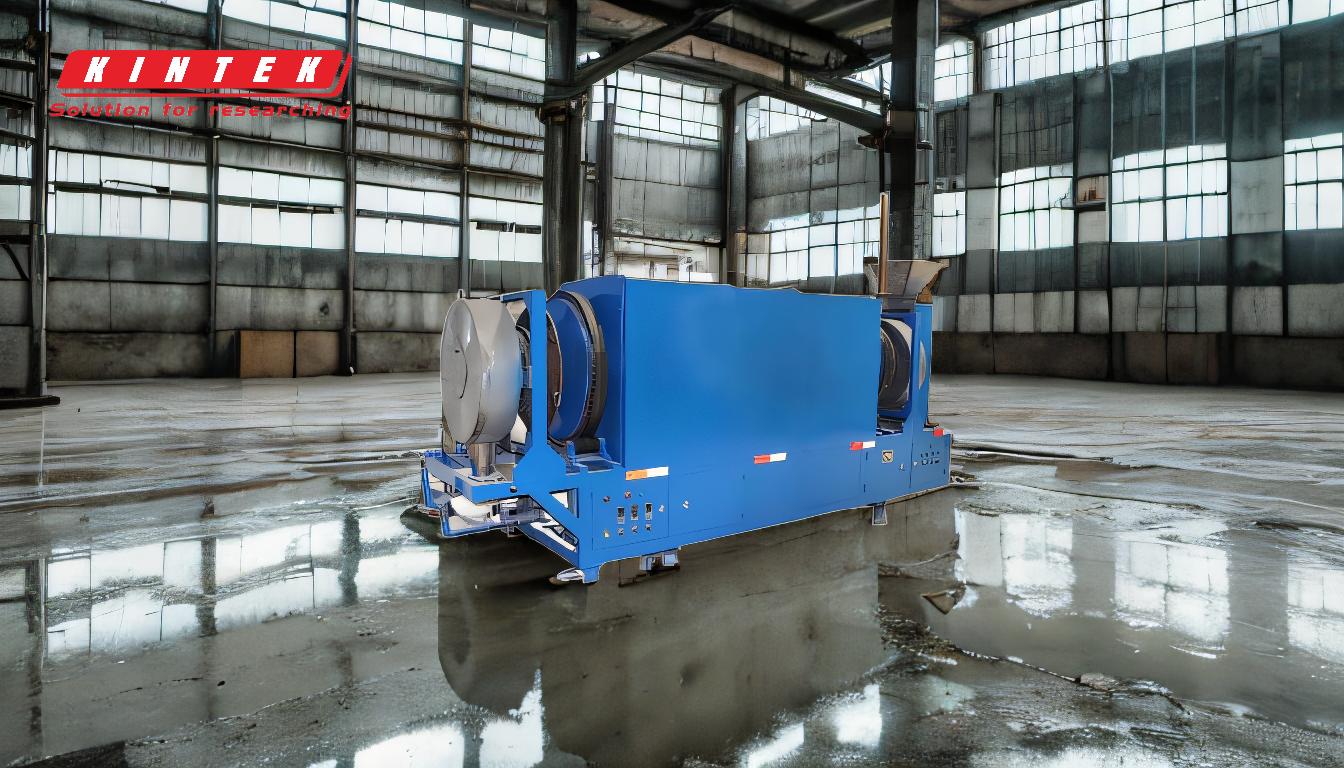
-
Konstruktionsparameter:
-
Materialeigenschaften: Die Konstruktion eines Drehrohrofens wird stark von den Eigenschaften des zu verarbeitenden Materials beeinflusst. Dazu gehören:
- Partikelgrößenverteilung: Sie bestimmt, wie das Material im Ofen fließt und reagiert.
- Schüttdichte: Beeinflusst das Volumen des Materials, das in einer bestimmten Zeit verarbeitet werden kann.
- Abrasivität und Korrosivität: Beeinflusst die Wahl der Materialien für die Konstruktion des Ofens, um die Haltbarkeit zu gewährleisten.
- Spezifische Wärme und Reaktionswärme: Bestimmen den Energiebedarf für die Verarbeitung.
- Wärmeleitfähigkeit: Beeinflusst die Effizienz der Wärmeübertragung innerhalb des Ofens.
- Chemische Zusammensetzung: Bestimmt die Beständigkeit des Ofens gegen chemische Reaktionen und Korrosion.
-
Materialeigenschaften: Die Konstruktion eines Drehrohrofens wird stark von den Eigenschaften des zu verarbeitenden Materials beeinflusst. Dazu gehören:
-
Strukturelle Parameter:
- Ofenmantel: Der Hauptkörper des Ofens, der sich häufig an den Enden konisch verjüngt und so konstruiert ist, dass er Torsions- und Biegebelastungen standhält.
- Feuerfeste Auskleidung: Schützt den Ofenmantel vor hohen Temperaturen und chemischen Reaktionen und sorgt für Langlebigkeit.
- Stützreifen und Walzen: Bieten strukturelle Unterstützung und ermöglichen eine reibungslose Drehung des Ofens.
- Antriebseinheit: Umfasst Mechanismen wie Ketten- und Kettenradantriebe, Zahnradantriebe, Reibungsantriebe oder Direktantriebe, die den Ofen in Drehung versetzen.
- Interne Wärmetauscher: Verbessern die Effizienz der Wärmeübertragung innerhalb des Ofens.
-
Betriebliche Parameter:
- Neigungswinkel: Die Neigung des Ofens wirkt sich auf die Durchflussrate des Materials durch den Ofen aus.
- Rotationsgeschwindigkeit: Bestimmt die Geschwindigkeit, mit der das Material gemischt und der Hitze ausgesetzt wird.
- Verweilzeit: Die Dauer, während der feste Partikel im Ofen verbleiben und das Ausmaß der Reaktion oder Verarbeitung beeinflussen.
- Temperatur-Profile: Der Ofen arbeitet mit mehreren Heizzonen (Trocknen, Erhitzen, Reagieren und Einweichen), um die gewünschte thermische Verarbeitung zu erreichen.
- Materialdurchsatz und Austragsgeschwindigkeit: Steuerung des Durchsatzes und Gewährleistung einer gleichmäßigen Verarbeitung.
- Betttiefe: Wird über einen Ringdamm gesteuert und beeinflusst die Wärmeeinwirkung auf das Material und die Reaktionsbedingungen.
-
Heizzonen:
- Trocknungszone: Entfernt Feuchtigkeit aus dem Material.
- Heizzone: Erhöht das Material auf die für die Verarbeitung erforderliche Temperatur.
- Reaktionszone: Wo die primären chemischen oder physikalischen Umwandlungen stattfinden.
- Einweichzone: Sorgt für eine gleichmäßige Temperaturverteilung und schließt alle verbleibenden Reaktionen ab.
-
Kontrollmechanismen:
- Ringdamm: Dient zur Steuerung der Betttiefe und gewährleistet, dass das Material der Hitze und den Reaktionsbedingungen optimal ausgesetzt ist.
- Antriebssysteme: Verschiedene Antriebsmechanismen (Kette und Kettenrad, Getriebe, Reibung oder Direktantrieb) werden je nach Größe und Betriebsanforderungen des Ofens ausgewählt.
Durch die sorgfältige Berücksichtigung dieser Parameter können Drehrohröfen so konstruiert und betrieben werden, dass die Effizienz, die Lebensdauer und die Effektivität des Prozesses maximiert werden. Jeder Parameter spielt eine entscheidende Rolle, wenn es darum geht, sicherzustellen, dass der Ofen die spezifischen Anforderungen des zu verarbeitenden Materials erfüllt, unabhängig davon, ob es sich um Trocknen, Erhitzen oder chemische Reaktionen handelt.
Zusammenfassende Tabelle:
Parameter Typ | Schlüsselfaktoren |
---|---|
Auslegungsparameter | Partikelgröße, Schüttdichte, thermische Eigenschaften, chemische Zusammensetzung |
Strukturelle Parameter | Ofenmantel, feuerfeste Auskleidung, Stützreifen, Antriebsaggregat, Wärmetauscher |
Betriebliche Parameter | Neigungswinkel, Drehgeschwindigkeit, Temperaturprofile, Verweilzeit |
Heizzonen | Trocknen, Erhitzen, Reaktion, Weichen |
Steuerungsmechanismen | Ringdamm, Antriebssysteme |
Sind Sie bereit, die Leistung Ihres Drehrohrofens zu optimieren? Kontaktieren Sie noch heute unsere Experten für maßgeschneiderte Lösungen!